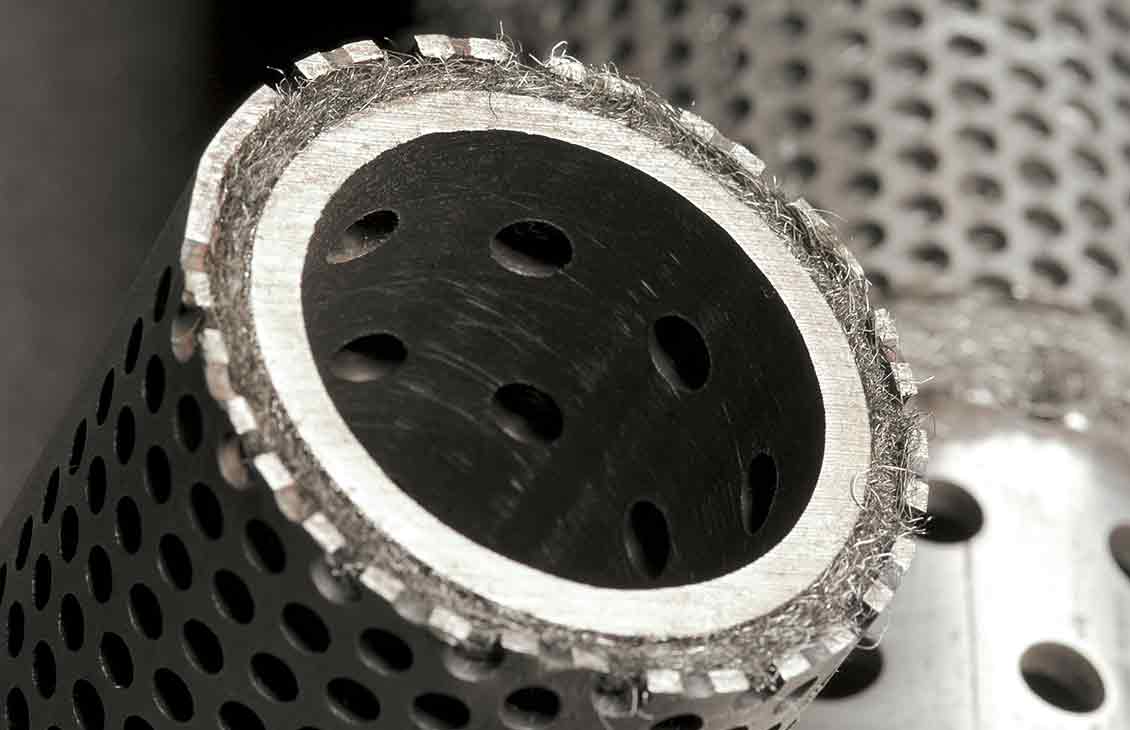
Sand Control Well Screen Selection research – Part 1
April 22, 2023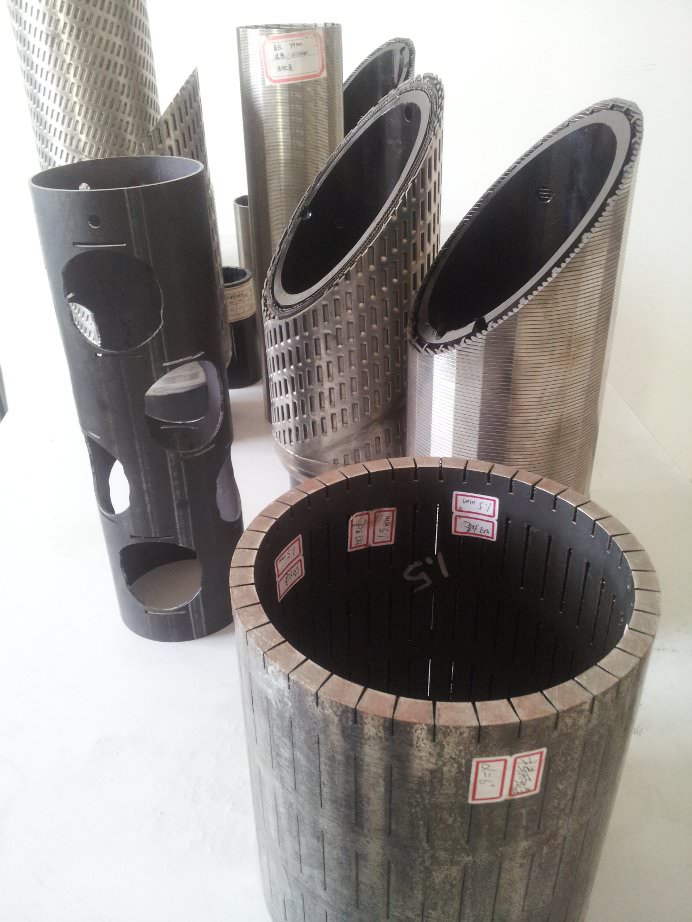
Sand Control Well Screen Selection research – Part 3
April 22, 2023Sand Control Screen Selection research – Part 2
Figure 2. Wire wrap and metal mesh screens. Both wire wrap screens (left) and metal mesh screens (right) are constructed around a perforated base pipe. Wire wrap screens include a screen that can be slipped over the base pipe and welded into place. The metal mesh screens,
made of woven metal layers that may include sintered metal, are placed between the base pipe and the perforated protective shroud
Figure 3. Slot width ranges for sand screen design. Mathematical modeling and laboratory results led scientists to define four slot widths for each target sand based on sand grain diameter (d). The lower and upper limits of width sizes are defined by d22 and d++. The optimum size range that will neither plug nor produce sand is bounded by d2 and d+ (green
Figure 4. Two types of sand retention tests. Slurry tests (top) are designed to simulate gradual failure of the formation surrounding the borehole. Technicians pump a low-concentration sand slurry through a screen coupon, then measure the weight of solids produced through the screen and the pressure buildup across the screen versus the amount of sand contacting the screen. Laboratories design prepack tests (bottom) to simulate a complete borehole collapse by placing a sand sample directly on the screen. A liquid is then flowed through the sand and screen. Technicians then create a confining stress on the sample that forces the sand into full contact with the screen. The test measures the amount of sand that passes through the screen—measured by weight—and the pressure drop across the screen
around the pipe during manufacturing or manu-factured as an individual jacket that is later welded to a base pipe. Mesh screens include one or more layers of woven stainless steel or mesh wire wrapped around a base pipe. The mesh, which acts as a filter, is covered by a protective shroud (Figure 2). Although uncommon, opera-tors have included shrouds on WWSs in side-tracked wells that have challenging casing exits.Even when widespread agreement exists that SASs are appropriate, recommendations for screen type and opening size often vary widely. Early efforts at screen sizing were based on a single point (d10) on the PSD and some amount of sand production that was assumed to be accept-able, as described earlier.4 In the 1990s, a mathematical model was developed to optimize sizing of slots in sand con-trol devices. This model was based on a fractal description of the entire PSD given in terms of the number of particles rather than particle mass.5 A series of laboratory tests were performed to establish a database of wire wrap screen behavior results using sands from the North Sea and the Haltenbanken Area offshore Norway.
From these experiments and the number-based particle size distributions, four slot widths were defined for each sand type tested: d22, d2, d+ and d++ (Figure 3). The designation d22 was the largest slot size at which severe plugging occurred and d++ was the smallest slot size at which continuous sand production occurred. The d2 and d+ slot widths were defined as the small-est hole size that did not allow plugging and the largest slot size that did not allow continuous sand production, respectively.6 The ideal slot size was stipulated to be between d2 and d+. Completion engineers often use these crite-ria to constrain screen size options before per-forming sand retention tests (SRTs) in the laboratory to determine a final screen size. Two types of SRTs are available: slurry tests and pre-pack tests. Slurry tests are designed to replicate gradual failure of the rock surrounding the borehole (Figure 4).
During slurry tests, a low-concentration slurry is pumped at a constant rate to form a sandpack around the screen. The mechanism of sand retention, therefore, is dic-tated only by particle size exclusion. To perform prepack tests, which represent complete hole collapse, technicians place a sandpack on the screen and pump clean solids-free liquid through the pack. Because a sand-pack is already in place, sand retention during a prepack test is achieved through both size exclusion and bridging. Recent research has shown that current SRT setup and interpretation methods tend to favor one screen type or other. The traditional criteria used to choose between a gravel pack or an SAS are overly conservative and often lead analysts to opt for a gravel pack. Numerous experiments indicate that, contrary to accepted wisdom, screen plugging is rarely a problem in clean sand formations; when plugging is a threat as a result of other factors such as contaminated fluids, the risk can be mitigated through proper hole prepa-ration procedures.7To address the variability and inconsistency inherent in screen selection and to better under-stand the physics of sand control, scientists recently used a numerical simulation approach to evaluate sand screen performance.
The effort was part of a larger plan to produce a systematic screen selection process. Screen sizing practices that relied on accepted standards were based on PSDs that did not use the results of sand retention tests. Despite the limitations of these standards, which are based on a few parameters of the formation sand size distribution and implicit assumptions about acceptable levels of sand production, most experts continue to use such standards not only to narrow screen size options but also to perform SRTs to confirm final screen selection. In general, three results from SRTs are of interest: sand production correlated to the screen’s sand retention efficiency, pressure development correlated to screen plugging ten-dency and size distribution of produced particles with which to evaluate the risk of screen erosion. However, because it has now been established that screen plugging is rarely a problem in clean formation sand of any PSD, the main criteria for screen selection become transient sand produc-tion and PSD of produced particles. Engineers can determine both criteria using models devel-oped in the last five years for specific screen and PSD combinations without having to conduct actual SRTs.