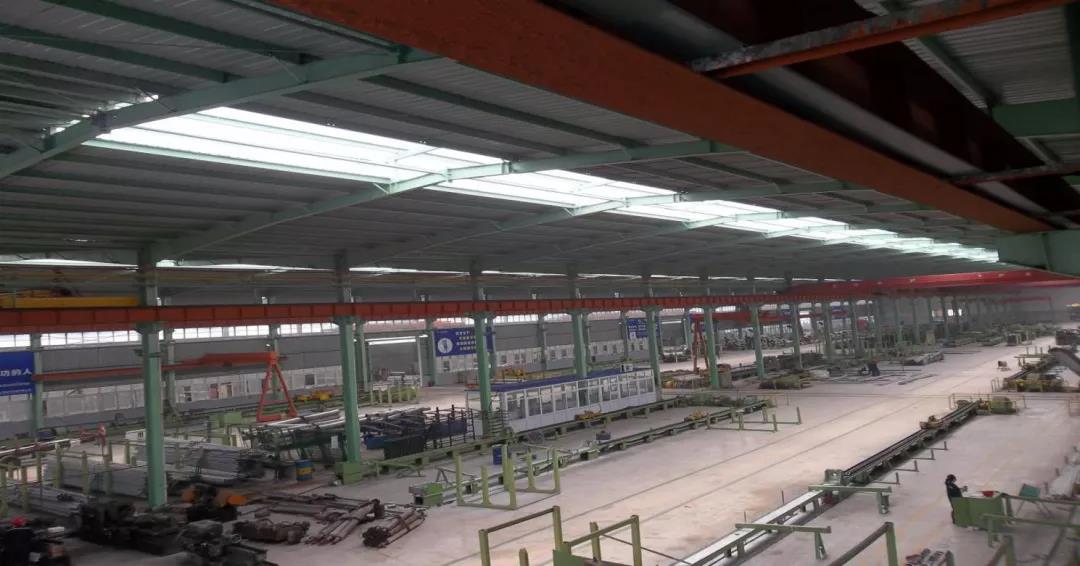
what the difference welded steel pipe and seamless steel pipe?
May 6, 2023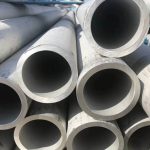
Composition of 201 Stainless Steel Pipes
May 21, 2023Common Pipeline Protection Techniques
Pipeline protection technologies are essential to safeguarding pipelines from physical damage, corrosion, and leaks. The following are some of the most common pipeline protection technologies:
Cathodic Protection (CP): Cathodic protection is an electrochemical technique used to prevent corrosion in metallic pipelines. CP systems use a sacrificial anode, which is a metal with a higher electrochemical potential than the pipeline material. The anode corrodes preferentially, protecting the pipeline from corrosion.
Coatings: Coatings are applied to the external and internal surfaces of pipelines to provide a barrier against corrosion, mechanical damage, and other environmental factors. Common coatings include fusion bonded epoxy (FBE), liquid epoxy, and polyurethane.
Composite Repair Systems: These systems use composite materials, such as fiber-reinforced polymers (FRP), to repair damaged or corroded pipelines. Composite repair systems can be used to restore the structural integrity and pressure containment capabilities of pipelines.
Leak Detection Systems: Leak detection technologies are critical to identifying and locating leaks in pipelines before they become catastrophic. Common leak detection methods include acoustic, pressure point analysis, fiber optic sensing, and infrared thermography.
Pipeline Inspection Gauges (PIGs): PIGs are devices that travel through the pipeline to perform various tasks, such as cleaning, inspecting, and maintaining the pipeline. PIGs can detect anomalies, such as corrosion, dents, and cracks, allowing for early intervention and repair.
Pipeline Monitoring Systems: These systems use sensors, data acquisition devices, and communication networks to monitor pipeline parameters, such as pressure, temperature, and flow rate. This information is used to detect potential issues and optimize pipeline operations.
Pipeline Integrity Management Systems (PIMS): PIMS are software solutions that integrate pipeline data, risk assessment, and decision-making processes to ensure pipeline safety and reliability. PIMS help operators identify, prioritize, and address potential threats to pipeline integrity.
Hydrostatic Testing: Hydrostatic testing involves filling a pipeline segment with water, pressurizing it to a predetermined level, and monitoring for leaks or pressure changes. This test is performed to validate the pipeline’s structural integrity and leak tightness.
Trenchless Technologies: These methods are used to install, repair, or replace pipelines without the need for traditional open-cut trenching. Common trenchless technologies include horizontal directional drilling (HDD), pipe bursting, and cured-in-place pipe lining (CIPP).
Geospatial Information Systems (GIS): GIS are computer-based tools used to store, analyze, and visualize spatial information. In the context of pipeline protection, GIS can be used to map and analyze pipeline data, identify potential threats, and support decision-making.
IT provides a concise summary of the most common pipeline protection technologies. These technologies play a crucial role in maintaining the safety, integrity, and reliability of pipeline systems.
Pipeline protection technology buried in soil
Metal pipes buried in the soil will have anode and cathode regions on the surface of the pipe due to various reasons, and local corrosion will occur in the anode region. Cathodic protection is the use of external means to force the protected metal surface in the electrolyte to become a cathode to achieve the purpose of inhibiting corrosion. When using cathodic protection, the protected metal pipeline should have a good anti-corrosion insulation layer to reduce the cost of cathodic protection. Cathodic protection technology can be divided into two protection methods: sacrificial anode method and forced current method according to the supply mode of protection current.
The main advantages of using the sacrificial anode method are: no need for external power supply, less interference to the outside world, low installation and maintenance costs, no need to requisition land or occupy other buildings and structures, and high utilization rate of protective current, so it is especially suitable for corrosion of buried steel pipes within the city. On the other hand, the forced current method has the advantages of large protection range, wide application range, high excitation potential and output current, and low comprehensive cost, so it is suitable for anti-corrosion of long-distance pipelines or suburban pipelines. If it is applied in an urban area, it will cause interference currents that will affect other pipelines and buildings, and it will also require land acquisition or occupation of buildings, so it will bring greater difficulties in implementation. Therefore, sacrificial anode method should be used for cathodic protection of urban buried gas pipeline anticorrosion. When conditions permit, the mandatory flow protection method can also be adopted.
(1) The selection of electrical protection methods should meet the following requirements: a) Zinc anodes should not be used in occasions with soil resistivity > 20O m; b) Magnesium anodes should not be used in occasions with soil resistance > 100Ω m; c) Impressed current cathodic protection method is not limited by soil resistivity when selected.
(2) When using the sacrificial anode method, the protective effect of the selected anode should meet the following requirements: a) The ground potential should reach -0.85V or more negative; 300mV; c) When the soil or water contains sulfate-reducing bacteria and the sulfate radical content is greater than 0.5%, after electrification, the ground potential should reach -0.95V or more negative.
(3) When selecting the magnesium anode in the sacrificial anode method, it must be selected according to the requirements.
(4) When the sacrificial anode is buried, the distance from the protected gas pipeline should not be less than 0.3m, nor greater than 7m, and the buried depth should not be less than 1m, and it should be buried directly in the moist soil. The buried form can be vertical or horizontal. It is strictly forbidden to set other metal structures between the anode and the protective pipeline.
(5) Sacrificial anode detection piles and detection heads should meet the following requirements when setting up: a) The detection piles and detection heads should be installed along the main gas pipe; b) One detection pile should be installed for every 5 groups of sacrificial anodes or at least 1Km; c) The detection piles should be installed near the sacrificial anode, and should be installed along the pipeline where the soil is highly corrosive, the humidity is high, the groundwater level is high, or the pipeline insulation and anticorrosion layer is weak; a detection head.
(6) The purpose of setting the inspection pile and detection head: the detection pile is to monitor the protection potential of the sacrificial anode device. The detection head is set up to detect and grasp the protected status of the pipeline after the cathodic protection system is running.
Sacrificial anode construction requirements:
a) Embedding of the anode: Prepare and mix the filler according to the proportion, put it into a φ300×1000 cotton or burlap bag, insert the anode that has been polished with iron sandpaper and cleaned the surface into the center of the filler in time, and compact it; Wrap and tie iron wires outside the package and lay flat or vertically on the side of the pipeline at 2-3M. The buried depth should be the same as the buried depth of the pipeline and below the freezing line. Use fine original soil mixed with salt to water in layers backfill concrete. b) All connections between cables and anodes, copper noses, pipes, and reinforcing plates shall be soldered (except for the connections inside the junction box). The outer bare part of the cable must be insulated and anti-corrosion treated; the cable and the PVC protective sleeve are loosely and naturally buried, and the burial depth is the same as the pipeline burial depth. c) The cable in the protective cover must have a redundant length of 0.8M (the redundant part of the cable does not add a PVC protective sleeve), so that the junction box can be lifted out of the ground for detection parameters; the two outlet holes of the junction box Fill it with asphalt-soaked hemp silk, and then fill it with asphalt for waterproofing. d) The color of the cable connected to the pipeline should be distinguished from other cables for identification and detection. e) After the construction, installation and testing of the junction box is completed, the cover of the junction box must be tightened and waterproof. f) The embedding point of the anode must be permanently marked and filled in the “commissioning protection parameter measurement table”. The permanent mark can include surrounding buildings.
At present, people have realized that the combined use of the external anti-corrosion insulating layer of pipelines and cathodic protection is the most economical and reasonable anti-corrosion measure. This is because the anti-corrosion layer cannot be guaranteed not to be damaged in production, transportation, and construction. Therefore, it is impossible to completely isolate the pipeline from the corrosive environment and medium. Moreover, the various materials used for the anti-corrosion insulation layer have water absorption and air permeability to varying degrees. Therefore, after being buried, it will gradually absorb water and age under the action of soil solution. To maintain effective corrosion protection, it is necessary to take cathodic protection at the same time, that is, joint protection. Cathodic protection actively intervenes in the corrosion reaction. It adopts the electrochemical means of cathodic polarization to ensure the electrochemical uniformity of the protected metal body and inhibit the generation of corrosion cells. Cathodic protection is not only used for the protection of new pipes, but also for the transformation and life extension of old pipelines.