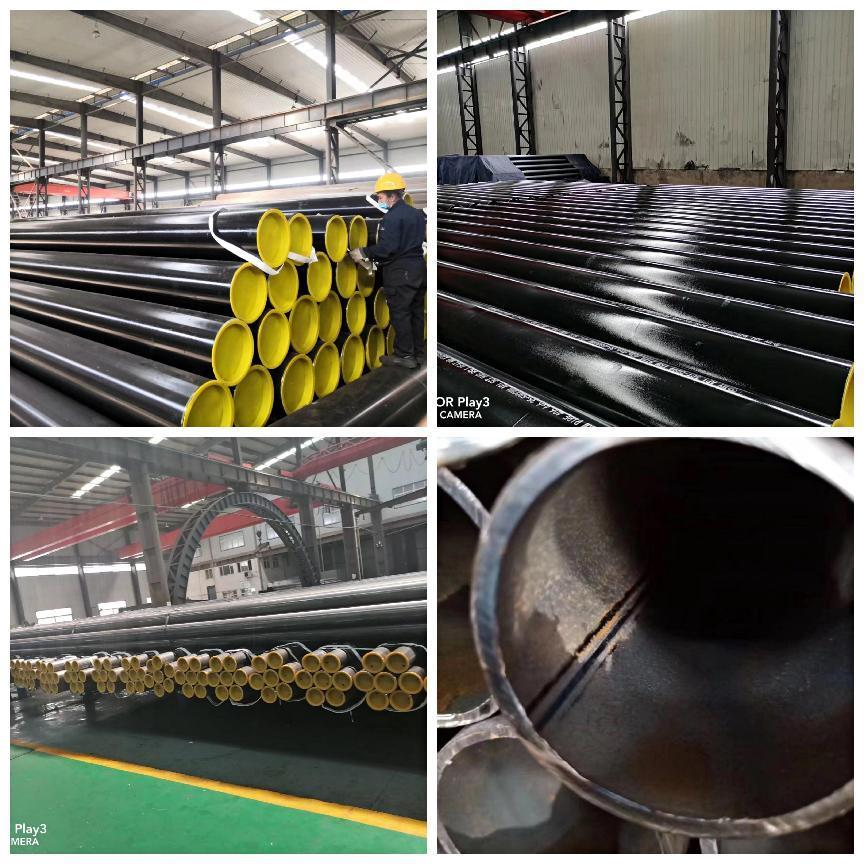
API 5L X52 and A106: Exploring the Differences – The Comparative Analysis
September 12, 2023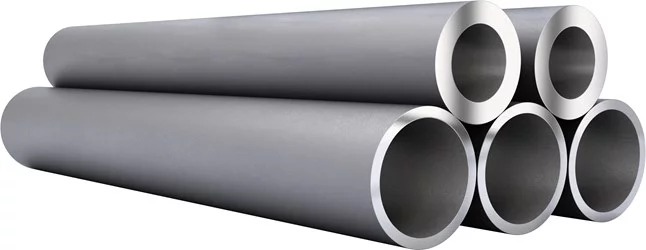
API 5L X65 Steel Pipe against Corrosion in Seawater Comparative Study of the Behavior
September 14, 2023Among the components that make up the vast network of oil and gas pipelines, steel pipes are the most crucial. They are the conduits that transport these valuable resources from the production sites to the consumption points. The quality, strength, and efficiency of these pipes are paramount, and that’s where standards such as API 5L come in. API 5L is a standard specification for line pipe by the American Petroleum Institute (API). It specifies requirements for both seamless and welded steel pipe for pipeline transportation systems in the petroleum and natural gas industries.
In this essay, we will delve into the differences between API 5L X80, X70, and L555M pipelines. We will discuss the distinct features, performance characteristics, and applications of these three types of pipelines, highlighting the differences that make each one unique.
API 5L X80 Pipeline
The API 5L X80 pipeline is one of the higher-grade pipelines under the API 5L standard. The “X” denotes its use for pipeline transportation systems in the petroleum and natural gas industries, while “80” signifies the pipe’s yield strength in ksi (kilo pounds per square inch). Yield strength refers to the pressure that the pipe can withstand without deforming permanently.
API 5L X80 pipelines are known for their high yield and tensile strength, making them suitable for use in high-pressure conditions. The high strength of API 5L X80 pipeline enables it to withstand the rigors of harsh environments and high-pressure operations commonly found in oil and gas operations.
The chemical composition of API 5L X80 pipelines often includes elements such as carbon, manganese, phosphorus, sulfur, silicon, and vanadium. This composition gives the pipeline its high strength, corrosion resistance, and excellent weldability. The weldability of API 5L X80 makes it a preferred choice for long-distance pipeline projects where welding joints are inevitable.
X80 steel plate/pipes is one mainly of Steel for large diameter pipes,API-X80 steel with good low temperature toughness was developed and the buckling behavior of X80 steel plate/pipe was investigated through large scale deformation tester.
X80 API5L Material#1.8978 | Comparison of steel grades | |
EN10208-2 | L555MB |
API 5L X80 Chemical analysis
Grades | Material number |
C max | Si max | Mn. max | P max | S max | AL min | Mo max | Ni max | Nb max |
X80 | 1.8978 | 0.08 | 0.26 | 1.75 | 0.011 | 0.0005 | 0.03 | 0.27 | 0.22 | 0.070 |
API 5L X80 Mechanical Propertities
Grade | Permissible yield point ratio |
Yield Strength MPa(min) |
Tensile Strength MPa |
Elongation % (min) |
X80 | ≤ 0.90 | 555 | 625 – 700 | 20 |
API 5L X70 Pipeline
API 5L X70 is another grade of pipeline under the API 5L standard. Like the X80, it is designed for petroleum and natural gas transportation, with the number “70” indicating its yield strength in ksi.
While the API 5L X70 pipeline has a lower yield strength compared to API 5L X80, it still offers sufficient strength for most oil and gas operations. Its chemical composition typically includes carbon, manganese, phosphorus, sulfur, silicon, nickel, chromium, and molybdenum. This composition gives the pipeline desirable properties such as good hardness, strength, and resistance to corrosion.
The API 5L X70 pipeline is often used in moderate to high-pressure environments. Its good weldability also makes it a popular choice for long-distance pipeline projects. However, due to its lower yield strength, it may not be suitable for extremely high-pressure operations where the X80 would be a better fit.
L555M Pipeline
L555M, another pipeline standard, is equivalent to API 5L X80M. The “M” denotes that the pipeline is manufactured through a thermo-mechanical process, which involves heating and cooling the steel under controlled conditions to improve its mechanical properties.
The L555M pipeline shares similar properties with the API 5L X80 pipeline, including high yield and tensile strength. However, the thermo-mechanical process used in the production of L555M imparts additional properties such as improved toughness, better weldability, and enhanced resistance to hydrogen-induced cracking (HIC).
The L555M pipeline is used in high-pressure environments that require superior mechanical properties. Its improved toughness and HIC resistance make it ideal for use in sour service applications, where the pipeline is exposed to corrosive substances such as hydrogen sulfide.
Yield Strength
The yield strength of L555M steel pipe is typically around 555 MPa (or 80,534 psi), which is quite high. Yield strength refers to the maximum stress that can be applied to the material without causing permanent deformation. This high yield strength makes L555M suitable for use in high-pressure environments.
Tensile Strength
The tensile strength of L555M steel pipe is approximately 625 – 700 MPa (or 90,679 – 101,526 psi). Tensile strength is a measure of the maximum force that the material can withstand while being stretched or pulled before breaking.
Conclusion
In summary, while API 5L X80, X70, and L555M pipelines all serve the purpose of transporting oil and gas, they differ significantly in their yield strength, chemical composition, and production process.
API 5L X80 pipeline, with its high yield strength and excellent weldability, is suitable for high-pressure operations and long-distance pipeline projects. On the other hand, API 5L X70, with slightly lower yield strength, is a good fit for moderate to high-pressure environments.
Meanwhile, the L555M pipeline, equivalent to API 5L X80M, offers enhanced toughness and HIC resistance due to its thermo-mechanical manufacturing process. It is ideal for high-pressure, sour service environments.
Understanding these differences is crucial for engineers and project managers in the oil and gas industry when selecting the most suitable pipeline for their operations. Ultimately, the choice depends on the specific requirements of the project, including the operating environment, pressure conditions, and length of the pipeline.