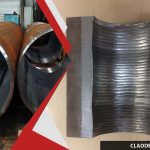
What is the Difference Between Cladding and Overlay ?
February 23, 2025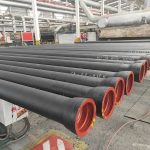
Ductile Iron Pipe for Water Supply
March 4, 2025Introduction to Ductile and Cast Iron Pipe
Ductile iron pipe and cast iron pipe are both iron-based materials widely used in piping systems, particularly for water distribution, wastewater management, and industrial applications. While they share a common heritage—both being derived from iron—they differ significantly in their composition, mechanical properties, and performance. Cast iron pipe, often referred to as gray cast iron pipe, has a long history dating back to the 17th century, while ductile iron pipe, a more modern innovation introduced in the mid-20th century, offers enhanced strength and flexibility. Understanding their differences requires examining their metallurgy, production, and practical use in detail.
What is Cast Iron Pipe?
Cast iron pipe, historically known as gray cast iron pipe, is made from an iron-carbon alloy with a high carbon content (typically 2-4%) and significant silicon (1-3%). The term “gray” comes from the appearance of its fracture surface, which reveals graphite flakes dispersed throughout the metal. These flakes give cast iron its characteristic brittleness but also contribute to its excellent casting properties, corrosion resistance, and ability to dampen vibrations.
Cast iron pipes were among the first metal pipes used for water supply systems, with early installations in Europe dating back to the 1600s. They dominated municipal water and sewer systems until the mid-20th century due to their durability and availability. The manufacturing process involves melting pig iron (a crude iron product from blast furnaces) and pouring it into molds, typically sand molds, to form pipes. The cooling process results in a rigid, brittle structure ideal for static applications but prone to cracking under stress.
What is Ductile Iron Pipe?
Ductile iron pipe, introduced in the 1940s and standardized by the 1950s, is an evolved form of cast iron. It retains a similar iron-carbon-silicon base but undergoes a critical modification: the addition of magnesium (or sometimes cerium) during the molten stage. This treatment transforms the graphite flakes of gray cast iron into spherical nodules, drastically improving the material’s ductility, strength, and toughness. The result is a pipe that combines the corrosion resistance of cast iron with mechanical properties closer to those of steel.
Ductile iron pipe was developed to address the limitations of cast iron, particularly its brittleness, making it suitable for modern, high-pressure water systems and dynamic environments. Its production involves casting followed by heat treatment (annealing) to refine its microstructure, ensuring consistent performance.
Key Differences Between Ductile and Cast Iron Pipe
The differences between ductile and cast iron pipe stem from their composition, microstructure, and resulting properties. Below is an in-depth comparison across multiple dimensions, followed by a summary table.
1. Composition and Microstructure
-
Cast Iron Pipe: Composed of iron, 2-4% carbon, and 1-3% silicon, with trace elements like sulfur and phosphorus. The carbon precipitates as graphite flakes during cooling, creating a brittle matrix. These flakes disrupt the iron’s continuity, reducing its ability to deform plastically.
-
Ductile Iron Pipe: Similar base composition (iron, 2-4% carbon, 1-3% silicon), but magnesium (typically 0.03-0.06%) is added to the molten iron. This promotes the formation of graphite nodules instead of flakes, enhancing the metal’s ability to stretch and absorb stress without fracturing.
2. Mechanical Properties
-
Strength: Cast iron has a tensile strength of 20,000-40,000 psi, while ductile iron ranges from 60,000-120,000 psi, depending on grade. Ductile iron’s higher strength makes it suitable for high-pressure systems.
-
Ductility: Cast iron is brittle, with elongation less than 1%, meaning it breaks rather than bends. Ductile iron offers 10-20% elongation, allowing it to deform under load without failing.
-
Toughness: Ductile iron’s nodular graphite structure absorbs impact energy, while cast iron’s flakes act as stress concentrators, leading to sudden failure under shock.
3. Corrosion Resistance
-
Both materials exhibit good corrosion resistance due to their iron base and the formation of a protective oxide layer in soil or water. However, ductile iron’s smoother surface (from modern manufacturing) and nodular structure may reduce localized corrosion compared to cast iron’s rougher, flake-prone surface.
4. Manufacturing Process
-
Cast Iron Pipe: Produced by traditional sand casting or centrifugal casting. Molten iron is poured into molds, cooled, and removed. The process is straightforward but results in a coarse microstructure.
-
Ductile Iron Pipe: Made via centrifugal casting, followed by magnesium treatment and annealing. The magnesium inoculation requires precise control, and annealing relieves internal stresses, enhancing uniformity.
5. Weight and Thickness
-
Cast iron pipes are typically thicker and heavier to compensate for their brittleness, often weighing 20-30% more than ductile iron pipes of the same diameter and pressure rating. Ductile iron’s strength allows for thinner walls, reducing material use and shipping costs.
6. Applications
-
Cast Iron: Historically used for water mains, sewer lines, and drainage systems. Today, it’s largely limited to non-pressure applications like soil pipes in buildings.
-
Ductile Iron: Preferred for modern water distribution, wastewater, and industrial systems under high pressure or dynamic loads.
7. Cost
-
Cast iron is generally cheaper to produce due to its simpler process, but its limitations reduce its cost-effectiveness in modern contexts. Ductile iron, though more expensive upfront, offers better long-term value due to its durability and versatility.
Here’s a tabular summary:
Property
|
Cast Iron Pipe
|
Ductile Iron Pipe
|
---|---|---|
Carbon Content
|
2-4% (graphite flakes)
|
2-4% (graphite nodules)
|
Key Additive
|
None
|
Magnesium (0.03-0.06%)
|
Tensile Strength
|
20,000-40,000 psi
|
60,000-120,000 psi
|
Elongation
|
<1% (brittle)
|
10-20% (ductile)
|
Toughness
|
Low (prone to cracking)
|
High (impact-resistant)
|
Corrosion Resistance
|
Good, but rougher surface
|
Good, smoother surface
|
Manufacturing
|
Sand or centrifugal casting
|
Centrifugal casting + Mg + annealing
|
Wall Thickness
|
Thicker, heavier
|
Thinner, lighter
|
Primary Use
|
Drainage, low-pressure systems
|
Water mains, high-pressure systems
|
Cost
|
Lower initial cost
|
Higher initial cost, better longevity
|
Manufacturing Processes in Detail
Cast Iron Pipe Production
The production of cast iron pipe relies on casting techniques refined over centuries:
-
Melting: Pig iron, scrap iron, and alloying elements (silicon, sulfur) are melted in a furnace, typically a cupola or electric furnace, at 2,500-2,800°F (1,370-1,540°C).
-
Casting: The molten iron is poured into molds. Early methods used static sand molds, while later centrifugal casting spun the mold to form uniform pipes. Centrifugal casting became standard in the 19th century, improving wall consistency.
-
Cooling: As the iron cools, graphite flakes form, giving the pipe its brittle structure. Cooling rates influence the size of these flakes—faster cooling produces finer flakes with slightly better strength.
-
Finishing: Pipes are cleaned, inspected, and sometimes lined with cement or bitumen to enhance corrosion resistance.
The process is energy-intensive but relatively simple, contributing to cast iron’s historical dominance.
Ductile Iron Pipe Production
Ductile iron pipe production builds on cast iron techniques with added steps for enhanced properties:
-
Melting: Similar to cast iron, iron is melted with carbon and silicon, but the composition is tightly controlled to ensure compatibility with magnesium.
-
Magnesium Treatment: Molten iron is treated with magnesium (via ladle inoculation or a converter process) at around 2,600°F (1,430°C). This step requires precision to avoid excessive magnesium, which can form slag or reduce nodule quality.
-
Centrifugal Casting: The treated iron is poured into a spinning mold. The centrifugal force ensures a dense, uniform wall with nodules distributed evenly.
-
Annealing: Pipes are heat-treated at 1,650-1,850°F (900-1,010°C) and slowly cooled to relieve stresses and refine the ferrite matrix around the nodules.
-
Finishing: Pipes are coated (e.g., with zinc or epoxy) and lined (e.g., with cement mortar) to meet modern standards like AWWA C151.
This process is more complex and costly but yields a superior product for demanding applications.
Mechanical Properties and Performance
Strength and Pressure Capacity
Cast iron’s tensile strength (20,000-40,000 psi) limits its use to low-pressure systems—typically below 150 psi without significant safety factors. Its compressive strength is higher (around 80,000 psi), making it suitable for static loads like gravity-fed drainage. Ductile iron, with tensile strength up to 120,000 psi, handles pressures exceeding 350 psi in water mains, often with thinner walls, as per standards like ANSI/AWWA C150/C151.
Ductility and Flexibility
Cast iron’s brittleness means it fails catastrophically under bending or impact—think of a hammer shattering a cast iron skillet. Ductile iron bends under load, absorbing energy like a steel rod. This ductility allows ductile iron pipes to flex in shifting soils or during seismic events, reducing the risk of failure.
Fatigue and Impact Resistance
Cast iron’s graphite flakes act as internal notches, initiating cracks under cyclic loading or sudden impacts. Ductile iron’s nodules distribute stress evenly, improving fatigue life and making it resilient to water hammer (pressure surges) or construction mishandling.
Corrosion and Durability
Both materials resist corrosion well in soil and water due to their iron content, which forms a passive oxide layer. Cast iron’s rougher surface and flake structure can trap moisture, accelerating localized pitting in aggressive soils (e.g., high sulfate content). Ductile iron’s smoother finish and nodular structure reduce these risks, though external coatings (zinc, polyethylene) and internal linings (cement) are standard for both to meet modern longevity expectations—often 50-100 years.
Applications and Practical Considerations
Historical Use of Cast Iron
Cast iron pipes were the backbone of urban water systems in the 19th and early 20th centuries. Cities like Paris and New York installed vast networks, some still in use today. Their thick walls and rigidity suited gravity-fed sewers and low-pressure water lines, but their weight and fragility limited upgrades as populations grew.
Modern Use of Ductile Iron
Ductile iron dominates today’s water infrastructure, from potable water distribution to fire hydrant lines. Its ability to handle pressures up to 500 psi (with safety margins) and resist soil movement makes it ideal for urban and rural systems. It’s also used in industrial settings for slurries, chemicals, and gas transport where cast iron would fail.
Installation and Maintenance
Cast iron pipes, being heavier, require more labor and equipment for installation. Their brittleness demands careful handling to avoid pre-installation damage. Ductile iron, lighter and tougher, installs faster and withstands rough handling. Maintenance for both involves replacing damaged sections, but ductile iron’s flexibility reduces the frequency of breaks.
Advantages and Disadvantages
Cast Iron Pipe
-
Advantages: Low cost, good corrosion resistance, vibration damping, long history of use.
-
Disadvantages: Brittle, heavy, limited pressure capacity, prone to cracking in dynamic conditions.
Ductile Iron Pipe
-
Advantages: High strength, ductility, impact resistance, lighter than cast iron, versatile for high-pressure systems.
-
Disadvantages: Higher initial cost, more complex manufacturing, requires protective coatings for maximum lifespan.
Aspect
|
Cast Iron Pipe
|
Ductile Iron Pipe
|
---|---|---|
Advantages
|
Cheap, corrosion-resistant, durable
|
Strong, flexible, lightweight
|
Disadvantages
|
Brittle, heavy, low pressure tolerance
|
Costlier, needs coatings
|
Metallurgical Insights
The graphite morphology—flakes in cast iron versus nodules in ductile iron—is the crux of their difference. Flakes create a heterogeneous structure where stress concentrates at sharp edges, leading to brittle failure. Nodules, being spherical, act like ball bearings in the iron matrix, allowing deformation without crack propagation. This metallurgical leap, enabled by magnesium, mirrors the difference between shattering glass and bending rubber.
Historical Context
Cast iron’s reign began with the Industrial Revolution, when cities needed reliable water and waste systems. The Versailles Palace’s fountains, fed by cast iron pipes in 1664, showcase its early success. Ductile iron emerged post-World War II as engineers sought materials to match growing urban demands and new pressure standards, with its first major use in the U.S. documented in 1955.
Performance in Extreme Conditions
In freezing climates, cast iron pipes crack when water expands, while ductile iron flexes. In earthquakes, like the 1994 Northridge event, ductile iron lines in Los Angeles bent but held, while older cast iron sections shattered. These real-world tests highlight ductile iron’s superiority in dynamic environments.
Economic Analysis
A 6-inch cast iron pipe might cost $10-15 per foot, versus $20-25 for ductile iron, but the latter’s thinner walls and longer life (50-100 years versus 30-50 for cast iron in harsh soils) offset the initial expense. Installation savings from ductile iron’s lighter weight further tip the scales.
Environmental Impact
Cast iron production emits more CO2 due to its higher material volume, while ductile iron’s efficiency reduces resource use. Both can be recycled, though ductile iron’s longevity delays scrapping, aligning with sustainable infrastructure goals.
Ductile iron pipe and cast iron pipe represent two eras of engineering. Cast iron, with its brittle, flake-laden structure, served humanity well for centuries but falters in modern, high-stress applications. Ductile iron, with its nodular graphite and steel-like properties, meets today’s needs for strength, flexibility, and durability. From composition to performance, their differences shape their roles—cast iron as a historical relic for low-demand uses, and ductile iron as the backbone of contemporary water systems.