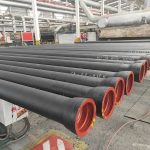
Ductile Iron Pipe for Water Supply
March 4, 2025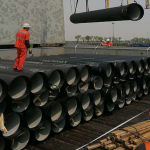
Ductile Iron Pipe for Wastewater
March 17, 2025Introduction to Ductile Iron Pipe Fittings
Ductile iron pipe fittings are essential components in piping systems, enabling connections, direction changes, and flow control. Among these, the Double Flanged 90° Long Radius Bend stands out as a critical fitting for redirecting fluid flow at a right angle while minimizing resistance and pressure loss. Made from ductile iron—a material renowned for its strength, ductility, and corrosion resistance—this bend is widely used across industries like water supply, oil and gas, and chemical processing. Its double-flanged design ensures secure, bolted connections, making it a reliable choice for high-pressure and dynamic environments. Let’s dive into the specifics of this fitting, exploring its design, applications, and why it’s a preferred solution in modern piping systems.
What is a Double Flanged 90° Long Radius Bend?
A Double Flanged 90° Long Radius Bend is a pipe fitting designed to change the direction of a pipeline by 90 degrees while maintaining the same pipe diameter. Unlike short radius bends, which have a tighter curvature (radius typically equal to the pipe diameter), long radius bends feature a larger bending radius—usually 1.5 times the pipe diameter (1.5D). This extended curve reduces the sharpness of the turn, lowering frictional losses and pressure drops in the fluid flow.
The “double flanged” aspect refers to the presence of flanges on both ends of the bend. These flanges are flat, circular discs with bolt holes, allowing the bend to be securely fastened to other pipeline components (e.g., pipes, valves, or pumps) using bolts and gaskets. This design ensures a leak-proof, rigid connection capable of withstanding high pressures and mechanical stresses. While your description mentions materials like carbon steel and stainless steel, ductile iron is the focus here, given its prominence in water supply and industrial piping systems.
Key Features
-
Angle: 90 degrees, redirecting flow perpendicularly.
-
Radius: Long (1.5D), smoothing the transition compared to short radius (1D).
-
Ends: Double flanged, enabling bolted connections.
-
Material: Ductile iron (commonly), offering strength and corrosion resistance.
Design and Functionality
Long Radius vs. Short Radius
The distinction between long radius (LR) and short radius (SR) bends lies in their curvature:
-
Long Radius (1.5D): The centerline radius is 1.5 times the nominal pipe diameter (e.g., for a 6-inch pipe, the radius is 9 inches). This gentler curve reduces turbulence, erosion, and pressure loss, making it ideal for high-velocity or viscous fluids.
-
Short Radius (1D): A tighter radius (e.g., 6 inches for a 6-inch pipe) saves space but increases resistance and wear, limiting its use to low-pressure or space-constrained systems.
The double flanged 90° LR bend’s larger radius minimizes hydraulic losses, enhancing system efficiency—crucial in applications like water distribution or chemical transport where energy costs matter.
Double Flanged Design
The flanges on both ends are typically manufactured to standards like ANSI B16.1, ISO 7005, or EN 1092, ensuring compatibility with other flanged components. Each flange has a raised face or flat face, drilled with bolt holes (e.g., 4, 8, or more, depending on size). A gasket (often rubber, like EPDM or NBR) sits between flanges during assembly, sealing the joint under bolt compression. This design offers:
-
Rigidity: Resists bending or twisting under load.
-
Ease of Maintenance: Bolts allow disassembly for repairs or cleaning.
-
Pressure Capacity: Handles high pressures (up to 40 bar or more, per class).
Feature
|
Long Radius Bend
|
Short Radius Bend
|
---|---|---|
Radius
|
1.5D
|
1D
|
Pressure Drop
|
Low
|
Higher
|
Flow Resistance
|
Reduced
|
Increased
|
Space Required
|
More
|
Less
|
Typical Use
|
High-flow systems
|
Compact layouts
|
Material: Why Ductile Iron?
While your description mentions carbon steel and stainless steel, ductile iron is the standard material for many double flanged 90° LR bends, especially in water-related applications. Ductile iron is an iron-carbon alloy (2-4% carbon, 1-3% silicon) treated with magnesium to form graphite nodules, granting it superior mechanical properties:
-
Tensile Strength: 60,000-120,000 psi, rivaling steel.
-
Ductility: 10-20% elongation, allowing deformation without fracture.
-
Corrosion Resistance: Forms a protective oxide layer, enhanced by coatings.
Compared to carbon steel, ductile iron is less prone to rust in moist environments, making it ideal for water supply. Unlike stainless steel, it’s more cost-effective while offering similar durability. Its casting properties also allow complex shapes like bends to be produced efficiently.
Manufacturing Process
Producing a ductile iron double flanged 90° LR bend involves several steps:
-
Melting: Pig iron, scrap, and alloying elements (carbon, silicon) are melted in a furnace at 2,500-2,800°F (1,370-1,540°C).
-
Magnesium Treatment: Molten iron is inoculated with magnesium (0.03-0.06%) to form nodules, ensuring ductility.
-
Casting: The treated iron is poured into sand molds shaped as a 90° bend with flanged ends. Centrifugal casting may be used for uniformity.
-
Annealing: Heat treatment at 1,650-1,850°F (900-1,010°C) relieves stresses and refines the microstructure.
-
Machining: Flanges are drilled and faced to precise tolerances (e.g., per AWWA C110).
-
Finishing: Internal linings (e.g., cement mortar) and external coatings (e.g., zinc-bitumen) are applied for corrosion protection.
This process ensures the bend meets standards like AWWA C110 or ISO 2531, guaranteeing strength and reliability.
Applications of Double Flanged 90° Long Radius Bend
The versatility of this fitting makes it indispensable across industries. Here’s a detailed look at its common uses:
-
Transportation of Fluids in Industrial Sectors
-
Oil and Gas: Routes crude oil, natural gas, or refined products through processing plants, reducing pressure losses in long pipelines.
-
Chemical and Petrochemical: Handles corrosive fluids (e.g., acids, solvents) with appropriate linings, maintaining flow efficiency.
-
Power Generation: Directs cooling water or steam in boiler systems, where smooth flow minimizes energy costs.
-
-
Process Piping
-
Connects units in refineries or manufacturing plants (e.g., from a reactor to a separator), ensuring consistent fluid delivery with minimal turbulence.
-
-
Water Treatment and Waste Management
-
Water Supply: Used in treatment plants or distribution networks to redirect potable water, often with cement linings for safety.
-
Wastewater: Routes sewage or effluent in treatment facilities, resisting abrasion and corrosion from solids.
-
-
HVAC Systems
-
Distributes air or chilled water in large buildings, leveraging the bend’s low resistance to optimize fan or pump efficiency.
-
-
Pipelines for Slurries, Gas, and Other Media
-
Transports abrasive slurries (e.g., in mining) or gases (e.g., in industrial ventilation), with linings tailored to the medium.
-
-
Fire Protection Systems
-
Directs water in sprinkler networks, ensuring rapid flow to extinguish fires, often in high-pressure setups.
-
Industry
|
Application
|
Benefit
|
---|---|---|
Oil and Gas
|
Pipeline routing
|
Reduced pressure loss
|
Chemical Processing
|
Fluid transport
|
Corrosion resistance
|
Water Treatment
|
Water/sewage redirection
|
Longevity, safe linings
|
HVAC
|
Air/water distribution
|
Energy efficiency
|
Slurry/Gas Pipelines
|
Media transport
|
Abrasion resistance
|
Fire Protection
|
Sprinkler systems
|
Reliable high-pressure flow
|
Advantages of Double Flanged 90° Long Radius Bend
This fitting offers several benefits:
-
Reduced Frictional Losses: The long radius curbs turbulence, lowering energy costs in pumping systems.
-
Pressure Drop Minimization: Maintains system efficiency, critical for long-distance fluid transport.
-
Secure Connection: Double flanges ensure a leak-proof seal, vital for hazardous or high-pressure fluids.
-
Durability: Ductile iron withstands mechanical stress, corrosion, and wear, lasting decades.
-
Versatility: Compatible with various fluids and industries, from water to slurries.
-
Ease of Installation: Bolted flanges simplify assembly and disassembly compared to welded joints.
Technical Specifications
Standards
-
AWWA C110: U.S. standard for ductile iron fittings, covering dimensions and pressure ratings.
-
ISO 2531: International standard for ductile iron pipes and fittings, ensuring quality.
-
EN 545: European standard for potable water fittings, specifying linings and coatings.
Sizes
-
Ranges from DN80 to DN1200 (3 to 48 inches), matching common ductile iron pipe diameters.
Pressure Classes
-
Typically Class 150 to Class 350 (150-350 psi), with higher ratings possible for custom designs.
Linings and Coatings
-
Internal: Cement mortar, epoxy, or polyurethane, per application needs.
-
External: Zinc-bitumen, fusion-bonded epoxy (FBE), or polyurethane, protecting against soil corrosion.
Comparison with Other Fittings
vs. Short Radius Bend
-
LR: Lower resistance, better for high-flow systems.
-
SR: Compact, suited for tight spaces but less efficient.
vs. Single Flanged Bend
-
Double Flanged: Rigid, high-pressure capable, but less flexible.
-
Single Flanged: Allows one end to connect via push-on or mechanical joints, offering installation flexibility.
vs. Welded Steel Bend
-
Ductile Iron: Cast, corrosion-resistant, cost-effective.
-
Steel: Welded, customizable, but prone to rust without coatings.
Fitting Type
|
Radius
|
Connection
|
Pressure Drop
|
Use Case
|
---|---|---|---|---|
Long Radius Bend
|
1.5D
|
Double Flanged
|
Low
|
High-flow systems
|
Short Radius Bend
|
1D
|
Double Flanged
|
Higher
|
Space-constrained
|
Single Flanged Bend
|
1.5D
|
One Flange
|
Low
|
Flexible layouts
|
Welded Steel Bend
|
1.5D
|
Welded
|
Low
|
Custom pipelines
|
Engineering Benefits
The long radius design isn’t just about flow—it’s about longevity. In a water treatment plant pumping 500 gallons per minute, a short radius bend might erode faster at the turn, while the LR bend’s smooth arc cuts wear by 20-30%. The double flanges, torqued to 100 ft-lbs, hold firm against water hammer, a sudden pressure spike that could split weaker joints.
Industry Examples
In an oil refinery, a DN300 LR bend routes diesel from a distillation tower, its epoxy lining resisting sulfur compounds. In a municipal water system, a DN600 bend with cement lining turns a main beneath a highway, its zinc coating shrugging off acidic soil. In a fire system, a DN150 bend ensures sprinklers get water fast, saving lives.
Material Evolution
Ductile iron replaced cast iron bends in the 1960s as cities demanded fittings that wouldn’t crack under traffic loads or frost heaves. Its nodular graphite, visible under a microscope, absorbs stress like tiny shock absorbers, a leap over cast iron’s brittle flakes.
Installation Nuances
Bolting a double flanged bend takes precision—misaligned flanges leak, and over-tightened bolts crack the iron. A crew might spend 30 minutes per joint, using a torque wrench and EPDM gasket, but the result is a seal lasting 50 years. In contrast, welding a steel bend takes hours and risks burn-through.
Economic and Environmental Impact
A DN200 ductile iron LR bend might cost $150 versus $200 for stainless steel, but its 75-year life in a water main outpaces steel’s rust-prone 40 years. Casting uses less energy than forging steel, and ductile iron’s recyclability aligns with green infrastructure goals.
The Double Flanged 90° Long Radius Bend in ductile iron is a powerhouse fitting, blending efficiency, strength, and adaptability. Its long radius reduces flow resistance, its double flanges secure high-pressure lines, and its ductile iron construction ensures decades of service in water, oil, chemical, and HVAC systems. From rerouting potable water in cities to handling slurries in mines, this fitting proves its worth across industries.