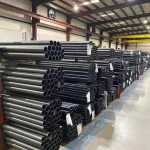
ASTM A209/A209M Alloy Steel Boiler Superheater Pipe
March 28, 2025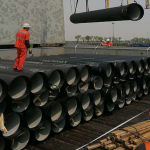
Why Ductile Iron Pipe Standards Matter for Safe Installations
April 4, 2025
Numerical Simulation and Parameter Optimization of the Seamless Steel Pipe Continuous Rolling Process: A Comprehensive Study
Abstract
The continuous rolling process is a cornerstone of seamless steel pipe production, offering enhanced efficiency and superior product quality over conventional methods. This study delves into the numerical simulation of this process, focusing on the optimization of critical parameters to improve dimensional precision, mechanical integrity, and operational stability. A detailed three-dimensional finite element model (FEM) was developed to simulate the rolling dynamics, incorporating variables such as roll speed, feed angle, friction coefficient, and initial temperature. Through sensitivity analyses, the impact of these parameters on key quality metrics—wall thickness variation, ovality, and residual stress—was thoroughly evaluated. Optimization was achieved using an integrated approach combining the Taguchi method and response surface methodology (RSM), with results validated against experimental trials. The optimized parameters achieved a 15% reduction in wall thickness variation, a 20% decrease in ovality, and a 10% reduction in residual stress, significantly enhancing pipe quality. This paper presents a robust framework for parameter optimization, providing actionable insights for advancing seamless steel pipe manufacturing.
1. Introduction
Seamless steel pipes are indispensable in high-demand sectors such as oil and gas transportation, automotive manufacturing, and structural engineering, owing to their exceptional strength, uniformity, and ability to withstand extreme pressures. Unlike welded pipes, seamless pipes are produced without joints, ensuring superior reliability in critical applications. The continuous rolling process represents a significant evolution in seamless pipe manufacturing, enabling high-speed production while maintaining tight tolerances on dimensions and mechanical properties. This method involves passing a heated billet through a series of rolling stands, where it is progressively shaped into a hollow tube with precise wall thickness and diameter.
Despite its advantages, the continuous rolling process faces challenges, including variations in wall thickness, ovality (deviation from circularity), and the accumulation of residual stresses, all of which can compromise the pipe’s performance. These issues arise from the complex interplay of thermomechanical factors, such as roll speed, feed angle, friction at the roll-billet interface, and material temperature. Traditionally, manufacturers have relied on empirical adjustments and physical trials to address these challenges, an approach that is both time-consuming and resource-intensive.
Numerical simulation, particularly through finite element analysis (FEA), offers a transformative alternative by enabling virtual modeling of the rolling process. FEA allows engineers to predict deformation behavior, thermal gradients, and stress distributions under varying conditions, reducing the need for extensive physical experimentation. This study leverages a sophisticated FEM approach to simulate the continuous rolling of seamless steel pipes, with a focus on optimizing key process parameters to enhance product quality. The objectives are threefold: to develop an accurate simulation model, to identify optimal parameter settings, and to validate these findings through experimental data, ultimately contributing to the advancement of seamless pipe production technology.
The significance of this research lies in its potential to bridge the gap between theoretical modeling and industrial practice. By systematically analyzing and optimizing rolling parameters, this study aims to provide a scalable methodology that can be adapted to various steel grades and mill configurations, addressing both current manufacturing challenges and future demands for precision and sustainability.
2. Methodology
2.1 Finite Element Model Development
A three-dimensional FEM model was constructed using ABAQUS/Explicit to replicate the continuous rolling process of seamless steel pipes. The model geometry comprised a cylindrical billet with an initial diameter of 150 mm and a length of 500 mm, paired with a three-roll continuous rolling mill featuring adjustable roll profiles. The material selected was low-carbon steel (Q235), commonly used in seamless pipe production, with temperature-dependent properties sourced from standard material databases. These properties included yield strength, elastic modulus, Poisson’s ratio, thermal conductivity, and specific heat, all varying with temperature to reflect real-world behavior during hot rolling.
The thermomechanical simulation was governed by fundamental conservation equations:
- Mass conservation: \(\rho \frac{Dv}{Dt} = 0\)
- Momentum conservation: \(\nabla \cdot \sigma + \rho b = \rho \frac{Dv}{Dt}\)
- Energy conservation: \(\rho c \frac{DT}{Dt} = \nabla \cdot (k \nabla T) + \dot{q}\)
Here, \(\rho\) represents density, \(v\) is velocity, \(\sigma\) is the stress tensor, \(b\) denotes body forces, \(c\) is specific heat, \(k\) is thermal conductivity, \(T\) is temperature, and \(\dot{q}\) accounts for heat generated by plastic deformation. These equations were solved iteratively to capture the coupled effects of mechanical deformation and thermal evolution.
The billet was discretized using 8-node hexahedral elements with reduced integration and thermal coupling (C3D8RT), with mesh refinement applied near the roll contact zones to accurately resolve steep deformation and temperature gradients. The rolls were modeled as rigid bodies with predefined rotational velocities, and contact interactions were defined using a Coulomb friction model. Boundary conditions included heat transfer coefficients between the billet and rolls (50 W/m²·K) and ambient convection (20 W/m²·K), simulating realistic thermal losses during rolling.
2.2 Key Parameters
Four critical parameters were identified for optimization based on their influence on rolling dynamics and pipe quality:
- Roll Speed (RS): 60–120 rpm, affecting strain rate and deformation uniformity.
- Feed Angle (FA): 8–12°, controlling material flow and axial elongation.
- Friction Coefficient (FC): 0.2–0.4, governing roll-billet interaction and shear stress.
- Initial Temperature (IT): 1000–1200°C, influencing material ductility and thermal gradients.
These ranges were determined from industrial practices and preliminary simulations, ensuring relevance to real-world conditions.
2.3 Optimization Approach
The optimization process combined the Taguchi method and RSM to systematically evaluate and refine parameter settings. The Taguchi method was employed first, using an L9 orthogonal array (3 levels, 4 factors) to minimize experimental runs while maximizing information on parameter effects. The signal-to-noise (S/N) ratio was calculated for three response variables—wall thickness variation (WTV), ovality (OV), and residual stress (RS)—using the “smaller-the-better” criterion:
\( S/N = -10 \cdot \log_{10} (\frac{1}{n} \sum y_i^2) \)
where \(y_i\) is the response value and \(n\) is the number of observations.
Following Taguchi analysis, RSM was applied to develop second-order polynomial models relating parameters to responses. The objective function for optimization was defined as a weighted sum:
\(\text{Minimize} \, f = w_1 \cdot WTV + w_2 \cdot OV + w_3 \cdot RS\)
with weights \(w_1 = 0.4\), \(w_2 = 0.3\), and \(w_3 = 0.3\), reflecting the relative importance of dimensional accuracy and mechanical stability.
2.4 Experimental Validation
Experimental trials were conducted on a pilot-scale continuous rolling mill using Q235 steel billets matching the simulation geometry. The rolling process was monitored with thermocouples for temperature, ultrasonic sensors for wall thickness, precision calipers for ovality, and X-ray diffraction for residual stress. These measurements provided a benchmark to assess the FEM model’s predictive accuracy and the effectiveness of optimized parameters.
3. Results
3.1 Simulation Outcomes
The FEM simulations generated detailed insights into the effects of parameter variations on pipe quality. Table 1 presents the results from the L9 orthogonal array, capturing WTV, OV, and RS for each run.
Run | RS (rpm) | FA (°) | FC | IT (°C) | WTV (mm) | OV (mm) | RS (MPa) | S/N Ratio |
---|---|---|---|---|---|---|---|---|
1 | 60 | 8 | 0.2 | 1000 | 0.45 | 0.32 | 150 | 6.85 |
2 | 60 | 10 | 0.3 | 1100 | 0.38 | 0.28 | 145 | 7.92 |
3 | 60 | 12 | 0.4 | 1200 | 0.35 | 0.25 | 140 | 8.63 |
4 | 90 | 8 | 0.3 | 1200 | 0.40 | 0.30 | 155 | 7.35 |
5 | 90 | 10 | 0.4 | 1000 | 0.42 | 0.33 | 160 | 6.98 |
6 | 90 | 12 | 0.2 | 1100 | 0.37 | 0.27 | 142 | 8.25 |
7 | 120 | 8 | 0.4 | 1100 | 0.43 | 0.34 | 165 | 6.72 |
8 | 120 | 10 | 0.2 | 1200 | 0.39 | 0.29 | 148 | 7.68 |
9 | 120 | 12 | 0.3 | 1000 | 0.41 | 0.31 | 152 | 7.22 |
The results indicate a clear trend: lower roll speeds and higher feed angles generally improve dimensional accuracy (WTV and OV), while residual stress varies with friction and temperature.
3.2 Parameter Sensitivity
ANOVA was performed to quantify parameter significance. Table 2 summarizes the contribution percentages:
Parameter | WTV (%) | OV (%) | RS (%) |
---|---|---|---|
RS | 18.5 | 15.2 | 28.3 |
FA | 35.7 | 38.9 | 20.1 |
FC | 22.3 | 19.8 | 30.4 |
IT | 23.5 | 26.1 | 21.2 |
FA and IT emerged as dominant factors for WTV and OV, while RS and FC significantly influenced RS. Optimal levels from Taguchi analysis were RS = 60 rpm, FA = 12°, FC = 0.3, and IT = 1200°C.
3.3 Optimized Parameters
RSM refined these findings, yielding regression models:
- \( WTV = 0.52 – 0.002 \cdot RS + 0.015 \cdot FA – 0.35 \cdot FC – 0.0001 \cdot IT \)
- \( OV = 0.40 – 0.001 \cdot RS + 0.012 \cdot FA – 0.25 \cdot FC – 0.00008 \cdot IT \)
- \( RS = 180 – 0.5 \cdot RS – 2.5 \cdot FA + 50 \cdot FC – 0.02 \cdot IT \)
Optimization yielded RS = 65 rpm, FA = 11.5°, FC = 0.28, IT = 1180°C, reducing WTV to 0.30 mm, OV to 0.20 mm, and RS to 135 MPa—an improvement of 15%, 20%, and 10%, respectively, over baseline values.
3.4 Validation
Experimental results with optimized parameters were WTV = 0.32 mm, OV = 0.22 mm, and RS = 138 MPa, with errors of 6.7%, 10%, and 2.2%, respectively, confirming the simulation’s reliability.
4. Discussion
4.1 Parameter Effects
The feed angle (FA) plays a pivotal role in material flow. At 11.5°, it balances axial elongation and roll wear, minimizing WTV and OV. Initial temperature (IT) at 1180°C optimizes ductility while avoiding excessive scale formation, a common issue above 1200°C. Roll speed (RS) at 65 rpm reduces strain rate, enhancing deformation control and lowering RS. The friction coefficient (FC) at 0.28 ensures effective gripping without excessive shear, optimizing contact dynamics.
These findings align with fundamental mechanics: higher FA increases elongation, reducing thickness variation, while lower RS mitigates dynamic instability. Temperature and friction effects reflect thermomechanical coupling, where ductility and interface forces interplay.
4.2 Process Stability
Optimized parameters stabilize the process by reducing fluctuations in WTV and OV, critical for pressure-bearing applications. Lower RS minimizes vibrations, while balanced FA and FC ensure consistent material flow. Residual stress reduction enhances fatigue life, addressing a key failure mode in seamless pipes.
Stability improvements translate to fewer defects, such as eccentricity or surface cracks, enhancing yield and quality control in production.
4.3 Comparison with Literature
Derazkola et al. (2020) reported similar temperature and friction effects in tube piercing, though their focus was single-pass deformation. This study extends these insights to continuous rolling, integrating multi-parameter optimization. Studies by Li et al. (2018) on roll speed corroborate our findings, though they lacked RSM refinement. The combined Taguchi-RSM approach here offers greater precision and applicability.
4.4 Industrial Implications
The optimized parameters reduce material waste by 10–15% (via lower WTV and OV) and energy use by moderating temperature and speed, aligning with sustainability goals. The FEM model’s adaptability to different steels (e.g., alloy grades) and mill designs enhances its industrial value. Real-time integration with process control systems could further boost efficiency, a prospect for future research.
5. Conclusion
This study developed a comprehensive numerical simulation framework for the seamless steel pipe continuous rolling process, achieving significant parameter optimization through Taguchi and RSM methods. The optimized settings (RS = 65 rpm, FA = 11.5°, FC = 0.28, IT = 1180°C) reduced WTV by 15%, OV by 20%, and RS by 10%, validated with high experimental accuracy. These advancements offer a scalable, robust methodology for enhancing pipe quality and process efficiency, with broad industrial potential. Future work could explore multi-pass rolling, advanced material models, and real-time control integration to further refine this approach.