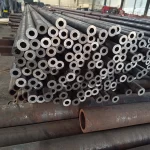
EN 10083-2 Grade C45 Carbon Steel Seamless Pipes
June 6, 2024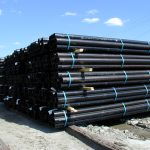
EN 10217 Pipes Special Considerations for Installation and Maintenance
June 10, 2024AISI 4140 Alloy Steel Pipe
What Is 4140 Alloy Steel?
AISI 4140 is a low-alloy steel containing chromium and molybdenum as strengthening agents. It is known for its good balance of strength, toughness, and wear resistance, making it suitable for a variety of applications.
How Is 4140 Alloy Steel Made?
4140 alloy steel is produced through the following steps:
- Melting: The raw materials (iron ore, chromium, molybdenum, and carbon) are melted in an electric arc or basic oxygen furnace.
- Refining: The molten steel is refined to remove impurities and achieve the desired chemical composition.
- Casting: The refined steel is cast into billets or blooms.
- Hot Rolling: The cast steel is hot-rolled into desired shapes and sizes, such as pipes.
- Heat Treatment: The steel undergoes heat treatment processes such as annealing, quenching, and tempering to enhance its mechanical properties.
What Are the Thermal Properties of 4140 Alloy Steel?
- Thermal Conductivity: Approximately 42.6 W/m·K at 23°C (73°F)
- Specific Heat: 477 J/kg·K at 23°C (73°F)
- Coefficient of Thermal Expansion: 12.3 µm/m·K from 20°C to 100°C (68°F to 212°F)
What Is the Carbon Content of 4140 Alloy Steel?
The carbon content of 4140 alloy steel is typically between 0.38% and 0.43%.
What Is 4140 Alloy Steel Used For?
4140 alloy steel is used in various applications, including:
- Automotive: Gears, shafts, and crankshafts
- Oil and Gas: Drill collars and tool joints
- Machinery: Spindles and couplings
- Construction: Structural components
- Tooling: Dies and molds
Machinability Rating of 4140 Alloy Steel
The machinability rating of 4140 alloy steel is around 66% of B1112 steel, making it moderately machinable with suitable equipment and techniques.
What Are the Properties of 4140 Alloy Steel?
- Tensile Strength: 655-895 MPa
- Yield Strength: 415 MPa
- Elongation: 20% in 50 mm
- Hardness: 197-237 HB (Brinell hardness)
- Impact Strength: Good toughness, even in hardened conditions
What Is the Chemical Composition of 4140 Alloy Steel?
- Carbon (C): 0.38-0.43%
- Manganese (Mn): 0.75-1.00%
- Phosphorus (P): ≤ 0.035%
- Sulfur (S): ≤ 0.040%
- Silicon (Si): 0.15-0.35%
- Chromium (Cr): 0.80-1.10%
- Molybdenum (Mo): 0.15-0.25%
What Are the Common Forms of 4140 Alloy Steel Material?
4140 alloy steel is available in various forms, including:
- Bars: Round, square, and flat bars
- Sheets and Plates: Various thicknesses
- Pipes and Tubes: Seamless and welded
- Forgings: Custom shapes and sizes
What Are Equivalents of 4140 Alloy Steel?
4140 alloy steel has several international equivalents, such as:
- EN 1.7225 (42CrMo4)
- DIN 42CrMo4
- JIS SCM440
- BS EN19
Chemical Composition of AISI 4140 Steel Material
ASTM A29/A29M | C | Si | Mn | P | S | Cr | Mo |
4140/G41400 | 0.35~0.40 | 0.20~0.35 | 0.70~0.90 | 0.025 Max | 0.025 Max | 0.80~1.10 | 0.18~0.25 |
DIN 17220, EN 10083 | C | Si | Mn | P | S | Cr | Mo |
1.7225/42CrMo4 | 0.38~0.45 | ≤0.40 | 0.60~0.90 | 0.035 Max | 0.035 Max | 0.90~1.20 | 0.15~0.30 |
GB/T 1229 | C | Si | Mn | P | S | Cr | Mo |
42CrMo | 0.38~0.45 | 0.17~0.37 | 0.50~0.80 | 0.030 Max | 0.030 Max | 0.90~1.20 | 0.15~0.25 |
JIS G4105 | C | Si | Mn | P | S | Cr | Mo |
SCM440 | 0.38~0.43 | 0.15~0.35 | 0.60~0.85 | 0.030 Max | 0.030 Max | 0.90~1.20 | 0.15~0.30 |
4. aisi 4140 alloy Steel Equivalent and Related Speciation
USA | German | Japan | China | ISO |
ASTM 29/A29M | DIN 17350 | JIS G4404 | GB/T 1229 | ISO 683/18 |
4140 | 1.7225/42CrMo4 | SCM440 | 42CrMo | 42CrMo4 |
aisi 4140 Steel Material Mechanical Properties
Mechanical properties of steel 42CrMo4 (1.7225)
Nominal diameter (mm): | to 16 | 16 – 40 | 40 – 100 | 100 – 160 | 160 – 250 | 250 – 330 | 330 – 660 |
Rm – Tensile strength (MPa) (+QT) | 1100-1300 | 1000-1200 | 900-1100 | 800-950 | 750-900 | 700 | 600 |
Nominal thickness (mm): | 0.3 – 3 |
Rm – Tensile strength (MPa) (+A) | 620 |
Rm – Tensile strength (MPa) (+AC) | 630 |
Nominal thickness (mm): | to 8 | 8 – 20 | 20 – 50 | 50 – 80 |
Rm – Tensile strength (MPa) (+QT) | 1100 | 1000 | 900 | 800 |
Rm – Tensile strength (MPa) (+C) | 720 |
Rm – Tensile strength (MPa) (+LC) | 670 |
Nominal diameter(mm): or for flat products thickness: to 8; 8-20; 20-60; 60-100; 100-160; | to 16 | 16 – 40 | 40 – 100 | 100 – 160 | 160 – 330 | 330 – 660 |
Re – Upper yield strength or Rp0.2 – 0.2% proof strength (MPa) (+QT) |
900 | 750 | 650 | 500-550 | 460-500 | 390 |
Nominal thickness(mm): | 0.3 – 3 |
Rp0.2 0.2% proof strength (MPa) (+A) | 480 |
KV – Impact energy (J) longitud., (+QT) | +20° 30-35 |
KV – Impact energy (J) transverse, (+QT) | +20° 22 |
Nominal thickness (mm): | 0.3 – 3 |
A – Min. elongation Lo = 80 mm (%) (+A) | 15 |
A – Min. elongation at fracture (%) transverse, (+QT) | 10-14 |
A – Min. elongation at fracture (%) (+C) | 4 |
A – Min. elongation at fracture (%) (+LC) | 6 |
Nominal thickness (mm): | to 16 | 16 – 40 | 40 – 100 | 100 – 160 | 160 – 250 |
A – Min. elongation Lo = 5,65 √ So (%) (+QT), round products | 10 | 11 | 12 | 13 | 14 |
Nominal diameter (mm): or for flat products thickness: to 8; 8-20; 20-60; 60-100; 100-160; | to 16 | 16 – 40 | 40 – 100 | 100 – 160 | 160 – 250 |
Z – Reduction in cross section on fracture (%) (+QT) | 40 | 45 | 50 | 50 | 55 |
Z – Reduction in cross section on fracture (%) (+AC) | 57 |
Brinell hardness (HBW): (+S) | 255 |
Brinell hardness (HBW): (+A) | 241 |
Vickers hardness ( HV): (+A) | 195 |
Vickers hardness ( HV): (+QT) | 340 – 490 |
Forging of ASTM 4140 Oil and Gas industry Steel material metal
Forging of 4140 steel should be carried out between 2200 and 1650 º F (1200 and 900 º C). The lower the finishing temperature from forging, the finer will be the grain size. This alloy steel should ideally not be forged below 1650 º F (900 º C) and should be slow cooled after forging in Oil or water.
Heat Treatment of SAE 4140 Alloy Steel
- ASTM 4140 Steel Annealing
Slowly heat to 800~8500 ºC, keep enough time, ensure heat thoroughly. then cooling in furnace to 480 ºC, then cool in air. After annealing, the hardness 92 HBS Max.
- AISI 4140 Steel Hardening & Quenching
4140 Steel is usually used at 18-22 HRc, If needs, AISI 4140 alloy steel can be hardened or Quenching by cold work. Quenching medium: oil
- Tempering Of ASTM 4140 Alloy Steel
/ ℃ tempering temperature: 205 ~ 649°C.
After tempering hardness HRC: 18-25 HRC.
Conclusion
AISI 4140 alloy steel is a versatile material known for its excellent combination of strength, toughness, and wear resistance. Its balanced chemical composition and mechanical properties make it suitable for a wide range of industrial applications, from automotive to construction. The availability of 4140 in various forms and its international equivalents ensure its adaptability and ease of use in global markets.