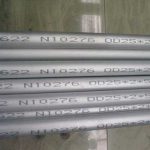
UNS N10276 Hastelloy C-276 Nickel Alloy Steel Pipes
May 21, 2024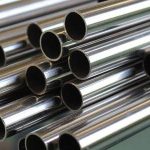
ASTM B167 UNS N06600 Nickel Alloy Steel Seamless Pipe
May 29, 2024B704 UNS N06625 UNS N08825 Nickel Alloy Steel Pipe
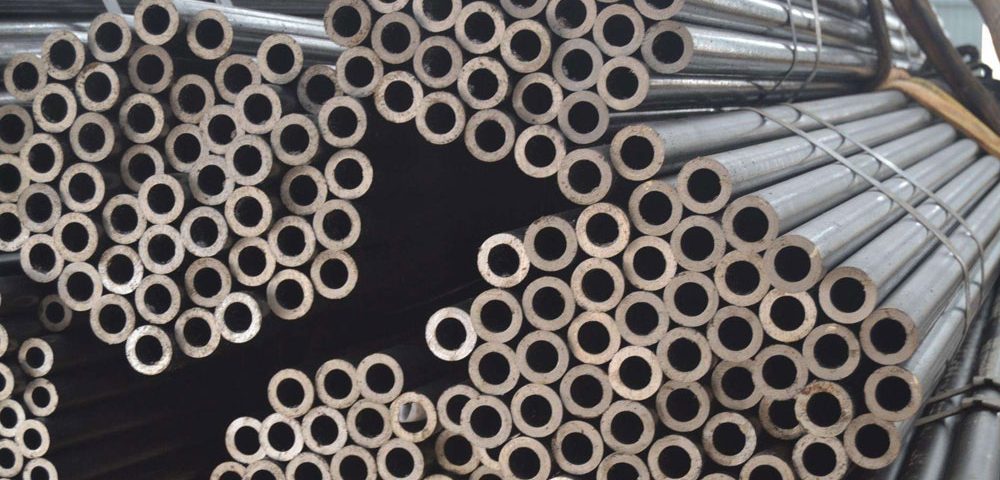
We offer UNS N06625 and UNS N08825 welded nickel alloy tubes conforming to ASTM A704 standard, UNS N06625 and UNS N08825 welded tubes are for use in boilers, heat exchangers and condensers for general corrosion prevention in either low or high-temperature environments. ASTM B704 covers welded tubes made of UNS N06625, UNS N06219 and UNS N08825 alloys in a wide range of sizes, tubes 1/8 to 5 in. (3.18 to 127 mm), inclusive, in outside diameter and 0.015 to 0.500 in. (0.38 to 12.70 mm), inclusive, in wall thickness.
B704 UNS N06625 and UNS N08825 Nickel Alloy Steel Pipe
We offer high-quality nickel alloy steel pipes conforming to ASTM B704 standards, specifically UNS N06625 and UNS N08825. These alloys are known for their excellent mechanical properties and resistance to corrosion, making them ideal for demanding applications in various industries.
UNS N06625 (Inconel 625)
UNS N06625, commonly known as Inconel 625, is a nickel-chromium-molybdenum alloy with excellent resistance to oxidation and corrosion. It is known for its high strength and toughness across a wide temperature range, making it suitable for a variety of applications, including marine, aerospace, and chemical processing industries.
Composition
Element | Percentage (%) |
---|---|
Nickel (Ni) | 58.0 min |
Chromium (Cr) | 20.0 – 23.0 |
Molybdenum (Mo) | 8.0 – 10.0 |
Columbium + Tantalum (Nb + Ta) | 3.15 – 4.15 |
Iron (Fe) | 5.0 max |
Manganese (Mn) | 0.5 max |
Silicon (Si) | 0.5 max |
Carbon (C) | 0.10 max |
Phosphorus (P) | 0.015 max |
Sulfur (S) | 0.015 max |
Mechanical Properties
Property | Value |
---|---|
Tensile Strength, min (psi) | 120,000 (827 MPa) |
Yield Strength, min (psi) | 60,000 (414 MPa) |
Elongation in 2 in. (50 mm), min (%) | 30% |
Hardness (Rockwell) | 30 – 40 HRC |
UNS N08825 (Incoloy 825)
UNS N08825, known as Incoloy 825, is a nickel-iron-chromium alloy with additions of molybdenum, copper, and titanium. This alloy offers exceptional resistance to both reducing and oxidizing acids, stress-corrosion cracking, and localized attack such as pitting and crevice corrosion.
Composition
Element | Percentage (%) |
---|---|
Nickel (Ni) | 38.0 – 46.0 |
Chromium (Cr) | 19.5 – 23.5 |
Iron (Fe) | 22.0 min |
Molybdenum (Mo) | 2.5 – 3.5 |
Copper (Cu) | 1.5 – 3.0 |
Titanium (Ti) | 0.6 – 1.2 |
Manganese (Mn) | 1.0 max |
Silicon (Si) | 0.5 max |
Carbon (C) | 0.05 max |
Phosphorus (P) | 0.03 max |
Sulfur (S) | 0.03 max |
Mechanical Properties
Property | Value |
---|---|
Tensile Strength, min (psi) | 85,000 (586 MPa) |
Yield Strength, min (psi) | 35,000 (240 MPa) |
Elongation in 2 in. (50 mm), min (%) | 30% |
Hardness (Rockwell) | 20 – 30 HRC |
Pipe Specifications
- Standard: ASTM B704
- Type: Seamless and welded pipes
- Applications: Suitable for heat exchangers, chemical processing, marine engineering, oil and gas, and aerospace industries.
Materials Testing & Quality Assurance
- Chemical Composition Testing: Ensures the material meets specified chemical composition.
- Tensile Property Testing: Verifies tensile strength, yield strength, and elongation.
- Hardness Testing: Confirms the material’s hardness range.
- Hydrostatic/Nondestructive Electric Testing: Ensures the integrity and quality of each pipe.
- Dimensional Inspection: Verifies compliance with specified dimensional tolerances.
- Visual Inspection: Detects surface defects and imperfections.
- Microstructure Analysis: Occasionally performed to confirm acceptable microstructure.
- Corrosion Resistance Testing: Ensures suitability for specific corrosive environments.