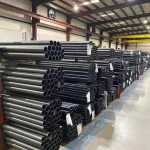
ASTM A209/A209M Legierungstahl -Stahlkessel -Superhitzerrohr
Marsch 28, 2025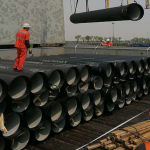
Warum duktile Eisenrohrstandards für sichere Installationen von Bedeutung machen
April 4, 2025
Numerische Simulation und Parameteroptimierung des nahtlosen Stahlrohrrohrs kontinuierlichen Rolling -Prozess: Eine umfassende Studie
Abstrakt
Der kontinuierliche Rolling -Prozess ist ein Eckpfeiler von nahtlose Stahlrohre Produktion, Verbesserte Effizienz und überlegene Produktqualität gegenüber herkömmlichen Methoden anbieten. Diese Studie befasst sich mit der numerischen Simulation dieses Prozesses, Konzentration auf die Optimierung kritischer Parameter zur Verbesserung der dimensionalen Genauigkeit, mechanische Integrität, und operative Stabilität. Ein detailliertes dreidimensionales Finite-Elemente-Modell (Fem) wurde entwickelt, um die Rolldynamik zu simulieren, Einbeziehung von Variablen wie Rollgeschwindigkeit, Futterwinkel, Reibungskoeffizient, und Anfangstemperatur. Durch Sensitivitätsanalysen, Die Auswirkungen dieser Parameter auf die wichtigsten Qualitätsmetriken - Variation der Wallendicke, Ovalität, und Reststress - wurde gründlich bewertet. Die Optimierung wurde unter Verwendung eines integrierten Ansatzes erreicht, der die Taguchi -Methode und die Reaktionsoberflächenmethode kombiniert (RSM), mit Ergebnissen, die gegen experimentelle Studien validiert wurden. Die optimierten Parameter erreichten a 15% Verringerung der Wandstärkevariation, ein 20% Abnahme der Ovalität, und a 10% Verringerung des Reststresses, erhebliche Verbesserung der Rohrqualität. In diesem Artikel wird ein robustes Framework für die Parameteroptimierung vorgestellt, Bereitstellung umsetzbarer Erkenntnisse für die Förderung nahtloser Stahlrohrherstellung.
1. Einführung
Nahtlose Stahlrohre sind in Hochdarstellungssektoren wie Öl- und Gastransport unverzichtbar, Automobilherstellung, und Bauingenieurwesen, aufgrund ihrer außergewöhnlichen Stärke, Gleichmäßigkeit, und Fähigkeit, dem extremen Druck standzuhalten. Im Gegensatz zu geschweißten Rohren, Nahlose Rohre werden ohne Gelenke hergestellt, Gewährleistung einer überlegenen Zuverlässigkeit bei kritischen Anwendungen. Der kontinuierliche Rolling -Prozess ist eine signifikante Entwicklung der nahtlosen Rohrherstellung, Aktivierung der Hochgeschwindigkeitsproduktion und gleichzeitig enge Toleranzen gegenüber Abmessungen und mechanischen Eigenschaften. Diese Methode beinhaltet die Übergabe eines erhitzten Billets durch eine Reihe von Rollständen, wo es zunehmend zu einem hohlen Rohr mit präziser Wandstärke und -durchmesser geformt wird.
Trotz seiner Vorteile, Der kontinuierliche Rolling -Prozess steht vor Herausforderungen, einschließlich Variationen der Wandstärke, Ovalität (Abweichung von der Zirkularität), und die Anhäufung von Restspannungen, All dies kann die Leistung der Pfeife beeinträchtigen. Diese Probleme ergeben sich aus dem komplexen Zusammenspiel von thermomechanischen Faktoren, wie Rollgeschwindigkeit, Futterwinkel, Reibung an der Rollbillet-Schnittstelle, und Materialtemperatur. Traditionell, Die Hersteller haben sich auf empirische Anpassungen und physische Versuche verlassen, um diese Herausforderungen zu bewältigen, Ein Ansatz, der sowohl zeitaufwändig als auch ressourcenintensiv ist.
Numerische Simulation, insbesondere durch endliche Elementanalyse (FEA), Bietet eine transformative Alternative, indem Sie die virtuelle Modellierung des Rolling -Prozesses aktivieren. FEA ermöglicht es Ingenieuren, das Verformungsverhalten vorherzusagen, Wärmegradienten, und Stressverteilungen unter unterschiedlichen Bedingungen, Reduzierung der Notwendigkeit umfassender körperlicher Experimente. Diese Studie nutzt einen ausgeklügelten FEM -Ansatz, um das kontinuierliche Rollen nahtloser Stahlrohre zu simulieren, Mit dem Fokus auf die Optimierung der wichtigsten Prozessparameter, um die Produktqualität zu verbessern. Die Ziele sind dreifach: Um ein genaues Simulationsmodell zu entwickeln, Um optimale Parametereinstellungen zu identifizieren, und um diese Ergebnisse durch experimentelle Daten zu validieren, letztendlich dazu beigetragen.
Die Bedeutung dieser Forschung liegt in ihrem Potenzial, die Lücke zwischen theoretischer Modellierung und industrieller Praxis zu schließen. Durch systematisch Analyse und Optimierung von Rolling -Parametern, Diese Studie zielt darauf ab, eine skalierbare Methodik bereitzustellen, die an verschiedene Stahlnoten und Mühlenkonfigurationen angepasst werden kann, Bewältigung der aktuellen Herstellungsherausforderungen und zukünftigen Anforderungen an Präzision und Nachhaltigkeit.
2. Methodik
2.1 Entwicklung des Finite -Elemente -Modells
Ein dreidimensionales FEM-Modell wurde unter Verwendung von ABAQUS/Explizit konstruiert, um den kontinuierlichen Rolling-Prozess von nahtlosen Stahlrohren zu replizieren. Die Modellgeometrie umfasste einen zylindrischen Billet mit einem Anfangsdurchmesser von 150 mm und eine Länge von 500 mm, gepaart mit einer kontinuierlichen Rollmühle mit drei Rollen mit verstellbaren Rollprofilen. Das ausgewählte Material war kohlenstoffarmer Stahl (Q235), häufig in der nahtlosen Rohrproduktion verwendet, mit temperaturabhängigen Eigenschaften aus Standardmaterialdatenbanken gesammelt. Diese Eigenschaften umfassten die Ertragsfestigkeit, Elastizitätsmodul, Poissonzahl, Wärmeleitfähigkeit, und spezifische Wärme, Alle variieren mit der Temperatur, um das reale Verhalten während des heißen Rollens widerzuspiegeln.
Die thermomechanische Simulation wurde von grundlegenden Erhaltungsgleichungen bestimmt:
- Massenschutz: \(\rho frac{Dv}{Dt} = 0\)
- Impulsschutz: \(\Nablas cdot sigma + \rho b = rho frac{Dv}{Dt}\)
- Energieeinsparung: \(\rho c frac{Dt}{Dt} = mon cdot (k nabla t) + \Punkt{Q}\)
Hier, \(\rho ) repräsentiert Dichte, \(v\) ist Geschwindigkeit, \(\sigma\) ist der Stress -Tensor, \(b\) bezeichnet Körperkräfte, \(c\) ist spezifische Wärme, \(k\) ist thermische Leitfähigkeit, \(T\) ist Temperatur, und \(\Punkt{Q}\) Berücksichtigt Wärme, die durch plastische Verformung erzeugt wird. Diese Gleichungen wurden iterativ gelöst, um die gekoppelten Wirkungen mechanischer Deformation und thermischer Entwicklung zu erfassen.
Der Billet wurde unter Verwendung von 8-Knoten-Hexaedralelementen mit reduzierter Integration und thermischer Kopplung diskretisiert (C3D8RT), Mit der Verfeinerung der Netzverfeinerung in der Nähe der Roll -Kontaktzonen, um eine steile Verformung und Temperaturgradienten genau aufzulösen. Die Rollen wurden als starre Körper mit vordefinierten Rotationsgeschwindigkeiten modelliert, und Kontaktinteraktionen wurden unter Verwendung eines Coulomb -Reibungsmodells definiert. Die Randbedingungen umfassten Wärmeübertragungskoeffizienten zwischen dem Billet und den Brötchen (50 W/m² · k) und Umgebungskonvektion (20 W/m² · k), Simulation realistischer thermischer Verluste während des Rollens.
2.2 Schlüsselparameter
Für die Optimierung wurden vier kritische Parameter basierend auf ihrem Einfluss auf die Rolldynamik und die Rohrqualität identifiziert:
- Rollgeschwindigkeit (Rs): 60–120 U / min, Auswirkung der Dehnungsrate und Verformungsgleichmäßigkeit.
- Futterwinkel (FA): 8–12 °, Steuerungsmaterialströmung und axiale Dehnung.
- Reibungskoeffizient (Der Vergleich zwischen den Kriechversuchsdaten und den Simulationsergebnissen bei drei verschiedenen Temperaturen ist in dargestellt): 0.2–0.4, Leitende Wechselwirkung und Scherbeanspruchung der Rollbillet.
- Anfangstemperatur (ES): 1000–1200 ° C., Beeinflussung der Material Duktilität und thermischen Gradienten.
Diese Bereiche wurden aus industriellen Praktiken und vorläufigen Simulationen bestimmt, Sicherstellung von Relevanz für die realen Bedingungen.
2.3 Optimierungsansatz
Der Optimierungsprozess kombinierte die Taguchi -Methode und RSM, um die Parametereinstellungen systematisch zu bewerten und zu verfeinern. Die Taguchi -Methode wurde zuerst angewendet, Verwenden eines orthogonalen L9 -Arrays (3 Tabelle C.61 – Zusammenfassung der NDE-Verfahren für nahtlose und geschweißte Rohrkörper, 4 Faktoren) Um experimentelle Läufe zu minimieren und gleichzeitig die Informationen zu Parameterffekten zu maximieren. Das Signal-Rausch (S / N) Das Verhältnis wurde für drei Antwortvariablen berechnet - Wallendicke Variation (Wtv), Ovalität (Ov), und Reststress (Rs)-Das Kriterium „kleinerer Teil“ verwenden:
\( S/n = -10 \cdot log_{10} (\Frac{1}{n} \sum y_i^2) \)
zeigt die experimentellen Kriechbedingungen \(y_i ) ist der Antwortwert und \(n\) ist die Anzahl der Beobachtungen.
Nach Taguchi -Analyse, RSM wurde angewendet, um Polynommodelle zweiter Ordnung zu entwickeln, die Parameter auf Antworten in Verbindung bringen. Die Zielfunktion für die Optimierung wurde als gewichtete Summe definiert:
\(\Text{Minimieren} \, f = w_1 \cdot WTV + w_2 \cdot OV + w_3 \cdot RS\)
mit Gewichten \(W_1 = 0.4\), \(w_2 = 0.3\), und \(w_3 = 0.3\), widerspiegeln die relative Bedeutung der dimensionalen Genauigkeit und der mechanischen Stabilität.
2.4 Experimentelle Validierung
Experimentelle Studien wurden an einer kontinuierlichen Rollmühle im Pilotstudium unter Verwendung von Stahlbeleg Q235 durchgeführt, die der Simulationsgeometrie entsprechen. Der Rolling -Prozess wurde mit Thermoelementen für die Temperatur überwacht, Ultraschallsensoren für die Wandstärke, Präzisionssättel für Ovality, und Röntgenbeugung für Restspannung. Diese Messungen lieferten einen Benchmark, um die prädiktive Genauigkeit des FEM -Modells und die Wirksamkeit optimierter Parameter zu bewerten.
3. Ergebnisse
3.1 Simulationsergebnisse
Die FEM -Simulationen erzeugten detaillierte Einblicke in die Auswirkungen von Parameterschwankungen auf die Rohrqualität. Tabelle 1 präsentiert die Ergebnisse aus der orthogonalen L9 -Array, WTV erfassen, Ov, und Rs für jeden Lauf.
Laufen | Rs (Drehzahl) | FA (°) | Der Vergleich zwischen den Kriechversuchsdaten und den Simulationsergebnissen bei drei verschiedenen Temperaturen ist in dargestellt | ES (° C) | Wtv (mm) | Ov (mm) | Rs (MPa) | S/N -Verhältnis |
---|---|---|---|---|---|---|---|---|
1 | 60 | 8 | 0.2 | 1000 | 0.45 | 0.32 | 150 | 6.85 |
2 | 60 | 10 | 0.3 | 1100 | 0.38 | 0.28 | 145 | 7.92 |
3 | 60 | 12 | 0.4 | 1200 | 0.35 | 0.25 | 140 | 8.63 |
4 | 90 | 8 | 0.3 | 1200 | 0.40 | 0.30 | 155 | 7.35 |
5 | 90 | 10 | 0.4 | 1000 | 0.42 | 0.33 | 160 | 6.98 |
6 | 90 | 12 | 0.2 | 1100 | 0.37 | 0.27 | 142 | 8.25 |
7 | 120 | 8 | 0.4 | 1100 | 0.43 | 0.34 | 165 | 6.72 |
8 | 120 | 10 | 0.2 | 1200 | 0.39 | 0.29 | 148 | 7.68 |
9 | 120 | 12 | 0.3 | 1000 | 0.41 | 0.31 | 152 | 7.22 |
Die Ergebnisse weisen auf einen klaren Trend hin: Niedrigere Rollgeschwindigkeiten und höhere Futterwinkel verbessern im Allgemeinen die dimensionale Genauigkeit (WTV und OV), während die Restspannung mit Reibung und Temperatur variiert.
3.2 Parameterempfindlichkeit
ANOVA wurde durchgeführt, um die Signifikanz der Parameter zu quantifizieren. Tabelle 2 fasst die Beitragsprozentsätze zusammen:
Parameter | Wtv (%) | Ov (%) | Rs (%) |
---|---|---|---|
Rs | 18.5 | 15.2 | 28.3 |
FA | 35.7 | 38.9 | 20.1 |
Der Vergleich zwischen den Kriechversuchsdaten und den Simulationsergebnissen bei drei verschiedenen Temperaturen ist in dargestellt | 22.3 | 19.8 | 30.4 |
ES | 23.5 | 26.1 | 21.2 |
FA und es wurde als dominierende Faktoren für WTV und OV, während RS und FC Rs erheblich beeinflussten. Die optimalen Ebenen aus der Taguchi -Analyse waren Rs = 60 Drehzahl, FA = 12 °, Fc = 0.3, und es = 1200 ° C.
3.3 Optimierte Parameter
RSM hat diese Ergebnisse verfeinert, Ergeben von Regressionsmodellen:
- \( Wtv = 0.52 – 0.002 \CDOT RS + 0.015 \CDOT FA – 0.35 \CDOT FC – 0.0001 \cdot it \)
- \( Ov = 0.40 – 0.001 \CDOT RS + 0.012 \CDOT FA – 0.25 \CDOT FC – 0.00008 \cdot it \)
- \( Rs = 180 – 0.5 \CDOT RS – 2.5 \CDOT FA + 50 \CDOT FC – 0.02 \cdot it \)
Die Optimierung ergab Rs = 65 Drehzahl, FA = 11,5 °, Fc = 0.28, Es = 1180 ° C., Reduzierung von WTV auf 0.30 mm, Ov zu 0.20 mm, und Rs zu 135 MPA - eine Verbesserung von 15%, 20%, und 10%, bzw., über Basiswerte.
3.4 Validierung
Experimentelle Ergebnisse mit optimierten Parametern waren WTV = 0.32 mm, Ov = 0.22 mm, und rs = 138 MPa, mit Fehlern von 6.7%, 10%, und 2.2%, bzw., Bestätigung der Zuverlässigkeit der Simulation.
4. Diskussion
4.1 Parameterffekte
Der Futterwinkel (FA) spielt eine entscheidende Rolle im Materialfluss. Bei 11,5 °, Es balanciert die axiale Dehnung und einen Rollbeschlus, Minimierung von WTV und OV. Anfangstemperatur (ES) Bei 1180 ° C optimiert die Duktilität und vermeidet gleichzeitig eine übermäßige Skalenbildung, Ein häufiges Problem über 1200 ° C. Rollgeschwindigkeit (Rs) bei 65 Drehzahl reduziert die Dehnungsrate, Verbesserung der Verformungsregelung und Senkung von Rs. Der Reibungskoeffizient (Der Vergleich zwischen den Kriechversuchsdaten und den Simulationsergebnissen bei drei verschiedenen Temperaturen ist in dargestellt) bei 0.28 sorgt für ein wirksames Greifen ohne übermäßige Schere, Optimierung der Kontaktdynamik.
Diese Erkenntnisse übereinstimmen mit der grundlegenden Mechanik: Höheres FA erhöht die Dehnung, Verringerung der Dicke Variation, während niedrigere RS dynamische Instabilität mindert. Temperatur- und Reibungseffekte spiegeln die thermomechanische Kopplung wider, wo Duktilität und Schnittstelle das Wechselspiel erzwingen.
4.2 Prozessstabilität
Optimierte Parameter stabilisieren den Prozess, indem sie Schwankungen in WTV und OV reduzieren, kritisch für druckhaltige Anwendungen. Niedriger RS minimiert Schwingungen, Während ausgeglichener FA und FC einen konsistenten Materialfluss gewährleisten. Die Reduzierung der Reststress verbessert die Lebensdauer der Müdigkeit, Ansprechen eines Schlüsselausfallmodus in nahtlosen Rohren.
Stabilitätsverbesserungen führen zu weniger Mängel, wie Exzentrizität oder Oberflächenrisse, Verbesserung der Ertrags- und Qualitätskontrolle in der Produktion.
4.3 Vergleich mit Literatur
Derustaking und Al. (2020) berichtete über ähnliche Temperatur- und Reibungseffekte beim Rohrsticher, Obwohl ihr Fokus auf Einzelpass-Verformung lag. Diese Studie erweitert diese Erkenntnisse auf kontinuierliches Rollen, Integration von Multi-Parameter-Optimierung. Studien von Li et al.. (2018) Auf Rollgeschwindigkeit bestätigen unsere Ergebnisse, Obwohl ihnen die RSM -Verfeinerung fehlte. Der kombinierte Taguchi-rsm-Ansatz bietet hier eine größere Präzision und Anwendbarkeit.
4.4 Industrielle Implikationen
Die optimierten Parameter reduzieren Materialabfälle um 10–15% (über niedrigeres WTV und OV) und Energieverbrauch durch Moderation von Temperatur und Geschwindigkeit, Ausrichtung auf Nachhaltigkeitsziele. Die Anpassungsfähigkeit des FEM -Modells an verschiedene Stähle (z.B., Legierungsnoten) und Mühlenentwürfe verbessern den industriellen Wert. Echtzeitintegration in Prozesssteuerungssysteme könnte die Effizienz weiter steigern, Eine Aussicht für zukünftige Forschung.
5. Der Vergleich zwischen den Kriechversuchsdaten und den Simulationsergebnissen bei drei verschiedenen Temperaturen ist in dargestellt
Diese Studie entwickelte ein umfassendes numerisches Simulationsrahmen für den ununterbrochenen Rolling -Prozess des nahtlosen Stahlrohrs, Erreichung einer signifikanten Parameteroptimierung durch Taguchi- und RSM -Methoden. Die optimierten Einstellungen (Rs = 65 Drehzahl, FA = 11,5 °, Fc = 0.28, Es = 1180 ° C.) reduziert WTV durch 15%, Ov durch 20%, und rs von 10%, validiert mit hoher experimenteller Genauigkeit. Diese Fortschritte bieten eine skalierbare, Robuste Methodik zur Verbesserung der Rohrqualität und der Prozesseffizienz, mit breitem industriellem Potenzial. Zukünftige Arbeit könnte das Multi-Pass-Rollen erkunden, Fortgeschrittene Materialmodelle, und Echtzeitkontrollintegration, um diesen Ansatz weiter zu verfeinern.