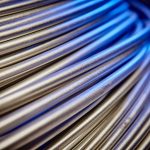
Inconel 601® Legierungstahlrohr | (UNS N06601, W.Nr. 2.4851)
April 26, 2025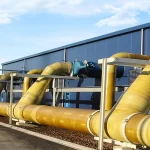
Materialdesign für 700 ℃ ultra-superkritische Hochdruckkesselrohre
Kann 6, 2025: Schweißprozess, Materialien, und Umgebung
Nahtlose Stahlrohre sind kritische Materialien mit breiten Anwendungen. Die Schweißtechnologie für nahtlose Stahlrohre ist ein Schlüsselfaktor für die Gewährleistung Pipeline Qualität und Leistung. In diesem Artikel wird das Wesentliche von erörtert nahtlose Stahlrohre Schweißtechnologie aus vier Perspektiven: Schweißverfahren, Schweißmaterialien, Schweißumgebung, und Qualitätskontrolle, Bereitstellung einer Referenz für Praktiker.
1. Schweißprozess
Das Schweißverfahren für nahtlose Stahlrohre muss den relevanten Standards entsprechen, einschließlich Schweißstrom, Stromspannung, Geschwindigkeit, und Abschirmung Gas. Vor dem Schweißen, Geräte sollten überprüft werden, um den normalen Betrieb sicherzustellen; Während des Schweißens, Die Bedingungen müssen streng kontrolliert werden, um die Schweißnahtqualität zu gewährleisten; nach dem Schweißen, Inspektionen sollten die Einhaltung der Standards überprüfen.
Gemeinsame Schweißmethoden für nahtlose Stahlrohre umfassen manuelles Lichtbogenschweißen, gasgeschirmtes Schweißen, und Löschen. Die entsprechende Methode und Parameter werden basierend auf Rohrmaterial ausgewählt, Durchmesser, Wandstärke, Groove -Typ, und Schweißposition. Im Folgenden finden Sie die Eigenschaften und wichtigen Punkte dieser Methoden.
1.1 Manuelles Lichtbogenschweißen
Manuelles Lichtbogenschweißen ist ein weit verbreitetes Verfahren, das sowohl für nahtlose als auch für geschweißte Stahlrohre geeignet ist. Es ist einfach zu bedienen, hat niedrige Ausrüstungskosten, und ist sehr anpassungsfähig. Jedoch, Es hat Nachteile wie instabile Schweißqualität, signifikanter Spritzer, große Verformung, und Anfälligkeit für Porosität und Risse.
Schlüsselpunkte für manuelles Lichtbogenschweißen:
-
Elektrodenauswahl: Wählen Sie Elektroden basierend auf Rohrmaterial, Dicke, Schweißstellung, und Typ. Elektroden mit niedrigem Wasserstoff (z.B., J507, J507FE, E7018) werden normalerweise verwendet, Mit Durchmesser im Bereich von 2,5 mm und 5 mm und Schweißströmen von 80A bis 300 A..
-
Rillenvorbereitung: Zum Hinternschweißen, Eine ordnungsgemäße Rillenvorbereitung oder -abteilung ist erforderlich. Verwenden Sie je nach Wandstärke V-förmige oder I-förmige Rillen. Rillenflächen müssen glatt und sauber sein; Defekte Rohrenden sollten nicht verschweißt werden. Rillenspezifikationen:WandstärkeGroove -TypRillenwinkelGroove Gap≤ 6 mmV60° ~ 70 °1~ 2 mm>6mmich30° ~ 40 °2~ 4mm
-
Rohrausrichtung: Ausrichten von Rohren mit Stützen oder Hebezeugen ausrichten, um eine zentrierte Positionierung ohne Verschiebung sicherzustellen. Die äußeren Oberflächen müssen bündig sein, Überprüft mit einem Stahllineer bei 200 mm von der Schweißnaht auf der gegenüberliegenden Rohroberfläche.
-
Heftschweißen: Nach Ausrichtung, Führen Sie Tackschweißungen mit einer Dicke durch, die der ersten Schweißschicht entspricht, jedoch nicht überschritten wird 70% von der Wandstärke. Die Schweißwurzel muss vollständig eingedrungen sein, mit Tackschweißungen gleichmäßig und symmetrisch platziert.
-
Schichtschweißen: Bestimmen Sie die Anzahl der Schweißschichten und die Sequenz basierend auf der Wandstärke und dem Elektrodendurchmesser. Schweißnaht von unten nach oben, Beginnend mit der Wurzel, gefolgt von Füllstoff- und Kappenschichten. Behalten Sie die richtige Schweißgeschwindigkeit und den Elektrodenwinkel für gleichmäßige, fehlerfreie Schweißnähte. Saubere Schlacke und Spritzer vor jeder Schicht und ermöglichen eine natürliche Kühlung. Initiierung und Terminierungspunkte von Staffelbogen um 20 mm oder 30 °.
1.2 Gasgeschirmtes Schweißen
Gas abgeschirmtes Schweißen verwendet Inerte oder aktive Gase, um den Bogen- und geschmolzenen Pool zu schützen, Verhinderung der Kontamination durch Sauerstoff oder Stickstoff. Es ist für nahtlose und geschweißte Stahlrohre geeignet, hochschweißige Qualität bieten, Minimale Verformung, niedriger Spritzer, und hohe Effizienz. Jedoch, Es hat höhere Ausrüstungskosten, strengere Betriebsanforderungen, und Empfindlichkeit gegenüber Umweltbedingungen.
Schlüsselpunkte für Gasabschweißen:
-
Abschirmung Gasauswahl: Wählen Sie Gasart, Durchflussmenge, und Druck basierend auf Rohrmaterial, Dicke, und Schweißtyp. Gemeinsame Gase umfassen CO₂- oder AR+Co₂ -Gemische, mit Strömungsraten von 10 l/min bis 25 l/min und Drücken von 0,2 MPa bis 0,4 MPa.
-
Schweißdrahtauswahl: Wählen Sie Draht basierend auf Rohrmaterial, Dicke, und Schweißtyp. Mit kohlenstoffarme Stahldrähte (z.B., H08MNA, H08MN2SIA) mit Durchmessern von 0,8 mm bis 1,6 mm werden normalerweise verwendet, mit umgekehrter Polarität (Werkstück negativ, Fackel positiv).
-
Rillenvorbereitung: Gleich wie manuelles Lichtbogenschweißen (Siehe Tabelle oben).
-
Rohrausrichtung: Gleich wie manuelles Lichtbogenschweißen.
-
Heftschweißen: Gleich wie manuelles Lichtbogenschweißen.
-
Schichtschweißen: Gleich wie manuelles Lichtbogenschweißen, Gewährleistung des richtigen Drahtwinkels und der Geschwindigkeit für gleichmäßige Schweißnähte.
1.3 Löschen
Das Löschen verwendet geschmolzene Metall oder Legierung als Füllstoff, um Metallteile zu verbinden, Geeignet für nahtlose und geschweißte Stahlrohre. Es bietet eine hohe Schweißqualität, Minimale Verformung, niedriger Spritzer, und hohe Effizienz, aber die gleichen Nachteile wie Gasschildschweißen.
Schlüsselpunkte für das Löschen:
-
Füllmetallauswahl: Wählen Sie den Füllstoff basierend auf Rohrmaterial, Dicke, und Schweißtyp. Kupferbasierte oder silberbasierte Füllstoffe (z.B., BCUP-2, BCUP-3, Bag-1) Mit Durchmesser von 1 mm bis 3 mm und Schmelzpunkte von 600 ° C bis 900 ° C sind häufig.
-
Flussauswahl: Verwenden Sie Anorganinsäuren oder Salze (z.B., Phosphor- oder Borsäure) als Fluss, mit 5% –10% Anwendung, gleichmäßig auf Schweißflächen oder Füllstoff überzogen.
-
Rillenvorbereitung, Rohrausrichtung, Heftschweißen, und Schichtschweißen: Gleich wie oben.
2. Schweißmaterialien
Schweißmaterialien wirken sich erheblich auf die Qualität und Leistung der Schweißnaht aus. Sie müssen mit dem Rohrmaterial übereinstimmen, zeigen gute Schweißbarkeit und mechanische Eigenschaften, und die Standards für die chemische Zusammensetzung entsprechen, mechanische Eigenschaften, und Schweißbarkeit. Materialien trocken aufbewahren, belüftet, und kühle Bedingungen, um Feuchtigkeit zu verhindern, Rost, oder Kontamination.
Gemeinsame Schweißmaterialien für nahtlose Stahlrohre enthalten Elektroden, Leitungen, und flecken füller. Ihre Merkmale und Auswahlprinzipien sind wie folgt:
2.1 Elektroden
Elektroden, verwendet im manuellen Lichtbogenschweißen, bestehen aus einem Kern (Für Strom- und Füllstoffmetall) und eine Beschichtung (Für Bogen- und Poolschutz). Sie sind einfach, kostengünstig, und anpassungsfähig, aber anfällig für instabile Qualität, Spritzer, Verformung, und Mängel.
Auswahlprinzipien:
-
Passen Sie die Elektrode an Rohrmaterial an, Typischerweise mit kohlenstoffhaltigem oder niedrigem Alloy-Stahl (z.B., J421, J422, J507, J507FE, E6013, E7018).
-
Wählen Sie Durchmesser (2.5MM - 5 mm) basierend auf Dicke; größere Durchmesser erhöhen den Strom und Effizienz, aber Risikospritzer und Deformation.
-
Verwenden Sie niedrige Wasserstoffelektroden für bessere Schweißbarkeit und mechanische Eigenschaften, Verringerung der Porosität und des Knackens.
2.2 Schweißdrähte
Schweißdrähte, Wird in gasgeschirmtem Schweißen verwendet, bestehen aus einem Kern und manchmal einem Flusskern zum Schutz. Sie bieten hohe Qualität, Minimale Verformung, niedriger Spritzer, und Effizienz, erfordern jedoch kostspielige Geräte und einen qualifizierten Betrieb.
Auswahlprinzipien:
-
Stimmen Sie Draht mit Rohrmaterial an, Typischerweise mit kohlenstoffhaltigem oder niedrigem Alloy-Stahl (z.B., H08MNA, H08MN2SIA, ER50-6, ER70S-6).
-
Wählen Sie Durchmesser (0.8mm - 1,6 mm) basierend auf Dicke; größere Durchmesser erhöhen die Effizienz, aber Risikospritzer.
-
Verwenden Sie feste oder fluxpostarische Drähte; Solid Drähte bieten bessere Eigenschaften, während fluxpostarische Drähte den Schutz verbessern und die Porosität verringern.
2.3 Füllstoffe ladern
Löhleberichte bestehen aus einem Kern (zum Beitritt) und Fluss (zur Entfernung und Benetzung von Oxid). Sie teilen die Vor- und Nachteile von Schweißdrähten.
Auswahlprinzipien:
-
Stimmen Sie Füllstoff an Rohrmaterial an, Typisch kupfer- oder silberbasiert (z.B., BCUP-2, BCUP-3, Bag-1, Bag-2).
-
Wählen Sie Durchmesser (1MM - 3 mm) basierend auf Dicke; größere Durchmesser erhöhen die Effizienz, aber Risikospritzer.
-
Verwenden Sie einen geeigneten Fluss (z.B., Phosphor- oder Borsäure) bei 5%–10%, gleichmäßig angewendet.
3. Schweißumgebung
Das Schweißumfeld wirkt sich erheblich auf Qualität und Leistung aus. Es muss Standards für die Temperatur erfüllen, Luftfeuchtigkeit, Windgeschwindigkeit, Beleuchtung, und Lärm, trocken halten, belüftet, hell, und ruhige Bedingungen, um Störungen durch extreme Hitze zu vermeiden, Luftfeuchtigkeit, Wind, Licht, oder Lärm.
Umweltanforderungen:
-
Temperatur: 5° C - 40 ° C.. Hohe Temperaturen verursachen Überhitzung, Porosität, Risse, oder durchbrennen; Niedrige Temperaturen verursachen kalte Risse, unvollständige Fusion, oder mangelnde Penetration.
-
Luftfeuchtigkeit: 40%–80%. Hohe Luftfeuchtigkeit verursacht materielle Feuchtigkeit, was zu Porosität führt, Risse, oder Oxidation; Niedrige Luftfeuchtigkeit verursacht übermäßige Trockenheit, was zu Spritzer oder Verformung führt.
-
Windgeschwindigkeit: 0.5m/s - 1,5 m/s. Stark Wind verteilt Abschirmgas, Fehler verursachen; Niedriger Wind verursacht Gasakkumulation, was zu Spritzer oder Verformung führt.
-
Beleuchtung: 300LX -500LX. Übermäßiges Licht beeinträchtigt das Sehen, Fehler verursachen; Unzureichendes Licht führt zu Mängel oder Gefahren.
-
Lärm: 60DB -80DB. Übermäßige Lärm beeinträchtigen das Gehör, Fehler verursachen; Niedriger Rauschen reduziert den Fokus, was zu Mängel oder Gefahren führt.
4. Isolierrohr
Qualitätskontrolle ist entscheidend für die Gewährleistung der Qualität und Leistung der Schweißnaht, Einhaltung von Standards für die Planung, Inspektion, und Bewertung. Es sollte vorher durchgeführt werden, während, und nach dem Schweißen.
Qualitätskontrollkomponenten:
-
Qualitätsplanung: Spezifikationen und Maßnahmen für Schweißprozesse entwickeln, Materialien, Ausrüstung, Personal, Umfeld, Inspektion, und Bewertung auf der Grundlage der Projektanforderungen. Vor dem Schweißen formulieren, implementieren während, und Bewertung nach.
-
Qualitätsinspektion: Tests durchführen, Analyse, und Bewertung von Schweißnähten vorher, während, und nach dem Schweißen durch qualifiziertes Personal oder Dritte. Zu den Methoden gehören nicht zerstörerische Tests, zerstörerische Tests, und metallographische Analyse, Beurteilung des Schweißaussehens, Maße, gestalten, Mängel, Struktur, und mechanische Eigenschaften. Feedback -Ergebnisse für Korrekturen umgehend.
-
Qualitätsbewertung: Klassifizieren und Zertifizierung der Schweißqualität anhand der Inspektionsergebnisse, Halten Sie sich an national ein, Industrie, oder Unternehmensstandards. Bewerten Sie Schweiß- und Projektqualitätsnoten und Akzeptanzbedingungen. Feedback -Ergebnisse für Korrekturen.
5. Der Vergleich zwischen den Kriechversuchsdaten und den Simulationsergebnissen bei drei verschiedenen Temperaturen ist in dargestellt
Nahtloses Stahlrohrschweißen ist eine vielfältige Technologie mit Prozessen, Materialien, Umgebungen, und Qualitätskontrolle. Das Beherrschen dieser Elemente ist entscheidend für die Verbesserung der Qualität und Leistung der Schweißnaht, Sicherheit und Zuverlässigkeit der Pipeline sicherstellen. In diesem Artikel wurden wichtige Punkte in diesen vier Bereichen beschrieben, in der Hoffnung, wertvolle Erkenntnisse zu liefern.