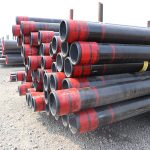
ASTM A333M Erdöl-Crackrohr
November 7, 2024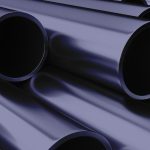
Unterschied zwischen Inconel-Legierung 600 und Incoloy-Legierung 800 Stahlrohre
November 20, 2024Schweißen von Rohrbutterungen aus Nickellegierungsstahl und Edelstahlrohren: Ein umfassender Leitfaden
Einführung
Schweißen unterschiedlicher Metalle, wie Rohre aus Nickellegierungsstahl und Edelstahlrohre, ist eine häufige Anforderung in Branchen wie der Energieerzeugung, Öl und gas, Petrochemie, und Kernenergie. Diese Metalle werden oft mit einer Technik namens Buttering verbunden, Dabei wird vor der endgültigen Schweißnaht eine Schicht kompatiblen Füllmaterials auf eines der Grundmetalle aufgetragen. Dieser Prozess trägt dazu bei, Probleme im Zusammenhang mit dem Schweißen unterschiedlicher Metalle zu mindern, wie z. B. eine Fehlanpassung der Wärmeausdehnung, Korrosion, und Rissbildung.
In diesem umfassenden Leitfaden, Wir werden den Prozess des Schweißens von Nickel untersuchen Legierungsstahlrohr Butter in Edelstahlrohren. Wir werden die Schweißtechniken behandeln, Füllmaterialien, Vorbereitungsschritte, und Nachbehandlungen, die für eine erfolgreiche Schweißung erforderlich sind. zusätzlich, Wir stellen Ihnen detaillierte Tabellen zur chemischen Zusammensetzung zur Verfügung, mechanische Eigenschaften, und Schweißparameter für verschiedene Nickellegierungen und Edelstähle.
Warum das Buttern beim Schweißen unterschiedlicher Metalle notwendig ist
Beim Schweißen unterschiedlicher Metalle wie Nickellegierungen und Edelstahl, Aufgrund der Unterschiede in ihrer chemischen Zusammensetzung ergeben sich mehrere Herausforderungen, Wärmeausdehnungskoeffizienten, und Korrosionsbeständigkeit. Diese Unterschiede können zu Problemen führen wie::
- Knacken: Die unterschiedlichen Wärmeausdehnungsraten von Nickellegierungen und Edelstahl können beim Erhitzen und Abkühlen zu Spannungen führen, Dies führt zu Rissen in der Schweißnaht.
- Korrosion: Unterschiedliche Metalle können galvanische Zellen bilden, Dies führt zu beschleunigter Korrosion an der Schweißverbindung.
- Verdünnung: Das Mischen unterschiedlicher Metalle beim Schweißen kann zu einer Schweißnaht mit unerwünschten mechanischen Eigenschaften oder Korrosionsbeständigkeit führen.
Um diese Herausforderungen zu meistern, Es wird eine Technik namens Buttering verwendet. Beim Buttern wird eine Schicht aus verträglichem Füllmaterial aufgetragen (meist eine Nickelbasislegierung) am Edelstahlrohr angebracht, bevor die endgültige Schweißung erfolgt. Diese Schicht fungiert als Puffer, Durch die Schaffung einer verträglicheren Grenzfläche zwischen den beiden unterschiedlichen Metallen wird das Risiko von Rissen und Korrosion verringert.
Nickellegierungen und rostfreie Stähle: Ein Überblick
Nickellegierungen
Nickellegierungen sind für ihre hervorragende Korrosionsbeständigkeit bekannt, Hochtemperaturfestigkeit, und Oxidationsbeständigkeit. Sie werden häufig in Branchen eingesetzt, in denen Materialien erforderlich sind, die rauen Umgebungen standhalten, wie chemische Verarbeitung, Luft-und Raumfahrt, und Stromerzeugung.
Zu den gängigen Nickellegierungen, die in Rohrleitungssystemen verwendet werden, gehören::
- Inconel 600: Eine Nickel-Chrom-Legierung mit ausgezeichneter Beständigkeit gegen Oxidation und Korrosion bei hohen Temperaturen.
- Inconel 625: Eine Nickel-Chrom-Molybdän-Legierung, die für ihre hohe Festigkeit und Beständigkeit gegen Lochfraß und Spaltkorrosion bekannt ist.
- Monel 400: Eine Nickel-Kupfer-Legierung mit guter Korrosionsbeständigkeit in einer Vielzahl von Umgebungen, einschließlich Meerwasser und sauren Umgebungen.
- Hastelloy C-276: Eine Nickel-Molybdän-Chrom-Legierung mit hervorragender Beständigkeit gegenüber einer Vielzahl korrosiver Medien, einschließlich starker Säuren und Chloridumgebungen.
Rostfreier Stahl
Edelstähle sind Legierungen auf Eisenbasis, die mindestens enthalten 10.5% Chrom, was ihnen ihre charakteristische Korrosionsbeständigkeit verleiht. Rostfreie Stähle werden häufig in Branchen wie der Lebensmittelverarbeitung verwendet, Arzneimittel, sowie Öl und Gas aufgrund ihrer Korrosionsbeständigkeit und einfachen Herstellung.
Zu den häufigsten in Rohrleitungssystemen verwendeten Edelstahlsorten gehören::
- 304 Edelstahl: Ein austenitischer Edelstahl mit guter Korrosionsbeständigkeit und ausgezeichneter Formbarkeit.
- 316 Edelstahl: Ein austenitischer Edelstahl mit Molybdänzusatz für verbesserte Beständigkeit gegen Lochfraß und Spaltkorrosion.
- 321 Edelstahl: Ein austenitischer Edelstahl, der mit Titan stabilisiert ist, um die Ausfällung von Karbiden beim Schweißen zu verhindern.
- Duplex-Edelstahl: Ein rostfreier Stahl mit einer gemischten Mikrostruktur aus Austenit und Ferrit, Bietet hohe Festigkeit und ausgezeichnete Beständigkeit gegen Spannungsrisskorrosion.
Schweißverfahren für die Butterung von Nickellegierungsstahlrohren und Edelstahlrohren
Schritt 1: Diese Informationen haben die hohe Festigkeit und Duktilität des Materials bestätigt
Der erste Schritt im Schweißprozess ist die Auswahl der geeigneten Nickellegierungs- und Edelstahlmaterialien. Die Wahl der Materialien hängt von der konkreten Anwendung ab, Betriebsumgebung, und die für die endgültige Schweißverbindung erforderlichen Eigenschaften.
Beispielsweise, wenn die Anwendung hohe Temperaturen und korrosive Umgebungen beinhaltet, Inconel 625 Als Nickellegierung kann gewählt werden, während 316 Für das Edelstahlrohr kann Edelstahl gewählt werden.
Schritt 2: Auswahl des Füllmaterials
Der beim Buttern und Schweißen verwendete Zusatzwerkstoff spielt eine entscheidende Rolle für den Erfolg der Schweißung. Das Füllmaterial muss sowohl mit der Nickellegierung als auch mit dem Edelstahl kompatibel sein, um Probleme wie Rissbildung zu vermeiden, Korrosion, und Verdünnung.
Zu den üblichen Füllmaterialien, die zum Schweißen von Nickellegierungen an Edelstahl verwendet werden, gehören::
- ERNiCr-3: Ein Nickel-Chrom-Zusatzwerkstoff, der üblicherweise zum Schweißen von Inconel verwendet wird 600 zu Edelstahl.
- ERNiCrMo-3: Ein Nickel-Chrom-Molybdän-Zusatzwerkstoff, der zum Schweißen von Inconel verwendet wird 625 und Hastelloy C-276 bis Edelstahl.
- ERNiCu-7: Ein Nickel-Kupfer-Zusatzwerkstoff, der zum Schweißen von Monel verwendet wird 400 zu Edelstahl.
Schritt 3: Das Edelstahlrohr mit Butter bestreichen
Beim Buttering-Verfahren wird vor der endgültigen Schweißung eine Schicht Füllmaterial auf das Edelstahlrohr aufgetragen. Diese Schicht fungiert als Übergangszone zwischen dem Edelstahl und der Nickellegierung, Reduzierung des Risikos von Rissen und Korrosion.
Butterverfahren:
- Oberflächenvorbereitung: Die Oberfläche des Edelstahlrohres muss gründlich gereinigt werden, um eventuelle Verunreinigungen zu entfernen, wie Öl, Fett, oder Oxidschichten. Dies kann mit mechanischen Methoden erfolgen (z.B., reibend) oder chemische Reinigung.
- Vorheizen: Abhängig von der Dicke der Materialien und den spezifischen Legierungen, die geschweißt werden, Um das Risiko einer Rissbildung zu verringern, kann ein Vorwärmen erforderlich sein. Die Vorwärmtemperaturen liegen typischerweise zwischen 100 °C und 200 °C.
- Buttering Pass: Eine Schicht Füllmaterial (z.B., ERNiCrMo-3) wird mittels eines Schweißverfahrens wie GTAW auf das Edelstahlrohr aufgebracht (Gas-Wolfram-Lichtbogenschweißen) oder SMAW (Lichtbogenschweißung). Die Butterschicht sollte dick genug sein, um eine Vermischung mit dem Grundmetall während der endgültigen Schweißung zu verhindern.
- Inspektion: Nachdem die Butterschicht aufgetragen wurde, Es sollte auf Mängel wie Risse untersucht werden, Porosität, oder unvollständige Fusion. Zerstörungsfreie Prüfung (NDT) Um die Qualität der Butterschicht sicherzustellen, können Methoden wie Ultraschallprüfung oder Röntgenprüfung eingesetzt werden.
Schritt 4: Schweißen der Nickellegierung an den gebutterten Edelstahl
Sobald die Butterschicht auf das Edelstahlrohr aufgetragen wurde, Die endgültige Schweißung kann zwischen dem Nickellegierungsrohr und dem gebutterten Edelstahlrohr erfolgen.
Schweißverfahren:
- Schweißprozess: Der Schweißprozess zum Verbinden der Nickellegierung mit dem gebutterten Edelstahlrohr kann je nach Material und Anwendung variieren. Zu den gängigen Schweißverfahren gehören::
- GTAW (WIG-Schweißen): Bietet eine präzise Kontrolle über die Schweißnaht und wird häufig für hochwertige Schweißnähte in kritischen Anwendungen verwendet.
- SMAW (Stabschweißen): Ein vielseitiges Verfahren, das zum Schweißen in verschiedenen Positionen und Umgebungen eingesetzt werden kann.
- GMAW (MIG-Schweißen): Geeignet für höhere Schweißgeschwindigkeiten und dickere Materialien.
- Füllmaterial: Das gleiche Füllmaterial, das auch zum Buttern verwendet wird (z.B., ERNiCrMo-3) Für die endgültige Schweißung sollte ein Metall verwendet werden, um die Kompatibilität zwischen der Nickellegierung und der gebutterten Schicht sicherzustellen.
- Schweißparameter: Die Schweißparameter, wie zum Beispiel Schweißstrom, Stromspannung, und Reisegeschwindigkeit, sollte sorgfältig kontrolliert werden, um Überhitzung und Verzerrung zu vermeiden. Die folgende Tabelle enthält typische Schweißparameter für GTAW- und SMAW-Verfahren:
Schweißprozess | Füllmaterial | Aktuell (A) | Stromspannung (V) | Reisegeschwindigkeit (mm/min) | Vorheiztemperatur (° C) | Zwischenlagentemperatur (° C) |
---|---|---|---|---|---|---|
GTAW (WIG) | ERNiCrMo-3 | 100-150 | 10-14 | 100-150 | 100-200 | 150-250 |
SMAW (Stock) | ERNiCrMo-3 | 80-120 | 20-24 | 80-120 | 100-200 | 150-250 |
GMAW (MIG) | ERNiCrMo-3 | 150-200 | 20-25 | 150-200 | 100-200 | 150-250 |
- Wärmebehandlung nach dem Schweißen (PWHT): Abhängig von den Materialien und der Anwendung, Möglicherweise ist eine Wärmebehandlung nach dem Schweißen erforderlich, um Restspannungen abzubauen und die mechanischen Eigenschaften der Schweißnaht zu verbessern. PWHT-Temperaturen liegen typischerweise zwischen 600 °C und 800 °C, Abhängig von den spezifischen Legierungen, die geschweißt werden.
Schritt 5: Inspektion und Prüfung
Nachdem der Schweißvorgang abgeschlossen ist, Die Schweißverbindung muss inspiziert und getestet werden, um ihre Qualität und Integrität sicherzustellen. Zu den gängigen Inspektionsmethoden gehören::
- Visuelle Inspektion: Die Schweißverbindung wird visuell auf Oberflächenfehler wie Risse überprüft, Porosität, oder unvollständige Fusion.
- Zerstörungsfreie Prüfung (NDT): Methoden wie Ultraschallprüfung (OUT), radiologische Prüfung (RT), oder Farbeindringprüfung (PT) kann verwendet werden, um innere Fehler in der Schweißverbindung zu erkennen.
- Mechanische Prüfung: Mechanische Tests wie Zugversuche, Biegeprüfung, oder es können Schlagprüfungen durchgeführt werden, um die Festigkeit und Zähigkeit der Schweißverbindung zu bewerten.
Herausforderungen beim Schweißen von Nickellegierungen an Edelstahl
Das Schweißen von Nickellegierungen mit Edelstahl stellt aufgrund der Unterschiede in ihrer chemischen Zusammensetzung und ihren physikalischen Eigenschaften mehrere Herausforderungen dar. Zu den größten Herausforderungen gehören::
1. Nichtübereinstimmung der Wärmeausdehnung
Nickellegierungen und rostfreie Stähle haben unterschiedliche Wärmeausdehnungskoeffizienten, die beim Aufheizen und Abkühlen zu thermischen Spannungen führen können. Diese Spannungen können zu Rissen in der Schweißverbindung führen, insbesondere bei dickwandigen Rohren oder komplexen Geometrien.
2. Verdünnung
Beim Schweißen, die unedlen Metalle (Nickellegierung und Edelstahl) kann sich mit dem Füllmaterial vermischen, was zu einer Verwässerung führt. Dies kann zu einer Schweißnaht mit unerwünschten mechanischen Eigenschaften oder Korrosionsbeständigkeit führen. Die Butterschicht trägt dazu bei, die Verdünnung zu reduzieren, indem sie eine verträglichere Grenzfläche zwischen den beiden unterschiedlichen Metallen schafft.
3. Korrosion
Durch das Schweißen unterschiedlicher Metalle können galvanische Zellen entstehen, Dies führt zu beschleunigter Korrosion an der Schweißverbindung. Die Verwendung eines kompatiblen Füllmaterials (z.B., ERNiCrMo-3) und geeignete Nachbehandlungen nach dem Schweißen können helfen, dieses Problem zu mildern.
4. Knacken
Während oder nach dem Schweißen kann es aufgrund thermischer Spannungen zu Rissen kommen, Verdünnung, oder Wasserstoffversprödung. Vorheizen, kontrollierte Schweißparameter, und eine Wärmebehandlung nach dem Schweißen kann dazu beitragen, das Risiko von Rissen zu verringern.
Tabelle: Chemische Zusammensetzung gängiger Nickellegierungen und rostfreier Stähle
Material | Nickel (NI) | Chrom (CR) | Molybdän (Mo) | Eisen (Fe) | Kupfer (Cu) | Kohlenstoff (C) | Andere Elemente |
---|---|---|---|---|---|---|---|
Inconel 600 | 72 mir | 14-17 | – | 6-10 | – | 0.15 max | MN, Si, S |
Inconel 625 | 58 mir | 20-23 | 8-10 | 5 max | – | 0.10 max | NB, MN, Si |
Monel 400 | 63 mir | – | – | 2.5 max | 28-34 | 0.30 max | MN, Si, S |
Hastelloy C-276 | 57 mir | 14.5-16.5 | 15-17 | 4-7 | – | 0.01 max | W, MN, Si, S |
304 Edelstahl | 8-10.5 | 18-20 | – | Balance | – | 0.08 max | MN, Si, P, S |
316 Edelstahl | 10-14 | 16-18 | 2-3 | Balance | – | 0.08 max | MN, Si, P, S |
321 Edelstahl | 9-12 | 17-19 | – | Balance | – | 0.08 max | TI, MN, Si, P, S |
Duplex-Edelstahl | 4.5-6.5 | 22-23 | 3-3.5 | Balance | – | 0.03 max | MN, Si, P, S |
Der Vergleich zwischen den Kriechversuchsdaten und den Simulationsergebnissen bei drei verschiedenen Temperaturen ist in dargestellt
Das Schweißen von Rohren aus nickellegiertem Stahl mit Rohren aus rostfreiem Stahl mithilfe der Buttering-Technik ist ein komplexer Prozess, der sorgfältige Aufmerksamkeit bei der Materialauswahl erfordert, Füllmaterial, Schweißparameter, und Nachbehandlungen nach dem Schweißen. Durch Auftragen einer Butterschicht aus verträglichem Spachtelmaterial, die Gefahr von Rissen, Korrosion, und die Verdünnung kann deutlich reduziert werden, Dadurch entsteht eine hochwertige Schweißverbindung.
Der Erfolg der Schweißung hängt von der richtigen Oberflächenvorbereitung ab, Vorheizen, kontrollierte Schweißparameter, und gründliche Inspektion und Prüfung. Indem Sie die in diesem Leitfaden beschriebenen Richtlinien und Best Practices befolgen, Sie können eine zuverlässige und dauerhafte Schweißnaht zwischen Nickellegierungs- und Edelstahlrohren gewährleisten.
Weitere Informationen oder Unterstützung beim Schweißen unterschiedlicher Metalle, Wenden Sie sich an einen Schweißingenieur oder Materialspezialisten, der Sie fachkundig zu den spezifischen Anforderungen Ihres Projekts beraten kann.