Aluminium Messing Rohre Prüfbericht
Juni 29, 2018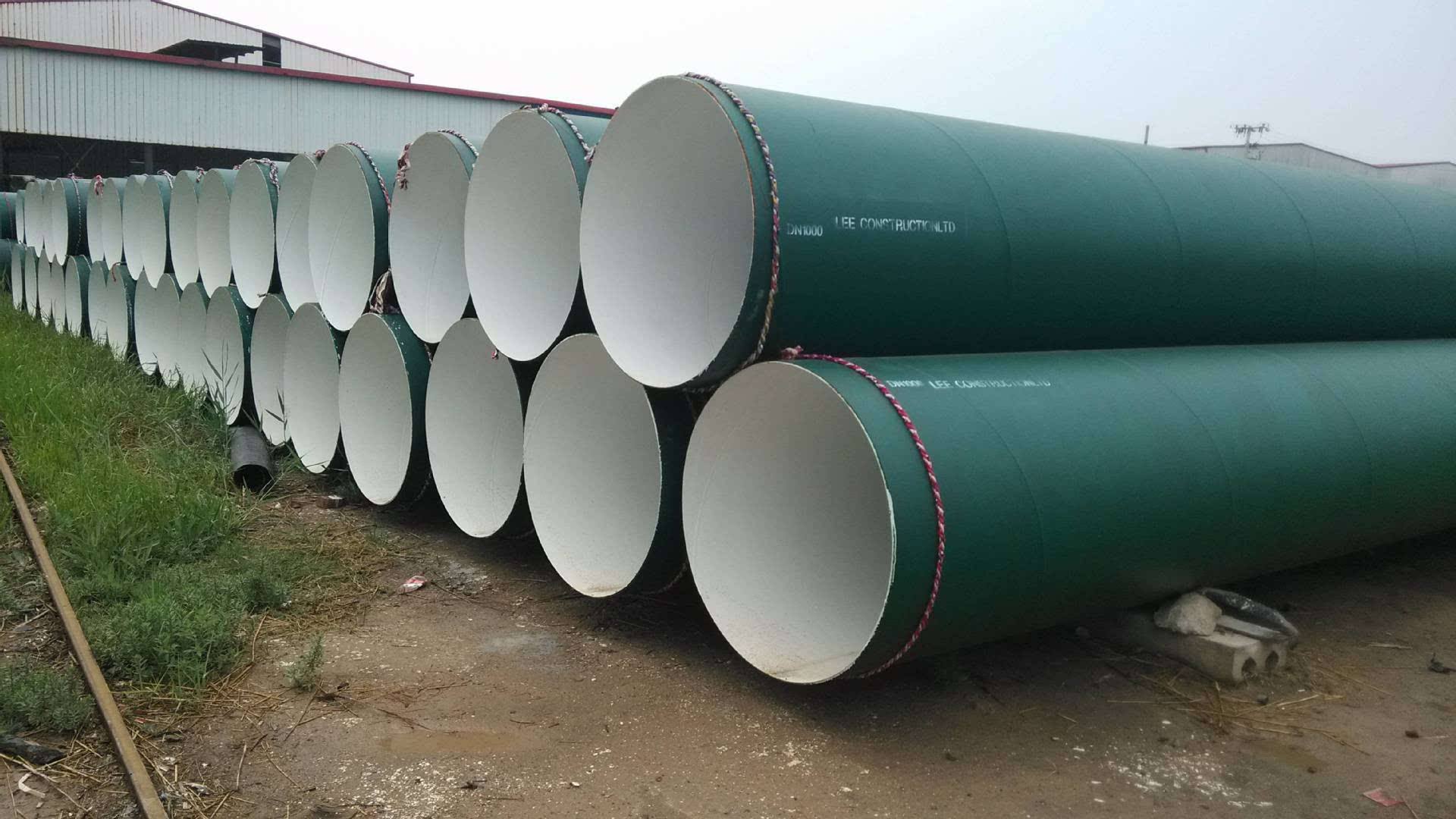
Stahlrohr-Beschichtungslösung
Juli 19, 2018Fügeverfahren und Rohr INSTALLATION
Dieses Datenblatt werden die häufigsten Fügeverfahren des Stahlwasserleitungen und die wichtigsten Phasen der Installation.
Anwendungen • Wasserleitungen • Abwasserrohre
1. Graben, Fundament und Befüllungs
Der Graben wird gegraben breit genug, gemäß Fig 1, um genügend Arbeitsfläche auf beiden Seiten des Pipeline. Falls benötigt, eine Ausgleichsschicht auf dem Boden des Grabens gelegt. Es ist zumindest zu sein 150 mm Dicke von der äußeren Unterseite des Rohres gemessen (siehe Abb. 2). der max. erlaubt Korngröße des Natursteinmaterials Nivellieren ist immer 60 mm, während des max. erlaubt Korngröße des mineralischen Zuschlagstoffen in direktem Kontakt mit der Rohrbeschichtung ist 32 mm. Keine scharfkantigen Steine sind in der Ausgleichsschicht erlaubt, und gefrorenes Nivellierungsmaterial darf nicht verwendet werden. Wenn der Untergrund weich, die Pipeline auf dem Gitter werden müssen gegründet oder sogar auf Pfählen.
Die gesamte Länge der Unterseite jeden Rohr muss auf dem Boden des Grabens ruht mit Ausnahme einer Strecke von etwa einem halben Meter von der Hülse in beiden Richtungen (siehe Abb. 3). Jedes Rohr der installierten Leitung muss tragen, zusätzlich zu ihrem Eigengewicht, auch das Gewicht des Wassers und die Verfüllung, sowie andere mögliche externe Lasten.
Wenn die Unterstützung Bohlen oder dergleichen in der Installation eine erdüberdeckten Pipeline verwendet, sie müssen vor dem Befüllen in dem Graben entfernt werden. Die anfängliche Füllmaterials müssen die gleichen Anforderungen wie die Ausgleichsschicht treffen und verdichtbaren Sand moräne oder moräne Kies um die untere Hälfte des Rohrs sein muß - Schluff und Ton kann auch um die obere Hälfte verwendet werden,. Füllen Material darf nicht auf ein Rohr fallen gelassen werden, so dass er sich bewegt oder beschädigt wird. Es ist darauf zu möglichst gleichmäßig auf beiden Seiten des Rohres und Stampf unterhalb und an den Seiten plaziert die Rohrbeschichtung Betreuung, und schließlich verdichtet.
Figur-1-Trench
Figur 2.-Filling-of-Graben
Figur-3-Trench-bottom-at-Hülse
Das Hauptprinzip eines Grabens in Füllen ist, dass Rohre, insbesondere Gelenke, eine ausreichende seitliche Abstützung gegen Kopflasten müssen. Deshalb, die Erstbefüllung entlang der Seiten wird mechanisch auf halber Höhe des Rohres in den Schichten von etwa Stampf 30 cm mindestens 90% Proctor Dichte, gewährleisten, jedoch, daß der Verdichtungs hebt nicht das Rohr up.
Der Verdichtungsgrad muss durch Messungen bestimmt werden,. Die Vibrationsplatte zu keinem Zeitpunkt ein Rohr berühren oder Montage Beschädigung Beschichtung zu vermeiden. Mechanische Verdichtung über das Rohr nur erlaubt, nachdem 50 cm Füllung wird auf der Oberseite platziert (siehe Abb. 2). Nach der endgültigen Füllung, es muss mindestens einen Meter dicker eine Schicht von Füllmaterial sein,, von der Spitze des Rohres gemessen, enthält keine Steine oder Geröll mehr als 300 mm Durchmesser. Jeder Stein oder Felsblock in dem endgültigen Füllmaterials muß nicht näher an das Rohr angeordnet sein als sein Durchmesser. Ausgehobenem Boden außerhalb Verkehrsflächen verwendet werden,. Eine Pipeline .
muss immer vorübergehend eingesteckt werden, wie Installation, um zu verhindern, dass Verunreinigungen aus der Eingabe Rohren unterbrochen wird. Während der Installation, der Wasserstand im Graben muß niedrig genug gehalten werden, damit Auftrieb nicht bewegen und kein Wasser das installierte Rohr beschädigt. Weitere detaillierte Anweisungen für den Einbau von Kunststoff beschichteten Rohrleitungen sind in den kommunalen Engineering Vorschriften des jeweiligen Landes. Wenn Rohre in Bereichen, wo es die Installation von Straßen oder Eisenbahnlinien, die Anweisungen des betreffenden Beamten sind zu befolge.
2. Fügeverfahren
Allgemeines
Rohrverbindungen (Feige. 4) werden verwendet, Rohre und Formteile in eine integrierte Rohrleitung anzuschließen. Gelenke lassen sich in zwei Haupttypen unterteilt werden: zugfeste und nicht-resistenten. Gelenke können auch durch Anwendungen wie folgt aufgeteilt werden:
2.1 Stoßverbindungs-
Verwendet, in erster Linie in zugfeste Druckleitungen wie Öl, Erdgas- und Fernwärmeleitungen. Verwendet in den Wasserleitungen vor allem bei Rohrgrößen ≥ DN 600 wenn das Gelenk von innen nach dem Schweißen repariert werden,. Für eine detailliertere Beschreibung, Siehe Abbildung 6 Auf Seite 5. Ein Schweißmuffe wird verwendet, um neue Rohrleitungen oder eine Montage an einer vorhandenen Linie zu verbinden. Innenschweiß und Fertigstellung der Betonauskleidung erfordern einen Schacht in Verbindung mit dem Gelenk. Installation des Schweißmuffe ist in Figur beschrieben 9.
2.2 DIN / G Schweißverbindung
Verwendet in den Rohrleitungen, wo eine einfache Installation des tensionresistant Gelenk- und die Möglichkeit, die weniger als 1.0 Grad-Kurven sind ein Muss. Geschweißt von außen. Anzüge Rohrdurchmesser DN 400-900 Druckstufe PN16 und PN10 DN1000-1200 Druckklasse. Nur interne Betonauskleidung wird mit dieser Art von Hülse verwendet, keine Malerei erfolgt. Die DIN / G Gelenk wird durch den Einbau eines Gummiring in der Betonauskleidung im Werk gefertigt, was bedeutet, dass keine Notwendigkeit besteht, die innere Betonauskleidung vor Ort zu vervollständigen. Der Gummiring verhindert, dass Wasser in den Spalt des Hülsengelenkes ändernden.
2.3 OV Schweißverbindung
Verwendet in den Wasserleitungen Installation zu erleichtern und zu ermöglichen, 1.5 – 3.0 Grad biegt an Gelenken. Da das Gelenk von innen geschweißt wird, um es zu machen Spannung beständig, es ist geeignet für Durchmesser ≥ DN 600 und Drücken bis zu 20 Bar. Für eine detailliertere Beschreibung, siehe Sektion 3.3 und Fig 8.
2.4 Flanschverbindung
Flanschverbindungen sind weit verbreitet in der Industrie. Mit unterirdischen Rohren, Flanschverbindungen werden verwendet, z. in Verbindung mit Ventilen und Schächten. Für eine detailliertere Beschreibung, siehe Sektion 3.4 und Fig 10. Die Gelenke können z.B durch Klinger-KGS Dichtungen abgedichtet werden,.
2.5 Kupplungsverbindung
Die Stahlrohre können auch durch verschiedene mechanische Rohrkupplungen, wie jene, hergestellt von Straub verbunden werden,, VikingJohnson und Victaulic. Dann, die Enden der Rohre sind abgedreht und Verputzen der Schweißnähte die Kupplungen passen sind geschliffen. Für eine detailliertere Beschreibung, siehe Sektion 3.5.
2.6 Schweißmuffe
Ein Schweißring eingesetzt wird, wenn neue Rohrleitung oder eine einzelne neue Komponente zu einer bestehenden Rohrverbindungs. Der Einbau eines Schweißmuffe ist in Figur beschrieben 9. Wenn eine einzelne neue Komponente installiert, es muss auch eine Schacht, so dass die Innenauskleidung repariert werden kann. Der Schweißring kann bis PN10 Druckklasse nur extern verschweißen, aber es erfordert auch internen Schweiß in Druckklasse PN16. nach dem Schweißen, das Innenfutter und extern Korrosion Schutzbeschichtung abgeschlossen.
2.7 Die Auswahl der Verbindungsmethode
Schweißen wird normalerweise mit Erdeinbau verwendet. Geschweißte Muffenverbindungen erleichtern die Montage und ermöglichen kleine Biegungen ohne Winkelrohrfittings. In Unterböden mit geringer Tragfähigkeit (Ton und Schluff), eine Schweißverbindung ist sicherer als ein Kupplungsgelenk. Falls ein Kupplungsgelenk in schwachen Böden verwendet, es wird empfohlen, robustere couplings.The Kopplung verwenden muß auf einer Betonplatte abgestützt werden oder dergleichen Scherspannungen zu eliminieren,. Bei hohen Wasserdrücken (≥ 10 Bar) es ist auch ratsam, einen robusteren Art der Kopplung zu verwenden,. Die Zähne der zugfesten, Zahnkupplungen beschädigen äußeren Schutzschichten. Deshalb, ihre Verwendung sollte in erster Linie begrenzt werden, um zu trocknen, Innen-Installationen, bei denen externen Korrosionsschutz nicht benötigt wird,.
Tensionresistant Flanschverbindungen sind in institutionellen und industriellen Anlagen eingesetzt Demontage zu erleichtern. Tensionresistant Fugen müssen immer in untergetauchten Installation verwendet werden. Bei der Verwendung von DIN / G-Typ Ärmel, Rohre sind nur mit Beton ausgekleideten intern, keine Malerei erfolgt.
3. Installation
Kunststoff-Abschlussdeckel
Die Kunststoffabdeckungen an den Enden der Rohre werden erst kurz vor der Montage entfernt werden, um eine übermäßige Härtung oder Verschmutzung des Innenbetonauskleidung während der Lagerung zu vermeiden,. Im Sommer, die externe schwarz PUR-Beschichtung auf den Rohrteilen ist mit weißen Kunststoff für die gesamte Lagerzeit abgedeckt, als Wärme von der Sonne wird die coating.When Entfernen der Kunststoffabdeckungen erweichen, eine Sichtprüfung der Ende, Innenflächen und Muffen der Rohre durchgeführt wird. Haarrisse in der Betonauskleidung, die durch eine übermäßige Härtung verursacht werden kann durch Benetzen des Betons mit Haushaltswasser hin und wieder im Sommer entfernt werden.
3.1. Stoßverbindungs-
Allgemeines
Zugfeste Stoßfugen (Feige. 6) wird mit dem gesamten Bereich von Rohrdurchmessern verwendet. Die Gelenke sind von außen mit Basiselektroden geschweißt. Arbeitstemperatur muss nicht erhöht werden. Die Gelenke als solche nicht Bögen erlauben, aber das Ende eines Rohres in einem Winkel geschnitten werden,, oder eine Rohrleitung mit innerer Betonauskleidung kann sicher gebogen werden, Falls benötigt, auf den minimalen Radius in der Tabelle angegebenen Krümmungs.
Schweißen
Der Schweißer muss mindestens die Kompetenz des von der Norm EN 9606-1. Die Schweißgüteklasse wird in der Norm EN ISO festgelegten 5817, Klasse C.Pipes werden zum Schweißen angepasst. Der Schweiß Hohlraum mindernde Wirkung von Heften und Schweißen muß bei der Bestimmung der Breite des Schweiß Hohlraums betrachtet werden (2 – 4 mm). nach dem Anheften, die Gelenke schweißt 2 – 3 läuft mit einer trockenen Grundelektrode, wie Esab OK 48.00, P48 im Ausland, Böhler Fox EV 48, Filarc 35 oder gleichwertig. Die Dicke der Elektrode wird durch die Rohrwanddicke bestimmt, die Art des Schweiß, die Art des Laufes und Schweißposition, sowie die Kompetenz des Schweißers. Die Schweißwerte werden gemäß den Anweisungen der Schweißzusätze Lieferanten ausgewählt. Ausführen einer Schweißverfahrensprüfung nach EN ISO 15614-1 wird vor empfohlen Schweißen zu Beginn.
Kontrolle der Schweißverbindung
Alle Schweißnähte sind zumindest visuell inspiziert. Beginn und Ende Defekte, Hinterschneidungen, Risse, etc.. Oberflächendefekte werden gemahlen oder durch Schweißen repariert. Zusätzlich Empfehlung ist, dass zumindest 10% von Schweißungen sind durch Magnetpulverprüfung untersucht. Grundvoraussetzung ist auch, dass zumindest 5 Schweißungen jeder Schweißer sind geprüft und, wenn irgendwelche Schweißungen versagt, Testfrequenz höher sein. Außerdem, Die Dichtheit der Gelenke wird durch Wasserdruckprobe geprüft, nachdem die Pipeline abgeschlossen ist.
Die Fertigstellung der inneren Betonauskleidung
Interne Betonauskleidung mit Rohr abgeschlossen ist Größen ≥ DN 600. nach dem Schweißen, loser Rost und Schweißschlacke und Fig 6. Stoßverbindungs- Alle Maße in Millimeter. mir. 50 Schrumpfbare Hülse oder Korrosionsschutzband DIN 30670 N-n 6 Eine mögliche konkrete abseits der Fugen kommt die Innenfläche abgebürstet. Im Winterbedingungen ist der Verbindungsbereich erhitzt mit einer Gasflamme. Der Verbindungsbereich wird zuerst befeuchtet und anschließend mit Mörtel beschichtet, die aus gleichen Teilen Sand und Zement bestehen (SR Zement). Der Sand ist genug sein, um sauber und mit einer Korngröße von 0.125 – 1.5 mm. Genug Wasser zugegeben, um einen ziemlich steifen Mörtel zu machen. Nur die Menge an Mörtel und Zement in einer Stunde verwendet wird, gemischt werden. Der Mörtel wird mit einer Kelle auf das Niveau des ursprünglichen Futters verteilt. Nach ungefaehr 2 Stunden wird die Fläche mit einem nassen Schwamm gerieben. Unter Bedingungen vor Ort, Beton benötigt mindestens 5 Tage aushärten. Wenn möglich, der Verbindungsbereich sollte feucht und an mehr als gehalten werden +5 ºC während dieser Zeit. Im Winter Bedingungen kann ein Warmluftgebläse zum Heizen verwendet werden. Frostsicher Zement darf nicht verwendet werden, da sie wasserlösliche Beimischungen ungeeignet für Trinkwasseranwendungen enthalten.
Die Fertigstellung der internen Malerei
Innenlackierung ist mit Rohr abgeschlossen Größen ≥ DN 600. Der Verbindungsbereich wird gemäß den Anweisungen des Lackherstellers behandelt. Fertigstellung der Außenbeschichtung Blanker Stahl Oberflächen mit einer Stahlbürste gereinigt (Reinheitsgrad St 2), getrocknet mit flüssigem Gasflamme und antikorrosive lackiert (Beispiel TEMAPRIME EE) bevor Hülse wird hinzugefügt. Die PE-Beschichtung wird über einen Abstand von etwa aufgeraut 100 mm. Der gereinigte und erwärmte Verbindungsbereich wird durch eine wärmeschrumpfbare Hülse oder Korrosionsschutzband geschützt (Canusa, Raychem, Denso, Stopaq usw.) gemäß den Anweisungen des Herstellers.