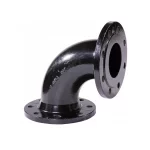
Ductile Iron Pipe Fittings – Long Radius Ductile Iron Bend
March 8, 2025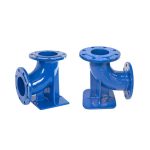
Double Flange 90° Duck Foot Ductile Iron Bend
March 23, 2025Introduction to Ductile Iron Pipe for Wastewater
Ductile iron pipe has become a preferred choice for wastewater systems due to its exceptional strength, durability, and resistance to the harsh conditions posed by sewage, industrial effluents, and stormwater. Unlike potable water systems, where purity is paramount, wastewater applications demand materials that can withstand corrosive chemicals, abrasive solids, and fluctuating pressures while maintaining structural integrity over decades. Ductile iron—a modern evolution of cast iron with nodular graphite—excels in these environments, offering a robust, cost-effective solution for municipal sewers, treatment plants, and industrial waste lines. This discussion explores why ductile iron is ideal for wastewater, detailing its specifications, applications, and performance advantages.
Material: Ductile Iron for Wastewater
Ductile iron is an iron-carbon alloy (2-4% carbon, 1-3% silicon) treated with magnesium (0.03-0.06%) to transform graphite flakes into spherical nodules. This microstructural shift grants ductile iron superior mechanical properties compared to traditional gray cast iron:
-
Tensile Strength: 60,000-120,000 psi, enabling it to handle high pressures and external loads.
-
Ductility: 10-20% elongation, allowing flexibility under stress without cracking.
-
Toughness: Resists impact and fatigue, critical in dynamic wastewater environments.
For wastewater, ductile iron’s natural corrosion resistance—due to its iron base forming a protective oxide layer—is a key advantage. However, raw ductile iron alone isn’t sufficient against the aggressive chemistry of sewage (e.g., hydrogen sulfide, acids) or abrasive slurries. Specialized linings and coatings, discussed later, enhance its suitability, making it a versatile material for both gravity-fed sewers and force mains (pressurized wastewater lines).
Design Features for Wastewater
Ductile iron pipes for wastewater are engineered to meet specific challenges:
-
Size Range: DN80 to DN2600 (80 mm to 2,600 mm), covering small laterals to large outfalls.
-
Pressure Classes: K7, K8, K9 (ISO 2531) or C25, C30, C40 (EN 598), with K9 and C40 common for force mains handling 50-40 bar (725-580 psi).
-
Length: Typically 6 meters, often cut to 5.7 meters for shipping, ensuring efficient installation.
-
Wall Thickness: Varies by class (e.g., K9 thicker than K7), balancing strength and weight.
These features ensure the pipe can endure internal pressures, external soil loads, and the corrosive/abrasive nature of wastewater flows.
Manufacturing Process
The production of ductile iron pipe for wastewater mirrors that for water supply, with tweaks for durability:
-
Melting: Iron, carbon, and silicon are melted at 2,500-2,800°F (1,370-1,540°C) in a furnace.
-
Magnesium Treatment: Molten iron is inoculated with magnesium to form nodules, ensuring ductility.
-
Centrifugal Casting: The treated iron is spun into pipe molds, creating uniform walls and a smooth interior.
-
Annealing: Heat treatment at 1,650-1,850°F (900-1,010°C) refines the microstructure, relieving stresses.
-
Lining and Coating: Specialized linings (e.g., polyurethane) and coatings (e.g., zinc-epoxy) are applied to combat wastewater’s corrosiveness.
-
Finishing: Pipes are tested (e.g., hydrostatic pressure per EN 598) and prepared for shipment.
This process adheres to standards like EN 598 (for wastewater) and ISO 2531, ensuring reliability.
Joint Types for Wastewater
Joints in wastewater systems must be leak-tight and adaptable to soil movement or pressure surges. Common types include:
-
T-Type (Push-On Joint): Quick to install, suitable for gravity sewers, with rubber gaskets (e.g., NBR) resisting sewage chemicals.
-
K-Type (Mechanical Joint): Bolted for security, used in force mains or unstable soils, offering high thrust resistance.
-
Self-Restrained Joint: Locks against pull-out, ideal for high-pressure wastewater lines without thrust blocks.
-
Flanged Joint: Rigid, bolted connections for treatment plant piping or pump stations.
Joint Type
|
Strength
|
Flexibility
|
Wastewater Use
|
---|---|---|---|
T-Type (Push-On)
|
Moderate
|
High (5° max)
|
Gravity sewers
|
K-Type (Mechanical)
|
High
|
Moderate
|
Force mains, unstable soils
|
Self-Restrained
|
High
|
Moderate
|
Pressurized lines
|
Flanged
|
Very High
|
None
|
Treatment plants
|
Internal Linings for Wastewater
Wastewater’s corrosiveness—driven by hydrogen sulfide (H₂S), sulfates, and organic acids—requires robust internal linings:
-
Portland Cement Mortar: Basic protection for mild sewage, but less effective against H₂S.
-
Sulphate Resistant Cement Mortar: Resists sulfate-reducing bacteria, common in septic sewage.
-
High-Aluminum Cement Mortar: Withstands acidic effluents (pH < 4), used in industrial wastewater.
-
Epoxy Resin: Smooth, non-porous, and corrosion-resistant, suitable for moderate chemical exposure.
-
Epoxy Ceramic: Adds ceramic particles for abrasion resistance, ideal for gritty sewage or slurries.
-
PU (Polyurethane): Highly durable against H₂S, acids, and abrasion, the gold standard for severe wastewater.
Lining Type
|
Key Benefit
|
Wastewater Application
|
---|---|---|
Portland Cement
|
Basic corrosion
|
Mild sewage
|
Sulphate Resistant Cement
|
Sulfate resistance
|
Septic sewage
|
High-Aluminum Cement
|
Acid resistance
|
Industrial effluents
|
Epoxy Resin
|
Smooth, durable
|
Moderate chemical exposure
|
Epoxy Ceramic
|
Abrasion resistance
|
Gritty sewage, slurries
|
PU (Polyurethane)
|
Chemical/abrasion
|
Severe wastewater
|
PU and epoxy ceramic linings are increasingly popular for their longevity in aggressive conditions.
External Coatings
External coatings protect against soil corrosion, especially in wet or acidic environments:
-
Zinc + Bitumen: Standard (130-200 g/m² zinc), offering galvanic protection and a moisture barrier.
-
Zinc-Epoxy: Enhanced corrosion resistance for aggressive soils (e.g., coastal areas).
-
PU (Polyurethane): Flexible and tough, resisting chemical attack and mechanical damage.
-
FBE (Fusion-Bonded Epoxy): Thick, uniform coating for long-term durability.
-
Epoxy-Ceramic: Combines corrosion and abrasion resistance for rocky or saline soils.
Coating Type
|
Protection
|
Soil Type
|
---|---|---|
Zinc + Bitumen
|
Basic corrosion
|
Standard soils
|
Zinc-Epoxy
|
Enhanced corrosion
|
Aggressive soils
|
PU
|
Flexibility, corrosion
|
Coastal/wet areas
|
FBE
|
Long-term durability
|
High-corrosion zones
|
Epoxy-Ceramic
|
Corrosion + abrasion
|
Rocky/saline soils
|
Rubber Gaskets
Gaskets ensure joint integrity, with materials per ISO 4633:
-
NBR (Nitrile Butadiene Rubber): Oil- and chemical-resistant, ideal for sewage with hydrocarbons.
-
SBR (Styrene Butadiene Rubber): Cost-effective for mild wastewater.
-
EPDM (Ethylene Propylene Diene Monomer): Resists weathering and chemicals, suitable for long-term exposure.
Gasket Type
|
Key Property
|
Wastewater Use
|
---|---|---|
NBR
|
Oil/chemical resistance
|
Industrial sewage
|
SBR
|
General durability
|
Mild sewage
|
EPDM
|
Weather/chemical
|
Long-term sewers
|
Applications in Wastewater Systems
Ductile iron pipes serve diverse wastewater needs:
-
Municipal Sewage: Gravity sewers (DN200-DN600) and force mains (DN80-DN300) transport domestic waste to treatment plants.
-
Industrial Effluents: Handles corrosive or abrasive discharges (e.g., from chemical plants or mines).
-
Stormwater: Large-diameter pipes (DN800-DN2600) manage runoff, resisting soil loads and debris.
-
Treatment Plants: Flanged pipes route processed wastewater within facilities.
-
Combined Systems: Accommodates mixed sewage and stormwater in urban areas.
Application
|
Size Range
|
Key Requirement
|
---|---|---|
Municipal Sewage
|
DN200-DN600
|
Corrosion resistance
|
Industrial Effluents
|
DN80-DN300
|
Chemical/abrasion
|
Stormwater
|
DN800-DN2600
|
Load capacity
|
Treatment Plants
|
DN100-DN500
|
Pressure handling
|
Combined Systems
|
DN300-DN1000
|
Versatility
|
Advantages for Wastewater
-
Corrosion Resistance: Enhanced by linings/coatings, withstands H₂S and acids.
-
Strength: Supports deep burials (10-20 meters) and traffic loads.
-
Ductility: Flexes in shifting soils or seismic zones, reducing breaks.
-
Abrasion Resistance: Ceramic or PU linings endure gritty flows.
-
Longevity: 50-100 years with proper protection, cutting replacement costs.
-
Pressure Capacity: Handles force mains up to 50 bar, unlike PVC or HDPE in some cases.
Challenges and Considerations
-
Hydrogen Sulfide (H₂S): Sewage generates H₂S gas, which forms sulfuric acid in moist conditions. PU or high-aluminum linings are critical to combat this.
-
Abrasion: Solids in wastewater (e.g., sand, gravel) wear linings; epoxy-ceramic or PU mitigate this.
-
Cost: Higher upfront cost than PVC, though lifecycle savings justify it.
-
Weight: Heavier than plastic alternatives, requiring more installation effort.
Wastewater Chemistry
Sewage isn’t just water—it’s a brew of organic waste, bacteria, and chemicals. In anaerobic conditions, sulfate-reducing bacteria produce H₂S, which corrodes untreated iron in 10-20 years. A DN300 ductile iron pipe with PU lining in a Los Angeles sewer lasted 40 years without failure, while an unlined cast iron pipe nearby pitted out in 15.
Force Main Dynamics
In a force main pumping 200 psi, a K9 ductile iron pipe with a restrained joint holds steady where HDPE might deform. During a 2019 flood in Houston, ductile iron force mains stayed intact while plastic lines buckled, proving its resilience.
Installation Realities
Laying a DN600 sewer in clay soil takes a skilled crew—cranes hoist 6-meter lengths, and push-on joints snap together in minutes. In rocky terrain, an epoxy-ceramic coating shrugs off scratches that would rust steel.
Economic Value
A DN400 K9 pipe might cost $30 per meter versus $20 for PVC, but PVC’s 30-year life pales against ductile iron’s 75+. In a 10-kilometer sewer, that’s $100,000 saved in replacements over a century.
Environmental Edge
Ductile iron’s recyclability and long life reduce waste. A treatment plant in Ontario swapped corroded steel for ductile iron in 2005, cutting maintenance emissions by 25% over 20 years.
Conclusion
Ductile iron pipe for wastewater is a robust, adaptable solution, excelling where corrosion, pressure, and abrasion test lesser materials. From its nodular iron core to its PU linings and zinc-epoxy coatings, it’s built to endure the nastiest flows—sewage, industrial waste, or stormwater—for decades. Whether channeling effluent through a DN200 force main or draining a city via a DN1200 outfall, its strength and longevity make it indispensable.