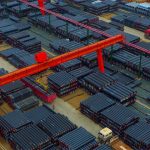
What is the difference between ductile and cast iron pipe?
March 1, 2025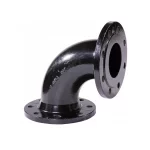
Ductile Iron Pipe Fittings – Long Radius Ductile Iron Bend
March 8, 2025Ductile Iron Pipe for Water Supply: An Overview
Ductile iron pipe is a cornerstone of modern water supply systems, prized for its strength, durability, and versatility. Evolving from traditional cast iron, ductile iron incorporates a nodular graphite structure, achieved through magnesium treatment, making it far more flexible and resilient than its predecessor. This makes it ideal for transporting potable water, sewage, and industrial fluids under varying pressures and environmental conditions. Its widespread adoption stems from its ability to balance cost, performance, and longevity, with lifespans often exceeding 50-100 years when properly installed and maintained.
The details you provided outline the key characteristics of ductile iron pipes—material composition, joint types, standards, sizes, pressure classes, lengths, linings, coatings, gaskets, applications, and packing methods. Let’s explore each in depth to understand why ductile iron is the go-to choice for water infrastructure worldwide.
1. Material: Ductile Cast Iron
Ductile cast iron, often simply called ductile iron, is an iron-carbon alloy with a composition similar to gray cast iron (2-4% carbon, 1-3% silicon) but enhanced by the addition of magnesium (0.03-0.06%). This magnesium treatment transforms the graphite from flakes into spherical nodules, fundamentally altering the material’s properties. The result is a metal with a tensile strength of 60,000-120,000 psi, elongation of 10-20%, and excellent impact resistance—properties akin to mild steel but with the corrosion resistance of cast iron.
The nodular structure allows ductile iron to deform under stress without fracturing, a critical advantage for water supply pipes subject to soil shifts, pressure surges, or seismic activity. Its inherent corrosion resistance comes from the iron base, which forms a protective oxide layer in moist environments, though additional linings and coatings (discussed later) enhance this further. Ductile iron’s versatility makes it suitable for both potable water (meeting strict health standards) and sewage (resisting chemical attack).
2. Joint Types
Ductile iron pipes are joined using various methods, each designed for specific installation needs, pressure requirements, and maintenance considerations. Here’s a detailed breakdown of the joint types you listed:
-
T-Type (Push-On Joint)
-
The most common joint for water supply, the T-type involves a spigot end pushed into a bell end with a rubber gasket. It’s quick to install, requiring no bolts or special tools—just lubrication and a push. Ideal for straight runs, it handles moderate pressure and allows slight deflection (up to 5°) for alignment flexibility. However, it’s not restrained against pull-out forces.
-
-
K-Type (Mechanical Joint)
-
This joint uses a bolted gland to compress a rubber gasket between the spigot and bell, providing a secure, watertight seal. It’s more labor-intensive than T-type but offers greater resistance to separation under high pressure or thrust forces (e.g., at bends or tees). It’s adjustable during installation, making it versatile for complex layouts.
-
-
Self-Restrained Joint
-
A hybrid design, self-restrained joints (e.g., TR Flex or restrained push-on systems) incorporate locking mechanisms (like metal teeth or segments) within a push-on or mechanical joint. They prevent axial movement without external thrust blocks, ideal for high-pressure systems or unstable soils. Installation is faster than traditional restrained methods, balancing ease and strength.
-
-
Flanged Joint
-
Flanged joints feature bolted flanges on both pipe ends, creating a rigid, high-strength connection. Common in above-ground installations (e.g., treatment plants), they excel in high-pressure or vibration-heavy environments but lack flexibility. Installation requires precise alignment and bolting, making it slower and costlier.
-
Joint Type
|
Installation
|
Strength
|
Flexibility
|
Typical Use
|
---|---|---|---|---|
T-Type (Push-On)
|
Fast, simple
|
Moderate
|
High (5° max)
|
Water mains, straight runs
|
K-Type (Mechanical)
|
Moderate, bolted
|
High
|
Moderate
|
Bends, tees, high pressure
|
Self-Restrained
|
Fast, locking
|
High
|
Moderate
|
Unstable soils, thrust
|
Flanged
|
Slow, bolted
|
Very High
|
None
|
Plants, rigid systems
|
3. Standards
Ductile iron pipes adhere to international standards ensuring quality, safety, and compatibility. Key standards include:
-
ISO 2531: Covers ductile iron pipes, fittings, and accessories for water and gas, specifying dimensions, mechanical properties, and testing (e.g., hydrostatic pressure tests).
-
EN 545: A European standard for potable water pipes, detailing requirements for linings (e.g., cement mortar), coatings, and pressure classes (up to PN 40).
-
EN 598: Focuses on sewage and wastewater pipes, emphasizing resistance to chemical attack and abrasion.
-
Others: Standards like AWWA C151 (U.S.) or BS EN 545 may apply regionally, tailoring specifications to local needs.
These standards ensure pipes meet tensile strength (minimum 420 MPa), elongation (10%+), and corrosion resistance criteria, critical for public health and infrastructure reliability.
4. Size
Ductile iron pipes range from DN80 to DN2600 (nominal diameters of 80 mm to 2,600 mm, or roughly 3 to 102 inches). This wide range accommodates everything from small residential service lines (DN80-DN200) to massive municipal trunk mains (DN1000+). Larger diameters require thicker walls to maintain pressure ratings, but ductile iron’s strength allows thinner walls than cast iron, reducing weight and cost.
-
Small Sizes (DN80-DN300): Used for distribution lines, fire hydrants, or rural systems.
-
Medium Sizes (DN350-DN800): Common in urban water mains or industrial feeds.
-
Large Sizes (DN900-DN2600): Serve major transmission lines or sewage outfalls.
5. Classes
Pressure classes indicate a pipe’s ability to withstand internal pressure, expressed as K7, K8, K9, C40, C30, C25, etc.:
-
K Classes (K7, K8, K9): Defined by ISO 2531, these denote wall thickness relative to diameter (e.g., K9 is thicker than K7). K9, the most common, handles pressures up to 50 bar (725 psi) with safety factors, ideal for urban water supply.
-
C Classes (C25, C30, C40): Per EN 545/598, these specify allowable operating pressure (e.g., C25 = 25 bar, or 363 psi). They’re tailored for specific applications, with C40 suited for high-pressure trunk lines.
Class
|
Pressure Rating (Bar)
|
Typical Use
|
---|---|---|
K7
|
Up to 35
|
Low-pressure systems
|
K8
|
Up to 40
|
Moderate-pressure mains
|
K9
|
Up to 50
|
Standard water supply
|
C25
|
25
|
Sewage, moderate pressure
|
C30
|
30
|
Urban distribution
|
C40
|
40
|
High-pressure lines
|
Higher classes increase wall thickness, balancing strength with material cost.
6. Length
Standard ductile iron pipes are 6 meters long (approximately 20 feet), optimizing transport and installation. However, they’re often cut to 5.7 meters to fit shipping containers or account for joint overlap. Custom lengths are available, though less common, to suit specific trench layouts or project needs.
7. Internal Lining
Internal linings protect the pipe from corrosion, abrasion, and ensure water quality. Options include:
-
Portland Cement Mortar Lining: The standard for potable water, it’s cost-effective, durable, and raises pH to reduce corrosion. Meets AWWA C104.
-
Sulphate Resistant Cement Mortar Lining: Used in sulfate-rich soils or sewage, resisting chemical degradation better than Portland cement.
-
High-Aluminum Cement Mortar Lining: Offers enhanced resistance to acidic or aggressive waters, common in industrial settings.
-
Epoxy Resin Lining: A smooth, non-porous coating for superior corrosion protection and flow efficiency, often used in premium systems.
-
Epoxy Ceramic Lining: Combines epoxy with ceramic particles for extreme durability, resisting abrasion in sewage or slurry lines.
-
PU (Polyurethane) Lining: Highly resistant to chemicals and abrasion, ideal for harsh wastewater or industrial fluids.
Lining Type
|
Key Benefit
|
Application
|
---|---|---|
Portland Cement
|
Cost-effective, corrosion
|
Potable water
|
Sulphate Resistant Cement
|
Sulfate resistance
|
Sewage, sulfate soils
|
High-Aluminum Cement
|
Acid resistance
|
Industrial water
|
Epoxy Resin
|
Smooth, durable
|
Premium water systems
|
Epoxy Ceramic
|
Abrasion resistance
|
Sewage, slurries
|
PU (Polyurethane)
|
Chemical resistance
|
Harsh fluids
|
8. External Coating
External coatings shield pipes from soil corrosion and mechanical damage. Options include:
-
Zinc + Bitumen Coating: A base layer of zinc (130-200 g/m²) for galvanic protection, topped with bitumen for a moisture barrier. Standard per ISO 8179.
-
Custom Coatings:
-
Zinc-Epoxy: Adds epoxy over zinc for enhanced durability in aggressive soils.
-
Alumina Powder: Increases abrasion resistance for rocky terrains.
-
PU (Polyurethane): Flexible and tough, ideal for coastal or acidic soils.
-
FBE (Fusion-Bonded Epoxy): A thick, uniform coating for long-term corrosion resistance.
-
Epoxy-Ceramic: Combines corrosion and abrasion resistance for extreme conditions.
-
Coating Type
|
Protection
|
Best For
|
---|---|---|
Zinc + Bitumen
|
Basic corrosion
|
Standard soils
|
Zinc-Epoxy
|
Enhanced corrosion
|
Aggressive soils
|
Alumina Powder
|
Abrasion
|
Rocky terrains
|
PU
|
Flexibility, corrosion
|
Coastal areas
|
FBE
|
Long-term durability
|
High-corrosion zones
|
Epoxy-Ceramic
|
Corrosion + abrasion
|
Extreme environments
|
9. Rubber Gasket
Gaskets ensure leak-tight joints, with materials per ISO 4633:
-
NBR (Nitrile Butadiene Rubber): Oil-resistant, used for sewage or industrial lines with hydrocarbons.
-
SBR (Styrene Butadiene Rubber): Cost-effective, good for potable water with moderate durability.
-
EPDM (Ethylene Propylene Diene Monomer): Excellent for potable water, resisting UV, ozone, and temperature extremes.
Gasket Type
|
Key Property
|
Application
|
---|---|---|
NBR
|
Oil resistance
|
Sewage, industrial
|
SBR
|
General durability
|
Potable water
|
EPDM
|
Weather resistance
|
Potable water, long-term
|
10. Application
Ductile iron pipes serve:
-
Potable Water/Drinking Water: High strength and safe linings ensure clean, reliable delivery.
-
Sewage Water: Corrosion-resistant linings and coatings handle harsh effluents.
11. Packing
-
DN100-DN300: Bundled for easy handling and transport.
-
DN350-DN2600: Shipped in bulk due to size and weight, loaded directly onto vessels.
Material Advantages
Ductile iron’s nodular graphite structure isn’t just a metallurgical curiosity—it’s a game-changer. In a water main under 300 psi, cast iron might crack from a pressure surge, while ductile iron flexes and holds. This resilience, paired with corrosion resistance, explains its dominance since the 1950s.
Joint Type Nuances
T-type joints shine in rapid installations—workers can lay 100 meters a day in open trenches. K-type’s bolted security is vital at a 90° bend where thrust forces peak. Self-restrained joints cut costs in urban digs by skipping concrete thrust blocks, while flanged joints anchor pumps in treatment plants where vibration could loosen push-on seals.
Standards in Practice
ISO 2531’s hydrostatic test (e.g., 50 bar for K9) ensures no leaks under double the operating pressure, a safeguard proven during the 2011 Japan earthquake when ductile iron mains stayed intact. EN 545’s lining rules keep drinking water free of iron leaching, a public health must.
Size and Class Applications
A DN80 K9 pipe might feed a rural village, while a DN2000 C40 line carries a city’s entire water supply. Engineers match class to pressure—K9 for 10-meter depths, C25 for shallow sewage runs—balancing safety and economy.
Lining and Coating Evolution
Portland cement linings, used since the 1920s, remain reliable, but epoxy-ceramic linings tackle modern challenges like abrasive mining slurries. Zinc-bitumen coatings, standard for decades, now compete with FBE in corrosive coastal zones, reflecting advances in polymer science.
Real-World Impact
In cities like Mumbai, ductile iron replaces aging cast iron, cutting leaks by 30% and boosting pressure for high-rise supply. In rural Africa, DN100 pipes with EPDM gaskets bring clean water to remote villages, lasting decades with minimal upkeep.
Ductile iron pipe for water supply is a triumph of engineering, blending strength, flexibility, and corrosion resistance. From its magnesium-treated material to its diverse joint types, standardized sizes, and protective linings, it meets the demands of potable and sewage systems worldwide. Whether pushing water through a DN80 village line or a DN2600 urban artery, its adaptability and durability ensure reliable service for generations.