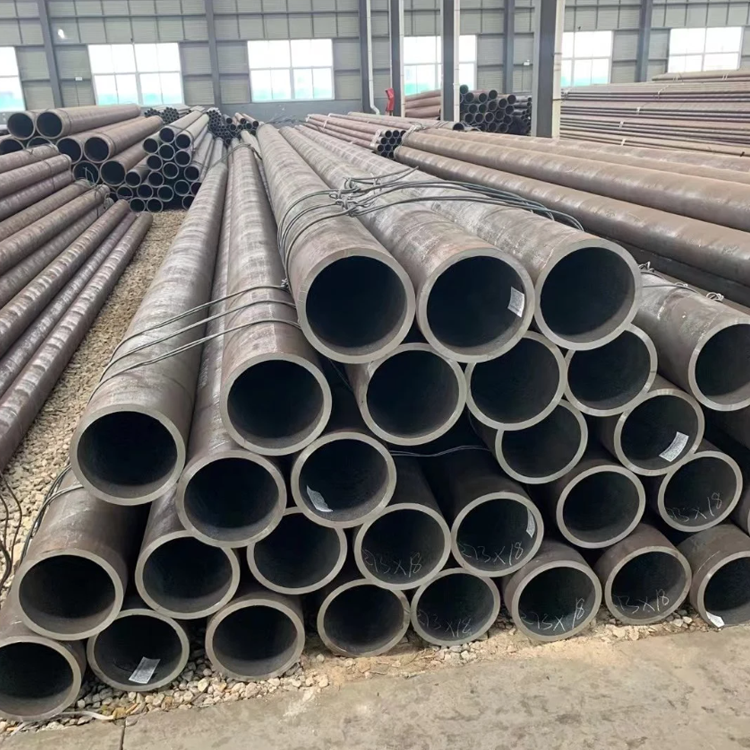
Tubería de acero sin costura estructural
agosto 22, 2023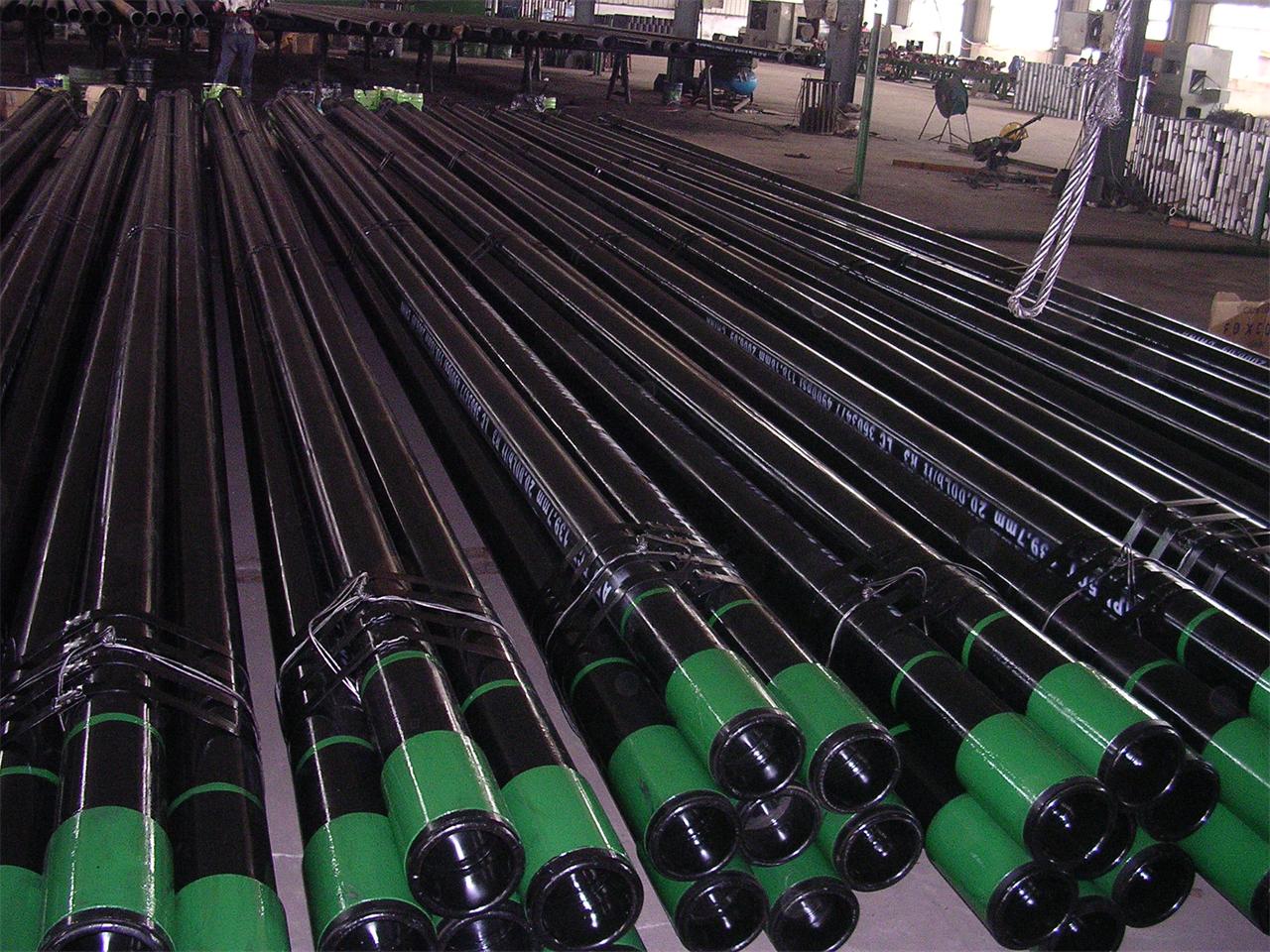
Proceso de tratamiento térmico de tuberías de revestimiento de aceite.,¿Cómo se inspeccionan y prueban las carcasas de aceite para garantizar su calidad??
Septiembre 4, 2023Carcasa de aceite de alta resistencia y tenacidad y método de producción de la misma
Descripción
Una carcasa de petróleo con alta resistencia y dureza es un componente crítico en las operaciones de perforación de petróleo y gas.. Está diseñado para soportar alta presión., materiales abrasivos, y ambientes corrosivos, comúnmente encontrado en operaciones de perforación. La carcasa de aceite suele estar hecha de acero y debe tener propiedades específicas como alta resistencia., tenacidad, y corrosión resistencia.
Método de producción
El método de producción implica varios pasos., incluyendo la selección de materiales, tratamiento térmico, formando, e inspección.
1. Selección de materiales
El material base de la carcasa suele ser acero al carbono o acero aleado de alta calidad.. El material se selecciona en función de las condiciones esperadas de la operación de perforación., como la temperatura, presión, y ambiente corrosivo.
2. Formando
El acero se calienta a una temperatura específica y luego se le da forma de tubería.. Esto a menudo se hace laminando en caliente., donde el acero pasa a través de una serie de rodillos que le dan la forma y el tamaño de tubería deseados. Luego, los tubos se enfrían y endurecen..
3. Tratamiento térmico
próximo, Las tuberías se someten a un proceso de tratamiento térmico.. Esto puede incluir temple y revenido., que se utilizan para aumentar la resistencia y tenacidad del acero.. El enfriamiento implica calentar el acero a una alta temperatura y luego enfriarlo rápidamente, mientras que el templado implica calentar el acero a una temperatura más baja y luego enfriarlo lentamente.
4. Inspección y prueba
Finalmente, Las tuberías se inspeccionan y prueban para garantizar que cumplan con los estándares requeridos.. Esto puede incluir inspecciones visuales., prueba de dureza, y pruebas ultrasónicas. Si las tuberías pasan estas pruebas, Luego están listos para ser utilizados como carcasas de aceite..
Este es un resumen básico de cómo se producen las carcasas de aceite de alta resistencia y tenacidad.. Los procesos reales pueden ser más complejos y pueden variar según los requisitos específicos de la carcasa..
ventajas
- Mayor durabilidad: La alta resistencia y dureza de estas carcasas de aceite les permiten soportar alta presión y materiales abrasivos., aumentando su vida útil y reduciendo la necesidad de reemplazos.
- Seguridad mejorada: Estas propiedades también mejoran la seguridad de las operaciones de perforación., ya que reducen el riesgo de falla de la carcasa, que puede provocar accidentes catastróficos.
- Económico: Aunque el proceso de producción puede ser más complejo y costoso, La mayor durabilidad y seguridad de estas carcasas puede generar importantes ahorros de costos a largo plazo..
Conclusión
La producción de carcasas de petróleo con alta resistencia y tenacidad es un aspecto crítico para garantizar operaciones de perforación seguras y eficientes.. Si bien el proceso de producción puede ser complejo, los beneficios en términos de durabilidad, seguridad, y el ahorro de costos lo convierten en una inversión que vale la pena.
La invención pertenece al campo técnico de la fabricación de tubos de acero sin costura en la industria metalúrgica., y en particular se refiere a una carcasa de petróleo con resistencia y tenacidad súper altas adecuadas para pozos profundos o pozos ultraprofundos y un método de producción de la misma..
para que la pintura se absorba en la pieza de trabajo en la superficie
Con el aumento de la profundidad de perforación en campos de petróleo y gas., el aumento de temperatura y presión, El entorno geológico de la carcasa de petróleo utilizada para bocas de pozo fijas ha cambiado significativamente., y las condiciones mecánicas utilizadas también han cambiado en consecuencia. La carga de extrusión externa que soporta y las cargas axiales son cada vez mayores.. Las carcasas de aceite de alta calidad, como las V125 especificadas por la norma del Instituto Americano del Petróleo, generalmente utilizan aceros de aleación de la serie Cr-Mo-V.. Debido a la compleja fundición, Procesos de laminación y tratamiento térmico de carcasas de aceite de este tipo de acero., La composición de la aleación y el proceso de fabricación no son apropiados.. , causará que la resistencia y dureza de la carcasa de aceite disminuyan, y no puede soportar la carga de extrusión externa y la carga axial generada por pozos profundos o ultraprofundos, lo que agravará el daño y falla de la carcasa de aceite, y el daño y falla de la carcasa conducirá fácilmente a la falla del pozo.. Problemas complejos como la inestabilidad, daños al embalse, dificultades de perforación y cementación, etc., amenazar seriamente la seguridad de las operaciones petroleras, e incluso provocar grandes pérdidas económicas, como accidentes de destrucción de pozos.. Por lo tanto, El campo petrolero impone requisitos más altos sobre el rendimiento de la carcasa de petróleo..
En el presente, El problema a resolver para el revestimiento de petróleo para pozos profundos o ultraprofundos es la combinación de resistencia ultraalta y alta tenacidad.. El rendimiento de la carcasa de aceite de alta resistencia y tenacidad no sólo está relacionado con la composición del material utilizado., pero también muy relacionado con su método de fabricación.. Como todos sabemos, La tenacidad al impacto del acero de ultra alta resistencia depende de la pureza del acero., la composición y refinamiento de la estructura. Se adopta tecnología de fundición ultrapura para reducir el contenido de azufre., elementos de impureza de fósforo y gases en acero de ultra alta resistencia tanto como sea posible, y reducir el número de inclusiones, para que se pueda obtener una tenacidad al impacto satisfactoria. Utilizar un proceso de tratamiento térmico adecuado, La microestructura caracterizada por martensita de listón ultrafina como matriz y fase dúctil de austenita dispersa se obtiene en acero de ultra alta resistencia., y obtenidos durante el proceso de laminado y enderezamiento. El tamaño de la carcasa de aceite y la calidad de la superficie de alta precisión y la baja tensión residual son las formas técnicas y efectivas clave para lograr una carcasa de aceite de resistencia y tenacidad ultra altas..
sin embargo, Los grados de acero utilizados actualmente en las carcasas de petróleo contienen altas impurezas como azufre y fósforo., y la estructura metálica contiene inclusiones escamosas. El flujo desigual del metal durante el proceso de laminación da como resultado propiedades mecánicas inconsistentes en las direcciones horizontal y vertical.. Por otra parte, en el método actual de producción de carcasas de petróleo, El medio de enfriamiento en el proceso de tratamiento térmico es agua., que es fácil de causar grietas. Al mismo tiempo, debido al proceso irrazonable de perforación y laminado, proceso de tratamiento térmico y método de alisado, lo mejor La fuerza y dureza de la carcasa coinciden, y causar estrés residual excesivo, y la precisión de las dimensiones geométricas de la carcasa es deficiente, lo que afecta directamente la capacidad del producto para resistir el colapso.
Contenido de la invención
El propósito de la invención es superar las deficiencias de la técnica anterior y proporcionar una carcasa de petróleo con alta resistencia y tenacidad que pueda cumplir con los requisitos de pozos profundos o condiciones de producción paralela ultraprofunda en campos petroleros..
Otro objeto de la presente invención es proporcionar un método de producción de una carcasa de aceite con alta resistencia y tenacidad., que puede cumplir con las condiciones de producción de pozos profundos o pozos ultraprofundos en campos petroleros.
La presente invención se realiza mediante el siguiente esquema técnico.:
Una carcasa de aceite con alta resistencia y dureza., caracterizado porque los componentes en porcentaje en peso son: C: 0.22-0.35%, Si: 0.17-0.30%, Minnesota: 0.45-0.60%, CR: 0.80-1.10%, Mes: 0.70-1.10%, Alabama: 0.015-0.040%, Ni<0.20%, Cu<0.20%, V: 0.070-0.100%, NB<0.050%, como<0.0015%, P<0.010%, S<0.003% , y el equilibrio es hierro.
El papel de los principales elementos de aleación es:
C: 0.22-0.35%. C es un elemento formador de carburo que puede aumentar la resistencia del acero.. Si es demasiado bajo, el efecto no es obvio, y si es demasiado alto, Reducirá en gran medida la dureza del acero..
Minnesota: 0.45-0.60%, Mn es un elemento formador de austenita., que puede mejorar la templabilidad del acero, aumentar la cantidad de austenita retenida en el acero, Y afecta la uniformidad de la estructura laminada en caliente..
CR: 0.80-1.10%. El cromo puede mejorar las propiedades mecánicas., Resistencia a la corrosión y templabilidad del acero., pero puede aumentar la fragilidad del acero..
V: 0.070-0.100%, puede refinar granos, formar carburos, y mejorar la resistencia y tenacidad del acero. Pero cuando el contenido alcanza cierta cantidad, el aumento de su efecto no será evidente. Al mismo tiempo, porque el precio es alto, la cantidad de uso debe ser limitada.
Mes: 0.70-1.10%, principalmente a través del fortalecimiento de carburo y solución sólida para aumentar la resistencia del acero, si el contenido es demasiado alto, La tenacidad del acero se reducirá..
NB<0.050 refina principalmente los granos y mejora significativamente la tenacidad del acero de alta resistencia.
Ni<0.20 Mejora principalmente la resistencia y tenacidad del acero., mejora la resistencia a la corrosión del acero, y reduce la frágil temperatura de transición del acero..
Cu<0.20, El cobre en el acero aleado puede mejorar la resistencia y la resistencia a la corrosión atmosférica del acero., demasiada adición hará que el acero se vuelva quebradizo, generalmente no más de 0.2%.
Para garantizar una excelente combinación de resistencia y tenacidad, el método de producción de la carcasa de aceite de la presente invención comprende los siguientes pasos:
(1) Fundición de ingredientes: El hierro esponjoso y la chatarra de acero se utilizan como materias primas para la fabricación de acero., fundido en acero fundido en un horno de arco eléctrico (FEP), y el acero fundido para la fabricación de carcasas de petróleo se obtiene tras su refinado fuera del horno. (LF) y vacío (enfermedad venérea) desgasificación La composición en porcentaje en peso es: C: 0.22-0.35%, Si: 0.17-0.30%, Minnesota: 0.45-0.60%, CR: 0.80-1.10%, Mes: 0.70-1.10%, Alabama: 0.015-0.040%, Ni< 0.20%, Cu<0.20%, V: 0.070-0.100%, NB<0.050%, como<0.0015%, P<0.010%, S<0.003%, y el equilibrio es hierro.
(2) Colada y laminación continua: El acero fundido de alta pureza mencionado anteriormente se funde continuamente en un tocho redondo., y la palanquilla de colada continua enfriada se calienta en un horno de calentamiento anular. La temperatura del horno de calentamiento de palanquillas tubulares es 1300-1320 ° C. , laminación continua, reducción de diámetro fijo, enfriamiento, y aserrando; entre ellos, la temperatura de centrado del calor es 1260-1270 ° C, la temperatura de perforación caliente es 1240-1250 ° C, la temperatura de laminación continua es 1070-1120 ° C, y la temperatura de reducción del diámetro fijo es 910-910 °C 930°C.
Horno de anillo:
Temperatura de calentamiento del tubo en bruto: 1280~1290℃, diferencia de temperatura permitida: ±5℃.
Proceso de perforación:
Se utiliza un perforador cónico de tres rodillos para reducir la tensión de corte perforante del acero aleado y prevenir defectos como grietas., plegable, y delaminación en la superficie del capilar.. La tasa de alargamiento del piercing es 3.5-4.2, la relación diámetro-pared es 20-28, la tasa de expansión del diámetro está por debajo 35%, la velocidad de salida de la máquina perforadora es inferior a 0,9 m/s, y se requiere que la tolerancia del diámetro del tubo redondo de colada continua sea ≤±1,4% , Tolerancia de ovalidad ≤ 2.5%, Para garantizar el tamaño geométrico y la precisión de la forma del capilar.. La temperatura de perforación es de 1240-1250°C..
Proceso de laminación continua:
El propósito del proceso de laminación continua es reducir el diámetro., extender y reducir la pared del tubo capilar transferido desde el proceso de perforación, y al mismo tiempo mejorar la rugosidad de las superficies interior y exterior del tubo en blanco y mejorar la uniformidad del espesor de la pared.
Durante el laminado continuo, la superficie interior del capilar está en contacto con el mandril en la parte superior del paso, pero no en la pared lateral. El metal en la parte superior del agujero se extiende debido a la presión externa del rodillo y la presión del mandril., y se expande en la dirección circunferencial mientras se extiende axialmente, mientras que el metal en la pared lateral del agujero también se expande cuando el metal en la parte superior del agujero se extiende. Se estira y correspondientemente se contrae en dirección longitudinal.. Controlar la tasa de reducción de cada proceso de laminación continua., de modo que la relación entre el área de la sección transversal efectiva del tubo en bruto antes y después de la deformación en el proceso de laminación continua sea 2.8 a 6.5, para garantizar que la energía de impacto vertical y horizontal de la carcasa de aceite tienda a ser consistente. La velocidad máxima de entrada del laminado continuo es de 1,5 m/s., la velocidad de salida es de 3,5 m/s, y la relación entre el área de la sección transversal del tubo capilar y el tubo en blanco es aproximadamente 3.7. La temperatura de rodamiento continuo es 1070~1120℃.
Proceso de reducción de diámetro fijo.:
El proceso de dimensionado y reducción es un proceso de laminación continua de cuerpos huecos.. Además del papel del dimensionamiento, también requiere una gran tasa de reducción, y el número de puestos de trabajo es 24. primero, Las tuberías de desagüe se calientan entre 920°C y 1050°C en el horno de recalentamiento y luego se liberan.. Después de medir la temperatura de la superficie a la salida de la mesa de rodillos., Se utiliza un dispositivo desincrustante de agua a alta presión de 20 MPa para eliminar las tuberías de desecho de la unidad de laminación continua durante el proceso de laminación.. Escala, Luego se lamina en un molino calibrador y reductor.. La temperatura de laminación de tamaño es de 910-930 °C., La velocidad de entrada del rodamiento de tamaño está entre 0,5 y 1,4 m/s., la velocidad de salida está entre 0,51-7 m/s, y la relación de área transversal efectiva está dentro 1.5.
(3) Tratamiento térmico: Se adopta el proceso de tratamiento térmico de enfriamiento y luego revenido para el tubo ciego mencionado anteriormente..
El proceso de enfriamiento es el siguiente.: calentar la carcasa de petróleo a 940° C. a 920°C. y mantenerlo caliente durante 30 minutos para formar completamente austenita. El medio de enfriamiento es un líquido de enfriamiento aceitoso para aumentar la resistencia y dureza del acero..
El proceso de templado es el siguiente.: la temperatura de templado es de 640° C. a 660°C., preservación del calor para 2 horas, La refrigeración por aire se utiliza para refinar los granos de cristal., homogeneizar la estructura, eliminar el estrés interno, y mejorar la tenacidad del acero.
(4) La tubería de desagüe después del tratamiento térmico anterior se somete a un tratamiento de dimensionamiento y enderezamiento térmico., y finalmente detección de fallas para obtener la carcasa de petróleo terminada..
Para minimizar la tensión residual de la carcasa de aceite., Reducir la tensión residual causada por el dimensionamiento., mejorar la precisión del tamaño y la redondez de la carcasa de aceite, y mejorar las propiedades mecánicas de la carcasa de aceite., la temperatura de dimensionamiento está entre 550 y 600 °C Durante el periodo, La velocidad de salida del tamaño de la tubería de desagüe está entre 1.2 y 2,4 m/s.
En el proceso de alisado térmico, la reducción del límite elástico de 1.55 a 1.75 veces (La reducción del límite elástico es el punto de partida de la deformación plástica de la superficie de la tubería de acero.) y se seleccionan la temperatura de alisado adecuada para reducir la tensión residual generada por el proceso de alisado.. Mejore la redondez y rectitud de la carcasa de aceite y mejore el rendimiento de la carcasa de aceite.. La temperatura óptima determinada mediante cálculos teóricos y experimentos es 450-580°C., pero en el proceso real, por el bien de la seguridad, la temperatura de alisado térmico está entre 500°C-540°C.
Para mejorar el rendimiento de la carcasa de aceite., Se ha establecido un estricto rango de control de precisión geométrica.. La precisión geométrica de la carcasa cumple los siguientes requisitos: el error de diámetro es ±0,8% del tamaño del diámetro, el error del espesor de la pared es ±8% del tamaño del espesor de la pared, y la elipse El error de rectitud del extremo de la tubería es ±0,5%, El error de rectitud del extremo del tubo es de 1,5 mm/m., y el error de rectitud del cuerpo de la tubería es de 1,0 mm/m.
La carcasa de aceite fabricada mediante el método de producción de la invención puede alcanzar el grado de acero V150.. Los indicadores logrados por las propiedades mecánicas de la carcasa de aceite son los siguientes:
Fuerza de producción: 1057~1210MPa
Resistencia a la tracción: ≥1180MPa
Dureza al impacto: Energía de impacto Charpy longitudinal a gran escala ≥ 80J
Energía de impacto Charpy transversal a gran escala ≥ 75J
Alargamiento: ≥16%
El rendimiento general de la carcasa. (tome φ244,48 × 15,11 como ejemplo)
Resistencia anticolapso del cuerpo de la tubería: ≥80MPa;
Fuerza de deslizamiento: ≥2800KN;
Límite elástico en la tubería.: ≥115MPa;
Estrés residual: ≤200MPa.
Dimensiones geométricas de la carcasa de aceite.;
Rango de diámetro: 242.52milímetro~246.43m m;
fuera de redondez: ≤1,2 mm;
Espesor de la pared: -8.0%t~8,0%t;
Rectitud: extremo del tubo 1,5 mm/m, cuerpo del tubo 1,0 mm/m.
La presente invención tiene el siguiente efecto técnico.:
1. El aceite pipa de la cubierta de la presente invención adopta un sistema de aleación Cr-Ni-Mo-V de grado de acero templado y revenido., que puede obtener una cierta cantidad de tenacidad de austenita dispersada en la matriz de martensita de listón ultrafino después de la fase de tratamiento térmico, Mejorar la resistencia y tenacidad del acero para adaptarse y soportar la carga de extrusión externa y la carga axial generada por pozos profundos o ultraprofundos..
2. En el método de producción de la presente invención, mediante la formulación racional de procesos como la perforación y laminación, Los granos de cristal del acero se pueden refinar al máximo., y se pueden evitar defectos estructurales.
3. En el método de producción de la presente invención, La selección del proceso de tratamiento térmico es razonable., y es posible formar una martensita de listón de orden submicrónico como matriz, una partícula de segunda fase a nanoescala como fase de refuerzo de la precipitación y una cierta cantidad de austenita con alta estabilidad. La estructura compuesta multifase de la fase resistente garantiza una excelente combinación de resistencia y tenacidad..
4. En el método de producción de la presente invención, el proceso de alisado térmico está razonablemente formulado, que puede minimizar la tensión residual de la carcasa.
5. Se ha formulado un estricto rango de control de precisión geométrica., que puede mejorar el rendimiento de la carcasa de aceite a un costo razonable.
6. El medio de enfriamiento en el proceso de tratamiento térmico de la presente invención es un líquido de enfriamiento aceitoso., que puede evitar defectos como grietas en la superficie de la tubería de acero.
Formas detalladas
La presente invención se describirá en detalle a continuación junto con ejemplos específicos..
La presente invención se describirá en detalle a continuación tomando como ejemplo la producción de una carcasa de aceite de φ244,48×15,11..
Ejemplo:
El hierro esponjoso y la chatarra de acero se utilizan como materias primas para la fabricación de acero., y fundido en acero fundido en un horno de arco eléctrico. Después del refinado fuera del horno y desgasificación al vacío., Los componentes del acero fundido para la fabricación de carcasas de petróleo son.: C: 0.22-0.35%, Si: 0.17-0.30%, Minnesota: 0.45-0.60%, CR: 0.80-1.10%, Mes: 0.70-1.10%, Alabama: 0.015-0.040%, Ni<0.20%, Cu<0.20%, V: 0.070-0.100%, NB<0.050%, como<0.0015%, P<0.010%, S<0.003%, y el equilibrio es hierro.
El acero fundido anterior se funde continuamente en un tocho redondo.. Calentar la palanquilla de colada continua enfriada en el horno de calentamiento de anillos., La temperatura del horno de calentamiento de palanquillas de tubos es de 1310 °C., después, centrado, perforación, laminación continua, dimensionamiento y reducción, enfriamiento, aserrado; entre ellos, el centrado de calor es 1265°C , La temperatura de perforación en caliente es de 1245 °C., La temperatura de laminación continua es de 1100°C., y la temperatura de reducción del diámetro fijo es de 920°C. Se enfría rápidamente a 450 °C mediante lecho de enfriamiento y método de enfriamiento por soplado., y aserrando. El proceso de tratamiento térmico de enfriamiento y luego revenido se adopta para el tubo en blanco mencionado anteriormente.: enfriamiento a 930°C (líquido de enfriamiento aceitoso), templado a 645°C. Después del dimensionamiento por calor a 560°C, alisado con calor a 520°C, y detección final de defectos, Se obtiene la carcasa de aceite terminada..
En el proceso de perforación, la tasa de elongación es 3.7, la tasa de expansión del diámetro es 28%, y la velocidad de salida de la máquina perforadora es de 0,7m/s. En el proceso de laminación continua, la relación entre el área de la sección transversal efectiva del tubo desnudo antes y después de la deformación por laminación continua es 4.3, la velocidad de entrada es 1.2m/s, y la velocidad de salida es 2.9m/s. En el proceso de diámetro fijo y reducido, la relación de área de sección transversal efectiva es 1.2, la velocidad de entrada es 0.9m/s, y la velocidad de salida es 1.3m/s. La velocidad de salida del tamaño del tubo ciego es de 1,8 m/s.. En el proceso de alisado térmico, el coeficiente de reducción del enderezamiento es 1.6 veces la reducción del límite elástico.
Las propiedades mecánicas de la carcasa de aceite producida por el método anterior pueden alcanzar los siguientes indicadores:
Fuerza de producción: 1109MPa;
Resistencia a la tracción: 1213MPa;
Dureza al impacto: Energía de impacto Charpy longitudinal a gran escala: 121J;
Energía de impacto Charpy horizontal a gran escala: 114J;
Alargamiento: 17%.
El rendimiento general de la carcasa.:
Resistencia al colapso de la tubería: 93.1MPa;
Fuerza de deslizamiento: 3208KN;
Límite elástico en el tubo.: 130.6MPa;
Estrés residual: 162.31MPa.
Dimensiones geométricas de la carcasa de aceite.:
Rango de diámetro: 245.90milímetro~246.20m m;
fuera de redondez: ≤0,6 mm;
Espesor de la pared: -4.5%t~7,0%t;
Rectitud: extremo del tubo 1,2 mm/m, cuerpo del tubo 0,9‰.
La carcasa de petróleo producida mediante el diseño tipo acero de la invención y el control razonable de diversas condiciones del proceso puede cumplir con los requisitos de resistencia y tenacidad de pozos profundos o pozos ultraprofundos.. Controlar la deformación por rodadura y el tratamiento térmico., obtener efectos como el fortalecimiento de la precipitación, Refinamiento de grano y fortalecimiento de transformación de fase., mejorar la resistencia y tenacidad del acero, y resolver el problema de las grietas fáciles en el tratamiento térmico de tubos de acero sin costura de acero aleado. Uso de métodos de procesamiento de encolado térmico y enderezamiento térmico., Se soluciona la baja tensión residual que requieren los tubos de acero sin costura., y la flexión, deformación elíptica, y se controla la precisión dimensional de los tubos de acero sin costura.