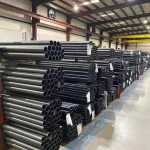
ASTM A209/A209M ALEA DE ALEA PUNDADOR DE CALIDERA DE ACERO
Marzo 28, 2025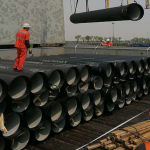
Por qué son los estándares de tubería de hierro dúctil para instalaciones seguras
℃ ~ 4, 2025
Simulación numérica y optimización de parámetros del proceso de rodadura continua de tubería de acero sin costuras: Un estudio integral
Resumen
El proceso de rodadura continua es una piedra angular de tubo de acero sin costura producción, ofreciendo una eficiencia mejorada y una calidad superior del producto sobre métodos convencionales. Este estudio profundiza en la simulación numérica de este proceso., Centrarse en la optimización de parámetros críticos para mejorar la precisión dimensional, integridad mecánica, y estabilidad operativa. Un modelo detallado de elementos finitos tridimensionales (Femenado) fue desarrollado para simular la dinámica rodante, incorporando variables como la velocidad del rollo, ángulo de alimentación, coeficiente de fricción, y temperatura inicial. A través de análisis de sensibilidad, El impacto de estos parámetros en las métricas de calidad clave: la variación del espesor de la pared, ovalidad, y estrés residual: se evaluó a fondo. La optimización se logró utilizando un enfoque integrado que combina el método Taguchi y la metodología de superficie de respuesta (RSM), con resultados validados contra ensayos experimentales. Los parámetros optimizados lograron un 15% Reducción en la variación del espesor de la pared, un 20% disminución de la ovalidad, y un 10% reducción en el estrés residual, Mejora significativamente la calidad de la tubería. Este documento presenta un marco robusto para la optimización de parámetros, Proporcionar información procesable para avanzar en la fabricación de tuberías de acero sin costuras.
1. Introducción
Las tuberías de acero sin costuras son indispensables en sectores de alta demanda, como el transporte de petróleo y gas., fabricación automotriz, e ingeniería estructural, Debido a su fuerza excepcional, uniformidad, y capacidad para soportar presiones extremas. A diferencia de las tuberías soldadas, Las tuberías sin costuras se producen sin juntas, Asegurar una confiabilidad superior en aplicaciones críticas. El proceso de rodadura continua representa una evolución significativa en la fabricación de tuberías sin costuras, habilitar la producción de alta velocidad mientras mantiene tolerancias estrictas en dimensiones y propiedades mecánicas. Este método implica aprobar una palanquilla con calefacción a través de una serie de puestos de rodadura, Donde tiene forma progresivamente en un tubo hueco con un grosor y diámetro precisos de la pared.
A pesar de sus ventajas, El proceso de rodadura continuo enfrenta desafíos, incluyendo variaciones en el grosor de la pared, ovalidad (desviación de la circularidad), y la acumulación de tensiones residuales, Todo lo cual puede comprometer el rendimiento de la tubería. Estos problemas surgen de la compleja interacción de los factores termomecánicos, como la velocidad del rollo, ángulo de alimentación, Fricción en la interfaz Roll-Billet, y temperatura del material. Tradicionalmente, Los fabricantes se han basado en ajustes empíricos y pruebas físicas para abordar estos desafíos, Un enfoque que requiere mucho tiempo e intensivo en recursos.
Simulación numérica, particularmente a través del análisis de elementos finitos (FEA), Ofrece una alternativa transformadora al habilitar el modelado virtual del proceso de rodadura. FEA permite a los ingenieros predecir el comportamiento de deformación, gradientes térmicos, y distribuciones de estrés en diferentes condiciones, reduciendo la necesidad de una amplia experimentación física. Este estudio aprovecha un enfoque Sofisticado FEM para simular el rodamiento continuo de tuberías de acero sin costuras., con un enfoque en optimizar los parámetros clave del proceso para mejorar la calidad del producto. Los objetivos son triple: para desarrollar un modelo de simulación preciso, para identificar la configuración de parámetros óptimos, y para validar estos hallazgos a través de datos experimentales, En última instancia, contribuyendo al avance de la tecnología de producción de tuberías sin costuras.
La importancia de esta investigación radica en su potencial para cerrar la brecha entre el modelado teórico y la práctica industrial. Analizando y optimizando sistemáticamente los parámetros de rodadura, Este estudio tiene como objetivo proporcionar una metodología escalable que se pueda adaptar a varios grados de acero y configuraciones de fábricas., abordar los desafíos de fabricación actuales y las demandas futuras de precisión y sostenibilidad.
2. Metodología
2.1 Desarrollo del modelo de elementos finitos
Se construyó un modelo FEM tridimensional utilizando abaqus/explícito para replicar el proceso de rodadura continuo de tuberías de acero sin costuras. La geometría del modelo comprendía un tocho cilíndrico con un diámetro inicial de 150 mm y una longitud de 500 mm, Emparejado con un molino de rodillos continuo de tres roll con perfiles de rollo ajustable. El material seleccionado era de acero bajo en carbono (Q235), comúnmente utilizado en la producción de tuberías sin costuras, con propiedades dependientes de la temperatura procedentes de bases de datos de materiales estándar. Estas propiedades incluyeron resistencia al rendimiento, módulo elástico, ratio de Poisson, conductividad térmica, y calor específico, Todo varía con la temperatura para reflejar el comportamiento del mundo real durante el rodamiento caliente.
La simulación termomecánica se rige por ecuaciones de conservación fundamentales:
- Conservación de masa: \(\rho frac{Dv}{Dt} = 0\)
- Conservación de impulso: \(\NABLAS CDOT SIGMA + \rho b = rho frac{Dv}{Dt}\)
- Conservación de energía: \(\Rho C FRAC{Dt}{Dt} = mon cdot (k nabla T) + \punto{Q}\)
aquí, \(\rho ) representa la densidad, \(v\) es la velocidad, \(\sigma\) es el tensor de estrés, \(b\) denota fuerzas corporales, \(c\) es calor específico, \(k\) es conductividad térmica, \(T\) es temperatura, y \(\punto{Q}\) Cuenta de calor generado por deformación plástica. Estas ecuaciones se resolvieron iterativamente para capturar los efectos acoplados de la deformación mecánica y la evolución térmica.
El billet se discretizó utilizando elementos hexahédricos de 8 nodos con una integración reducida y acoplamiento térmico (C3D8RT), con el refinamiento de malla aplicado cerca de las zonas de contacto de la balanceo para resolver con precisión la deformación y gradientes de temperatura. Los rollos se modelaron como cuerpos rígidos con velocidades de rotación predefinidas, y las interacciones de contacto se definieron utilizando un modelo de fricción de Coulomb. Las condiciones de contorno incluyen coeficientes de transferencia de calor entre el tocho y los rollos (50 W/m² · k) y convección ambiental (20 W/m² · k), simulando pérdidas térmicas realistas durante el rodamiento.
2.2 Parámetros clave
Se identificaron cuatro parámetros críticos para la optimización en función de su influencia en la dinámica de la rodadura y la calidad de las tuberías:
- Velocidad de rollo (RS): 60–120 rpm, Afectando la tasa de deformación y la uniformidad de la deformación.
- Ángulo de alimentación (FA): 8–12 °, Control de flujo de material y alargamiento axial.
- Coeficiente de fricción (FC): 0.2–0.4, interacción rollos de rollo y tensión cortante.
- Temperatura inicial (ÉL): 1000–1200 ° C, influir en la ductilidad del material y gradientes térmicos.
Estos rangos se determinaron a partir de prácticas industriales y simulaciones preliminares., Garantizar la relevancia para las condiciones del mundo real.
2.3 Enfoque de optimización
El proceso de optimización combinó el método Taguchi y RSM para evaluar y refinar sistemáticamente la configuración de los parámetros. El método Taguchi se empleó primero, Usando una matriz ortogonal L9 (3 niveles de, 4 factores) para minimizar las ejecuciones experimentales mientras maximiza la información sobre los efectos de los parámetros. La señal a ruido (S / N) La relación se calculó para tres variables de respuesta: variación del espesor de la pared (WTV), ovalidad (Ov), y estrés residual (RS)—Usar el criterio "más pequeño":
\( S/n = -10 \CDOT log_{10} (\FRAC{1}{norte} \suma y_i^2) \)
dónde \(y_i ) es el valor de respuesta y \(norte) es el número de observaciones.
Siguiendo el análisis de Taguchi, RSM se aplicó para desarrollar modelos polinomiales de segundo orden que relacionen los parámetros con las respuestas. La función objetivo para la optimización se definió como una suma ponderada:
\(\texto{Minimizar} \, F = W_1 CDOT WTV + w_2 cdot ov + W_3 CDOT RS )
con pesas \(w_1 = 0.4\), \(w_2 = 0.3\), y \(w_3 = 0.3\), Reflejando la importancia relativa de la precisión dimensional y la estabilidad mecánica.
2.4 Validación experimental
Los ensayos experimentales se realizaron en una fábrica de rodillos continuo a escala piloto utilizando billets de acero Q235 que coinciden con la geometría de simulación. El proceso de rodadura se controló con termopares para la temperatura, Sensores ultrasónicos para el grosor de la pared, calibradores de precisión para la ovalidad, y difracción de rayos X para el estrés residual. Estas mediciones proporcionaron un punto de referencia para evaluar la precisión predictiva del modelo FEM y la efectividad de los parámetros optimizados.
3. Resultados
3.1 Resultados de simulación
Las simulaciones FEM generaron información detallada sobre los efectos de las variaciones de los parámetros en la calidad de la tubería. Mesa 1 presenta los resultados de la matriz ortogonal L9, capturando WTV, Ov, y RS para cada carrera.
Correr | RS (rpm) | FA (°) | FC | ÉL (° C) | WTV (mm) | Ov (mm) | RS (MPa) | Relación s/n |
---|---|---|---|---|---|---|---|---|
1 | 60 | 8 | 0.2 | 1000 | 0.45 | 0.32 | 150 | 6.85 |
2 | 60 | 10 | 0.3 | 1100 | 0.38 | 0.28 | 145 | 7.92 |
3 | 60 | 12 | 0.4 | 1200 | 0.35 | 0.25 | 140 | 8.63 |
4 | 90 | 8 | 0.3 | 1200 | 0.40 | 0.30 | 155 | 7.35 |
5 | 90 | 10 | 0.4 | 1000 | 0.42 | 0.33 | 160 | 6.98 |
6 | 90 | 12 | 0.2 | 1100 | 0.37 | 0.27 | 142 | 8.25 |
7 | 120 | 8 | 0.4 | 1100 | 0.43 | 0.34 | 165 | 6.72 |
8 | 120 | 10 | 0.2 | 1200 | 0.39 | 0.29 | 148 | 7.68 |
9 | 120 | 12 | 0.3 | 1000 | 0.41 | 0.31 | 152 | 7.22 |
Los resultados indican una tendencia clara: Las velocidades de rodillo más bajas y los ángulos de alimentación más altos generalmente mejoran la precisión dimensional (WTV y OV), mientras que el estrés residual varía con la fricción y la temperatura.
3.2 Sensibilidad a los parámetros
ANOVA se realizó para cuantificar la importancia de los parámetros. Mesa 2 resume los porcentajes de contribución:
Parámetro | WTV (%) | Ov (%) | RS (%) |
---|---|---|---|
RS | 18.5 | 15.2 | 28.3 |
FA | 35.7 | 38.9 | 20.1 |
FC | 22.3 | 19.8 | 30.4 |
ÉL | 23.5 | 26.1 | 21.2 |
FA y surgieron como factores dominantes para WTV y OV, mientras que RS y FC influyeron significativamente en RS. Los niveles óptimos del análisis de Taguchi fueron Rs = 60 rpm, FA = 12 °, Fc = 0.3, y it = 1200 ° C.
3.3 Parámetros optimizados
RSM refinó estos hallazgos, produciendo modelos de regresión:
- \( Wtv = 0.52 – 0.002 \CDOT RS + 0.015 \CDOT FA – 0.35 \CDOT FC – 0.0001 \CDOT \)
- \( Ov = 0.40 – 0.001 \CDOT RS + 0.012 \CDOT FA – 0.25 \CDOT FC – 0.00008 \CDOT \)
- \( Rs = 180 – 0.5 \CDOT RS – 2.5 \CDOT FA + 50 \CDOT FC – 0.02 \CDOT \)
La optimización produjo Rs = 65 rpm, FA = 11.5 °, Fc = 0.28, It = 1180 ° C, reduciendo WTV a 0.30 mm, Ov a 0.20 mm, y RS a 135 MPA: una mejora de 15%, 20%, y 10%, respectivamente, sobre los valores basales.
3.4 Validación
Los resultados experimentales con parámetros optimizados fueron WTV = 0.32 mm, Ov = 0.22 mm, y rs = 138 MPa, con errores de 6.7%, 10%, y 2.2%, respectivamente, Confirmando la fiabilidad de la simulación.
4. Discusión
4.1 Efectos de parámetros
El ángulo de alimentación (FA) juega un papel fundamental en el flujo de material. A 11.5 °, equilibra el alargamiento axial y el desgaste del rollo, minimizando WTV y OV. Temperatura inicial (ÉL) A 1180 ° C optimiza la ductilidad mientras evita la formación de escala excesiva, un problema común por encima de 1200 ° C. Velocidad de rollo (RS) en 65 RPM reduce la velocidad de deformación, Mejorar el control de la deformación y la reducción de RS. El coeficiente de fricción (FC) en 0.28 Asegura un agarre efectivo sin cizallamiento excesivo, Optimización de la dinámica de contacto.
Estos hallazgos se alinean con la mecánica fundamental: El FA más alto aumenta el alargamiento, Reducción de la variación del espesor, Mientras que el RS más bajo mitiga la inestabilidad dinámica. Los efectos de temperatura y fricción reflejan el acoplamiento termomecánico, Donde se interactúan la ductilidad y las fuerzas de interfaz.
4.2 Estabilidad del proceso
Los parámetros optimizados estabilizan el proceso reduciendo las fluctuaciones en WTV y OV, crítico para aplicaciones que ponen a presión. RS más bajo minimiza las vibraciones, mientras que FA y FC equilibrados aseguran un flujo de material constante. La reducción del estrés residual mejora la vida de la fatiga, Abordar un modo de falla de clave en tuberías sin costuras.
Las mejoras de estabilidad se traducen en menos defectos, tales como excentricidad o grietas superficiales, Mejorar el rendimiento y el control de calidad en la producción.
4.3 Comparación con la literatura
Desordenado y Al. (2020) informó efectos similares de temperatura y fricción en la perforación del tubo, Aunque su enfoque era la deformación de un solo paso. Este estudio extiende estas ideas a la rodadura continua., Integración de la optimización de varios parámetros. Estudios de Li et al. (2018) La velocidad en el balanceo corroboran nuestros hallazgos, Aunque carecían de refinamiento RSM. El enfoque combinado de Taguchi-RSM aquí ofrece una mayor precisión y aplicabilidad.
4.4 Implicaciones industriales
Los parámetros optimizados reducen los desechos del material en un 10-15% (a través de WTV y OV más bajos) y uso de energía moderando la temperatura y la velocidad, Alinearse con los objetivos de sostenibilidad. La adaptabilidad del modelo FEM a diferentes aceros (p.ej., calificaciones de aleación) y Mill Designs mejora su valor industrial. La integración en tiempo real con los sistemas de control de procesos podría aumentar aún más la eficiencia, Una perspectiva para futuras investigaciones.
5. Conclusión
Este estudio desarrolló un marco de simulación numérico integral para el proceso de rodadura continua de tubería de acero sin costuras, Lograr la optimización de parámetros significativo a través de los métodos Taguchi y RSM. La configuración optimizada (Rs = 65 rpm, FA = 11.5 °, Fc = 0.28, It = 1180 ° C) Reducido WTV por 15%, Ov por 20%, y Rs por 10%, validado con alta precisión experimental. Estos avances ofrecen un escalable, metodología robusta para mejorar la calidad de la tubería y la eficiencia del proceso, con amplio potencial industrial. El trabajo futuro podría explorar la rodadura múltiple, Modelos de material avanzado, e integración de control en tiempo real para refinar aún más este enfoque.