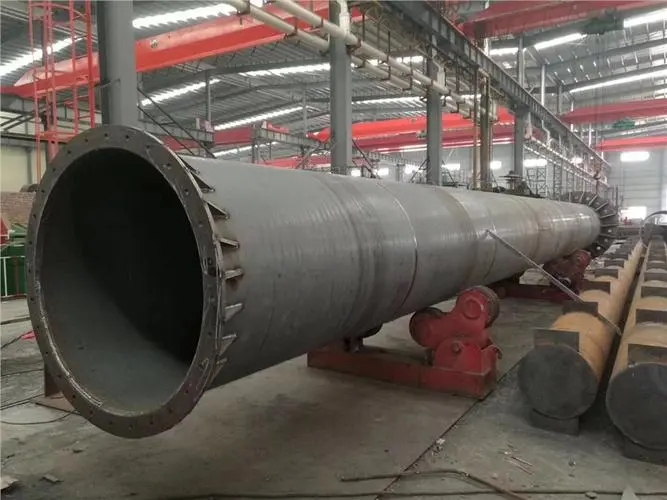
Cómo se produce el desgaste en las tuberías y por qué el acero resistente al desgaste de alta resistencia supera a las tuberías de acero normales en entornos abrasivos
junio 21, 2022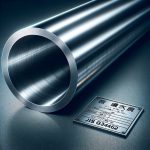
Conocimientos básicos y usos de los tubos de acero sin costura, carcasas y tubos de aceite
junio 23, 2022Reducir la cantidad de variación, o lograr una mayor consistencia en el grosor de la pared, puede ser la diferencia entre cumplir con los requisitos de un cliente o no. También ayuda a reducir o incluso puede eliminar la necesidad del cliente de procesos posteriores como el mecanizado..
El tubo sin costura generalmente se fabrica en un molino perforador de dos rodillos. En algunos casos, este paso por sí solo es suficiente para producir un tubo que satisfaga los requisitos del cliente.. sin embargo, si la consistencia del grosor de la pared necesita mejorar aún más después de perforar, un productor de tubos puede utilizar equipos y pasos de proceso adicionales. Dos de estos tipos de equipos son un molino alargador de laminación cruzada (comúnmente conocido por su nombre comercial, como un molino Assel o Diescher), y un banco de extracción en frío.
Descripción general de los tres pasos del proceso
La fabricación de tubos sin costura suele comenzar con el laminado cruzado en caliente en un laminador perforador. La perforación es el primer paso del proceso para hacer un tubo con una pared de alta calidad.. Este paso generalmente es seguido por uno o más procesos de elongación que pueden mejorar la calidad de la pared y al mismo tiempo aumentar la longitud del tubo.. Después de que el tubo sale del molino sin soldadura y se enfría, se puede terminar en un banco de estirado en frío como tercer paso para mejorar las tolerancias de la pared.
Molino perforado. La mayor parte de la atención sobre la calidad de la pared sin juntas se dirige a la fresa perforadora.. Esta atención se justifica porque el molino perforador tiene el mayor efecto sobre la variación de la pared.. La tubería producida por un molino perforador se puede optimizar para 7 a 10 porcentaje de variación de la pared.
Aunque una concha perforada puede tener menos de 10 porcentaje de variación de la pared, esta cantidad de variación es para una sección de pared relativamente gruesa. Por ejemplo, lograr una tolerancia de pared de ±10 por ciento produce un tubo con un rango de espesor de pared de 13.5 mm (0.531 en.) a 16.5 mm (0.650 en.) o más cuando se pide en 15 mm (0.590 en.). Es posible que se requiera un procesamiento adicional por parte de un molino de alargamiento para requisitos más estrictos del cliente.
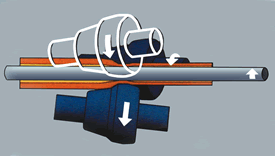
El proceso de laminación cruzada utiliza tres rodillos de trabajo para reducir el diámetro exterior y el grosor de la pared del tubo.. Dibujo cortesía de Copperweld, Shelby, Ohio.
Molino alargador. En la industria de producción de tubos se utilizan cinco tipos principales de molinos alargadores: el molino de tubos de mandril, el banco de empuje, el molino de enchufe, el molino reductor de estiramiento, y el molino alargador de laminación cruzada. Cincuenta años de uso en toda la industria han demostrado que, de estos molinos alargadores, el alargador de laminación cruzada proporciona la mejora más significativa en la tolerancia de la pared del tubo producido en un molino perforador. Un molino alargador de laminación cruzada utiliza rodillos de trabajo en el diámetro exterior y un mandril en el diámetro interior. (Ver Figura 1).
Banco de estirado en frío. Dibujar en un banco es un método de acabado en frío que mejora la dimensión de la pared del tubo sin costura. En el proceso de banco de dibujo, primero, el tubo se enrosca sin apretar en un mandril unido a una varilla. Luego, un conjunto de pinzas agarra el tubo y lo tira a través de un troquel estacionario de carburo o acero para herramientas.. El resultado es un tubo personalizado con muy buen control dimensional. La tolerancia típica del diámetro exterior es de ±0,1 mm (±0,004 pulg.), que es aproximadamente una décima parte de la tolerancia de un tubo sin costura típico con acabado en caliente.
Los beneficios adicionales del proceso de dibujo incluyen un acabado superficial mejorado, la capacidad de proporcionar tolerancias de identificación, y propiedades mecánicas mejoradas. Tubos producidos con este proceso requieren un procesamiento mínimo o adicional y se consideran productos de valor agregado.
Directrices para elongación transversal
Para alargamiento por laminación cruzada, Dos requisitos principales se relacionan con el caparazón perforado.. Estos están llenando la sección de altura de la joroba para 80 a 90 por ciento de su diseño y maximizar el agarre lateral de entrada. Ambos requisitos están relacionados con el diseño del paso de rodillos en el molino Assel..3
Figura 2
La joroba del rodillo se encuentra cerca de la mitad del rodillo de trabajo.. Es importante hacer coincidir la sección del tubo que ingresa al molino con las características de diseño de los rodillos de trabajo.. Dibujo cortesía de Copperweld, Shelby, Ohio.
llenando la joroba. Joroba es un término general para la región cerca de la mitad del rollo de trabajo que contiene un perfil elevado (Ver Figura 2). Rellenar la joroba es una cuestión de medir la pared perforada y luego compararla con la dimensión conocida de la joroba de la impresión.. Luego se ajusta el molino perforador para obtener el valor adecuado. Por ejemplo, si el diseño de la joroba es 8 mm (0.315 en.), la concha perforada debe medir 7 mm (0.276 en.) más que el tamaño del cliente (porque 7 es 90 por ciento de 8).
Esta relación es importante en la producción de tubos de pared delgada porque la tolerancia de la pared para los tubos mecánicos se basa en porcentajes. (según la norma ASTM A519). Las tolerancias para tubos de paredes más delgadas son más difíciles de lograr porque, por ejemplo, 5 por ciento de 5 mm (0.197 en.) es una dimensión mucho más estrecha que 5 por ciento de 10 mm (0.394 en.). Los productores de tubos deben entender que si la capacidad del molino es 1 mm (0.040 en.) de la variación de la pared, esto podría representar la mitad de la tolerancia comercial para secciones de pared media (valor cp de 2.0) y variación fuera de tolerancia para secciones de pared delgada (Cp de menos de 1.0).
Es necesario reducir el grosor de la pared de la carcasa del molino perforador para garantizar un llenado adecuado a la altura de la joroba.. Para tubos de pared extremadamente delgada, los fabricantes pueden encontrar que la mejora de la calidad en el laminador cruzado puede ser difícil, si no imposible, de lograr porque la carcasa perforada tiene demasiada variación. Para algunos tamaños de tubo, la variación de la pared como porcentaje se puede aumentar en lugar de disminuir en el molino perforador. El porcentaje de variación se determina mediante un cálculo cuidadoso. Aunque la variación dimensional total disminuye el numerador, el denominador disminuye a un ritmo mayor porque el tubo del tren de alargamiento de laminado cruzado ha 50 a 75 por ciento menos de espesor de pared que el tubo del molino perforador.
Agarre de rodadura cruzada. El segundo requisito es mantener el mejor agarre en el proceso de laminado cruzado.. El agarre se define como el número de espirales del tubo antes de la línea central de la joroba en el diseño de paso de rodillo del laminador cruzado del alargador, en términos simples., la cubierta perforada debe hacer contacto con la cara del rodillo al principio del proceso para que la alimentación del tubo se establezca antes de que llegue a la zona de trabajo en la sección de joroba. El trabajo realizado en la sección de la joroba requiere una cantidad extrema de energía., hasta varios miles de caballos de fuerza. La fuerza de trabajo se aplica en un tramo muy corto, normalmente 15 a 25 mm (menos de 1 en.) amplio. Si el tubo no está bien sujeto, girará en lugar de alimentarse, o puede alimentarse irregularmente a través de la zona de trabajo, creando variación.
En la mayoría de los casos, la mejor condición para la carcasa perforada se logra al producir el diámetro exterior máximo que encajará correctamente en la cara del rodillo del tren de alargamiento de laminación transversal.. Por lo general, esta relación se resuelve ajustando la configuración del molino perforador para producir la dimensión correcta del tubo.. Pero en algunos casos puede ser necesario aumentar o disminuir ligeramente el ángulo divergente del molino alargador para garantizar que la carcasa se ajuste y agarre correctamente..
Los experimentos realizados sobre la calidad de la pared de los tubos tomados directamente de un molino alargador se utilizaron para determinar si los tubos tenían una mejor calidad de pared que los tubos procesados posteriormente por un molino de tamaño o un molino reductor de estiramiento.. Se determinó que en el proceso de reducción de tamaño, las fuerzas longitudinales y de compresión actúan sobre la pared y pueden aumentar la variación de la pared. Los tubos extraídos directamente de un tren de alargamiento de laminación cruzada tienen una consistencia de espesor de pared superior y una mejor calidad de superficie porque no están expuestos a las condiciones de laminación en el tren de encolado.. Tubos que han pasado por un molino de encolado, sin embargo, se puede reducir la variación de la pared estirando en frío en un banco de estirado.
Directrices para el estirado en frío
El éxito en el procesamiento de tubos sin costura estirados en frío depende de mantener una alta calidad de pared del tren de laminación en caliente sin costura y de seleccionar adecuadamente las herramientas de banco de estirado en frío (juegos de mandriles y matrices).
Los tres puntos principales relacionados con el dibujo del tubo perforado son:
- Se necesita algo de reducción de la pared para garantizar que el mandril muerda contra la pared al comienzo del estirado y luego asiente correctamente el mandril en el cojinete del dado durante el estirado.. Si la pared entrante es demasiado irregular o demasiado clara, el mandril no avanzará hacia el cojinete del dado, y el tubo resultante no tendrá buenas tolerancias para la dimensión exterior, dimensión interior, y espesor de pared.
- El dibujo de banco está limitado a un máximo 40 porcentaje de reducción en el área. Si la pared entrante es demasiado pesada, puede causar que el metal falle en lugar de ceder durante el estirado, especialmente para grados de acero aleado para endurecimiento por trabajo.
- Dibujar es un proceso longitudinal.. Existe un potencial limitado para corregir la variación severa de la pared longitudinal porque el troquel y el mandril flotan libremente y seguirán la variación de la pared en lugar de corregirla..
El estirado en frío se puede optimizar seleccionando el perfil de troquel más adecuado (Ver Figura 3). Ningún diseño único funciona mejor para todos los tubos sin costura porque el diseño depende de muchos factores, como el espesor de la pared, grado de acero, requisitos de reducción de pases, y limitaciones del banco de dibujo.
Figura 3
Tres perfiles principales de matriz de estirado en frío son radio, directo, y mezcla recta/radio, o combinación
Tres perfiles de matriz son:
- Matriz de radio: la entrada de la matriz es un arco sin ángulos agudos ni superficies planas.
- Matriz recta: la entrada de la matriz tiene un plano, superficie angular, típicamente 10 a 20 grados por lado.
- Matriz combinada: la entrada de la matriz combina superficies planas y mezclas de radio.
Para cada orden de producción dibujada, Se puede completar y utilizar un gráfico de control estadístico o el método de prueba t de Student para optimizar el perfil del troquel y la dimensión del troquel como un registro permanente..
Para la mayoría de los tubos sin soldadura, un dado radial produce la mejor calidad de pared. Debido a que el dado de radio tiene un perfil de entrada más gradual y una mezcla suave en la sección del cojinete, el dibujo del tubo es más consistente y da como resultado dimensiones de mayor calidad. Pero hay un inconveniente en este tipo de matriz.: Debido al perfil de entrada gradual, solo se puede hacer una pequeña reducción de OD en el tubo. El tubo sin costura debe personalizarse para usar este tipo de troquel., agregando gastos de cambio.
Lograr la consistencia de manera consistente
Lograr consistencia requiere analizar el proceso hacia atrás., desde el final hasta el principio. El espesor de pared especificado por el cliente del producto terminado proporciona las dimensiones finales para el tubo procesado por el banco de estirado, que guía la selección de matrices y mandriles. Esta selección determina el tamaño adecuado de la tubería del molino sin costura., que determina la configuración adecuada y los parámetros operativos.