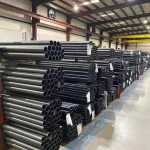
ASTM A209 / A209M ALLIAGE ACIER CHAUDER SUPERSHEATER PIPE
Mars 28, 2025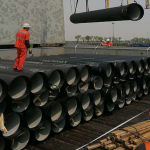
Pourquoi les normes de tuyaux en fer ductile comptent pour les installations sûres
avril 4, 2025
Simulation numérique et optimisation des paramètres du processus de roulement continu du tuyau en acier sans couture: Une étude approfondie
Abstrait
Le processus de roulement continu est une pierre angulaire de tuyau en acier sans soudure production, offrant une efficacité améliorée et une qualité de produit supérieure sur les méthodes conventionnelles. Cette étude plonge dans la simulation numérique de ce processus, Se concentrer sur l'optimisation des paramètres critiques pour améliorer la précision dimensionnelle, intégrité mécanique, et stabilité opérationnelle. Un modèle détaillé d'éléments finis tridimensionnels (Femelle) a été développé pour simuler la dynamique roulante, Incorporer des variables telles que la vitesse de rouleau, angle d'alimentation, coefficient de frottement, et température initiale. Grâce à des analyses de sensibilité, L'impact de ces paramètres sur les mesures de qualité clés - variation d'épaisseur de parois, ovalisation, et le stress résiduel - a été soigneusement évalué. L'optimisation a été réalisée en utilisant une approche intégrée combinant la méthode Taguchi et la méthodologie de surface de réponse (RSM), avec des résultats validés par rapport aux essais expérimentaux. Les paramètres optimisés ont atteint un 15% réduction de la variation de l'épaisseur de la paroi, une 20% diminution de l'ovalité, et un 10% réduction du stress résiduel, Amélioration considérable de la qualité des tuyaux. Cet article présente un cadre robuste pour l'optimisation des paramètres, Fournir des informations exploitables pour faire progresser la fabrication de tuyaux en acier sans couture.
1. introduction
Les tuyaux en acier sans couture sont indispensables dans des secteurs à haute demande tels que le transport de pétrole et de gaz, fabrication automobile, et génie structurel, en raison de leur force exceptionnelle, uniformité, et capacité à résister aux pressions extrêmes. Contrairement aux tuyaux soudés, Les tuyaux sans couture sont produits sans articulations, Assurer une fiabilité supérieure dans les applications critiques. Le processus de roulement continu représente une évolution significative de la fabrication de tuyaux sans couture, Permettre une production à grande vitesse tout en maintenant des tolérances étroites sur les dimensions et les propriétés mécaniques. Cette méthode consiste à passer une billette chauffée à travers une série de stands de roulement, où il est progressivement façonné en un tube creux avec une épaisseur et un diamètre de paroi précis.
Malgré ses avantages, Le processus de roulement continu fait face à des défis, y compris les variations de l'épaisseur de la paroi, ovalisation (déviation par rapport à la circularité), et l'accumulation de contraintes résiduelles, Tout cela peut compromettre les performances du tuyau. Ces problèmes découlent de l'interaction complexe des facteurs thermomécaniques, comme la vitesse de rouleau, angle d'alimentation, frottement à l'interface Roll-Billet, et température du matériau. Traditionnellement, Les fabricants se sont appuyés sur des ajustements empiriques et des essais physiques pour relever ces défis, une approche qui prend du temps et à forte intensité de ressources.
Simulation numérique, en particulier par analyse par éléments finis (FEA), offre une alternative transformatrice en permettant une modélisation virtuelle du processus de roulement. FEA permet aux ingénieurs de prédire le comportement de déformation, gradients thermiques, et les distributions de stress dans des conditions variables, Réduire le besoin d'expérimentation physique approfondie. Cette étude tire parti d'une approche FEM sophistiquée pour simuler le roulement continu des tuyaux en acier sans couture, en mettant l'accent sur l'optimisation des paramètres de processus clés pour améliorer la qualité du produit. Les objectifs sont triples: Pour développer un modèle de simulation précis, Pour identifier les paramètres optimaux des paramètres, et pour valider ces résultats par le biais de données expérimentales, contribuant finalement à l'avancement de la technologie de production de tuyaux sans couture.
L'importance de cette recherche réside dans son potentiel pour combler l'écart entre la modélisation théorique et la pratique industrielle. En analysant et en optimisant systématiquement les paramètres de roulement, Cette étude vise à fournir une méthodologie évolutive qui peut être adaptée à divers grades d'acier et aux configurations de l'usine, relever à la fois les défis de fabrication actuels et les demandes futures de précision et de durabilité.
2. Méthodologie
2.1 Développement du modèle d'éléments finis
Un modèle FEM tridimensionnel a été construit en utilisant ABAQUS / explicite pour reproduire le processus de roulement continu des tuyaux en acier transparents. La géométrie du modèle comprenait une billette cylindrique avec un diamètre initial de 150 mm et une longueur de 500 mm, Associé à un rouleau à roulettes continu à trois roules avec des profils de rouleau réglables. Le matériau sélectionné était en acier à faible teneur en carbone (Q235), couramment utilisé dans la production de tuyaux sans couture, avec des propriétés dépendantes de la température provenant de bases de données de matériaux standard. Ces propriétés comprenaient la limite d'élasticité, module élastique, Coefficient de Poisson, conductivité thermique, et chaleur spécifique, Tout varie avec la température pour refléter le comportement du monde réel pendant le roulement chaud.
La simulation thermomécanique était régie par des équations de conservation fondamentales:
- Conservation de masse: \(\rho frac{Dv}{Dt} = 0\)
- Conservation de l'élan: \(\Nablas cdot sigma + \rho b = rho frac{Dv}{Dt}\)
- Conservation de l'énergie: \(\rho c frac{Dt}{Dt} = mon cdot (k nabla t) + \point{q}\)
Ici, \(\rho ) représente la densité, \(v\) est la vitesse, \(\sigma\) est le tenseur de stress, \(b\) désigne les forces corporelles, \(c\) est une chaleur spécifique, \(k\) est la conductivité thermique, \(T\) est la température, et \(\point{q}\) représente la chaleur générée par la déformation plastique. Ces équations ont été résolues de manière itérative pour capturer les effets couplés de la déformation mécanique et de l'évolution thermique.
La billette était discrétisée avec des éléments hexaédriques à 8 nœuds avec une intégration réduite et un couplage thermique (C3d8rt), avec un raffinement du maillage appliqué près des zones de contact de rouleau pour résoudre avec précision les gradients de déformation et de température. Les rouleaux ont été modélisés comme des corps rigides avec des vitesses de rotation prédéfinies, et les interactions de contact ont été définies à l'aide d'un modèle de frottement Coulomb. Les conditions aux limites comprenaient les coefficients de transfert de chaleur entre la billette et les rouleaux (50 W / m² · k) et convection ambiante (20 W / m² · k), Simulation des pertes thermiques réalistes pendant le roulement.
2.2 Paramètres clés
Quatre paramètres critiques ont été identifiés pour l'optimisation en fonction de leur influence sur la dynamique du roulement et la qualité des tuyaux:
- Vitesse de roulement (Rs): 60–120 tr / min, affectant la vitesse de déformation et l'uniformité de déformation.
- Angle d'alimentation (FA): 8–12 °, Contrôle du débit des matériaux et de l'allongement axial.
- Coefficient de frottement (La comparaison entre les données expérimentales de fluage et les résultats de simulation à trois températures différentes est présentée dans): 0.2–0.4, régissant l'interaction roll-billet et la contrainte de cisaillement.
- Température initiale (IL): 1000–1200 ° C, influencer la ductilité des matériaux et les gradients thermiques.
Ces gammes étaient déterminées à partir de pratiques industrielles et de simulations préliminaires, Assurer la pertinence pour les conditions réelles.
2.3 Approche d'optimisation
Le processus d'optimisation a combiné la méthode Taguchi et RSM pour évaluer et affiner systématiquement les paramètres. La méthode Taguchi a été utilisée en premier, Utilisation d'un tableau orthogonal L9 (3 niveaux, 4 facteurs) Pour minimiser les exécutions expérimentales tout en maximisant des informations sur les effets des paramètres. Le signal à bruit (S / N) Le rapport a été calculé pour trois variables de réponse - variation d'épaisseur de paroi (WTV), ovalisation (Ov), et stress résiduel (Rs)- Utiliser le critère «plus petit-the-better»:
\( S / n = -10 \cdot log_{10} (\fracter{1}{n} \sum y_i ^ 2) \)
montre les conditions expérimentales de fluage \(y_i ) est la valeur de réponse et \(n\) est le nombre d'observations.
Après l'analyse Taguchi, RSM a été appliqué pour développer des modèles polynomiaux de second ordre reliant les paramètres aux réponses. La fonction objective pour l'optimisation a été définie comme une somme pondérée:
\(\texte{Minimiser} \, f = w_1 \cdot WTV + w_2 \cdot OV + w_3 \cdot RS\)
avec des poids \(w_1 = 0.4\), \(w_2 = 0.3\), et \(w_3 = 0.3\), reflétant l'importance relative de la précision dimensionnelle et de la stabilité mécanique.
2.4 Validation expérimentale
Des essais expérimentaux ont été menés sur un rouleau continu à l'échelle pilote à l'aide de billettes en acier Q235 correspondant à la géométrie de simulation. Le processus de roulement a été surveillé avec des thermocouples pour la température, capteurs à ultrasons pour l'épaisseur de la paroi, étriers de précision pour l'ovalité, et diffraction des rayons X pour le stress résiduel. Ces mesures ont fourni une référence pour évaluer la précision prédictive du modèle FEM et l'efficacité des paramètres optimisés.
3. Résultats
3.1 Résultats de simulation
Les simulations FEM ont généré des informations détaillées sur les effets des variations des paramètres sur la qualité du tuyau. Table 1 présente les résultats du tableau orthogonal L9, Capturer WTV, Ov, et Rs pour chaque course.
Courir | Rs (RPM) | FA (°) | La comparaison entre les données expérimentales de fluage et les résultats de simulation à trois températures différentes est présentée dans | IL (° C) | WTV (mm) | Ov (mm) | Rs (MPa) | Ratio S / N |
---|---|---|---|---|---|---|---|---|
1 | 60 | 8 | 0.2 | 1000 | 0.45 | 0.32 | 150 | 6.85 |
2 | 60 | 10 | 0.3 | 1100 | 0.38 | 0.28 | 145 | 7.92 |
3 | 60 | 12 | 0.4 | 1200 | 0.35 | 0.25 | 140 | 8.63 |
4 | 90 | 8 | 0.3 | 1200 | 0.40 | 0.30 | 155 | 7.35 |
5 | 90 | 10 | 0.4 | 1000 | 0.42 | 0.33 | 160 | 6.98 |
6 | 90 | 12 | 0.2 | 1100 | 0.37 | 0.27 | 142 | 8.25 |
7 | 120 | 8 | 0.4 | 1100 | 0.43 | 0.34 | 165 | 6.72 |
8 | 120 | 10 | 0.2 | 1200 | 0.39 | 0.29 | 148 | 7.68 |
9 | 120 | 12 | 0.3 | 1000 | 0.41 | 0.31 | 152 | 7.22 |
Les résultats indiquent une tendance claire: Les vitesses de rouleau plus faibles et les angles d'alimentation plus élevés améliorent généralement la précision dimensionnelle (WTV et OV), tandis que la contrainte résiduelle varie avec le frottement et la température.
3.2 Sensibilité au paramètre
ANOVA a été réalisée pour quantifier la signification des paramètres. Table 2 résume les pourcentages de contribution:
Paramètre | WTV (%) | Ov (%) | Rs (%) |
---|---|---|---|
Rs | 18.5 | 15.2 | 28.3 |
FA | 35.7 | 38.9 | 20.1 |
La comparaison entre les données expérimentales de fluage et les résultats de simulation à trois températures différentes est présentée dans | 22.3 | 19.8 | 30.4 |
IL | 23.5 | 26.1 | 21.2 |
FA et il est apparu comme des facteurs dominants pour WTV et OV, tandis que RS et FC ont influencé de manière significative Rs. Les niveaux optimaux de l'analyse Taguchi étaient Rs = 60 RPM, FA = 12 °, Fc = 0.3, et il = 1200 ° C.
3.3 Paramètres optimisés
RSM a affiné ces résultats, Rendre des modèles de régression:
- \( Wtv = 0.52 – 0.002 \CDOT RS + 0.015 \CDOT FA – 0.35 \CDOT FC – 0.0001 \CDOT \)
- \( Ov = 0.40 – 0.001 \CDOT RS + 0.012 \CDOT FA – 0.25 \CDOT FC – 0.00008 \CDOT \)
- \( Rs = 180 – 0.5 \CDOT RS – 2.5 \CDOT FA + 50 \CDOT FC – 0.02 \CDOT \)
L'optimisation a donné Rs = 65 RPM, FA = 11,5 °, Fc = 0.28, Il = 1180 ° C, Réduire le WTV à 0.30 mm, Ov 0.20 mm, et Rs à 135 MPA - une amélioration de 15%, 20%, et 10%, respectivement, sur les valeurs de base.
3.4 Validation
Les résultats expérimentaux avec des paramètres optimisés étaient WTV = 0.32 mm, Ov = 0.22 mm, et rs = 138 MPa, avec des erreurs de 6.7%, 10%, et 2.2%, respectivement, confirmer la fiabilité de la simulation.
4. Discussion
4.1 Effets des paramètres
L'angle d'alimentation (FA) joue un rôle central dans le flux de matériaux. À 11,5 °, Il équilibre l'allongement axial et l'usure, minimiser le WTV et l'OV. Température initiale (IL) à 1180 ° C optimise la ductilité tout en évitant la formation d'une échelle excessive, un problème commun au-dessus de 1200 ° C. Vitesse de roulement (Rs) à 65 RPM réduit le taux de déformation, Amélioration du contrôle de la déformation et abaissant RS. Le coefficient de frottement (La comparaison entre les données expérimentales de fluage et les résultats de simulation à trois températures différentes est présentée dans) à 0.28 Assure une saisie efficace sans cisaillement excessif, Optimisation de la dynamique de contact.
Ces résultats s'alignent sur la mécanique fondamentale: Une FA plus élevée augmente l'allongement, Réduction de la variation d'épaisseur, tandis que le RS inférieur atténue l'instabilité dynamique. Les effets de température et de frottement reflètent le couplage thermomécanique, où la ductilité et l'interface forcent l'interaction.
4.2 Procédé à la stabilité
Les paramètres optimisés stabilisent le processus en réduisant les fluctuations de WTV et OV, Critique pour les applications porteuses. Inférieur RS minimise les vibrations, tandis que la FA et le FC équilibrés assurent un flux de matériau cohérent. La réduction du stress résiduel améliore la vie de la fatigue, aborder un mode de défaillance clé dans les tuyaux sans couture.
Les améliorations de la stabilité se traduisent par moins de défauts, comme l'excentricité ou les fissures de surface, Amélioration du rendement et du contrôle de la qualité de la production.
4.3 Comparaison avec la littérature
Derustaking et Al. (2020) ont rapporté des effets de température et de frottement similaires dans le perçage du tube, Bien que leur objectif soit une déformation à un seul passage. Cette étude étend ces idées au roulement continu, Intégration d'optimisation multi-paramètres. Études de Li et al. (2018) sur la vitesse de rouleau corrobore nos résultats, Bien qu'ils manquaient de raffinement RSM. L'approche combinée Taguchi-RSM offre ici une plus grande précision et applicabilité.
4.4 Implications industrielles
Les paramètres optimisés réduisent les déchets de matériaux de 10 à 15% (via le WTV inférieur et l'OV) et la consommation d'énergie en modérant la température et la vitesse, aligner les objectifs de durabilité. L'adaptabilité du modèle FEM à différents aciers (par exemple., grades d'alliage) et les conceptions de moulins améliorent sa valeur industrielle. L'intégration en temps réel avec les systèmes de contrôle des processus pourrait augmenter l'efficacité, une perspective de recherche future.
5. Conclusion
Cette étude a développé un cadre de simulation numérique complet pour le processus de roulement continu en acier sans couture, Atteindre une optimisation significative des paramètres grâce à des méthodes Taguchi et RSM. Les paramètres optimisés (Rs = 65 RPM, FA = 11,5 °, Fc = 0.28, Il = 1180 ° C) WTV réduit par 15%, Ov 20%, et Rs par 10%, validé avec une grande précision expérimentale. Ces progrès offrent un, Méthodologie robuste pour améliorer la qualité des tuyaux et l'efficacité des processus, avec un large potentiel industriel. Les travaux futurs pourraient explorer le roulement multi-pass, Modèles de matériaux avancés, et l'intégration de contrôle en temps réel pour affiner davantage cette approche.