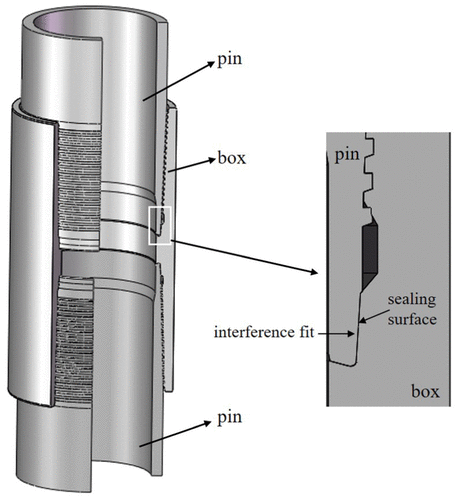
demande de tuyau enveloppe dans des puits de gaz à haute température
janvier 4, 2019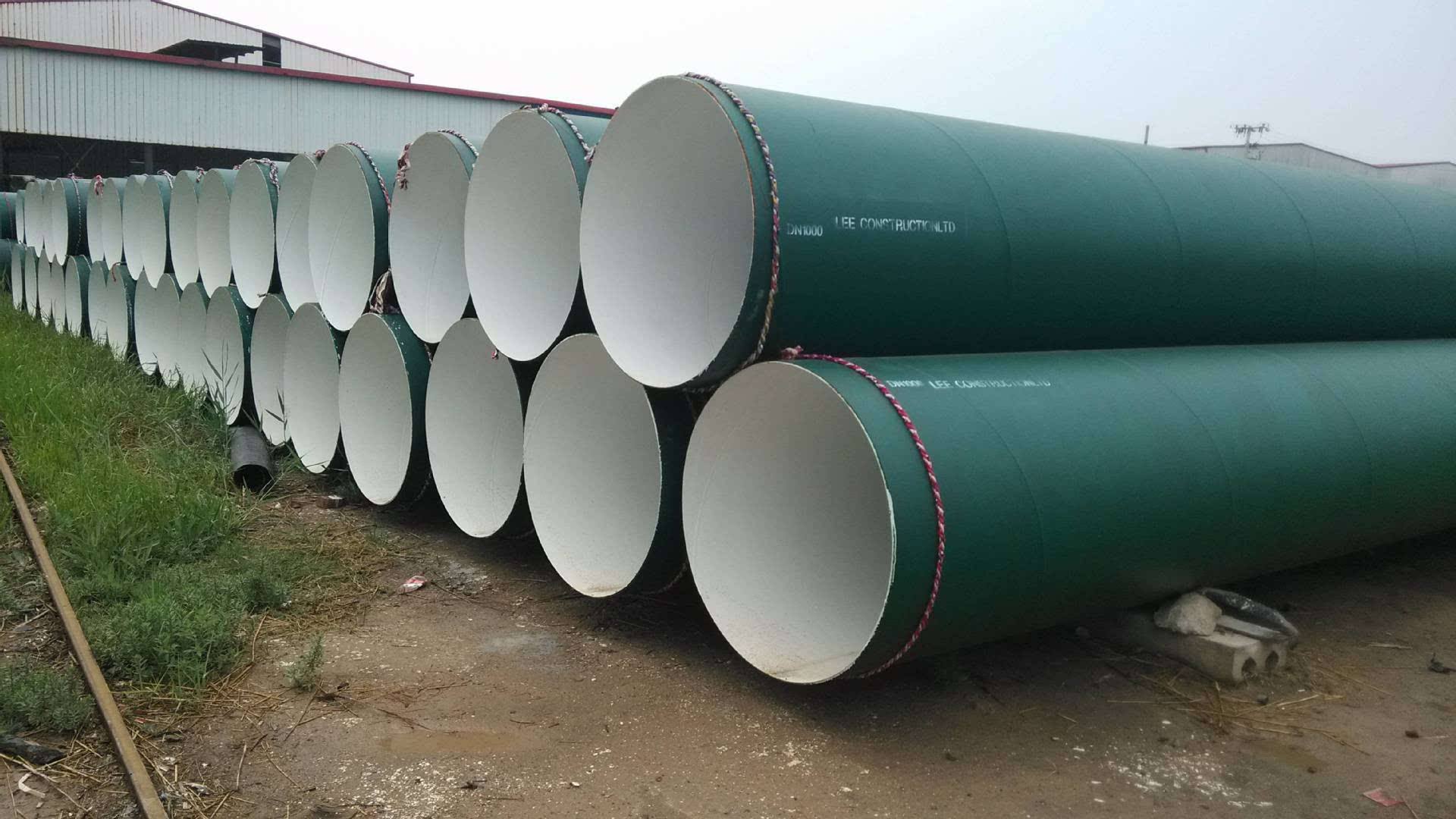
Comment le poids théorique du tuyau d'acier en spirale calculée?
janvier 8, 2019ABSTRAIT
le corrosion les résistances de l'émail-pipe en acier revêtue dans 3.5 % En poids de solution de NaCl a été évaluée et comparée à celles d'un tuyau revêtu d'époxy en utilisant un potentiel de circuit ouvert, po linéaire- résistance larization, et l'impédance électrochimique Spectros- tests de copie. T-001c suspension d'émail et de la poudre d'émail GP2118 ont été pulvérisées sur le tuyau en acier dans des procédés humides et électrostatiques, respectivement. La composition de phase et microstructures des deux émaux ont été caractérisés par diffraction des rayons X et microscopie électronique à balayage (SEM). La rugosité de surface des émaux et leur force d'adhérence avec des substrats en acier ont été quantifiée pour comprendre la qualité du revêtement. images MEB a révélé que les deux types de revêtements d'émail ont une structure solide avec des bulles isolées. Des tests électrochimiques ont montré une résistance élevée à la corrosion des revêtements d'émail comme véri fi é en matière d'inspection visuelle sur les échantillons testés. En particulier, les échantillons revêtus d'émail GP2118 constamment surpassé les échantillons revêtus d'époxy.
MOTS CLÉS: corrosion, spectroscopie d'impédance électrochimique, revêtement d'émail, pipeline en acier, La microscopie électronique à balayage
INTRODUCTION
gaz naturel, huile, et dangereux pipelines de transport et de collecte de liquide sont parvenus 484,000 miles dans les pipelines vieillissants U.S.1 sont confrontés à une réduction
durée de vie et la fiabilité en raison de la corrosion. Ils peuvent être protégés contre la corrosion par un revêtement de protection, la protection cathodique, et l'utilisation des inhibiteurs de corrosion. Revêtement de barrière physique à l'électrolyte penetra- tion est l'un des plus efficaces et ef méthodes de fi caces dans l'atténuation de la corrosion.
Appliqué à l'intérieur des canalisations en acier, manteau- ING présente plusieurs avantages. Premier, le revêtement intérieur peut empêcher fluide ou de gaz d'interagir et réagir avec l'acier sous-jacent,. Seconde, revêtue de tuyaux en acier réduit les dépôts microbiologiques et des bactéries fi lm bio forma- tions parce que la rugosité de surface supérieure du tuyau non couché aide à protéger les bactéries et de fournir des conditions de croissance pour colonies.2 bactérienne troisième et dernière, le
revêtement intérieur permet de réduire la chute de pression sur une longue distance d'un pipeline et donc la puissance requise pour transmettre le pétrole et le gaz. La chute de pression dans le tuyau revêtu a été expérimentalement démontré que 35% inférieure à celle dans le tuyau d'acier nu à un nombre de Reynolds
1 × 107.3
Aujourd'hui, deux parties revêtements époxy à base de solvant, solvant revêtements libres et liés par fusion, et les revêtements polyamides sont largement utilisés dans le pétrole brut et le gaz naturel pipelines.4-6 Ces revêtements sont faiblement liées avec
leur substrat en acier et donc sujettes à des sous-fi lm corrosion.7
émail porcelaine, en tant que matériau inorganique, est chimiquement lié au substrat métaux à une température de 750 ° C à ~850 ° C. Il ne peut être que fi ni avec une surface lisse et esthétique, mais aussi fournir ex- la stabilité chimique cellent, bonne résistance à la corrosion, et la durabilité dans divers environments.8 dur Contrairement
revêtement époxy, revêtement en émail n'a pas de corrosion sous fi lm lorsque violé localement en raison de sa liaison chimique avec substrates.9 métallique Il a été largement utilisé pour la protection des ustensiles de cuisson domestique ou la protection des conteneurs en acier dans les industries. Sa corrosion re- sistance en tant que revêtement de protection pour l'armature d'acier dans des structures de béton a été étudiée en pré- Des études Vious et se sont avérées satisfaisantes dans general.10-11
Dans cette étude, le comportement à la corrosion du tube en acier revêtu intérieurement avec deux types d'émail (T-001 bouillie et de la poudre GP2118) a été examiné dans 3.5 % En poids de solution de NaCl. La composition de la phase et de la microstructure des émaux ont été caractérisés par diffraction des rayons X
(DRX) et microscopie électronique à balayage (SEM), respectivement. La rugosité de surface du revêtement d'émail et de sa force d'adhérence sur des supports de tuyaux en acier ont été déterminés. Les comportements électrochimiques ont été étudiés avec un potentiel de circuit ouvert (OCP), linéaire polaire- résistance isation (LPR), et imped électrochimique- spectroscopie ANCE (EIE) essais. inspections visuelles ont été effectuées sur des échantillons testés pour des signes évidents de corrosion. La résistance à la corrosion de l'acier revêtu d'émail est comparée à celle de l'acier revêtu d'époxy.
PROCÉDURES EXPÉRIMENTALES
Émaillage et Specimens
Une API 5L X65 tuyau en acier (MRC mondial) avec 323.85 mm de diamètre extérieur et 9.53 mm d'épaisseur de paroi a été utilisé comme métal du substrat dans cette étude. La composition chimique de l'acier fournies par le vendeur est présentée dans le tableau 1. Le tube en acier est d'abord découpé en 18 25 mm × 50 mm spécimens promo. Les échantillons coupés ont ensuite été fustigé pour l'acier 1 min pour se débarrasser de calamine et rouilles, et fi nalement nettoyée avec
un solvant de nettoyage disponible dans le commerce.
Deux types d'émail ont été appliqués sur les coupons en acier: T-001 bouillie et de la poudre GP2118. Les compositions chimiques de T-001 frittes de verre et la poudre d'émail de GP2118 ont été déterminées par rayons X de fluorescence (XRF) tel que présenté dans le tableau 2. La suspension de l'émail a été préparé par d'abord frittes de verre de fraisage, argile, et certains électrolytes, puis en les mélangeant avec de l'eau jusqu'à ce que le mélange est dans un état de suspension stable. La suspension épaisse d'émail a été pulvérisée manuellement sur des échantillons de coupon en utilisant un pistolet de pulvérisation, qui a été effectuée par un jet d'air comprimé comme spéci fi ées dans le tableau 3. Les échantillons ont été chauffés à 150 ° C pendant 10 min pour chasser l'humidité, fi rouge à 815 ° C pendant 10 moi, et en fi refroidi à la température ambiante. Pour la pulvérisation électrostatique, la poudre d'émail de GP2118 avec une taille moyenne de particules de 32.8 um a été utilisée. Un champ électrique est formé entre une électrode de buse et l'échantillon. des particules d'émail, propulsé hors du pistolet de pulvérisation par un courant d'air, est devenu chargé négativement, migré vers l'échantillon (électrode positive) et ont été radiées- postulés. Après la pulvérisation de puissance, les coupons en acier ont été transférés dans un four et fi rouge à 843 ° C pendant 10 moi, puis déplacé hors et refroidi à la température ambiante. L'épaisseur de la T-001 revêtement est contrôlé par le temps de pulvérisation, tandis que l'épaisseur du revêtement de GP2118 a été contrôlée par le nombre de pistolets de pulvérisation. En comparaison, échantillons d'acier revêtu d'époxy ont été pré- pared et testé. Dans ce cas, 3M Scotchkote 323 † résine époxy, qui a été appliquée dans l'industrie du pipeline, a été utilisé pour enrober les échantillons. coupons d'acier ont été revêtus par brossage à la température ambiante époxy, puis séchées à l'air pendant 3 d avant les essais électrochimiques.
Caractérisation des revêtements émail
L'épaisseur du revêtement et de la rugosité ont été mesurées avec une jauge d'épaisseur de revêtement MiniTest 6008 † et microscope optique Hirox †, respectivement.
La force d'adhérence entre le revêtement et son substrat en acier a été déterminée en utilisant PosiTest † suivant ASTM D4541-09.12 Afin d'améliorer sa liaison avec le revêtement, une 20 mm dolly de diamètre à la base a été rendue rugueuse avec des papiers abrasifs, et nettoyé avec de l'alcool pour éliminer les contaminants et l'oxydation. La base du chariot a été collée avec une couche uniforme de colle sur la surface du revêtement de test. Après durcissement pendant 24 h, le revêtement autour du chariot a été éliminé en utilisant un 20 mm outil de coupe afin d'isoler le chariot sur une zone de test spéci fi que. Le chariot a fi nalement tiré hors de la surface de l'échantillon perpendiculairement à un taux de stress 0.4 MPa / s. La force maximale de chaque échantillon revêtu a été enregistré.
A l'issue des essais de corrosion, les phases de revêtement ont été examinés directement sur la surface des échantillons d'acier revêtus par XRD (Philip X'Pert †) avec un angle de diffraction (2Je) varié entre 10 ° et 55 °. Les sections transversales des échantillons revêtus d'émail ont été préparés pour l'analyse de la microstructure avec SEM (Hitachi S4700 †). Chaque échantillon a été revêtu d'émail à froid d'abord monté dans une résine époxy (EpoxyMount †, Allied High Tech Produits, Inc.) et couper en un 10 mm section transversale d'épaisseur en utilisant une scie à diamant. alors, la section a été abrasée avec des papiers en carbure à 1200 grincer, rincé à l'eau déminéralisée, et fi nalement séché à l'air à la température ambiante avant l'examen. images SEM ont été analysées avec le logiciel ImageJ † pour l'évaluation de la porosité.
Tests Electrochemical
Chaque échantillon a été soudé avec un fil de cuivre pour des mesures électrochimiques, comme illustré sur la figure 1. Tous les côtés de l'échantillon à l'exception de l'émail- ou le visage recouvert d'époxy ont été couverts avec de l'époxy Marine.
La surface de l'émail ou de l'époxy exposée était 30 mm × 20 mm en taille,.
Tous les échantillons ont été immergés dans 3.5 % En poids de solution de NaCl au pH de 7 et testé à tempera chambre- ture pour 69 usinage. La solution a été préparée par addition de puri fi chlorure de sodium ed (Fisher Scientific, Inc.) dans de l'eau distillée.
Au moment de la 1, 3, 6, 13, 27, 41, 55, et 69 usinage, OCP, LPR, et les tests de l'EIE ont été réalisées pour suivre l'évolution de la corrosion de l'émail- et les échantillons d'acier revêtu d'époxy. Un système à trois électrodes standard a été utilisé pour les tests électrochimiques, y compris une 25.4 mm × 25.4 mm × 0.254 mm feuille de platine comme contre-électrode, électrode au calomel saturé (SCE) comme une électrode de référence, et l'échantillon revêtu comme une électrode de travail. Les trois électrodes sont connectées à un Gamry 1000E potentiostat / Galvanostat † pour l'acquisition de données.
Après chaque OCP stable (durable pour 1 h) a été enregistré, On a effectué un essai EIS avec une onde sinusoïdale de potentiel 10 mV en amplitude autour de l'OCP et une fréquence de 100 kHz 5 mHz. Le test LPR a été réalisée en balayant une plage de ± 15 mV autour de l'OCP à une vitesse de balayage de 0.167 mV / s. Les courbes LPR sont utilisées pour déterminer la résistance de polarisation Rp, qui est égale à la pente de la partie linéaire d'une courbe de polarisation autour de zéro de courant:13
Rp = AE = Ai
où Ai et AE représentent les incréments de tension et de courant, respectivement, dans la partie linéaire d'une courbe de polarisation à i = 0. LPR mesures ont été utilisées pour calculer la densité de courant à la corrosion par l'équation de Stern-Geary:13
Icorr = vavc = ½2.303dva + βcThRp (2)
où ßA et ßC représente la constante de Tafel anodique (0.12) et la constante de Tafel cathodique (0.12), respectivement, et Icorr est le courant de corrosion.
RÉSULTATS ET DISCUSSION
revêtement Caractérisation
Phases en émail - motifs de diffraction des rayons X sur la surface de GP2118 et T-001 échantillons revêtus d'émail après immersion dans 3.5 % En poids de solution de NaCl pour 69 d sont identi fi és et affichés à la figure 2. Quartz SiO2 est présent dans les deux types de revêtements d'émail. Les pics les plus élevés d'intensité de quartz SiO2 étaient à 26 ° et 26,5 ° pour GP2118 et T-001 Emaux, respectivement.
Microstructure à l'interface émail / substrat - images transversales SEM à l'interface acier / revêtement avec différents cations de grossissement sont présentés sur la figure 3. Les revêtements d'émail ont une structure solide avec de l'air déconnectée barbote à travers l'épaisseur du revêtement (figures 3[a1] et [b1]). Les bulles d'air ont été formés au cours de la substance chimique à haute température
réaction de la fritte de verre de l'émail avec l'acier au cours de bague de fi process.14-15 Les revêtements d'émail ont de nombreuses
petits pores isolés à l'exception de l'émail GP2118 qui a quelques grands pores d'un diamètre d'environ 105 Μm. La teneur en porosité de T-001 émail a été mesurée à 4.26%, qui est inférieure à 12.72% pour l'émail GP2118. figures 3(a2) et (b2) montrer les interfaces émail / acier fi é Magni à laquelle des saillies petites Fe poussent dans la couche d'émail pour former différents points d'ancrage. Ces particules de spinelle épitaxiales améliorer la liaison entre l'émail et son substrate.16 d'acier
Pull-Off Force - L'épaisseur mesurée, rugosité de surface, et la force de liaison de trois types de revêtements sont résumés dans le Tableau 4. La moyenne et l'écart-type de la rugosité de surface et l'épaisseur de chaque couche ont été calculées à partir de
27 les mesures prises à partir de trois échantillons différents qui ont été polis pour avoir une surface plate pour le test d'arrachement. La moyenne et l'écart type de la résistance de liaison de chaque couche ont été calculés à partir des trois essais d'extraction réalisés hors. On peut voir dans le tableau 4 ce revêtement époxy est la plus épaisse (396 Μm) et T-001 émail est le plus mince (230 Μm). le
la rugosité des trois couches est de l'ordre 1 Μm, indiquant des surfaces lisses dans tous les spécimens.
A l'issue des essais d'extraction au large, les surfaces fracture chariot et de substrat sont représentés sur la figure 4. Dans un test d'adhérence pull-off, quatre modes de défaillance possibles comprennent: (1) rupture d'adhérence entre le revêtement et son substrat d'acier, (2) rupture de cohésion au sein de la couche de revêtement, (3) la rupture de la colle, et (4) rupture mixte ou une combi- nation des pauses ci-dessus à plusieurs locations.17
revêtements émail ont un mode de défaillance mixte dans- volving une rupture à l'intérieur du revêtement (cohésive rupture) et une rupture de la colle utilisée pour coller le chariot à l'échantillon. revêtement époxy a également un mode de défaillance mixte impliquant une rupture à l'intérieur du revêtement (cohésive rupture), une rupture entre le revêtement et l'acier de substrat (rupture adhésive), et un saut de colle. Il n'y a pas de pauses adhésifs pour revêtements en émail, parce que les points d'ancrage sur l'interface augmentent la liaison entre un revêtement d'émail et de son substrat en acier comme montré sur la Figure 3. Plus précisément, revêtement d'émail GP2118 a la plus grande force de liaison avec une valeur moyenne de 17.89 MPa, revêtement époxy a la plus faible force de liaison de 8.01 MPa, et T-001 revêtement d'émail possède une force de liaison de 16.85 MPa.
figures 5(une) et (b) représenter les morphologies de surface de fracture fi é Magni comme représenté sur les figures 4(a2) et (b2), respectivement. Lorsque le dolly a été retiré de l'échantillon revêtu à angle droit, une fissure amorcée et se propage à travers de grandes bulles d'air au sein de l'COAT- InG de moins lors des pics. cHiFFRES 6(une) et (b) Afficher SEM iMaGes pour les sections de la SPE TESTE- cIMEnS En AnGULAIReS GÉNÉRATEURS DES FIGURES 4(a2) et (b2), respectivement. Les surfaces fracturées des échantillons sont généralement Lissez avec le minimum n'a pas subi REVÊTEMENT éPAISSEURS D'ENVIRON 70 iM et
40 iM Pour GP2118 et T-001 éMAUX, respectivement. Par rapport à gRAphIqUE 3, cHiFFRES 6(une) et (b) INDIQUENT que les surfaces fracturées sont loin de leur COUCHES CORRESPONDANTS Bonding au INTERFACES Émail / de SuPPOrT et TRAVERSER LA PLUS FAIBLE LAYER Connexion BULLES DE GRANDE Aïr au COATING PARCE QUE L'adhésion de Émail sur les surfaces en acier EST Chimiquement Renforcement des liens avec la croissance des épitaxiales spinelle PArticules dans le émail au cours REACTION cHIMIQUE dans la fi RING processus.16