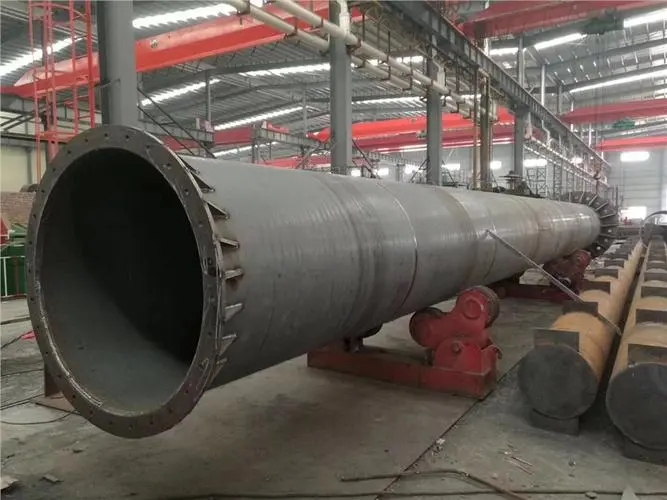
Comment l'usure se produit dans les tuyaux et pourquoi l'acier résistant à l'usure à haute résistance surpasse les tuyaux en acier ordinaires dans les environnements abrasifs
juin 21, 2022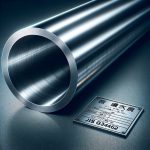
Connaissances de base et utilisations des tubes en acier sans soudure, carters et tuyaux d'huile
juin 23, 2022Réduire la quantité de variation, ou obtenir une plus grande cohérence d'épaisseur de paroi, peut faire la différence entre répondre aux exigences d'un client ou non. Cela permet également de réduire, voire d'éliminer, le besoin du client pour des processus ultérieurs tels que l'usinage..
Le tube sans soudure est généralement fabriqué sur un laminoir perceur à deux rouleaux. Dans certains cas, cette étape suffit à elle seule à produire un tube qui répond aux exigences du client. toutefois, si la consistance de l'épaisseur de paroi doit encore être améliorée après le perçage, un producteur de tubes peut utiliser des équipements et des étapes de processus supplémentaires. Deux de ces types d'équipements sont un laminoir allongeur à laminage croisé (communément connu sous son nom commercial, comme un moulin Assel ou Diescher), et un banc d'étirage à froid.
Aperçu des trois étapes du processus
La fabrication de tubes sans soudure commence généralement par un laminage croisé à chaud dans un laminoir perceur. Le perçage est la première étape du processus pour fabriquer un tube avec une paroi de haute qualité. Cette étape est généralement suivie d'un ou plusieurs processus d'allongement qui peuvent améliorer la qualité de la paroi tout en augmentant la longueur du tube.. Après que le tube quitte le broyeur sans soudure et se refroidit, il peut être fini sur un banc d'étirage à froid comme troisième étape pour améliorer les tolérances des murs.
Moulin de Pierce. L'essentiel de l'attention portée à la qualité des parois sans soudure est dirigé vers l'usine de perçage. Cette attention est justifiée car le broyeur perceur a le plus grand effet sur la variation de paroi. Les tubes produits par un laminoir perceur peuvent être optimisés pour 7 à 10 pourcentage de variation de la paroi.
Bien qu'une coquille percée puisse avoir moins de 10 pourcentage de variation de la paroi, cette quantité de variation est pour une section de paroi relativement épaisse. Par exemple, l'obtention d'une tolérance de paroi de ± 10% produit un tube avec une épaisseur de paroi de 13.5 mm (0.531 dans.) à 16.5 mm (0.650 dans.) ou plus lorsque commandé à 15 mm (0.590 dans.). Un traitement supplémentaire par un broyeur d'élongation peut être nécessaire pour les exigences plus strictes des clients.
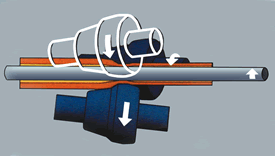
Le processus de laminage croisé utilise trois rouleaux de travail pour réduire le diamètre extérieur et l'épaisseur de paroi du tube. Dessin avec l'aimable autorisation de Copperweld, Shelby, Ohio.
Moulin d'allongement. Cinq principaux types d'élongateurs sont utilisés dans l'industrie de production de tubes: la tuberie à mandrin, le banc de poussée, le moulin à bouchons, l'usine de réduction d'étirage, et le laminoir allongeur à laminage croisé. Cinquante ans d'utilisation à l'échelle de l'industrie ont montré que, de ces moulins à allonge, l'allongeur à laminage croisé fournit l'amélioration la plus significative de la tolérance de paroi du tube produit sur un laminoir perceur. Un laminoir allongeur à laminage croisé utilise des rouleaux de travail sur le diamètre extérieur et un mandrin sur le diamètre intérieur (Voir Chiffre 1).
Banc d'étirage à froid. Dessiner sur un banc est une méthode de finition à froid qui améliore la dimension de la paroi du tube sans soudure. Dans le processus de tirage au banc, le tube est d'abord vissé de manière lâche sur un mandrin fixé à une tige. Ensuite, une pince saisit le tube et le tire à travers une matrice fixe en carbure ou en acier à outils. Le résultat est un tube personnalisé avec un très bon contrôle dimensionnel. La tolérance OD typique est de ± 0,1 mm (±0,004 po.), qui correspond à environ un dixième de la tolérance d'un tube sans soudure fini à chaud typique.
Les avantages supplémentaires du processus d'étirage incluent une finition de surface améliorée, la possibilité de fournir des tolérances d'identification, et propriétés mécaniques améliorées. Tubes produits avec ce processus nécessitent un traitement minimal ou supplémentaire et sont considérés comme des produits à valeur ajoutée.
Lignes directrices pour l'allongement des rouleaux croisés
Pour l'allongement transversal, deux exigences principales concernent l'obus brut de perçage. Ceux-ci remplissent la section de hauteur de bosse pour 80 à 90 pour cent de sa conception et maximisant l'adhérence côté entrée. Les deux exigences sont liées à la conception de la passe des rouleaux dans l'usine d'Assel.3
Chiffre 2
La bosse de rouleau est située près du milieu du rouleau de travail. Il est important de faire correspondre la section de tube entrant dans le broyeur avec les caractéristiques de conception des cylindres de travail. Dessin avec l'aimable autorisation de Copperweld, Shelby, Ohio.
Remplir la bosse. Hump est un terme général pour la région près du milieu du rouleau de travail qui contient un profil surélevé (Voir Chiffre 2). Remplir la bosse consiste à mesurer le mur tel que percé, puis à le comparer à la dimension de bosse connue à partir de l'impression. Le broyeur perceur est ensuite ajusté pour obtenir la bonne valeur. Par exemple, si la conception de la bosse est 8 mm (0.315 dans.), la coquille telle que percée doit mesurer 7 mm (0.276 dans.) plus que la taille du client (car 7 est 90 pourcentage de 8).
Cette relation est importante dans la production de tubes à paroi mince car la tolérance de paroi pour les tubes mécaniques est basée sur un pourcentage (selon la norme ASTM A519). Les tolérances pour les tubes à paroi plus mince sont plus difficiles à atteindre car, par exemple, 5 pourcentage de 5 mm (0.197 dans.) est une dimension beaucoup plus étroite que 5 pourcentage de 10 mm (0.394 dans.). Les producteurs de tubes doivent comprendre que si la capacité de l'usine est 1 mm (0.040 dans.) de la variation du mur, cela pourrait représenter la moitié de la tolérance commerciale pour les sections à paroi moyenne (Valeur CP de 2.0) et variation hors tolérance pour les sections à parois minces (Cp inférieur à 1.0).
L'épaisseur de paroi de la coque du broyeur perceur doit être réduite pour assurer un remplissage correct de la hauteur de la bosse. Pour tubes à paroi extrêmement fine, les fabricants peuvent constater que l'amélioration de la qualité dans le laminoir croisé peut être difficile, voire impossible, à réaliser car la coque percée présente trop de variations. Pour certaines tailles de tube, la variation de paroi en pourcentage peut être augmentée plutôt que diminuée dans le broyeur perceur. Le pourcentage de variation est déterminé par un calcul minutieux. Bien que la variation dimensionnelle totale diminue le numérateur, le dénominateur diminue à un taux plus élevé parce que le tube du laminoir d'allongement croisé a 50 à 75 pour cent moins d'épaisseur de paroi que le tube du broyeur perceur.
Cross-rolling Grip. La deuxième exigence est de maintenir la meilleure adhérence dans le processus de laminage croisé. L'adhérence est définie comme le nombre de spirales de tube avant l'axe central de la bosse dans la conception de la passe de rouleau du laminoir d'allongement à laminage croisé - en termes simples, la coque percée doit entrer en contact avec la face du rouleau au début du processus afin que l'alimentation du tube soit établie avant qu'elle ne rencontre la zone de travail dans la section de bosse. Le travail effectué dans la section de bosse nécessite une quantité extrême d'énergie, jusqu'à plusieurs milliers de chevaux. La force de travail est appliquée dans une section très courte, d'habitude 15 à 25 mm (moins de 1 dans.) large. Si le tube n'est pas correctement saisi, il va tourner au lieu de se nourrir, ou il peut se déplacer irrégulièrement dans la zone de travail, créer des variantes.
Dans la plupart des cas, la meilleure condition pour la coque percée est obtenue en produisant le diamètre extérieur maximal qui s'adaptera correctement à la face du rouleau de l'allongeur à laminage croisé.. Habituellement, cette relation est résolue en ajustant la configuration du broyeur perceur pour produire la bonne dimension de tube. Mais dans certains cas, il peut être nécessaire d'augmenter ou de diminuer légèrement l'angle divergent de l'élongateur pour s'assurer que la coque s'adaptera et s'agrippera correctement..
Des expériences menées sur la qualité des parois de tubes provenant directement d'un broyeur d'allongement ont été utilisées pour déterminer si les tubes avaient une meilleure qualité de paroi que les tubes traités ultérieurement par un broyeur de dimensionnement ou un broyeur de réduction d'étirage.. Il a été déterminé que dans le processus de réduction de taille, les forces longitudinales et de compression agissent sur le mur et peuvent augmenter la variation du mur. Les tubes prélevés directement à partir d'un laminoir allongeur à laminage croisé ont une consistance d'épaisseur de paroi supérieure et une meilleure qualité de surface car ils ne sont pas exposés aux conditions de laminage dans le laminoir d'encollage. Tubes qui ont traversé une usine de dimensionnement, toutefois, peut avoir une variation de paroi réduite par étirage à froid sur un banc d'étirage.
Lignes directrices pour l'étirage à froid
Le succès du traitement des tubes sans soudure étirés à froid dépend du maintien d'une qualité de paroi élevée à partir du laminoir à chaud sans soudure et de la sélection appropriée des outils de banc d'étirage à froid (jeux de mandrins et matrices).
Trois points principaux qui concernent l'étirage du tube percé sont:
- Une certaine réduction de la paroi est nécessaire pour s'assurer que le mandrin mord contre le mur au début du tirage, puis place correctement le mandrin dans le palier de matrice pendant le tirage. Si le mur entrant est trop irrégulier ou trop clair, le mandrin n'avance pas dans le palier de matrice, et le tube résultant n'aura pas de bonnes tolérances pour la dimension extérieure, dimension intérieure, et l'épaisseur de paroi.
- Le dessin au banc est limité au maximum 40 pourcentage de réduction de la superficie. Si le mur entrant est trop lourd, cela peut provoquer la rupture du métal plutôt que de céder pendant l'étirage, spécialement pour les aciers alliés écrouis.
- Le dessin est un processus longitudinal. Il y a un potentiel limité pour corriger une variation de paroi longitudinale importante parce que la matrice et le mandrin flottent librement et suivront la variation de paroi plutôt que de la corriger.
L'étirage à froid peut être optimisé en sélectionnant le profil de matrice le plus approprié (Voir Chiffre 3). Aucune conception unique ne fonctionne mieux pour tous les tubes sans soudure, car la conception dépend de nombreux facteurs, comme l'épaisseur de paroi, nuance d’acier, passer les exigences de réduction, et dessiner les limites du banc.
Chiffre 3
Trois principaux profils de matrice d'étirage à froid sont le rayon, droit, et mélange droit/rayon, ou combinaison
Trois profils de matrice sont:
- Matrice à rayon - l'entrée de la matrice est un arc sans angles vifs ni surfaces planes.
- Matrice droite - l'entrée de la matrice a un plat, surface angulaire, typiquement 10 à 20 degrés par côté.
- Matrice combinée—l'entrée de la matrice combine des surfaces planes et des mélanges de rayon.
Pour chaque ordre de fabrication tiré, une carte de contrôle statistique ou une méthode de test t de Student peut être complétée et utilisée pour optimiser le profil et la dimension de la matrice en tant qu'enregistrement permanent.
Pour la plupart des tubes sans soudure, une matrice à rayon produit la meilleure qualité de paroi. Parce que la matrice de rayon a un profil d'entrée plus progressif et un mélange en douceur dans la section de roulement, le tirage du tube est plus cohérent et donne des dimensions de meilleure qualité. Mais il y a un inconvénient à ce type de matrice: En raison du profil d'admission progressive, seule une petite réduction OD peut être faite sur le tube. Le tube sans soudure doit être personnalisé pour utiliser ce type de matrice, ajouter des frais de conversion.
Atteindre la cohérence de manière cohérente
Atteindre la cohérence nécessite d'analyser le processus en amont, de la fin au début. L'épaisseur de paroi du produit fini spécifiée par le client fournit les dimensions finales du tube traité par le banc d'étirage, qui guide la sélection des matrices et des mandrins. Cette sélection détermine la bonne taille de tube de l'usine sans soudure, qui détermine les paramètres de configuration et de fonctionnement appropriés.