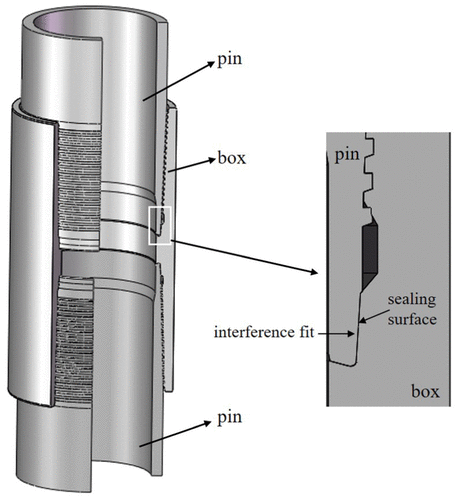
Involucro applicazione tubo in pozzi di gas ad alta temperatura
gennaio 4, 2019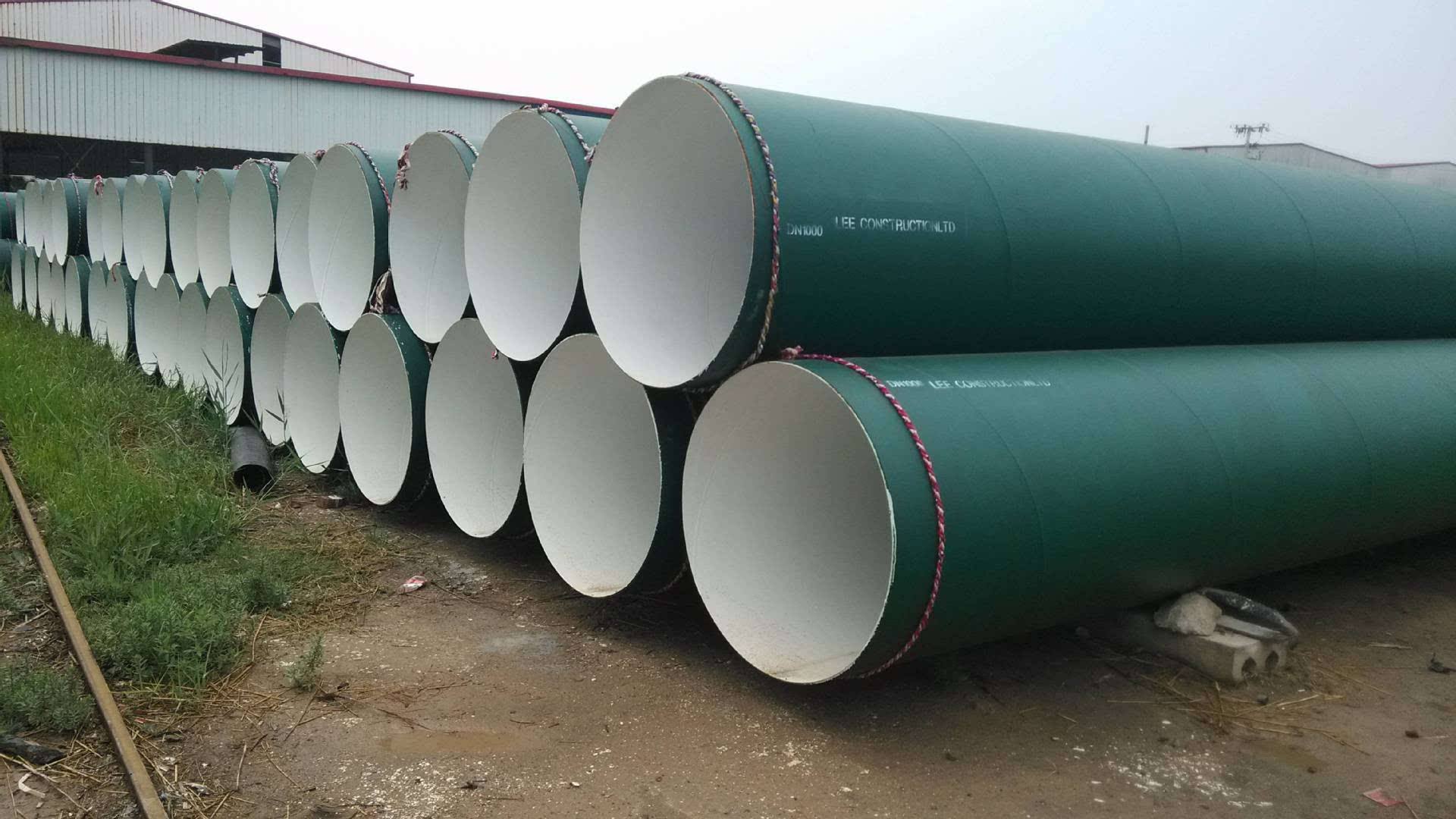
Come è il peso teorico di tubi in acciaio a spirale calcolato?
gennaio 8, 2019ASTRATTO
Il corrosione resistenze di smalto-tubo d'acciaio rivestito nel 3.5 % in peso di soluzione di NaCl è stata valutata e confrontata con quelle del tubo epossidico con potenziale a circuito aperto, Po lineari- resistenza larization, e spectros impedenza elettrochimica- test di copia. T-001c smalto liquami e smalto in polvere GP2118 sono state spruzzate per tubi in acciaio in processi a umido ed elettrostatiche, rispettivamente. La composizione della fase e microstrutture dei due smalti sono stati caratterizzati con diffrazione di raggi X e microscopia elettronica a scansione (SEM). La rugosità superficiale di smalti e la loro forza adesiva con substrati di acciaio sono stati quantificati ed al capire qualità del rivestimento. immagini SEM ha rivelato che entrambi i tipi di rivestimenti smaltati hanno una struttura solida con bolle isolate. prove elettrochimiche mostrato una elevata resistenza alla corrosione dei rivestimenti smaltati come veri fi cata in esame visivo sui campioni testati. In particolare, i campioni di smalto rivestite GP2118 costantemente superato i campioni rivestimento epossidico.
PAROLE CHIAVE: corrosione, spettroscopia di impedenza elettrochimica, smalto, pipeline in acciaio, microscopia elettronica a scansione
INTRODUZIONE
gas naturale, olio, e pericolosi di trasmissione e raccolta dei tubi del liquido hanno raggiunto 484,000 miglia nelle condotte Aging U.S.1 si trovano ad affrontare ridotto
durata e affidabilità a causa della corrosione. Essi possono essere protetti dalla corrosione mediante rivestimento protettivo, Protezione catodica, e l'uso di inibitori di corrosione. Coating come una barriera fisica a elettrolita penetra- zione è uno dei metodi di fi cienti più efficaci ed EF di mitigazione corrosione.
Quando viene applicato internamente per tubazioni in acciaio, cappotto- ing ha diversi vantaggi. Primo, il rivestimento interno può impedire fl uido o gas di interagire e reagire con l'acciaio sottostante. Secondo, tubo di acciaio rivestito riduce i depositi microbiologici e batteri bio fi lm forma- zioni perché maggiore rugosità della superficie di tubo rivestito aiuta scudo i batteri e ad assicurare condizioni di crescita per colonies.2 batterica Terzo e ultimo, il
rivestimento interno può ridurre la caduta di pressione su una lunga distanza di un potere pipeline e quindi impiegato per la trasmissione di petrolio e gas. La caduta di pressione nel tubo rivestito è stato sperimentalmente dimostrato di essere 35% inferiore a quello del tubo di acciaio nudo in un numero di Reynolds di
1 × 107.3
Oggi, due parti solvente rivestimenti epossidici a base, solvente rivestimenti liberi e fusion bonded, e rivestimenti poliammide sono ampiamente utilizzati in petrolio greggio e gas naturale pipelines.4-6 Questi rivestimenti sono debolmente legate con
loro substrato di acciaio e quindi soggetta a sotto- fi lm corrosion.7
smalto porcellanato, come un materiale inorganico, è legato chimicamente al substrato metalli ad una temperatura di 750 ° C per ~850 ° C. Può non solo essere fi nito con una superficie liscia ed estetico, ma anche fornire ex- cellent stabilità chimica, buona resistenza alla corrosione, e durata in vari environments.8 dura differenza
rivestimento epossidico, smalto ha sotto- corrosione pellicola quando localmente violato a causa del suo legame chimico con substrates.9 metallo E 'stato ampiamente utilizzato per la protezione di cottura domestici utensile o protezione contenitore in acciaio nelle industrie. La sua corrosione re- sistance come rivestimento protettivo per il rinforzo di acciaio nelle strutture in calcestruzzo è stato studiato in pre- Studi cedente e dimostrato di essere soddisfacente in general.10-11
in questo studio, il comportamento alla corrosione del tubo in acciaio rivestito internamente con due tipi di smalto (T-001 liquami e GP2118 polvere) è stato esaminato in 3.5 % In peso di NaCl. La composizione di fase e microstruttura di smalti sono stati caratterizzati con diffrazione dei raggi X
(XRD) e microscopia elettronica a scansione (SEM), rispettivamente. La rugosità superficiale del rivestimento di smalto e la sua forza di adesione su substrati di tubi di acciaio sono stati determinati. I comportamenti elettrochimici sono stati studiati con potenziale a circuito aperto (OCP), lineari polare- resistenza ization (LPR), e IMPED elettrochimica- spettroscopia ANCE (EIS) test. ispezioni visive sono state effettuate su campioni esaminati per eventuali segni evidenti di corrosione. La resistenza alla corrosione dell'acciaio smaltato viene confrontato con quello di vernice epossidica.
PROCEDURE SPERIMENTALI
Smaltatura e campioni
Un tubo di acciaio 5L X65 API (MRC globale) con 323.85 mm di diametro esterno e 9.53 mm di spessore della parete è stato usato come substrato metallico in questo studio. La composizione chimica dell'acciaio fornito dal fornitore è presentata nella Tabella 1. Il tubo in acciaio è stato tagliato in primo 18 25 mm × 50 campioni coupon mm. I campioni sono stati poi tagliati in acciaio fatto saltare per 1 min per sbarazzarsi di scaglie di laminazione e di ruggini, e infine purificato con
un solvente di pulizia disponibile in commercio.
Due tipi di smalto sono stati applicati sui tagliandi d'acciaio: T-001 liquami e GP2118 polvere. Le composizioni chimiche delle T-001 fritte di vetro e polvere di smalto GP2118 sono stati determinati mediante raggi X fluorescenza (XRF) come presentato nella Tabella 2. La poltiglia di smalto è stato preparato da fritte di vetro prima fresatura, argilla, e alcuni elettroliti, e poi mescolandoli con acqua finchè il composto era in uno stato di sospensione stabile. L'impasto liquido è stato spruzzato smalto manualmente su provini coupon utilizzando una pistola a spruzzo, che è stato alimentato da un getto di aria compressa come speci fi cato nella Tabella 3. I campioni sono stati riscaldati a 150 ° C per 10 min per scacciare umidità, fi rosso a 815 ° C per 10 min, e infine raffreddato a temperatura ambiente. Per spruzzatura elettrostatica, la polvere GP2118 smalto con una granulometria media di 32.8 um fu usato. Un campo elettrico è formata tra un elettrodo di ugello e il campione. particelle di smalto, spinto fuori la pistola a spruzzo da un flusso d'aria, divenne carica negativa, migrato verso il campione (elettrodo positivo) e sono stati de- postulato. Dopo spruzzatura potere, i tagliandi d'acciaio sono stati spostati in una fornace e fi rosso a 843 ° C per 10 min, e poi spostato fuori e raffreddato a temperatura ambiente. Lo spessore della T-001 rivestimento fu controllato dal tempo di spruzzatura, mentre lo spessore del rivestimento GP2118 era controllata dal numero di pistole. Per confronto, Campioni con vernice epossidica sono stati pre- sbucciato e testato. In questo caso, 3M Scotchkote 323 † epossidica, che è stata applicata nel settore industriale gasdotto, è stato utilizzato per rivestire i campioni. Buoni acciaio sono state rivestite mediante spazzolatura epossidico a temperatura ambiente e poi essiccate all'aria per 3 d prima prove elettrochimiche.
Caratterizzazione di smalto Coatings
Lo spessore del rivestimento e rugosità sono stati misurati con uno spessimetro rivestimento MINITEST 6008 † e microscopio ottico Hirox †, rispettivamente.
La forza di adesione tra il rivestimento e il suo acciaio substrato è stata determinata usando PosiTest † seguente ASTM D4541-09.12 Per migliorare il legame con il rivestimento, un 20 mm dolly diametro alla base è stata irruvidita con carte abrasive, e purificato con alcool per rimuovere l'ossidazione e contaminanti. La base del carrello è stato fatto aderire con uno strato uniforme di colla sulla superficie del rivestimento di prova. Dopo l'indurimento per 24 h, il rivestimento intorno il carrello è stato rimosso utilizzando un 20 mm utensile di taglio al fine di isolare il carrello in una zona di prova speci fi. Il carrello è stato finalmente tirato fuori la superficie del campione perpendicolarmente ad un tasso stress 0.4 MPa / s. La forza massima di ciascun campione rivestito è stato registrato.
Al completamento del test di corrosione, le fasi di rivestimento sono stati esaminati direttamente sulla superficie dei campioni di acciaio rivestiti di XRD (Philip X'Pert †) con angolo di diffrazione (2io) varia tra 10 ° e 55 °. sezioni dei campioni di smalto rivestite sono state preparate per l'analisi microstruttura con SEM (Hitachi S4700 †). Ogni campione è stato smaltato primo freddo montato in resina epossidica (EpoxyMount †, Allied High Tech Products, Inc.) e tagliata in un 10 sezione trasversale di spessore mm utilizzando una sega diamantata. Poi, la sezione trasversale è stata abrasa con documenti carburo 1200 grinta, risciacquato con acqua deionizzata, e infine essiccato in aria a temperatura ambiente prima dell'esame. immagini SEM sono stati analizzati con il software ImageJ † per la valutazione della porosità.
prove elettrochimiche
Ogni campione è stato saldato con un filo di rame per misurazioni elettrochimiche come illustrato in figura 1. Tutti i lati del campione, tranne lo smalto- o faccia epossidico sono stati coperti con resina epossidica Marine.
L'area smalto o epossidico esposto era 30 mm × 20 mm dimensioni.
Tutti i campioni sono stati immersi in 3.5 soluzione NaCl% in peso con il pH 7 e testato presso la sala tempera- ture per 69 d. La soluzione è stata preparata aggiungendo purificato cloruro di sodio ed (Fisher Scientific, Inc.) in acqua distillata.
Al tempo di 1, 3, 6, 13, 27, 41, 55, e 69 d, OCP, LPR, e prove EIS sono state effettuate per monitorare l'evoluzione corrosione dello smalto- e campioni vernice epossidica. Un sistema a tre elettrodi standard è stato utilizzato per prove elettrochimiche, tra cui un 25.4 mm × 25.4 mm × 0.254 foglio platino mm come controelettrodo, elettrodo a calomelano (SCE) come un elettrodo di riferimento, e il campione rivestito come elettrodo di lavoro. Tutti e tre gli elettrodi sono stati collegati ad un Gamry 1000E potenziostato / galvanostato † per l'acquisizione dati.
Dopo ogni OCP stabile (della durata di 1 h) è stato registrato, un test EIS è stata eseguita con un'onda sinusoidale di potenziale 10 mV in ampiezza intorno al OCP ed una frequenza di 100 kHz 5 mHz. Il test è stato condotto da LPR scansione di un campo di ± 15 mV intorno al OCP ad una velocità di scansione di 0.167 mV / s. Le curve LPR vengono utilizzati per determinare la resistenza di polarizzazione Rp, che è uguale alla pendenza della regione lineare di una curva di polarizzazione attorno corrente zero:13
Rp = AE = Δi
dove AE e Δi rappresentano gli incrementi di tensione e corrente, rispettivamente, nella parte lineare della curva di polarizzazione a i = 0. misurazioni LPR sono stati usati per calcolare la densità di corrente di corrosione dall'equazione Stern-Geary:13
icorr = vavc = ½2.303dva + βcThRp (2)
dove ba e βc rappresentare la costante anodica Tafel (0.12) e la costante Tafel catodica (0.12), rispettivamente, e icorr è la corrente di corrosione.
RISULTATI E DISCUSSIONE
coating Caratterizzazione
Fasi in smalto - modelli XRD sulla superficie del GP2118 e T-001 campioni di smalto rivestite dopo immersione in 3.5 soluzione di NaCl% in peso per 69 d sono identi fi cati e visualizzati nella figura 2. Quarzo SiO2 è presente in entrambi i tipi di rivestimenti smalto. Le cime più alte intensità di quarzo SiO2 erano a 26 ° e 26,5 ° per GP2118 e T-001 smalti, rispettivamente.
Microstruttura a smalto / Substrato Interfaccia - immagini a sezione trasversale SEM all'interfaccia acciaio / rivestimento con diversi fi ingrandite sono rappresentati in figura 3. I rivestimenti smaltati hanno una struttura solida con aria scollegato bolle attraverso lo spessore del rivestimento (figure 3[a1] e [b1]). Le bolle d'aria sono formati durante la chimica ad alta temperatura
reazione della fritta di vetro smalto dell'acciaio durante anello fi process.14-15 I rivestimenti smalto hanno numerosi
isolate piccoli pori, ad eccezione di GP2118 smalto che ha alcuni grandi pori con un diametro di circa 105 Μm. Il contenuto porosità del T-001 smalto è stato misurato essere 4.26%, che è inferiore 12.72% per lo smalto GP2118. figure 3(a2) e (b2) mostra le interfacce fi cato smalto / acciaio ingrandite in cui sporgenze piccola-Fe crescono nel rivestimento di smalto per formare vari punti di ancoraggio. Queste particelle di spinello epitassiali migliorare l'adesione tra lo smalto e la sua substrate.16 acciaio
Pull-Off Forza - lo spessore misurato, ruvidezza della superficie, e forza di legame di tre tipi di rivestimenti sono riassunte nella Tabella 4. La media e la deviazione standard dello spessore e la rugosità superficiale di ciascuna rivestimento sono stati calcolati da
27 misure effettuate da tre diversi campioni che sono stati lucidati per avere una superficie piatta per il test pull-off. La media e la deviazione standard della forza di legame di ciascun rivestimento sono stati calcolati dalle tre prove a strappo condotte. Si può vedere dalla tabella 4 che rivestimento epossidico è più spessa (396 Μm) e T-001 smalto è il più sottile (230 Μm). Il
rugosità delle tre rivestimenti è intorno 1 Μm, indicando superfici lisce in tutti i campioni.
Al termine delle prove di pull-off, le superfici dolly e frattura substrato sono mostrati in figura 4. In un test di legame pull-off, quattro possibili cause di guasto includono: (1) pausa adesione tra il rivestimento e il suo substrato di acciaio, (2) pausa coesione all'interno dello strato di rivestimento, (3) pausa colla, e (4) pausa mista o un combi- nazione delle pause di cui sopra a locations.17 multipla
rivestimenti smaltati hanno una modalità mista in fallimento- volving una rottura all'interno del rivestimento (pausa coesa) e una pausa nel collante usato per legare il carrello al modello. Rivestimento epossidico ha anche una modalità mista guasto coinvolge una rottura all'interno del rivestimento (pausa coesa), una pausa tra il rivestimento e il substrato di acciaio (pausa adesivo), e una pausa di colla. Non ci sono interruzioni adesivi per rivestimenti smaltati perché i punti di ancoraggio sull'interfaccia aumentano il legame tra un rivestimento di smalto e suo acciaio substrato come mostrato in figura 3. Specificamente, smalto GP2118 ha la forza di legame più alto con un valore medio di 17.89 MPa, rivestimento epossidico ha la forza di legame più basso di 8.01 MPa, e T-001 smalto ha una forza di legame 16.85 MPa.
figure 5(un) e (b) rappresentare le morfologie superficiali Magni fi cata frattura come illustrato nelle figure 4(a2) e (b2), rispettivamente. Quando il carrello è stato tirato fuori il campione rivestiti ad angolo retto, una crepa avviato e propaga attraverso grandi bolle d'aria all'interno del cappotto- Ing sotto carichi crescenti. figure 6(un) e (b) Immagini mostrano SEM per le sezioni trasversali della SPE testato- cIMEnS nelle aree rettangolari di figure 4(a2) e (b2), rispettivamente. Superfici di frattura dei provini sono generalmente liscia con il minimo è rimasto rivestimento spessori di circa 70 micrometri e
40 micron Per GP2118 e T-001 sMALTI, rispettivamente. Nel confronto con la figura 3, figure 6(un) e (b) Indicano che le superfici di frattura sono lontani da loro strati di legame corrispondenti alle interfacce smalto / substrato e passare attraverso lo strato più debole che collega le bolle d'aria di grandi dimensioni nel rivestimento perché l'aderenza dello smalto sulle superfici in acciaio è chimicamente rinforzato con la crescita delle particelle epitassiale spinello nello smalto durante la reazione chimica nel fi anello ProcESS.16