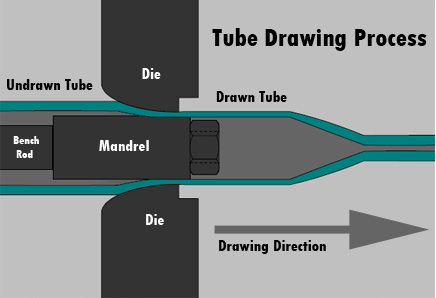
The influence of the processing parameters on the performance of the two-roll piercing operation
June 29, 2022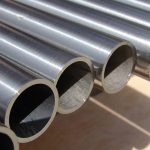
Classification, production process and mechanical properties of seamless steel pipes
July 5, 2022The e®ectiveness of weld joints primarily depends on the fusion of base metal, minimum heat- a®ected zone (HAZ) and lesser residual stresses. The severity of thermomechanical e®ects e.g. weld shrinkages and residual stresses is signi¯cantly minimized by narrow gap welding tech- nique over the traditional welding. This work describes the welding of A333 Grade 3 steel pipes by the application of GMAW and PGMAW techniques. The analysis is made to capture the e®ects of groove designs on residual stress and transverse shrinkage. The process parameters used for the analysis are voltage, current and welding speed. In this work, narrow groove design using PGMAW process is capable of reducing the number of passes and area of weld deposit by 35–40% by volume. In PGMAW, decrement in residual stresses is observed with a narrow groove compared to conventional V groove technique. The results are validated by metallurgical and mechanical investigation of welded joints. This work will help other researchers to under- stand the e®ect of narrow gap welding using an optimum number of passes for thick pipes.
Keywords: Transverse shrinkage; PGMAW; residual stresses; HAZ; narrow groove design; A333 steel.
1. Introduction
Mild steel pipes of various thickness are accessible ¯nancially and have a wide scope of utilization in the development of cutting edge structures. Mechanical properties of these steels mainly depend on the chemical composition of the constituents. A333,
*Corresponding author.Grade 3 pipes have great formability and weldability. These alloys have high yield strength and ultimate tensile strength, i.e. 240 and 450 MPa, respectively. According to American piping products, A333 steel is good for low-temperature applications.1
Welding is majorly used in the construction and piping industries. Welded joints are subjected to severe residual distortion because of weld thermal cycles.2–4 The residual stresses cause many problems such as crack, performance deterioration, shrinkage and less strength.5 Therefore, it is necessary to measure the shrinkage and
associated residual stress produced during the welding.6 Moreover, there is a re-
quirement to develop a suitable welding technique for minimizing residual stresses in the weld.
Common processes for thick pipe welding are SMA, FSW, TIGW and gas metal arc welding (GMAW). These processes in°uence the weld thermal cycle, amount of weld deposition, shielding environment and the various welding parameters.7–9 PGMAW process was ¯rst used in late 80s and has better control on the arc for sound welds.10,11 Better control on the arc in GMAW process is due to peak current (Ibase current (Ib ), frequency (f ), peak pulse duration (tp ), base current duration (tb ),
etc. These parameters provide comparatively low heat input. A dimensionless key factor Ø ¼½ðIb =Ip Þf *tb ] is used to in°uence the pulse characteristics.9,12–14
Large thermal gradients can be developed in the welding of the thicker section due to uneven localized heating and cooling cycle in the weld region. A signi¯cant mis¯t strain will be developed due to the di®erence in the expansion and contraction of the material being welded. Di±dent value of the mis¯t can be attuned by elastic strain. However, very high mis¯t strain induces localized plastic deformation resulting in the development of residual stresses. When the component comes under thermal equi- librium, noteworthy residual stresses occur near the weld. This case can be found predominantly for the thicker sections due to a large number of thermomechanical cycles.15 For large components, it is di±cult to apply the residual stress removal
techniques like shot peening, laser shock peening, etc.16
In a heavy plate, GMAW with narrow groove design provides maximum e±ciency and better quality as compared to traditional welding.17 The severity of thermo-
mechanical e®ects can be signi¯cantly reduced by lowering the volume of weld metal in a joint and the same can be achieved by a narrow gap welding technique for thicker sections. Narrow groove also provides better productivity due to less weld volume and lesser welding time. Tan et al.. demonstrated the narrow gap TIG welding of nuclear rotor steel pipes. They studied the residual stress developed using the hole drilling technique.18 Xu et al. studied the mechanical and microstructural
properties of HSLA steel fabricated by narrow gap welding. E®orts have not been done to compare the residual stresses generated in varied groove designs. This work is being carried out to evaluate the residual stress and transverse shrinkage (TS) using GMAW and PGMAW process. For better results, a comparison of these processes with narrow groove design has been reported.