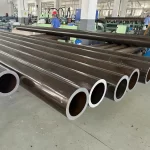
API X65 Line-Pipe Steels Effects of Granular Bainite and Polygonal Ferrite on Yield Point Phenomenon
September 13, 2024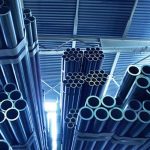
High Temperature and High Pressure Resistance Line Pipe Steel and Pipes of Key Technologies
September 21, 2024Introduction:
Line pipes are a crucial yet often overlooked piece of infrastructure that form the backbone of our energy distribution systems. By transporting liquids and gases over long distances, these metal pipes power our economies and way of life. However, the structural integrity demands on line pipes are immense—they must withstand both the internal pressure of fluids moving within and the external forces exerted by surrounding soils over many decades of service. This places stringent requirements on the manufacturing and design of line pipes to ensure public safety and operational reliability.
This report will examine the structural mechanics and metallurgical engineering considerations that underpin the manufacturing of line pipes. Key focus areas include common line pipe materials, thickness and geometry designs, welding and coating processes, and quality control measures. The goal is to provide insight into how line pipes are engineered to withstand the immense and multidirectional stresses they experience underground.
Line Pipe Materials:
The choice of material is a foundational decision in line pipe design, as it dictates critical properties like strength, ductility, and corrosion resistance. Carbon steels were traditionally used due to their availability and cost-effectiveness. However, advanced grades of alloy and stainless steels have increasingly replaced carbon varieties for many applications:
- Carbon steels: Used for low-pressure distribution lines. Compositions contain 0.15-0.3% carbon. Provide moderate strength at low cost. However, limited corrosion resistance drives use of protective coatings.
- Alloy steels: Used for high-pressure transmission lines. Alloying elements like chromium, molybdenum boost strength properties significantly. Popular grades are X65, X70, X80 with minimum yield strengths up to 80 ksi. Offer good strength-to-weight ratios.
- Stainless steels: Deployed for extremely corrosive services involving hydrogen sulfide or carbon dioxide. Steels like 316L and 904L have excellent corrosion resistance from chromium content of 16-25%. However, reduced formability requires higher cost welding processes.
Line pipe steel must satisfy specifications across mechanical properties like tensile strength and impact energies. Production is closely controlled to ensure consistent metallurgy throughout each heat treated pipe.
Pipe Thickness Design:
The thickness of line pipe walls is deliberately engineered based on factors such as internal pressures, operating temperatures, soil conditions, and design life. Pipe pressure ratings are represented in psi or bars, where higher rated pipes require thicker material to safely withstand greater internal forces.
Considerations for thickness include:
- Pressure containment: Minimum required thickness per code is calculated using pressure vessel equations accounting for stresses from internal and sometimes external loads. Higher pressures mandate thicker cross-sections.
- Handling/installation: Pipe needs sufficient rigidity to resist damage and deformation during transportation, stringing, bending, and welding operations. Thicker walls help maintain pipe integrity.
- Corrosion allowance: An added thickness dimension accounts for any metal loss expected over the design life from external corrosion or erosion effects. Typically 0.09-0.18 inches for underground pipes.
- Weight considerations: Overly thick walls increase transportation and installation costs significantly. Structural analyses aim to use minimum gage needed for safety.
Proper wall thickness ensures line pipes can withstand pressures over 50+ years underground while minimizing material usage and installation expenses. Non-destructive testing checks for thickness uniformity.
Pipe Geometry:
Beyond material selection and thickness, precise pipe geometry is crucial for withstanding mechanical and hydraulic stresses in service. Close dimensional tolerances are maintained for:
- Diameter: Nominal sizes range from 2-60 inches for most transmission lines. Tolerances of +0.125 inches ensure consistent internal volumes.
- Roundness: Ovalities less than 1% of nominal diameter per code. Out-of-roundness creates undesirable pressure peaks.
- Straightness: Deviation from a straight centerline must remain under generally accepted amounts based on pipe length. Kinks or curling weaken pipe structurally.
- End finishes: Beveled ends on most pipes aid butt welding. Square cut ends are also used, requiring more time-consuming preparation before joining.
- Surface finish: As-rolled or as-manufactured surfaces below aGivenRa/Ry threshold per API specification. Smoother surfaces ease coating application and avoid defects.
- Tolerances: All dimension checks occur with micrometers and other tools to ensure pipes conform to industry standards like ANSI, API or ASTM criteria.
Compliance to tight geometric specifications is vital for dependable field performance of line pipes over many pressure cycles.
Welding of Line Pipes:
The two dominant joining techniques for line pipes require careful engineering implementation to uphold structural integrity goals.
Longitudinal or spiral welding: Used for most large-diameter, high-pressure steel pipelines. It involves welding rolled strips or plates into cylindrical tubes using automated welding machines. This builds pipe lengths up to 60 feet and diameters into the 60-inch range. Advantages are more continuous pipe qualities and higher field production rates. However, achieving full joint penetration and fusion across large, tapered edges presents technical challenges.
Butt welding: Commonly deployed for smaller diameter, lower pressure gathering lines. It involves abutting pipe ends and directing concentrated heat to fully fuse the two joint areas together. Though smaller diameters of 2-16 inches are more easily accommodated, it creates discontinuities at each weld point that need testing. Alignment holds importance.
Robotic and automatic welding techniques like SAW (submerged arc welding) promote joint quality assurance and repeatability at high work rates. Still, each weld receives non-destructive evaluation using x-ray, ultrasonic, or radiographic methods to ensure structural and pressure containment abilities meet applicable pipeline safety codes.
Coatings for Corrosion Protection:
Exposed carbon and low-alloy steels rely upon protective coatings to maintain pipe integrity in corrosive buried or submerged environments over many decades. Common anti-corrosion methods involve:
Fusion bonded epoxy (FBE): Heat-cured powder epoxy yields a hard, impermeable shell that withstands direct burial and cathodic protection applications. Applied as a liquid on preheated pipes, it adheres tenaciously. Extensively used for transmission lines transporting natural gas, oil, and other commodities.
Three-layer polyurethane: Multiple coats of liquid polyurethane, adhesive, and topcoat provide flexibility with similar protection to fusion bonded epoxy for some sour gas lines. Better elongation properties accommodate thermal cycling.
Concrete weight coating: Slurried cementitious material circulated onto wet FBE coatings balls into a protective shell that also dampens pipe vibrations during backfilling and adds mass for buoyancy control offshore.
Specialized alloys and non-traditional coatings enable pipelines to accommodate hydrogen sulfide, carbon dioxide and abrasive slurries as well. Coating selection considers economics, application challenges, and long-term shielding abilities against corrosion.
Quality Assurance in Manufacturing:
Given public safety and environmental protection duties, line pipes undergo rigorous quality checks throughout fabrication. Key assurance stages involve:
- Mill testing of steel compositions, strengths and impact properties on samples from each heat.
- Non-destructive testing of pipe body using ultrasonic, magnetic particle, or radiographic exams to screen for imperfections.
- Geometric measurements for diameters, wall thicknesses, straightness and ovalities recorded electronically.
- Visual and mechanical inspections of weld beads and heat affected zones using dye-penetrant and guided-bend tests.
- Hydrotesting of finished pipe strings at elevated pressures, often 1.5 times the MAOP.
- Coating thickness checks and holiday detection testing for pinholes or areas of missing FBE.
- Traceability of pipe records to original heat numbers for batch-by-batch defect analysis if needed.
Quality management systems based on ISO, CSA or API standards drive manufacturing with zero-defect mindsets. This provides assurance line pipes will safely sustain pressures over long-term underground deployments.
The Backbone of Infrastructure
Imagine the vast networks of pipelines snaking across countries, transporting essential resources like oil, gas, and water. These pipelines are the unsung heroes of modern infrastructure, and at the heart of them are metal pipes, designed with precision and strength to withstand various environmental challenges.
The Art of Pipe Manufacturing
The journey of a metal pipe begins with raw materials, typically steel, which is chosen for its durability and strength. The manufacturing process involves several steps, each critical to ensuring the pipe’s integrity and performance.
- Material Selection and Preparation: It all starts with selecting the right grade of steel. The steel is then processed into sheets or coils, ready to be transformed into pipes.
- Forming: This is where the magic happens. The steel is shaped into a cylindrical form through processes like rolling or extrusion. It’s fascinating to watch as flat sheets morph into round pipes!
- Welding: To ensure the pipe holds its shape, the edges are welded together. There are various welding techniques, like electric resistance welding (ERW) or submerged arc welding (SAW), each chosen based on the pipe’s intended use.
- Sizing and Shaping: Once welded, the pipe is sized to precise dimensions. This step is crucial for ensuring the pipe fits perfectly in its intended application.
- Heat Treatment: To enhance the pipe’s mechanical properties, it undergoes heat treatment. This process involves heating the pipe to a specific temperature and then cooling it, which improves its strength and flexibility.
- Inspection and Testing: Quality control is paramount. Pipes are subjected to rigorous testing, including ultrasonic testing and hydrostatic testing, to ensure they meet industry standards and can withstand the pressures they’ll face in the field.
Structural Mechanics: The Science of Strength
Now, let’s talk about the structural mechanics involved in designing these metal marvels. At its core, it’s about understanding how materials behave under various forces and conditions.
- Stress and Strain: Pipes must endure immense pressure, especially in oil and gas applications. Engineers analyze stress (force per unit area) and strain (deformation) to ensure the pipe can handle these forces without failing.
- Buckling and Collapse: Imagine a straw collapsing when you suck too hard. Pipes face similar risks under external pressure. Engineers design pipes to resist buckling and collapse, using mathematical models and simulations to predict and prevent such failures.
- Fatigue and Fracture: Over time, repeated stress can cause materials to weaken and fracture. By studying fatigue, engineers can design pipes that last longer, even under constant pressure cycles.
Designing for the Real World
Designing metal pipes isn’t just about crunching numbers. It’s about considering real-world conditions like temperature fluctuations, corrosive environments, and seismic activity. Engineers use advanced software to simulate these conditions, ensuring the pipes perform reliably in any scenario.
Innovations in Pipe Design
The field of pipe manufacturing is constantly evolving, with innovations aimed at improving performance and sustainability. For instance, researchers are exploring new materials and coatings to enhance corrosion resistance, which is a major concern in harsh environments.
Conclusion: The Unsung Heroes
Conclusion:
Designing and manufacturing line pipes to serve as structural conduits for fluids over decades requires understanding the demanding interactive stresses they experience and implementing smart material choices, precision manufacturing techniques, and quality control protocols. Using structural analysis and metallurgical engineering principles benefits producers and end-users by ensuring transmission pipelines maintain integrity without fail under both internal pressure and external force loadings. Continued improvements in steel grades, non-destructive testing abilities, and corrosion prevention methods will further enhance the reliability of buried infrastructure transporting energy resources to societies worldwide.Metal pipes might not be the most glamorous topic, but they’re essential to our daily lives. From transporting oil and gas to delivering clean water, they play a vital role in modern infrastructure. Understanding the structural mechanics and design behind these pipes gives us a deeper appreciation for the engineering feats that keep our world running smoothly.