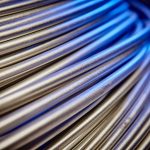
Inconel 601® Alloy Steel Pipe | (UNS N06601, W.Nr. 2.4851)
April 26, 2025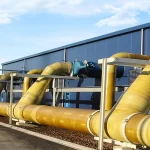
Material Design for 700℃ Ultra-Supercritical High-Pressure Boiler Pipe
May 6, 2025: Welding Process, Materials, and Environment
Seamless steel pipes are critical materials with wide applications. The welding technology for seamless steel pipes is a key factor in ensuring pipeline quality and performance. This article discusses the essentials of seamless steel pipe welding technology from four perspectives: welding process, welding materials, welding environment, and quality control, providing a reference for practitioners.
1. Welding Process
The welding process for seamless steel pipes must comply with relevant standards, including welding current, voltage, speed, and shielding gas. Before welding, equipment should be inspected to ensure normal operation; during welding, conditions must be strictly controlled to ensure weld quality; after welding, inspections should verify compliance with standards.
Common welding methods for seamless steel pipes include manual arc welding, gas-shielded welding, and brazing. The appropriate method and parameters are selected based on pipe material, diameter, wall thickness, groove type, and welding position. Below are the characteristics and key points of these methods.
1.1 Manual Arc Welding
Manual arc welding is a widely used method suitable for both seamless and welded steel pipes. It is simple to operate, has low equipment costs, and is highly adaptable. However, it has drawbacks such as unstable weld quality, significant spatter, large deformation, and susceptibility to porosity and cracks.
Key points for manual arc welding:
-
Electrode Selection: Choose electrodes based on pipe material, thickness, weld position, and type. Low-hydrogen electrodes (e.g., J507, J507Fe, E7018) are typically used, with diameters ranging from 2.5mm to 5mm and welding currents from 80A to 300A.
-
Groove Preparation: For butt welding, proper groove preparation or beveling is required. Use V-shaped or I-shaped grooves depending on wall thickness. Groove surfaces must be smooth and clean; defective pipe ends should not be welded. Groove specifications:Wall ThicknessGroove TypeGroove AngleGroove Gap≤6mmV60°~70°1~2mm>6mmI30°~40°2~4mm
-
Pipe Alignment: Align pipes using supports or hoists to ensure centered positioning without displacement. The outer surfaces must be flush, verified using a steel ruler at 200mm from the weld on the opposite pipe surface.
-
Tack Welding: After alignment, perform tack welds with a thickness matching the first weld layer but not exceeding 70% of the wall thickness. The weld root must be fully penetrated, with tack welds evenly and symmetrically placed.
-
Layered Welding: Determine the number of weld layers and sequence based on wall thickness and electrode diameter. Weld from bottom to top, starting with the root, followed by filler and cap layers. Maintain proper welding speed and electrode angle for uniform, defect-free welds. Clean slag and spatter before each layer and allow natural cooling. Stagger arc initiation and termination points by 20mm or 30°.
1.2 Gas-Shielded Welding
Gas-shielded welding uses inert or active gases to protect the arc and molten pool, preventing contamination by oxygen or nitrogen. It is suitable for seamless and welded steel pipes, offering high weld quality, minimal deformation, low spatter, and high efficiency. However, it has higher equipment costs, stricter operational requirements, and sensitivity to environmental conditions.
Key points for gas-shielded welding:
-
Shielding Gas Selection: Choose gas type, flow rate, and pressure based on pipe material, thickness, and weld type. Common gases include CO₂ or Ar+CO₂ mixtures, with flow rates of 10L/min to 25L/min and pressures of 0.2MPa to 0.4MPa.
-
Welding Wire Selection: Select wire based on pipe material, thickness, and weld type. Low-carbon steel wires (e.g., H08MnA, H08Mn2SiA) with diameters of 0.8mm to 1.6mm are typically used, with reverse polarity (workpiece negative, torch positive).
-
Groove Preparation: Same as manual arc welding (see table above).
-
Pipe Alignment: Same as manual arc welding.
-
Tack Welding: Same as manual arc welding.
-
Layered Welding: Same as manual arc welding, ensuring proper wire angle and speed for uniform welds.
1.3 Brazing
Brazing uses molten metal or alloy as filler to join metal parts, suitable for seamless and welded steel pipes. It offers high weld quality, minimal deformation, low spatter, and high efficiency but shares the same drawbacks as gas-shielded welding.
Key points for brazing:
-
Filler Metal Selection: Choose filler based on pipe material, thickness, and weld type. Copper-based or silver-based fillers (e.g., BCuP-2, BCuP-3, BAg-1) with diameters of 1mm to 3mm and melting points of 600°C to 900°C are common.
-
Flux Selection: Use inorganic acids or salts (e.g., phosphoric or boric acid) as flux, with 5%–10% application, evenly coated on weld surfaces or filler.
-
Groove Preparation, Pipe Alignment, Tack Welding, and Layered Welding: Same as above.
2. Welding Materials
Welding materials significantly affect weld quality and performance. They must match the pipe material, exhibit good weldability and mechanical properties, and comply with standards for chemical composition, mechanical properties, and weldability. Store materials in dry, ventilated, and cool conditions to prevent moisture, rust, or contamination.
Common welding materials for seamless steel pipes include electrodes, wires, and brazing fillers. Their characteristics and selection principles are as follows:
2.1 Electrodes
Electrodes, used in manual arc welding, consist of a core (for current and filler metal) and a coating (for arc and pool protection). They are simple, cost-effective, and adaptable but prone to unstable quality, spatter, deformation, and defects.
Selection principles:
-
Match electrode to pipe material, typically low-carbon or low-alloy steel (e.g., J421, J422, J507, J507Fe, E6013, E7018).
-
Choose diameter (2.5mm–5mm) based on thickness; larger diameters increase current and efficiency but risk spatter and deformation.
-
Use low-hydrogen electrodes for better weldability and mechanical properties, reducing porosity and cracking.
2.2 Welding Wires
Welding wires, used in gas-shielded welding, consist of a core and sometimes a flux core for protection. They offer high quality, minimal deformation, low spatter, and efficiency but require costly equipment and skilled operation.
Selection principles:
-
Match wire to pipe material, typically low-carbon or low-alloy steel (e.g., H08MnA, H08Mn2SiA, ER50-6, ER70S-6).
-
Choose diameter (0.8mm–1.6mm) based on thickness; larger diameters increase efficiency but risk spatter.
-
Use solid or flux-cored wires; solid wires offer better properties, while flux-cored wires enhance protection and reduce porosity.
2.3 Brazing Fillers
Brazing fillers consist of a core (for joining) and flux (for oxide removal and wetting). They share the advantages and disadvantages of welding wires.
Selection principles:
-
Match filler to pipe material, typically copper- or silver-based (e.g., BCuP-2, BCuP-3, BAg-1, BAg-2).
-
Choose diameter (1mm–3mm) based on thickness; larger diameters increase efficiency but risk spatter.
-
Use appropriate flux (e.g., phosphoric or boric acid) at 5%–10%, applied evenly.
3. Welding Environment
The welding environment significantly impacts quality and performance. It must meet standards for temperature, humidity, wind speed, lighting, and noise, maintaining dry, ventilated, bright, and quiet conditions to avoid interference from extreme heat, humidity, wind, light, or noise.
Environmental requirements:
-
Temperature: 5°C–40°C. High temperatures cause overheating, porosity, cracks, or burn-through; low temperatures cause cold cracks, incomplete fusion, or lack of penetration.
-
Humidity: 40%–80%. High humidity causes material moisture, leading to porosity, cracks, or oxidation; low humidity causes excessive dryness, leading to spatter or deformation.
-
Wind Speed: 0.5m/s–1.5m/s. High wind disperses shielding gas, causing defects; low wind causes gas accumulation, leading to spatter or deformation.
-
Lighting: 300lx–500lx. Excessive light impairs vision, causing errors; insufficient light leads to defects or hazards.
-
Noise: 60dB–80dB. Excessive noise impairs hearing, causing errors; low noise reduces focus, leading to defects or hazards.
4. Quality Control
Quality control is critical for ensuring weld quality and performance, adhering to standards for planning, inspection, and evaluation. It should be conducted before, during, and after welding.
Quality control components:
-
Quality Planning: Develop specifications and measures for welding processes, materials, equipment, personnel, environment, inspection, and evaluation based on project requirements. Formulate before welding, implement during, and review after.
-
Quality Inspection: Conduct testing, analysis, and evaluation of welds before, during, and after welding by qualified personnel or third parties. Methods include non-destructive testing, destructive testing, and metallographic analysis, assessing weld appearance, dimensions, shape, defects, structure, and mechanical properties. Feedback results promptly for corrections.
-
Quality Evaluation: Classify and certify weld quality based on inspection results, adhering to national, industry, or enterprise standards. Evaluate weld and project quality grades and acceptance conditions. Feedback results for corrections.
5. Conclusion
Seamless steel pipe welding is a multifaceted technology involving processes, materials, environments, and quality control. Mastering these elements is crucial for improving weld quality and performance, ensuring pipeline safety and reliability. This article has outlined key points across these four areas, hoping to provide valuable insights.