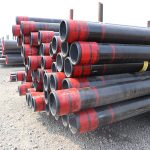
ASTM A333M Petroleum Cracking Pipe
November 7, 2024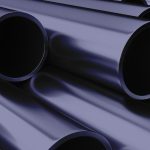
Difference Between Inconel Alloy 600 and Incoloy Alloy 800 Steel Pipes
November 20, 2024Welding of Nickel Alloy Steel Pipe Buttering and Stainless Steel Pipe: A Comprehensive Guide
Introduction
Welding dissimilar metals, such as nickel alloy steel pipes and stainless steel pipes, is a common requirement in industries like power generation, oil and gas, petrochemical, and nuclear energy. These metals are often joined using a technique called buttering, which involves applying a layer of compatible filler material to one of the base metals before the final weld is made. This process helps to mitigate issues related to dissimilar metal welding, such as thermal expansion mismatch, corrosion, and cracking.
In this comprehensive guide, we will explore the process of welding nickel alloy steel pipe buttering to stainless steel pipes. We will cover the welding techniques, filler materials, preparation steps, and post-weld treatments required to ensure a successful weld. Additionally, we will provide detailed tables outlining the chemical composition, mechanical properties, and welding parameters for various nickel alloys and stainless steels.
Why Buttering is Necessary for Dissimilar Metal Welding
When welding dissimilar metals like nickel alloys and stainless steel, several challenges arise due to differences in their chemical composition, thermal expansion coefficients, and corrosion resistance. These differences can lead to issues such as:
- Cracking: The different thermal expansion rates of nickel alloys and stainless steel can cause stress during heating and cooling, leading to cracking in the weld joint.
- Corrosion: Dissimilar metals can form galvanic cells, leading to accelerated corrosion at the weld joint.
- Dilution: The mixing of dissimilar metals during welding can result in a weld with undesirable mechanical properties or corrosion resistance.
To overcome these challenges, a technique called buttering is used. Buttering involves applying a layer of compatible filler material (usually a nickel-based alloy) to the stainless steel pipe before the final weld is made. This layer acts as a buffer, reducing the risk of cracking and corrosion by creating a more compatible interface between the two dissimilar metals.
Nickel Alloys and Stainless Steels: An Overview
Nickel Alloys
Nickel alloys are known for their excellent corrosion resistance, high-temperature strength, and oxidation resistance. They are commonly used in industries that require materials to withstand harsh environments, such as chemical processing, aerospace, and power generation.
Some common nickel alloys used in piping systems include:
- Inconel 600: A nickel-chromium alloy with excellent resistance to oxidation and corrosion at high temperatures.
- Inconel 625: A nickel-chromium-molybdenum alloy known for its high strength and resistance to pitting and crevice corrosion.
- Monel 400: A nickel-copper alloy with good corrosion resistance in a wide range of environments, including seawater and acidic environments.
- Hastelloy C-276: A nickel-molybdenum-chromium alloy with excellent resistance to a wide range of corrosive media, including strong acids and chloride environments.
Stainless Steels
Stainless steels are iron-based alloys that contain at least 10.5% chromium, which gives them their characteristic corrosion resistance. Stainless steels are widely used in industries such as food processing, pharmaceuticals, and oil and gas due to their resistance to corrosion and ease of fabrication.
Common types of stainless steel used in piping systems include:
- 304 Stainless Steel: An austenitic stainless steel with good corrosion resistance and excellent formability.
- 316 Stainless Steel: An austenitic stainless steel with added molybdenum for improved resistance to pitting and crevice corrosion.
- 321 Stainless Steel: An austenitic stainless steel stabilized with titanium to prevent carbide precipitation during welding.
- Duplex Stainless Steel: A stainless steel with a mixed microstructure of austenite and ferrite, offering high strength and excellent resistance to stress corrosion cracking.
Welding Process for Nickel Alloy Steel Pipe Buttering and Stainless Steel Pipe
Step 1: Material Selection
The first step in the welding process is selecting the appropriate nickel alloy and stainless steel materials. The choice of materials depends on the specific application, operating environment, and the properties required for the final weld joint.
For example, if the application involves high temperatures and corrosive environments, Inconel 625 may be chosen for the nickel alloy, while 316 stainless steel may be selected for the stainless steel pipe.
Step 2: Filler Material Selection
The filler material used for buttering and welding plays a crucial role in the success of the weld. The filler material must be compatible with both the nickel alloy and the stainless steel to prevent issues such as cracking, corrosion, and dilution.
Common filler materials used for welding nickel alloys to stainless steel include:
- ERNiCr-3: A nickel-chromium filler material commonly used for welding Inconel 600 to stainless steel.
- ERNiCrMo-3: A nickel-chromium-molybdenum filler material used for welding Inconel 625 and Hastelloy C-276 to stainless steel.
- ERNiCu-7: A nickel-copper filler material used for welding Monel 400 to stainless steel.
Step 3: Buttering the Stainless Steel Pipe
The buttering process involves applying a layer of filler material to the stainless steel pipe before the final weld is made. This layer acts as a transition zone between the stainless steel and the nickel alloy, reducing the risk of cracking and corrosion.
Buttering Procedure:
- Surface Preparation: The surface of the stainless steel pipe must be thoroughly cleaned to remove any contaminants, such as oil, grease, or oxide layers. This can be done using mechanical methods (e.g., grinding) or chemical cleaning.
- Preheating: Depending on the thickness of the materials and the specific alloys being welded, preheating may be required to reduce the risk of cracking. Preheating temperatures typically range from 100°C to 200°C.
- Buttering Pass: A layer of filler material (e.g., ERNiCrMo-3) is applied to the stainless steel pipe using a welding process such as GTAW (Gas Tungsten Arc Welding) or SMAW (Shielded Metal Arc Welding). The buttering layer should be thick enough to prevent dilution with the base metal during the final weld.
- Inspection: After the buttering layer is applied, it should be inspected for defects such as cracks, porosity, or incomplete fusion. Non-destructive testing (NDT) methods such as ultrasonic testing or radiographic testing may be used to ensure the quality of the buttering layer.
Step 4: Welding the Nickel Alloy to the Buttered Stainless Steel
Once the buttering layer has been applied to the stainless steel pipe, the final weld can be made between the nickel alloy pipe and the buttered stainless steel pipe.
Welding Procedure:
- Welding Process: The welding process used for joining the nickel alloy to the buttered stainless steel pipe can vary depending on the specific materials and application. Common welding processes include:
- GTAW (TIG Welding): Provides precise control over the weld and is commonly used for high-quality welds in critical applications.
- SMAW (Stick Welding): A versatile process that can be used for welding in various positions and environments.
- GMAW (MIG Welding): Suitable for faster welding speeds and thicker materials.
- Filler Material: The same filler material used for buttering (e.g., ERNiCrMo-3) should be used for the final weld to ensure compatibility between the nickel alloy and the buttered layer.
- Welding Parameters: The welding parameters, such as welding current, voltage, and travel speed, should be carefully controlled to prevent overheating and distortion. The following table provides typical welding parameters for GTAW and SMAW processes:
Welding Process | Filler Material | Current (A) | Voltage (V) | Travel Speed (mm/min) | Preheat Temperature (°C) | Interpass Temperature (°C) |
---|---|---|---|---|---|---|
GTAW (TIG) | ERNiCrMo-3 | 100-150 | 10-14 | 100-150 | 100-200 | 150-250 |
SMAW (Stick) | ERNiCrMo-3 | 80-120 | 20-24 | 80-120 | 100-200 | 150-250 |
GMAW (MIG) | ERNiCrMo-3 | 150-200 | 20-25 | 150-200 | 100-200 | 150-250 |
- Post-Weld Heat Treatment (PWHT): Depending on the materials and application, post-weld heat treatment may be required to relieve residual stresses and improve the mechanical properties of the weld. PWHT temperatures typically range from 600°C to 800°C, depending on the specific alloys being welded.
Step 5: Inspection and Testing
After the welding process is complete, the weld joint must be inspected and tested to ensure its quality and integrity. Common inspection methods include:
- Visual Inspection: The weld joint is visually inspected for surface defects such as cracks, porosity, or incomplete fusion.
- Non-Destructive Testing (NDT): Methods such as ultrasonic testing (UT), radiographic testing (RT), or dye penetrant testing (PT) can be used to detect internal defects in the weld joint.
- Mechanical Testing: Mechanical tests such as tensile testing, bend testing, or impact testing may be performed to evaluate the strength and toughness of the weld joint.
Challenges in Welding Nickel Alloys to Stainless Steel
Welding nickel alloys to stainless steel presents several challenges due to the differences in their chemical composition and physical properties. Some of the key challenges include:
1. Thermal Expansion Mismatch
Nickel alloys and stainless steels have different coefficients of thermal expansion, which can lead to thermal stresses during heating and cooling. These stresses can cause cracking in the weld joint, especially in thick-walled pipes or complex geometries.
2. Dilution
During welding, the base metals (nickel alloy and stainless steel) can mix with the filler material, leading to dilution. This can result in a weld with undesirable mechanical properties or corrosion resistance. The buttering layer helps to reduce dilution by creating a more compatible interface between the two dissimilar metals.
3. Corrosion
Welding dissimilar metals can create galvanic cells, leading to accelerated corrosion at the weld joint. The use of a compatible filler material (e.g., ERNiCrMo-3) and proper post-weld treatments can help to mitigate this issue.
4. Cracking
Cracking can occur during or after welding due to thermal stresses, dilution, or hydrogen embrittlement. Preheating, controlled welding parameters, and post-weld heat treatment can help to reduce the risk of cracking.
Table: Chemical Composition of Common Nickel Alloys and Stainless Steels
Material | Nickel (Ni) | Chromium (Cr) | Molybdenum (Mo) | Iron (Fe) | Copper (Cu) | Carbon (C) | Other Elements |
---|---|---|---|---|---|---|---|
Inconel 600 | 72 min | 14-17 | – | 6-10 | – | 0.15 max | Mn, Si, S |
Inconel 625 | 58 min | 20-23 | 8-10 | 5 max | – | 0.10 max | Nb, Mn, Si |
Monel 400 | 63 min | – | – | 2.5 max | 28-34 | 0.30 max | Mn, Si, S |
Hastelloy C-276 | 57 min | 14.5-16.5 | 15-17 | 4-7 | – | 0.01 max | W, Mn, Si, S |
304 Stainless Steel | 8-10.5 | 18-20 | – | Balance | – | 0.08 max | Mn, Si, P, S |
316 Stainless Steel | 10-14 | 16-18 | 2-3 | Balance | – | 0.08 max | Mn, Si, P, S |
321 Stainless Steel | 9-12 | 17-19 | – | Balance | – | 0.08 max | Ti, Mn, Si, P, S |
Duplex Stainless | 4.5-6.5 | 22-23 | 3-3.5 | Balance | – | 0.03 max | Mn, Si, P, S |
Conclusion
Welding nickel alloy steel pipes to stainless steel pipes using the buttering technique is a complex process that requires careful attention to material selection, filler material, welding parameters, and post-weld treatments. By applying a buttering layer of compatible filler material, the risk of cracking, corrosion, and dilution can be significantly reduced, resulting in a high-quality weld joint.
The success of the weld depends on proper surface preparation, preheating, controlled welding parameters, and thorough inspection and testing. By following the guidelines and best practices outlined in this guide, you can ensure a reliable and durable weld between nickel alloy and stainless steel pipes.
For more information or assistance with welding dissimilar metals, consult with a welding engineer or materials specialist who can provide expert guidance on the specific requirements of your project.