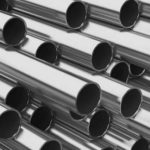
Incoloy 825 (UNS N08825) Steel Pipe
August 3, 2024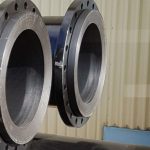
HDPE Inner Steel Pipe System for Drinking Water Pipelines
August 7, 2024Customer Case Study: 3PE Coated Pipe Installation and Construction by ABTERSteel
Introduction
ABTERSteel, a leading manufacturer and supplier of high-quality steel pipes, recently completed a significant project involving the installation and construction of 3PE coated pipes. This case study provides a detailed account of the project, highlighting the benefits of using 3PE coated pipes, the installation process, and the overall construction experience.
Project Overview
Client Background
Our client, a prominent oil and gas company, required a reliable and durable pipeline solution for transporting crude oil over a long distance. The project demanded a pipeline system that could withstand harsh environmental conditions, including soil corrosion and mechanical stress.
Project Scope
The project involved the supply and installation of 50 kilometers of 3PE coated pipes, ranging in diameter from 16 inches to 24 inches. The pipeline was to be installed in a remote area with challenging terrain, requiring meticulous planning and execution.
What is 3PE Coated Pipe?
Definition
3PE (Three-layer Polyethylene) coated pipes are steel pipes coated with three layers of polyethylene to provide superior corrosion resistance and mechanical protection. The three layers include:
- Fusion Bonded Epoxy (FBE) Layer: Provides excellent adhesion to the steel pipe and offers primary corrosion protection.
- Adhesive Layer: Binds the epoxy layer to the outer polyethylene layer, ensuring a strong bond.
- Polyethylene Layer: Offers mechanical protection and additional corrosion resistance.
Benefits
- Corrosion Resistance: The 3PE coating provides excellent protection against soil corrosion, extending the pipeline’s service life.
- Mechanical Protection: The polyethylene layer offers resistance to mechanical damage during transportation, handling, and installation.
- Cost-Effectiveness: The long service life and reduced maintenance costs make 3PE coated pipes a cost-effective solution for long-distance pipelines.
Installation Process
Pre-Installation Planning
Site Survey
Before the installation began, a comprehensive site survey was conducted to assess the terrain, soil conditions, and potential obstacles. This information was crucial for planning the pipeline route and ensuring a smooth installation process.
Material Preparation
The 3PE coated pipes were manufactured at ABTERSteel’s state-of-the-art facility, ensuring they met the highest quality standards. The pipes were then transported to the site, where they were inspected for any damage during transit.
Installation Steps
Trenching
The first step in the installation process was trenching. Excavators were used to dig trenches along the planned pipeline route. The depth and width of the trenches were carefully calculated to accommodate the pipes and provide adequate protection.
Pipe Laying
Once the trenches were prepared, the 3PE coated pipes were laid into the trenches. Special care was taken to avoid damaging the polyethylene coating during this process. The pipes were aligned and welded together using advanced welding techniques to ensure a secure and leak-free connection.
Backfilling
After the pipes were laid and welded, the trenches were backfilled with soil. The backfilling process was carried out in layers, with each layer being compacted to provide stability and support to the pipeline.
Testing and Inspection
Before commissioning the pipeline, a series of tests and inspections were conducted to ensure its integrity and performance. These included pressure testing, leak detection, and visual inspections of the welds and coatings.
Construction Experience
Challenges Faced
Remote Location
The remote location of the project site presented logistical challenges, including transportation of materials and equipment. ABTERSteel’s project management team worked closely with the client to coordinate the delivery of materials and ensure timely completion of the project.
Harsh Terrain
The challenging terrain required careful planning and execution to avoid damaging the pipes and ensure a smooth installation process. Specialized equipment and techniques were used to navigate the difficult terrain and complete the installation successfully.
Solutions Implemented
Advanced Equipment
ABTERSteel utilized advanced equipment and machinery to overcome the challenges posed by the remote location and harsh terrain. This included specialized trenching machines, pipe laying equipment, and welding tools.
Skilled Workforce
A team of skilled and experienced professionals was deployed to the project site. Their expertise and dedication were instrumental in overcoming the challenges and ensuring the successful completion of the project.
Project Outcome
The installation and construction of the 3PE coated pipeline were completed on time and within budget. The client was highly satisfied with the quality of the materials and the professionalism of the ABTERSteel team. The pipeline is now operational, providing a reliable and durable solution for transporting crude oil.
Conclusion
The successful completion of the 3PE coated pipe installation and construction project by ABTERSteel demonstrates our commitment to delivering high-quality pipeline solutions. The project’s success can be attributed to meticulous planning, advanced equipment, and a skilled workforce. The 3PE coated pipes provided the necessary corrosion resistance and mechanical protection, ensuring a long service life and cost-effective solution for the client.
FAQ
1. What are the main benefits of 3PE coated pipes?
The main benefits include excellent corrosion resistance, mechanical protection, and cost-effectiveness due to their long service life and reduced maintenance costs.
2. What is the composition of the 3PE coating?
The 3PE coating consists of three layers: a fusion bonded epoxy (FBE) layer, an adhesive layer, and a polyethylene layer.
3. What challenges were faced during the installation of the 3PE coated pipes?
Challenges included the remote location of the project site, harsh terrain, and logistical issues related to the transportation of materials and equipment.
4. How were the challenges overcome during the project?
The challenges were overcome by using advanced equipment, deploying a skilled workforce, and meticulous planning and coordination with the client.
5. What was the outcome of the project?
The project was completed on time and within budget, with the client highly satisfied with the quality of the materials and the professionalism of the ABTERSteel team. The pipeline is now operational, providing a reliable and durable solution for transporting crude oil.