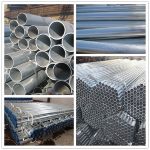
Galvanized Steel Pipe: The Ideal Choice for Construction Scaffold Galvanized Pipe , STK400 STK500
February 3, 2024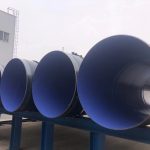
AWWA C210 Epoxy Coating Pipeline and Fittings for Water
February 12, 2024Introduction
In the world of pipeline infrastructure, protecting the integrity of pipelines is of utmost importance. One effective method of safeguarding pipelines against corrosion and other forms of damage is through the application of liquid epoxy coating. In this article, we will explore the benefits of AWWA C210 liquid epoxy coating for pipeline protection, highlighting its effectiveness and advantages over other coating methods.
Understanding AWWA C210 Liquid Epoxy Coating
AWWA C210 is a standard set by the American Water Works Association (AWWA) that outlines the requirements for liquid epoxy coating systems for the interior and exterior of steel water pipelines. This coating system is designed to provide a durable and protective barrier against corrosion, chemical attack, and abrasion, ensuring the longevity and reliability of the pipelines.
Standard and Certifications
SSAW steel pipes adhere to various industry standards and certifications to ensure their quality and performance. Some of the commonly followed standards include:
- AWWA C200: Standard for steel water pipe
- AWWA C203: Standard for coal-tar protective coatings and linings for steel water pipelines
- AWWA C205: Standard for cement-mortar protective lining and coating for steel water pipe
- AWWA C208: Standard for dimensions for fabricated steel water pipe fittings
- AWWA C210: Standard for liquid-epoxy coating systems for the interior and exterior of steel water pipelines
- AWWA C213: Standard for fusion-bonded epoxy coating for the interior and exterior of steel water pipelines
In addition to these standards, SSAW steel pipes may also hold certifications such as EN10217 and EN10219, which further validate their quality and compliance with European standards.
Specifications
SSAW steel pipes come in a range of specifications to meet different project requirements. The key specifications include:
- Out Diameter: The outer diameter of SSAW steel pipes typically ranges from 219.1mm to 3048mm, allowing for versatility in application.
- Wall Thickness: The wall thickness of SSAW steel pipes ranges from 5.0mm to 25.4mm, providing the necessary strength and durability for low pressure liquid delivery.
- Length: SSAW steel pipes can be manufactured in lengths of up to 70m, allowing for seamless installation over long distances.
Steel Grade
SSAW steel pipes are available in various steel grades to meet specific mechanical and chemical requirements. Some commonly used steel grades include:
- API 5L: GR A, GR B, X42, X46, X56, X60, X65, X70
- ASTM A252: GR 1, GR 2, GR 3
- ASTM A53: GR A, GR B, GR C, GR D
- BS 4360: Grade 43, Grade 50
- EN: S275, S275JR, S355JRH, S355J2H
The selection of the appropriate steel grade depends on factors such as the intended application, environmental conditions, and required mechanical properties.
Surface Treatment
To enhance the performance and longevity of SSAW steel pipes, various surface treatments can be applied. These treatments include:
- Fusion Bond Epoxy Coating: Provides excellent corrosion resistance and adhesion to the steel surface.
- Coal Tar Epoxy: Offers high chemical resistance and protection against corrosion.
- 3PE (Three-Layer Polyethylene): Provides a triple-layer protective coating, combining the benefits of fusion bond epoxy, adhesive, and polyethylene.
- Vanish Coating: Offers additional protection against corrosion and abrasion.
- Bitumen Coating: Provides a waterproof barrier and protection against external elements.
- Black Oil Coating: A basic coating that provides temporary protection during storage and transportation.
The choice of surface treatment depends on the specific requirements of the project and the environmental conditions the SSAW steel pipes will be exposed to.
Testing
SSAW steel pipes undergo various tests to ensure their quality and compliance with industry standards. These tests include:
- Chemical Component Analysis: Determines the chemical composition of the steel, ensuring it meets the specified requirements.
- Mechanical Properties: Measures the ultimate tensile strength, yield strength, and elongation of the steel, ensuring it meets the required mechanical properties.
- Technical Properties: Includes tests such as flattening, bending, blow, and impact tests to assess the structural integrity and performance of the SSAW steel pipes.
- Exterior Size Inspection: Verifies the dimensional accuracy and consistency of the pipes.
- Hydrostatic Test: Checks the integrity of the SSAW steel pipes by subjecting them to water pressure to ensure they can withstand the intended operating conditions.
- X-ray Test: Utilizes X-ray imaging to detect any internal defects or inconsistencies in the welds of the SSAW steel pipes.
These tests ensure that the SSAW steel pipes meet the necessary quality standards and are suitable for their intended application.
Advantages of AWWA C210 Liquid Epoxy Coating
1. Corrosion Resistance
One of the primary benefits of AWWA C210 liquid epoxy coating is its exceptional corrosion resistance. The epoxy coating forms a protective barrier on the surface of the pipeline, preventing contact between the steel and corrosive elements in the environment. This barrier effectively inhibits the formation of rust and corrosion, extending the lifespan of the pipeline.
2. Chemical Resistance
In addition to corrosion resistance, AWWA C210 liquid epoxy coating also offers excellent chemical resistance. The coating is resistant to a wide range of chemicals, including acids, alkalis, and solvents, making it suitable for pipelines that transport corrosive substances. This chemical resistance ensures that the pipeline remains intact and unaffected by the substances it carries.
3. Abrasion Resistance
Pipelines are often subjected to abrasive forces, such as the flow of solid particles or the movement of equipment. AWWA C210 liquid epoxy coating provides a high level of abrasion resistance, protecting the pipeline from wear and tear. This resistance ensures that the coating remains intact, preserving the structural integrity of the pipeline.
4. Flexibility and Adhesion
AWWA C210 liquid epoxy coating exhibits excellent flexibility and adhesion properties. The coating adheres tightly to the surface of the pipeline, forming a strong bond that is resistant to peeling, cracking, or delamination. This ensures that the coating remains intact even under varying temperature conditions and mechanical stress.
5. Easy Application and Maintenance
Another advantage of AWWA C210 liquid epoxy coating is its ease of application and maintenance. The coating can be applied using various methods, including spray, brush, or roller, allowing for flexibility in different project scenarios. Additionally, the coating requires minimal maintenance once applied, reducing the need for frequent inspections and repairs.
AWWA C210 liquid epoxy coating offers numerous benefits for pipeline protection. Its corrosion resistance, chemical resistance, abrasion resistance, flexibility, and adhesion properties make it an ideal choice for safeguarding pipelines against damage. With its easy application and low maintenance requirements, AWWA C210 liquid epoxy coating provides a cost-effective solution for ensuring the longevity and reliability of pipelines. By utilizing this coating system, pipeline operators can have peace of mind knowing that their infrastructure is well-protected and can withstand the challenges of the environment.
Introduction
Liquid epoxy coating is a versatile and effective solution for protecting pipelines against corrosion, abrasion, and chemical attack. In this article, we will delve into the specifications and technical parameters of liquid epoxy coating, exploring its different types and applications. Whether it’s external or internal coating, field joint coating, or density and price considerations, liquid epoxy coating provides a reliable and durable protective layer for pipelines.
What is Liquid Epoxy Pipeline Coating?
Liquid epoxy pipeline coating refers to the application of a liquid epoxy paint or resin onto the surface of a pipeline to create a protective layer. This coating acts as a barrier, preventing the pipeline from coming into direct contact with corrosive substances, chemicals, or abrasive materials. It is commonly used in the oil and gas industry, water distribution systems, and other industries where pipeline integrity is crucial.
External Liquid Applied Epoxy Coating
External liquid applied epoxy coating is specifically designed to protect the exterior surface of pipelines. It provides excellent corrosion resistance and weatherability, ensuring that the pipeline remains intact even in harsh environmental conditions. This type of coating is typically applied using spray equipment, ensuring a uniform and consistent layer of protection.
Internal Liquid Epoxy Coating
Internal liquid epoxy coating is applied to the interior surface of pipelines to safeguard against corrosion and chemical attack. It is commonly used in water distribution systems, where the coating acts as a barrier between the water and the pipeline material. Internal liquid epoxy coating is typically applied using a spray or brush method, ensuring complete coverage and adhesion to the pipeline surface.
Liquid Epoxy Coating 323
Liquid epoxy coating 323 is a specific type of epoxy coating that meets the requirements of various industry standards. It offers exceptional corrosion resistance, chemical resistance, and adhesion properties. Liquid epoxy coating 323 is commonly used for pipeline applications, providing long-term protection and durability.
Density of Liquid Epoxy Paint
The density of liquid epoxy paint can vary depending on the specific product and formulation. However, on average, the density of liquid epoxy paint ranges from 1.1 to 1.5 grams per cubic centimeter (g/cm³). It is important to consider the density of the coating during application to ensure proper coverage and thickness.
Price List of Liquid Epoxy Coating
The price of liquid epoxy coating can vary based on several factors, including the type of coating, the quantity required, and the supplier. It is recommended to obtain quotes from different suppliers to compare prices and ensure the best value for your specific project. Additionally, it is important to consider the long-term benefits and cost savings that come with using a high-quality liquid epoxy coating to protect your pipelines.
Technical Parameters of Liquid Epoxy Field Joint Coating
Liquid epoxy field joint coating is specifically designed for coating the joints and welds of pipelines. It provides a seamless and durable protective layer, ensuring that the vulnerable areas of the pipeline are well-protected. The technical parameters of liquid epoxy field joint coating can vary depending on the specific product and manufacturer. It is essential to consult the manufacturer’s technical data sheet for detailed information on parameters such as curing time, temperature resistance, and application guidelines.
Conclusion
Liquid epoxy coating is a reliable and effective solution for protecting pipelines against corrosion, abrasion, and chemical attack. Whether it’s external or internal coating, field joint coating, or considering density and price, liquid epoxy coating offers excellent performance and durability. By adhering to the specified technical parameters and utilizing high-quality products, pipeline operators can ensure the long-term integrity and reliability of their infrastructure. Invest in liquid epoxy coating and provide your pipelines with the protection they deserve.