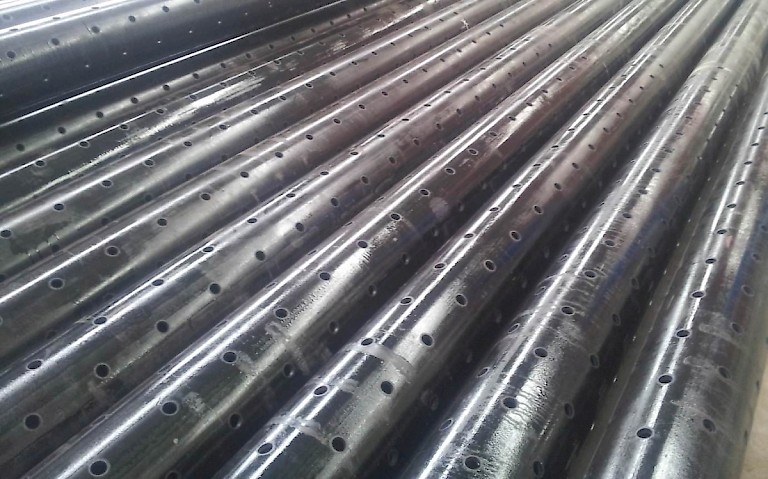
What is the difference between casing pipe and well screen pipe?
January 16, 2018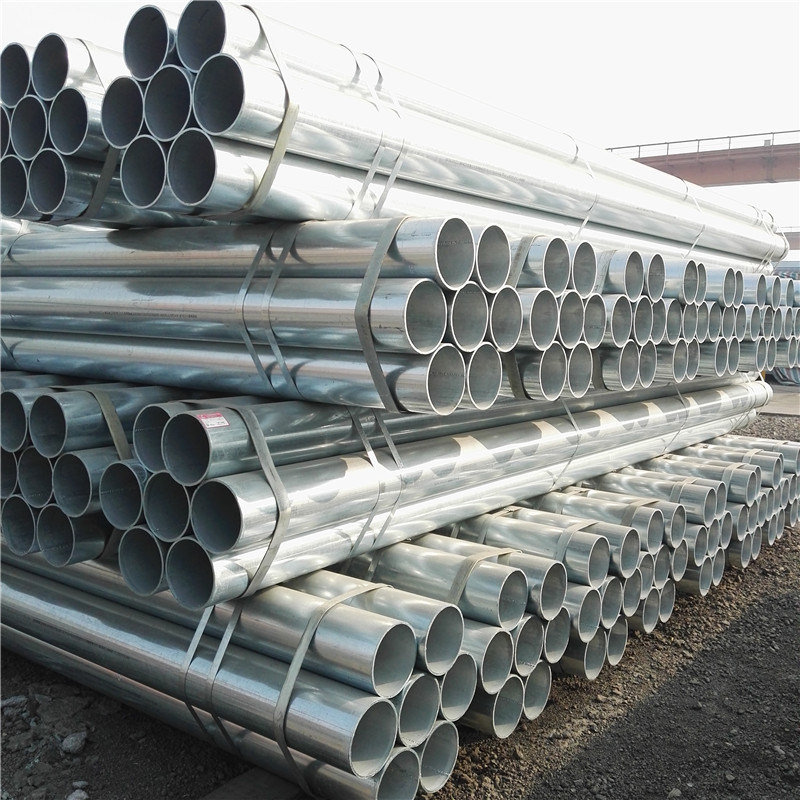
ASTM A53 Black & Galvanized Pipe, 1/8″ – 26″
January 26, 2018Spiral steel pipe& Welded Pipe Manufacturing Process
Spiral steel pipe & Welded Pipe is the primary manufacturing process for steel thicknesses that exceed spiral mill capabilities (greater than 1”).
Electric resistance weld (ERW) pipe Definition : is normally produced in sizes from 2-³∕₈” OD thru 24” OD.ERW is produced from individual sheets or continuously from rolls of skelp. There are two important differences in the production of ERW pipe versus CW pipe. ERW pipe is cold formed into a cylindrical shape rather than hot formed. An electric current rather than a flame is used to heat the edges of the strip for the fusion weld. Revolving copper discs serve as electrodes and raise the temperature to approximately 2600°F for effective welding. As in CW pipe, no extraneous metal is added; in fact, due to the extreme pressure of the rolls, steel is extruded on both the inside and outside of the pipe at the point of the weld. This is called flash and is removed on the OD by stationary
cutters while still white-hot for A252 grades, and both the ID and OD for other grades. As in CW production, ERW pipe is subject to numerous finishing operations. ERW pipe is primarily used as API line pipe for the transmission of gas and oil. It is also used for the transmission of water, under AWWA specifications, as piling and slurry pipe and in mechanical applications.
Spiral weld pipe Definition : as the name implies, is a steel pipe that has a seam running its entire length in a spiral form. In the past, due to the method of manufacture, spiral welded pipe was relegated to low pressure and structural applications. With the development of the submerged arc welding process, the production of large
hot rolled coils of sufficient width and the development of dependable non-destructive testing methods, it is now possible to produce spiral weld pipe for high-pressure service.
Present spiral weld mills consist of a de-coiling device (in the case of strip base material), a strip connecting welder, straightening rollers, edge preparation tools (shearing and trimming), prebending devices, a bending and cage forming system, an internal welder, an external welder (both submerged arc), ultrasonic testing
apparatus and cutting devices.
The material passes through all these production stages continuously. The angle between the flat strip being fed into the machine and the finished pipe leaving the machine controls the pipe diameter in ratio to strip width and the angle of the weld in the pipe.
Because of the method of manufacture, a wide variety of diameters can be produced. The diameter tolerance is small, particularly with regard to ovality; and the pipe, due to its axial symmetry, has an inherent straightness.
The length range is infinite and is controlled only by the economics of transportation.
Spiral weld pipe is used for piling and structural applications, as well as for dredging, slurry, water and other pipelines.
Spiral weld pipe is produced in accordance with the dimensional and tolerance requirements of various ASTM, AWWA and API specifications.
ERW Pipe Manufacturing Process:
1 | 2 | 3 | 4 |
PLATE The raw material – pieces of flat steel plate – is received into our manufacturing plant. |
CUTTING A single flat sheet of steel plate is cut on a burning table, using plasma or cutting gases. This plate is cut according to the equired width and length for the cylinder it will be rolled into. |
BEVELING After the plate is cut, it is transferred to the beveling station where different bevel angles are cut into the plate edge for welding. |
BENDING After beveling, the plate is transferred to the bending rolls. Skyline Steel uses a 4-roll system to produce a true cylinder, also referred to as a can. |
5 | 6 | 7 | 8 |
WELDING The can is then staged for longitudinal welding (Long Seam). During this process, the seam between the two plates is welded on both the inside and outside, using a tandem wire submerged arc welding process. |
QUALITY CONTROL Once the welding is complete, the can is visually inspected by Quality Control (QC) and, if required, Ultrasonic (UT) testing is performed to ensure the weld is defect-free. |
CIRCUMFERENTIAL WELDING During this last step of the manufacturing process, cans are fit together and the pipe is manufactured using the submerged arc process, according to customer requirements for specific lengths. |
FINISHED PIPE The finished pipe, produced according to the customer’s specifications, is then removed and ready for delivery. |
Certifications
All weld systems are qualified and certified to AWS D1.1. Our mills are quality
certified by the Steel Plate Fabricators Association (SPFA) and audited by Lloyd’s Registry Quality Assurance. Additionally, each plant is staffed with Certified
Weld Inspectors to assure a quality weld in every pipe.
Spiral weld Pipe Manufacturing Process
The spiral weld manufacturing process is one of the most cost effective ways to produce steel pipe. The mill setup offers a varying degree of flexibility, allowing for a wide range of
pipe diameters and wall thicknesses to be produced. As a result, Skyline Steel is able to offer spiral weld products to many structural and non-structural markets at the most economical cost.
Spiral
weld Pipe is manufactured from steel coil.
1 | 2 | 3 | 4 | ||
UNCOILING Upon receipt of the coil, it is placed on a horizontal un- coiler mandrel and fed into the straightener. |
FLATTENING The strip of coil is introduced into the flattener through a roll stand and the coil set is removed. 1 |
OINING OF THE COIL ENDS As the coil continues to move through the straightener, the leading and trailing edges of the strip are trimmed in preparation for butt welding – coil to coil. |
EDGE MILLING The edges of the coil are trimmed in preparation for welding. |
||
5 | 6 | 7 | 8 | ||
PIPE SPIRALING The strip of coil enters the three roll apparatus composed of lead, buttress and mandrel roll sets. At this stage, the coil starts to form the spiral shape that will then become pipe. |
SINGLE & TANDEM PIPE WELDING The welding system welds the pipe, both inside and outside, using a submerged arc welding system. |
PIPE CUT-OFF Once the pipe reaches the desired length, the cut-off machine is engaged. Traveling with the pipe, a plasma torch provides the cut-off of the finished pipe. |
PIPE WEIGHT lbs/ft (kg/m) APPROXIMATE VALUES |
||||||||||||||
Outside Diameter (D〇) in (mm) |
Wall Thickness (t) in (mm) | |||||||||||||
0.250 6.35 |
0.312 7.92 |
0.375 9.52 |
0.438 11.13 |
0.500 12.70 |
0.562 14.27 |
0.625 15.87 |
0.688 17.48 |
0.750 19.05 |
0.875 22.22 |
1.000 25.40 |
1.250 31.75 |
1.375 34.92 |
1.50 – 2.25 38.10 – 57.15 | |
24 609.6 |
63.47 94.45 |
79.01 117.58 |
94.71 140.94 |
110.32 164.17 |
125.61 186.93 |
141.05 209.91 |
156.17 232.41 |
171.45 255.15 |
186.41 277.41 |
|||||
30 762.0 |
79.51 118.32 |
99.02 147.36 |
118.76 176.73 |
138.42 205.99 |
157.68 234.65 |
176.86 263.20 |
196.26 292.07 |
215.58 320.82 |
234.51 348.99 |
272.43 405.42 |
310.01 461.35 |
|||
36 914.4 |
95.54 142.18 |
119.03 177.14 |
142.81 212.53 |
166.51 247.79 |
189.75 282.38 |
212.90 316.83 |
236.35 351.73 |
259.71 386.49 |
282.62 420.59 |
328.55 488.94 |
374.15 556.80 |
464.35 691.03 |
||
42 1067 |
111.58 166.05 |
139.04 206.91 |
166.86 248.32 |
194.60 289.60 |
221.82 330.11 |
248.95 370.48 |
276.44 411.39 |
303.84 452.16 |
330.72 492.17 |
384.67 572.45 |
438.29 652.25 |
544.52 810.34 |
597.14 888.64 |
Max. wall thickness of 1.50″ (38.1mm). Please call for weight. |
48 1219 |
127.61 189.90 |
159.05 236.69 |
190.92 284.12 |
222.70 331.41 |
253.89 377.83 |
285.00 424.13 |
316.52 471.03 |
347.97 517.84 |
378.83 563.76 |
440.80 655.98 |
502.43 747.70 |
624.70 929.66 |
685.33 1019.89 |
|
54 1372 |
143.65 213.78 |
179.06 266.47 |
214.97 319.91 |
250.79 373.22 |
285.96 425.56 |
321.04 477.76 |
356.61 530.70 |
392.09 583.50 |
426.93 635.34 |
496.92 739.50 |
566.57 843.15 |
704.87 1048.96 |
773.52 1151.13 |
|
60 1524 |
159.68 237.63 |
199.08 296.26 |
239.02 355.70 |
278.88 415.02 |
318.03 473.28 |
357.09 531.41 |
396.70 590.36 |
436.22 649.17 |
475.04 706.94 |
553.04 823.02 |
630.71 938.60 |
785.05 1168.29 |
861.71 1282.37 |
Max. wall thickness of 1.625″ (41.3mm). Please call for weight. |
66 1676 |
175.72 261.50 |
219.09 326.04 |
263.07 391.49 |
306.98 456.84 |
350.10 521.01 |
393.14 585.06 |
436.79 650.02 |
480.35 714.84 |
523.14 778.52 |
609.16 906.53 |
694.85 1034.05 |
865.22 1287.59 |
949.91 1413.62 |
|
72 1829 |
191.75 285.36 |
239.10 355.82 |
287.13 427.30 |
335.07 498.64 |
382.17 568.73 |
429.18 638.69 |
476.87 709.66 |
524.48 780.51 |
571.25 850.12 |
665.29 990.06 |
758.99 1129.50 |
945.40 1406.91 |
1038.10 1544.87 |
Max. wall thickness of 1.75″ (44.4mm). Please call for weight. |
78 1981 |
207.79 309.23 |
259.11 385.60 |
311.18 463.09 |
363.16 540.44 |
414.24 616.46 |
465.23 692.34 |
516.96 769.32 |
568.61 846.19 |
619.35 921.70 |
721.41 1073.58 |
823.13 1224.95 |
1025.57 1526.22 |
1126.29 1676.11 |
|
84 2134 |
223.82 333.08 |
279.12 415.38 |
335.23 498.88 |
391.26 582.26 |
446.31 664.18 |
501.28 745.99 |
557.05 828.98 |
612.74 911.86 |
667.46 993.29 |
777.53 1157.09 |
887.27 1320.41 |
1105.75 1645.54 |
1214.48 1807.35 |
|
90 2286 |
239.86 356.95 |
299.13 445.16 |
359.28 534.67 |
419.35 624.06 |
478.38 711.91 |
537.32 799.62 |
597.14 888.64 |
656.86 977.52 |
715.56 1064.87 |
833.65 1240.61 |
951.41 1415.86 |
1185.92 1764.85 |
1302.68 1938.61 |
|
96 2438 |
255.89 380.81 |
319.15 474.95 |
383.34 570.47 |
447.44 665.87 |
510.45 759.63 |
573.37 853.27 |
637.22 948.29 |
700.99 1043.19 |
763.67 1136.47 |
889.78 1324.14 |
1015.55 1511.31 |
1266.10 1884.17 |
1390.87 2069.85 |
Max. wall thickness of 2.00″ (50.8mm). Please call for weight. |
102 2591 |
271.93 404.68 |
339.16 504.73 |
407.39 606.26 |
475.54 707.68 |
542.52 807.36 |
609.42 906.92 |
677.31 1007.95 |
745.12 1108.86 |
811.77 1208.05 |
945.90 1407.66 |
1079.69 1606.76 |
1346.27 2003.47 |
1479.06 2201.09 |
|
108 2743 |
287.96 428.53 |
359.17 534.50 |
431.44 642.05 |
503.63 749.49 |
574.59 855.09 |
645.46 960.55 |
717.40 1067.61 |
789.25 1174.54 |
859.88 1279.65 |
1002.02 1491.17 |
1143.83 1702.21 |
1426.45 2122.80 |
1567.25 2332.33 |
|
114 2896 |
304.00 452.40 |
379.18 564.28 |
455.49 677.85 |
531.72 791.29 |
606.66 902.81 |
681.51 1014.20 |
757.49 1127.27 |
833.38 1240.21 |
907.98 1351.23 |
1210.48 1801.40 |
1207.97 1797.66 |
1506.62 2242.10 |
1655.45 2463.59 |
|
120 3048 |
320.03 476.26 |
399.19 594.06 |
479.55 713.65 |
559.82 833.11 |
638.73 950.54 |
717.56 1067.85 |
797.57 1186.92 |
877.51 1305.88 |
956.09 1422.82 |
1274.62 1896.85 |
1272.11 1893.11 |
1586.80 2361.42 |
1743.64 2594.83 |
Max. wall thickness of 2.25″ (57.1mm). Please call for weight. |
126 3200 |
419.20 623.84 |
503.60 749.44 |
587.91 874.91 |
670.80 998.26 |
753.60 1121.48 |
837.66 1246.58 |
921.63 1371.54 |
1004.19 1494.40 |
1338.76 1992.30 |
1336.25 1988.56 |
1666.97 2480.73 |
1831.83 2726.07 |
||
132 3353 |
439.22 653.63 |
527.65 785.23 |
616.00 916.71 |
702.87 1045.99 |
789.65 1175.13 |
877.75 1306.24 |
965.76 1437.21 |
1052.30 1566.00 |
1402.90 2087.75 |
1400.39 2084.01 |
1747.15 2600.05 |
1920.02 2857.31 |
||
138 3505 |
551.70 821.02 |
644.10 958.53 |
734.94 1093.71 |
825.70 1228.78 |
917.84 1365.90 |
1009.89 1502.88 |
1100.40 1637.58 |
1467.07 2183.25 |
1464.53 2179.47 |
1827.32 2719.36 |
2008.22 2988.57 |
|||
144 3657.6 |
575.76 856.83 |
672.19 1000.33 |
767.01 1141.44 |
861.74 1282.41 |
957.92 1425.54 |
1054.02 1568.56 |
1148.51 1709.17 |
1531.18 2278.65 |
1528.67 2274.92 |
1907.50 2838.68 |
2096.41 3119.81 |
|||
150 3810 |
599.81 892.62 |
700.28 1042.13 |
799.08 1189.16 |
897.79 1336.06 |
998.01 1485.21 |
1098.15 1634.23 |
1196.61 1780.76 |
1595.32 2374.10 |
1592.81 2370.37 |
1987.67 2957.98 |
2184.60 3251.05 |
|||
156 3962 |
623.86 928.41 |
728.38 1083.95 |
831.15 1236.89 |
933.84 1389.71 |
1038.10 1544.87 |
1142.28 1699.90 |
1244.72 1852.35 |
1659.46 2469.55 |
1656.95 2465.82 |
2067.85 3077.31 |
2272.79 3382.29 |
|||
162 4115 |
756.47 1125.75 |
863.22 1284.62 |
969.88 1443.34 |
1078.19 1604.53 |
1186.40 1765.56 |
1292.82 1923.93 |
1723.82 2565.33 |
1721.09 2561.27 |
2148.02 3196.61 |
2360.99 3513.55 |
||||
168 4267 |
784.56 1167.56 |
895.29 1332.34 |
1005.93 1496.99 |
1118.27 1664.17 |
1230.53 1831.23 |
1340.93 1995.53 |
1787.74 2660.46 |
1785.23 2656.72 |
2228.20 3315.93 |
2449.18 3644.79 |
||||
169-204 4293 – 5182 | Please call for weight. |
Qualifications
• American Welding Society (AWS)
• American Society of Mechanical
Engineers (ASME)
• Pre-qualified
• AWS Section 3
• Qualified by Test
• AWS Section 4 / ASME Section IX
• AWS Section 4 WPS – Weld
Procedure Specification
• AWS Section 4 PQR -Procedure
Qualification Test Record
• Weld Quality Control Plan (WQCP)
• Steel Plate Fabricators Association
(SPFA) Quality Program
Quality Assurance
Non-destructive Testing (NDT)
• Visual Inspection (VI)
• Ultrasonic Testing (UT)
• Radiographic Testing / X-ray (RT)
• Magnetic Particle Testing
(Mag. Testing)
• Dye Penetration Testing
• Macro Etch Testing
• Hydrostatic Testing
• Destructive Testing
• Tensile Strength Test: Base
Metal/Across the Weld
• Bend Test: Root, Face, Side
• Charpy Impact Test (CVN): Base
Metal, Weld Metal, Heat Affected
Zone (HAZ)
• Custom Tests: Hoop Stresses, etc.
• Third-party Inspection
• UT, RT, VI, Etch and Weld
Observations
• Procedure QA/QC Review