
SEAMLESS & WELDED STEEL PIPE SUBSTITUTE MATERIAL FOR ASTM STANDARD SPECIFICATION – JIS, BS, DIN
November 11, 2023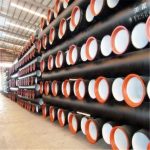
Ductile Iron pipe vs Galvanized Steel Pipe for Water Transmission Systems – A Compa rative Study
November 20, 2023Pipe Fittings Manufacturing Processes
Several manufacturing processes are employed to produce pipe fittings such as elbows, tees, and reducers.
Pipe fittings are typically fabricated from seamless pipes and welded pipes that include filler material. However, ERW (Electric Resistance Welded) and EFW (Electric Fusion Welded) pipes are not suitable for creating fittings. For the production of large-diameter fittings, plates are commonly used.
Introduction
Pipe fittings are integral components in plumbing, mechanical, and industrial applications, used to connect sections of pipe or tube. Manufacturing these fittings involves various methods, each suitable for different types of fittings such as elbows, tees, reducers, caps, and stub ends. This article explores these diverse manufacturing processes.
Hot Forming or Extrusion Method
The hot forming or extrusion process is a versatile manufacturing method, often used to create a variety of pipe fittings.
Overview
The extrusion process begins with heating a billet (a solid, cylindrical block of metal) until it’s pliable. The heated billet is then forced through a shaped die, a tool used to cut or shape material using a press.
Process
As the billet is pushed through the die, it begins to take the shape of the die’s opening, forming a lengthy, straight pipe. Once fully through the die, the extruded metal is cooled and hardened, retaining its new form.
Applications
The extrusion method is especially useful for manufacturing long, straight pipe fittings. It is also used for creating complex profiles for various industrial applications, including the production of elbows and tees.
Hydraulic Bulge Method – Cold Forming
The hydraulic bulge method, a cold forming process, is another common technique used in the manufacturing of pipe fittings.
Overview
In the hydraulic bulge method, a tube is placed and sealed within a die. High-pressure hydraulic fluid is then introduced into the tube, causing it to expand and adapt to the shape of the die.
Process
The pressure applied by the hydraulic fluid causes the metal tube to “bulge” outwards, matching the contours of the die. Once the hydraulic pressure is released, the now-expanded tube retains its new form.
Applications
The hydraulic bulge method is ideal for creating complex shapes or bends in pipe fittings, such as tees and reducers. It’s also used for manufacturing fittings that need to withstand high pressure, as the process results in a seamless and robust fitting.
The article would continue with detailed sections on:
- UO or Single Weld Seam Method
- Monaka or Double Weld Seam Method
- Deep Drawing Method for Caps
- Flare Method for Stub Ends
- UO or Single Weld Seam Method: This method is named after the process it involves: bending a flat plate into a U shape and then further bending it into an O shape (hence “UO”). The plate’s edges are then welded together to create a single seam. This method is often used to manufacture seamless pipe fittings, which are preferred in certain applications for their smooth inner surface and greater strength.
- Monaka or Double Weld Seam Method: The Monaka method also involves forming a flat plate, but in this case, the plate is shaped into a half-pipe. Two of these half-pipes are welded together to create a pipe fitting with two weld seams. This method is especially useful for larger pipe fittings, where a single weld seam might not provide sufficient strength.
- Deep Drawing Method for Caps: Deep drawing is a method used to manufacture pipe caps and similar end pieces. It involves radially drawing a metal blank into a forming die using a mechanical punch. This process is a type of shape transformation with material retention, resulting in a seamless, highly robust fitting.
- Flare Method for Stub Ends: The flare method is used to produce stub ends, a type of fitting used to join pipes together. It involves flaring or expanding the end of a pipe or tube. The flared end of the pipe is slipped over the end of the smaller pipe, and the two are then welded together, allowing for the connection of two pipes of different diameters.