
Black and Galvanized Steel Pipe For Water Transmission & Scaffolding
December 30, 2018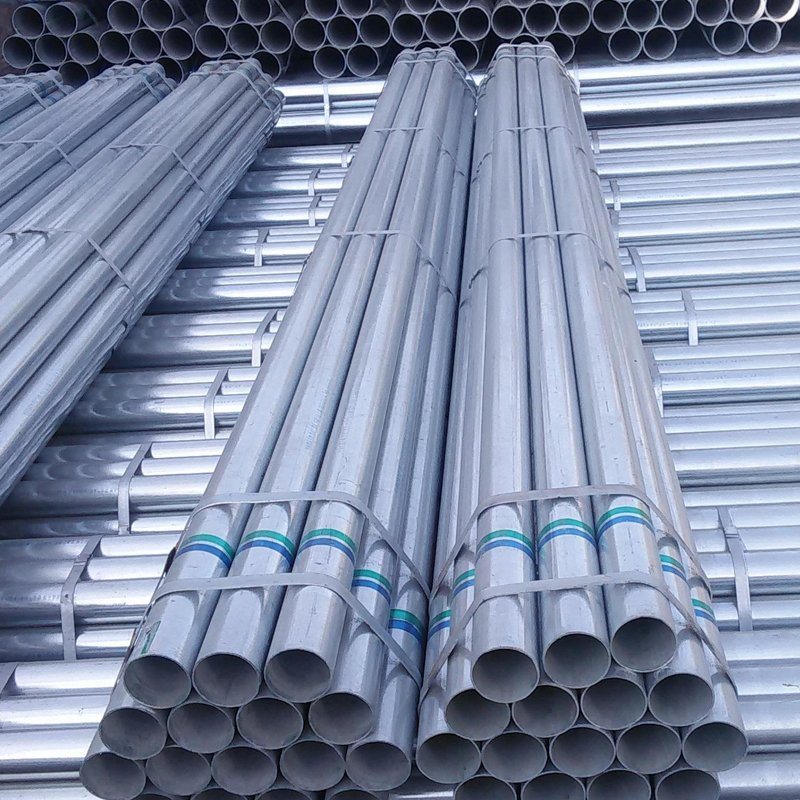
Properties of Galvanized Steel Pipe Welds
January 4, 2019Why not galvanizing after welding
Why not avoid the whole problem of welding galvanized steel pipe sheets after galvanizing? After all, steel products are always galvanized after manufacture, because there has been no practical way to restore the galvanizing effect after welding.
Zinc plating after manufacture is still conventional, but must be done with great care. The manufacturing must be cleaned in acid, the acid must be neutralized, and then made into a liquid zinc can that must be immersed in excess of 900 °F. People must be very careful to make it dry when it is put into zinc, because any trapped water will flash into steam, and zinc is everywhere. It must also be noted that zinc can easily flow into and out of any corners and gaps to achieve complete coverage; this is particularly difficult if the manufacture is made of tubes, since the tubes must be open at both ends to allow the zinc to flow properly. In addition to the simplest manufacturing, achieving uniform coverage is very difficult. Finally, the manufactured product must be able to fit into a molten zinc can – this is a problem with large structures.
Sheets, sheets, wires, structural shapes, especially tubing, are easily galvanized before they are made because they are very simple in shape – no corners or gaps, no hidden cavities, no water trapped.
Ordinary hot dip galvanizing, rather than “online” galvanized products, present particular problems during welding, primarily due to coating non-uniformity. Edges and corners – usually where welding is taking place – usually have very thick heavy zinc deposits, which may interfere more than the evenly applied weld of zinc. In addition, hot dip products typically have a rough Finshes that does not perform topcoating well, and the top coat, especially the powder topcoat, must be completed within 48 hours to avoid white rust formation difficulties.
1) galvanized steel pipe can be welded using the same arc welding processes that are being used for fabrication today.
2) galvanized steel pipe can be arc welded safely with little increase in cost or welder discomfort.
3) Corrosion resistance at welds can be effectively restored by application of paint coatings which are high in elemental zinc or by thermal spraying zinc over the weld areas.
4) Galvanizing simple shapes can be controlled better than psot-fabrication galvanizing, resulting in smoother surfaces and a more uniform top coating appearance.
Restoring Corrosion Resistance
The heat from welding vaporizes the protective zinc coating near the weld. Even though the remaining zinc continues to provide some protection to the zinc-free areas, the appearance is poor, and the zinc-free areas will rust when exposed to the environment. Paints which are high in elemental zinc (i.e., “Zinc-rich”), properly applied, will effectively restore full corrosion protection to the weld areas. These paints are available in either spray cans or in containers suitable for brush or spray application. This paint can be applied to the weld after sand blasting or wire brushing to remove all welding slag followed by wiping the weld clean with a rag. Thermal- sprayed zinc is also effective in restoring corrosion resistance, but the surface has to be sufficiently roughened, usually by sand blasting or coarse abrasive conditioning to enable thermal- sprayed zinc to stick properly.