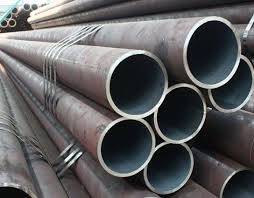
Construction scaffolding steel pipe specification table
February 26, 2022Coupling standards and requirements for oil casing
March 8, 202210.4 Tensile test
10.4.1 Stress release temperature
For the purpose of tensile test frequency requirements, stress-relief tempered tubes are considered to have not been “heat-treated” when the stress-relief temperature is 56°C (1000°F) below the final temper temperature.
10.4.2 Furnace—Controlled Tensile Test—Group 1, 2, 3
For each heat of steel produced in accordance with this standard, the manufacturer shall conduct a tensile test as a control test for each heat of steel. For electric welded pipes, this controlled tensile test may be selected by the manufacturer, or be carried out on the steel billet or on finished tubes.
A furnace-controlled tensile test on a tube may also be used as a product test for this batch of tubes.
10.4.3 Test frequency and sampling location—–casing and tubing
The test frequencies for all sets of casing and tubing are specified in Table C40 or Table E40.
See Appendix H for additional requirements for PSL-2 and PSL-3 steel pipes.
Test tubes shall be randomly selected, and when more than one test is performed, the sampling method shall ensure that the samples provided represent the beginning and end of the heat treatment cycle (if applicable) and both ends of the tube. When more than one test is carried out, the specimens shall be taken from different steel pipes, except that the specimens for thickened pipes may be taken from both ends of one pipe.
10.4.4 Test Frequency and Sampling Location—Coupling Stock, Couplings, Pup Joints, and Accessories
See Table C.41 and Table E.41 for the test frequency of coupling blanks and couplings, and see Table C.42 or E.42 for the test frequency of pup joints and accessories.
For Groups 1, 2 (except C90 and T95), and Group 3 accessories, when sampling from the bar stock, it is taken from the middle corresponding to the wall thickness of the final finished pipe.
Groups 2 (C90 and T95) and 4, tensile test specimens for coupling stock, coupling, pup joints, and accessory material heat treated as a whole shall be taken in accordance with Figure D.10.
Pup joints or accessories made from previously tested and qualified casing, tubing or coupling semi-finished products shall not be subjected to tensile testing if they are not subsequently heat treated.
Furnace—Controlled Tensile Testing may also be used as a product test for this batch of tubes.
10.4.5 Specimen—–General
The tube body tensile test specimens can be selected by the manufacturer, either full-section specimens, bar specimens, or round bar specimens, as shown in Figure D.9. Strip specimens taken from seamless pipe and coupling stock may be determined by the manufacturer. Taken anywhere on the circumference of the tube. The round bar specimen shall be taken from the middle of the pipe wall. The strip and round bar specimens taken from electric welded pipes shall be taken at a position about 90º to the weld, or at the choice of the manufacturer, parallel to the rolling direction on the steel plate for pipe making, at a distance of about four points from the edge of the plate One of the strip widths is sampled. Tensile specimens of heat-treated steel pipe and coupling stock shall be taken from the final heat-treated pipe on the production line.
The width of all bar specimens over the gauge length of approximately 38 mm (1.500 in. ). Otherwise, for the pipe whose size code 1 is less than 4, the width within the gauge length of the sample is about 19mm (0.75in); for the pipe whose size code 1 is 4~7 5/8 size, the width is about 25mm (1.00in) ); for tubes larger than 7 5/8, the width is approximately 38mm (1.500in).
All tensile specimens of the pipe body, except round bar specimens, shall represent the entire wall thickness of the intercepted pipe and shall not be flattened during the test. If a round bar specimen is used, a specimen with a diameter of 12.7 mm (0.500 in) shall be used when the size of the pipe allows; for pipes of other specifications, a round bar specimen with a diameter of 8.9 mm (0.350 in) shall be used. When the tube size is too small to take an 8.9 mm (0.350 in) specimen, the round bar tensile specimen is not suitable. When it is necessary to record or report the elongation, the record and report shall report the specified width of the strip sample used, or the diameter and gauge length of the round bar sample used, or the case of the full-section tubular sample used.
10.4.6 Specimen—Additional Requirements for Grade Q125 Couplings, Pup Joints, and Accessories
In addition to the requirements of Section 10.4.5, longitudinal tensile test specimens shall be taken from the material of the coupling, pup joint or accessory, or after the final heat treatment for coupling semi-finished products, pup joints or accessories that are heat treated separately. The tensile test specimen shall be a strip test specimen, or when the wall thickness of the pipe is greater than 19.1 mm (0.750 in), a round bar test specimen with a diameter of 12.7 mm (0.500 in) as shown in Figure D.9 may be used.
For couplings, pup joints or accessories that are heat-treated in the form of semi-finished couplings or single pieces, the tensile test specimens shall be cut as shown in Figure D.10.
According to the agreement between the supplier and the buyer, strip samples with small cross-sections can be used.
10.4.7 Test method
The tensile properties of the product shall be determined on longitudinal test specimens that meet the requirements of Section 10.4.5, ISO 6892 or ASTM A370, and that of grade Q125 shall meet the requirements of Section 10.4.6. Tensile tests should be carried out at room temperature. The strain rate during tensile test shall meet the requirements of ISO6892 or ASTM A370.
Tensile testing machines shall be calibrated to ISO 7500-1 or ASTM E4 within 15 months prior to any testing. The extensometer shall be calibrated in accordance with ASTM E83 within 15 months prior to any testing. Records shall be kept as specified in 13.5.
10.4.8 Test invalid
If any tensile specimen fails to be machined or defective, that specimen may be discarded and replaced with another specimen.
10.4.9 Reinspection —– all products except couplings, coupling stock, pup joints and accessories of grades C90, T95 and Q125
If one tensile test specimen representing a batch of pipes does not meet the specified requirements, the manufacturer may take three additional pipes from the same batch for re-inspection.
If all the re-inspection samples meet the requirements, the batch of steel pipes shall be judged as qualified except the unqualified pipe that was initially sampled.
If more than one sample in the initial test does not meet the specified requirements or one or more samples in the re-tested sample do not meet the specified requirements, the manufacturer may inspect the remaining steel pipes of the batch one by one. The sampling method for retest specimens shall be the same as those specified in Sections 10.4.5 and 10.4.6. Retest specimens for grades M65, L80 and C95 shall be taken from the same end of the original specimen.
Unqualified batches may be reheat treated and retested as a new batch of tubes.
10.4.10 Retest – Couplings, Coupling Stocks, Pup Joints and Accessories of Grades C90, T95 and Q125
For materials heat-treated as a whole tube, if a tensile specimen does not meet the specified requirements, the manufacturer shall take samples from both ends of the tube in question for testing or discard the tube. No additional testing shall be allowed to determine compliance of coupling, pup joint or accessory material. Both samples should meet the specified requirements, otherwise the steel pipe will be rejected. The manufacturer may re-heat treat the batch of waste tubes and re-test as a batch of tubes.
For materials that are heat-treated as coupling semi-finished products or single products, if one tensile test fails to meet the specified requirements, the manufacturer shall re-heat treat the batch in question, or take three additional tubes from the batch in question. If one or more samples do not meet the requirements, the batch should be discarded. The manufacturer may re-heat treat this batch of waste tubes and re-test as a new batch of tubes.
10.5 Flattening test
10.5.1 General requirements for testing
A flattening test shall be performed on all welded pipes with the D/t ratios shown in Tables C.23 and E.23.
In Sections 10.5.2 to 10.5.7, the 0º position refers to the weld contacting the platen (defined as the 12 o’clock or 6 o’clock position), and the 90º position refers to the weld at the 3 o’clock or 9 o’clock position.
10.5.2 Test frequency
The test frequency shall be determined according to Table C.44 or E.44.
10.5.3 Specimen
Specimens shall be specimen rings or end-cuts not less than 63.5 mm (2-1/2 in) in length.
For pipes cut from coils of multiple gauges, the test of one end of a pipe shall be representative of the test of a subsequent pipe and its adjacent end. If the pipe is to be thickened, the specimen shall be taken before the pipe is thickened.
Specimens may be cut prior to heat treatment, but subjected to the same heat treatment as the tubes represented. If batch testing is used, measures shall be taken to identify the relationship between the sample and the sampling tube. A flattening test shall be performed for each heat in each batch.
For fully normalized ERW pipes, including ERW pipes processed by hot tension rolling in accordance with the requirements of Section 6.2.1, the flattening test may be selected by the manufacturer and taken before or after heat treatment.
10.5.4 Test method—Group 1 non-integrally heat-treated steel pipes
The specimen shall be flattened between two parallel plates. In each set of flattening test specimens, one weld was flattened at 90º and the other was flattened at 0º. The specimen shall be flattened until the tube walls are in contact with each other. Before the distance between the parallel plates is less than the value specified in Table C.23 or E.23, no cracks or fractures shall occur in any part of the specimen. During the entire flattening process, there should be no poor structure, unfused welds, delamination, metal over-burning or extrusion of metal.
10.5.5 Test method—–Group 1 and 2 integral heat-treated steel pipes
The sample is flattened between two parallel plates, and the weld should be at the maximum bend; at the decision of the inspector, the flattening test should also be performed so that the weld and the maximum bend are at a position of 90º. The specimen shall be flattened until it touches the opposite tube wall. Before the distance between parallel plates is less than those specified in Table C.23 or E.23,
There shall be no cracks or fractures in any part of the specimen. During the entire flattening process, there should be no poor structure, unfused welds, delamination, metal over-burning or extrusion of metal.
10.5.6 Test Methods —– Grade P110 Pipe and Grade Q125 Casing
When the buyer specifies ERW (electric welding resistance) and SR11, the requirements of A.6 (SR11) shall be implemented.
10.5.7 Retest
If any of the specimens representing a tube does not meet the specified requirements, the manufacturer may take samples from the same end of the tube for supplementary testing until the requirements are met. However, the length of the finished tube after sampling shall not be less than 80% of the original length. If any sample of a tube representing a batch of products does not meet the specified requirements, the manufacturer may take two other tubes from the batch of products to cut Sample retest. If these re-inspection results meet the specified requirements, the batch of pipes is qualified except for the pipe originally selected as the sample. If any sample for re-inspection fails to meet the specified requirements, the manufacturer may take samples from the remaining pipes of the batch one by one. The method of taking samples for re-inspection is the same as that specified in 10.5.3. At the option of the manufacturer, any batch of tubes may be reheat treated and retested as a new batch of tubes.
10.6 Hardness test
10.6.1 PSL requirements
Additional requirements for PSL-3 grades N80(Q), C95 and P110 are given in Annex H.
10.6.2 Test frequency—–General
The frequency of hardness testing for all products is shown in Tables C.43 and E.43.
Both parties agree that the steel pipe and the thickened part can be subjected to the additional hardness test of the outer surface and the hardness test of the full wall thickness. The test method for this additional test shall be agreed upon by both parties.
A hardness test is not required for pup joints or accessories machined from tested pup joint or accessory material of grades M65, L80, C90, T95 or Q125 without subsequent heat treatment.
10.6.3 Frequency of Tests—–Furnace—Controlled Test—–M65 and L80 Grades
Hardness specimens taken from each furnace-controlled tensile specimen shall be subjected to a full-wall hardness test to determine compliance with hardness requirements.
A furnace-controlled test on one tube may also be used as a product test for this batch of tubes.
10.6.4 Test frequency—–M65 and L80 grades
For steel pipe, coupling and accessory materials, the frequency of hardness testing shall be the same as the frequency of tensile testing corresponding to each product.
See Appendix H for additional requirements for PSL-3 products.
10.6.5 Test Frequency and Sampling Location—–Non-upper tube—–C90 and T95 grades
For non-pumped pipes, a full wall hardness test shall be performed in one quadrant, and the specimen shall be taken from one end of each pipe, with approximately 50% of the specimen loops taken from the front end of the pipe and the other half from the pipe the back end.
See Appendix H for additional requirements for PSL-3 products.
10.6.6 Test Frequency and Sampling Location —– Thickened Pipe—–C90 and T95 Grades
A full-wall hardness test shall be carried out in four quadrants on the body of each tube subjected to the tensile test in accordance with the requirements of 10.4.3 to determine compliance. The test frequency for thickened pipes shall be once every 20 pieces in each batch. Specimens shall be taken from the thickest part of the thickened part and a full-thickness hardness test shall be carried out in four quadrants.
In addition to the full-wall (cross-section) hardness test, a Brinell or Rockwell hardness test shall be performed on the outer surface of the body and thickened portion of each pipe.
10.6.7 Test frequency and sampling location—–couplings, pup joints and accessories—–C90 and T95 grades
For thick-walled pipes used to produce more than one coupling, pup joints and accessories, a sample ring shall be taken at each end of the pipe, and both sample rings shall be subjected to a full-wall hardness test.
For single heat treated couplings, pup joints, and accessories, the pipe fitting with the greatest surface hardness in the lot shall be selected for testing.
For a single heat-treated coupling, the hardness test ring shall be cut from the middle as shown in Figure D.10. For single heat-treated pup joints and accessories, for couplings, pup joints or accessories heat-treated by method c) specified in 10.2.3, the hardness test ring may be cut from the middle as shown in Figure D.10, or from Extended section interception.
The full-thickness hardness test shall be performed in four quadrants.
10.6.8 Test frequency—–Q125 steel grade
For casing, 3 pipes were selected from each batch for full wall hardness testing. If the sampling method can ensure that the samples provided can represent the beginning and end of the heat treatment cycle and both ends of the pipe, the test pipe shall be randomly selected.
For couplings, pup joints or accessory materials heat treated in full pipe, one end of each pipe shall be subjected to a full wall hardness test (with a 50% probability of sampling at each end).
For couplings, pup joints or accessories heat-treated in the form of semi-finished couplings or a single piece, one sample from each batch shall be taken for the full-wall hardness test.
The full wall thickness test shall be performed in one quadrant.
For products of the PSL-3 category, see Appendix H for additional requirements.
10.6.9 Specimen
The hardness test specimen shall be cut from the product according to the position shown in Figure D.10, or cut from the pipe end or extension according to the provisions of this standard. For all grades, the full wall hardness test shall be carried out on a test ring or test block.
For a full-wall hardness test in a quadrant, it shall be carried out on a specimen block taken from the specimen ring or tensile specimen. For full-wall hardness testing in four quadrants, it shall be performed on a sample ring or a sample block taken from a sample ring. The full-wall hardness test ring shall be prepared as specified in Figure D.11.
The two surfaces of the hardness sample should be ground parallel and smooth, and there should be no oxide scale, impurities and lubricants on the surface of the hardness sample.
10.6.10 Test method
Brinell hardness test should be carried out according to ISO6506-1 or ASTM E10, Rockwell hardness according to ISO 6508-1 or ASTM E18.
In this standard, two test methods are used:
a) The outer surface test consists of an indentation;
b) The full wall hardness test includes multiple indentations.
The outer surface hardness test can be carried out by either the Rockwell hardness method or the Brinell hardness method. As specified in this standard, the outer surface hardness test is used for product identification and process control.
The full-thickness hardness test shall be performed in accordance with the Rockwell hardness method and shall be used for product determination of maximum hardness, allowable quantification of hardness change and hardenability in the quenched state. The full-wall hardness test shall be carried out perpendicular to the axis of the steel pipe. When the sample ring is taken from the pipe end, the hardness test shall be carried out from the side of the sample ring away from the pipe end (ie away from the quenched end face). To reduce possible errors, the first hardness indentation in the first quadrant of each hardness test block or ring can be ignored.
When the specified wall thickness is less than 7.62mm (0.30in), for the full wall thickness hardness test, three indentations at the middle of the wall thickness of the sample shall be taken. For all other products, the 3 indentations in each quadrant should be in three locations. The hardness readings of 3 indentations at each location (eg: outer, middle and inner) are averaged as the average hardness reading for that location. The full-wall hardness test consists of the average hardness reading at each location in a quadrant. Whether the full-wall hardness test is performed in one quadrant or four quadrants shall be calibrated in accordance with this standard.
Internal and external indentations shall be measured in a band 2.54-3.18 mm from the surface, but the distance between the center of the indentation and the inner and outer surfaces shall not be less than 2½ times the diameter of the indentation. The distance between indentations should be at least 3 times the indentation diameter (from the center of the indentation to the center of the indentation). For thin-walled tubes, the spacing of each row is allowed to be staggered.
The full wall thickness test generally adopts the Rockwell C scale method. Materials with hardness below 20HRC are accepted by the Rockwell C scale method. When the hardness measured is lower than 20HRC, it should be used with care due to the loss of accuracy, but these results can be used to determine the hardness. Selected by the manufacturer or specified by the purchaser, the Rockwell B scale method may be used for materials with hardness below 20HRC. Rockwell hardness readings and average hardness readings shall be reported on the Rockwell C scale, accurate to one decimal place. When the order specifies the implementation of A.9 (SR15), the manufacturer shall provide three readings to the purchaser.
Unless agreed by the purchaser, the hardness conversion shall be selected by the manufacturer and converted according to a suitable conversion table.
The Brinell hardness reading should be rounded to three significant figures. When the test pressure is greater than 29.342kN (3000kgf), the diameter of the pressure ball is greater than 10mm, and the test pressure lasts for 10s~15s, the test conditions should be reported.
In case of dispute, the laboratory HRC scale hardness test shall be used as the drawing method.
10.6.11 Test invalid
If any hardness test specimen fails to be machined or defective, that test specimen may be scrapped and replaced with another test specimen.
10.6.12 Periodic calibration of hardness testing machines
Brinell hardness testing machine should be regularly calibrated according to ISO6506-1 or ASTM E18 Part B steps, Rockwell hardness tester should be regularly calibrated according to ISO6508-1 or ASTM E10 Part B steps; ISO title is “User Periodic Calibration” Testing Machine Procedures” section is linked to the ASTM section entitled “User Periodic Calibration Procedures”. At the beginning and end of the continuous operation of the testing machine, the tests are calibrated the required number of times so that the manufacturer, the purchaser (or its representative) can confirm that the testing machine is within the calibration range. Calibration is performed using standard test blocks in the following hardness ranges:
a) The second group: 20HRC~35HRC
b) Q125 steel grade: 25HRC~35HRC
If the calibration result of the testing machine is not within the calibration range, for Brinell hardness testing machines, use a standard test block according to ISO6506-2 or ASTM E18 Part B for indirect verification, and for Rockwell hardness testing machines, use a standard test block according to ISO6508-2. or ASTM E10 Part B Indirect Verification.
10.6.13 Re-inspection—–M65 and L80 steel grades
For M65 and L80 steel grades, if a full-wall hardness sample representing a batch of steel pipes does not meet the specified requirements, the manufacturer may take two more samples from the same batch and the same end of the original sample for re-inspection. If all the re-inspection samples meet the requirements, the batch of steel pipes shall be judged as qualified except the unqualified pipe that was initially sampled. If one or more of the re-inspection samples do not meet the specified requirements, the manufacturer may inspect the remaining steel pipes one by one or discard them as a whole.
10.6.14 Re-inspection—–Except coupling semi-finished products, pup joints or accessories cut into single pieces for heat treatment, other products of C90 and T95 grades
For grades C90 and T95, if either average hardness reading is between 25.4HRC and 27.0HRC (including 27.0HRC), then 3 more hardness readings shall be taken in the closest area to determine a new average hardness reading . If the new average hardness reading does not exceed 25.4HRC, the tube is qualified. If the new average hardness reading exceeds 25.4HRC, the canal should be rejected.
10.6.15 Reinspection—–C90 and T95 steel grades cut into single pieces and heat treated coupling semi-finished products, pup joints or accessories
For the semi-finished couplings, pup joints or accessories of steel grades C90 and T95 cut into single pieces for heat treatment, if a hardness sample representing a batch of steel pipes does not meet the specified requirements, the steel pipe shall be rejected. For the batch of steel pipes selected for the initial test, the manufacturer shall re-heat treatment of the batch of steel pipes or use the same selection criteria to retake 3 samples for testing. If any of the three re-test samples fails to meet the specified requirements, the entire heat treatment will be rejected.
10.6.16 Re-inspection—–Q125 steel grade—–General
If the permissible hardness variation on a sample exceeds that specified in C.6 or Table E.6, the hardness indentation in that quadrant may be ground away (at the option of the manufacturer), and the indentation in the initial test can be placed on the lower surface of the indentation. Try again. Only one regrind and retest is allowed for each specimen. After re-inspection, products that do not meet the requirements shall be scrapped.
10.6.17 Re-inspection—–Q125 steel grade—–casing
If more than one of the first 3 test tubes representing a batch of casing fails, the manufacturer may choose to test the remaining tubes of the batch one by one. Retests of these tubes shall only be permitted as specified in 10.6.16.
If only one of the first 3 test tubes representing a batch of casings fails. Then another 3 pipes can be taken for re-inspection to determine whether the batch of casings is qualified. When re-testing, only those specified in Section 10.6.16 are allowed. If any one of the 3 pipes in the re-inspection fails, the manufacturer can choose to test the remaining pipes one by one, or reprocess the batch of pipes (that is, for a batch of casings, 6 pipes Five of the test tubes must comply with Section 7.8 and Table C.6 or E.6 to qualify the batch of casing).
10.6.18 Reinspection—–Grade Q125—–Couplings, pup joints and accessories
When couplings, pup joints or accessories are heat treated with coupling semi-finished products or single pipes, if the hardness change specified in Section 7.8 exceeds the value specified in Table C.6 or E.6, it is at the option of the manufacturer and may be selected from the batch. Another 3 pieces of the products are taken for full wall thickness hardness re-examination. If any of the 3 re-inspected products does not meet the maximum hardness change value, the batch of products should be scrapped.
10.6.19 Retirement —– Groups 2 and 4
For all products, the whole batch of scrap steel pipe shall be reprocessed (ie reheat treated) and retested for hardness as a new batch.
10.7 Impact test
10.7.1 Sampling —– J55, K55 and N80 Grade 1 Pipe
For the accessory materials and coupling blanks required in 7.6, one steel tube from each batch shall be selected for impact testing.
10.7.2 Sampling —– M65 grade pipe
Each batch of steel pipes shall be selected for a set of impact tests.
10.7.3 Sampling —–N80Q, L80, C90, C95, T95 and P110 grades
For tubes, unless compliance with the requirements is determined by documented procedures, one tube from each lot shall be subjected to a set of impact tests, see Section 7.5.6. This test is mandatory if the purchaser implements the requirements of Annex A.10 (SR16).
For the accessory materials and coupling blanks or coupling semi-finished products required in 7.6, one steel tube from each batch shall be selected for a set of impact tests.
10.7.4 Sampling and sample location —– Q125 grade
For casing, 3 steel pipes shall be sampled from each batch for testing. The test pipes shall be randomly selected, and the sampling method shall ensure that the samples provided can represent the beginning and end of the heat treatment cycle and both ends of the treated casing.
For coupling stock, pup joints, or accessory material, when heat treated as a whole pipe, one end of each pipe shall be tested with approximately a 50% chance of sampling each end of the treated ends.
For couplings, pup joints, or accessories, when heat treating coupling blanks and individual pieces, one tube per lot shall be tested.
10.7.5 Specimen
The sampling directions of longitudinal and transverse specimens are shown in Figure D.12.
Impact specimens shall not use flattened tubes.
When using transverse specimens for electric welded pipes, the welds shall be located at the notch position of the Charpy impact test specimens.
The surface of the final machined transverse test specimens may contain the outer diameter surface of the original pipe product, provided that the requirements of Figure D.13 are met. These test specimens shall only be used in transverse test specimens cut to the maximum thickness consistent with Table C.9 or E.9. should be used only when this is the case.
10.7.6 Test method
The Charpy V-notch impact test shall be performed in accordance with ASTM A370 or ASTM E23.
To determine whether a measured value meets these requirements, the measured value should be rounded to the nearest whole number. The impact energy value of a group of impact tests (that is, the average value of three samples) should be expressed as an integer, and the rounding should be carried out according to the ISO31-0 or ASTM E29 rounding method.
10.7.7 Test invalid
Whether before or after the test, if it is found that the sample preparation is unqualified or there is a lack of material unrelated to the test item, the sample can be scrapped and replaced with another sample from the same pipe. The sample shall not be rejected because it does not meet the minimum absorbed work requirement (10.7.7~10.7.9).
10.7.8 Re-examination of a single canal —– all groups
If more than one sample is less than the specified minimum absorbed energy requirement or a single value is less than two-thirds of the specified minimum absorbed energy requirement, three additional samples shall be taken from the same steel pipe for retest. The impact energy of each sample of the re-examination sample shall be equal to or greater than the specified minimum absorbed energy requirement, otherwise the steel pipe shall be judged waste.
10.7.9 Replacement of a single scrap steel pipe —– all groups
If a test result does not meet the requirements of Sections 7.4-7.6 (if applicable), and the re-test results do not meet the requirements of Section 10.7.7, three specimens shall be cut from each of the three additional steel pipes from the batch. , if the test results of these samples are all qualified, the batch of steel pipes shall be judged as qualified except the steel pipe that was initially judged to be discarded; if the test results of one or two steel pipes in such samples still do not meet the requirements, Then the manufacturer may choose, either to test the remaining steel tubes one by one, or to re-heat treat the batch and re-test as a new batch.
10.7.10 Multiple scrap steel pipes —– Q125 grade
If more than one of the three steel pipes in the initial test of a batch of casings is judged to be scrapped, the batch of steel pipes is not allowed to be re-inspected. At the manufacturer’s option, either test the remaining tubes one by one from the batch, or reheat the batch and retest as a new batch.