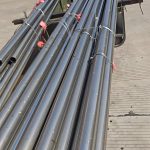
Inconel Alloy X-750 Superalloy Pipes & Tubes
January 11, 2025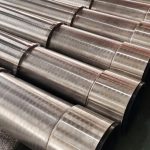
Gravel Pack Screen Pipe
February 6, 2025Quality in Turning of Inconel X-750 Superalloy Steel Pipe
Main Topics | Subtopics |
---|---|
Introduction to Inconel X-750 | Overview of Inconel X-750; Chemical composition and properties; Applications in various industries |
Properties of Inconel X-750 | Heat resistance; High-temperature performance; Corrosion resistance; Mechanical strength |
Challenges in Machining Inconel X-750 | Work-hardening tendencies; Thermal conductivity; High cutting tool wear rates |
Turning Process: An Overview | Definition of turning; Components of turning machines; Importance of precision in turning processes |
Turning of Inconel X-750 | Specialized tools for machining; Process parameters; Surface finish requirements |
Cutting Tools for Turning Inconel X-750 | Material of cutting tools (carbide, ceramics, CBN); Tool geometry and coating; Factors affecting tool life |
Cutting Parameters in Turning | Cutting speed, feed rate, and depth of cut; Optimal parameter ranges for Inconel X-750 |
Tool Wear Mechanisms | Types of wear (flank, crater, notch); Causes and prevention; Tool failure modes in turning Inconel X-750 |
Coolant and Lubrication in Turning | Importance of coolant; Types of coolants for Inconel X-750; Minimum quantity lubrication (MQL) |
Surface Quality in Turning | Definition of surface quality; Factors affecting surface roughness; Techniques to achieve superior surface finishes |
Optimization of Turning Parameters | Methods to optimize machining parameters; Role of computational models and simulations |
Monitoring and Controlling Quality | Real-time monitoring systems; Quality control metrics; Non-destructive testing (NDT) for surface quality |
Environmental Considerations | Environmental impact of machining; Waste management in turning; Eco-friendly coolant alternatives |
Case Studies on Turning of Inconel X-750 | Examples of industrial applications; Lessons learned; Comparison of techniques and results |
Future Trends in Machining Inconel X-750 | Advanced tool materials; Automation and AI in machining; Emerging techniques (e.g., cryogenic cooling) |
FAQs on Turning of Inconel X-750 | Answers to common questions related to machining, tool life, and optimization of processes |
Conclusion | Summary of turning processes for Inconel X-750; Recommendations for achieving high quality |
Quality in Turning of Inconel X-750 Superalloy Steel Pipe
Introduction to Inconel X-750
Inconel X-750 is a high-performance nickel-chromium superalloy renowned for its excellent mechanical and thermal properties. It is specifically designed to withstand extreme operating conditions, including high temperatures, corrosive environments, and mechanical stresses. This superalloy is primarily used in aerospace, automotive, nuclear, and petrochemical industries, where its superior strength and corrosion resistance make it a preferred material for components such as turbine blades, nuclear reactor springs, and gas pipelines.
The chemical composition of Inconel X-750 includes nickel, chromium, iron, and trace amounts of other elements such as titanium, aluminum, and niobium. This unique blend of elements provides excellent resistance to oxidation, creep deformation, and fatigue, even at elevated temperatures. These qualities, while beneficial for operational performance, also pose significant challenges during machining processes like turning.
Properties of Inconel X-750
1. Heat Resistance
One of the most distinctive properties of Inconel X-750 is its ability to retain its strength at high temperatures. The alloy can operate efficiently at temperatures exceeding 700°C, making it ideal for applications in gas turbines, jet engines, and exhaust systems.
2. Corrosion Resistance
Inconel X-750 offers superior resistance to various forms of corrosion, including pitting, crevice corrosion, and oxidation. This makes it a popular choice for components exposed to aggressive environments such as saltwater or acidic conditions.
3. Mechanical Strength
The alloy exhibits remarkable mechanical properties, including high tensile and yield strength. These characteristics are maintained even after prolonged exposure to high temperatures, ensuring durability in critical applications.
4. Work-Hardening Behavior
Inconel X-750 is prone to rapid work-hardening, which means that the material becomes harder and stronger as it is deformed. While this improves its operational strength, it also complicates machining processes.
Challenges in Machining Inconel X-750
1. Work-Hardening Tendencies
Inconel X-750 hardens quickly during machining, increasing the cutting forces required and leading to rapid wear of cutting tools.
2. Poor Thermal Conductivity
The alloy’s low thermal conductivity results in heat being concentrated in the cutting zone, accelerating tool wear and potentially compromising surface quality.
3. High Cutting Tool Wear Rates
Due to its hardness and toughness, machining Inconel X-750 causes significant abrasion and adhesion wear on cutting tools. This necessitates the use of specialized tool materials and coatings to ensure efficiency.
Turning Process: An Overview
Turning is a fundamental machining process that involves the removal of material from a rotating workpiece using a single-point cutting tool. It is widely employed to produce cylindrical components with precise dimensions, smooth surfaces, and tight tolerances. Turning operations play a crucial role in manufacturing Inconel X-750 pipes, where precision and surface quality are critical for functionality.
Components of a Turning Machine
- Chuck: Holds and rotates the workpiece.
- Cutting Tool: Removes material from the workpiece.
- Tool Post: Provides stability to the cutting tool.
- Coolant System: Reduces heat and friction during machining.
Turning of Inconel X-750
Specialized Tools for Machining
Turning Inconel X-750 requires the use of advanced cutting tools made from carbide, ceramic, or cubic boron nitride (CBN). These materials can withstand high temperatures and resist wear effectively. Additionally, coatings such as titanium nitride (TiN) or aluminum oxide (Al2O3) improve tool life and reduce friction.
Process Parameters
Optimal cutting parameters, including cutting speed, feed rate, and depth of cut, are essential for achieving high-quality results. These parameters must be carefully selected to minimize tool wear and maintain surface integrity.
Surface Finish Requirements
In applications where Inconel X-750 pipes are used for high-pressure or high-temperature environments, achieving a smooth surface finish is critical. A fine finish reduces stress concentrations and enhances fatigue resistance.
Cutting Tools for Turning Inconel X-750
1. Tool Materials
- Carbide Tools: Provide good wear resistance and heat dissipation.
- Ceramic Tools: Ideal for high-speed cutting due to their hardness and thermal stability.
- CBN Tools: Suitable for high-precision applications and extended tool life.
2. Tool Geometry
The geometry of the cutting tool, including rake angle, clearance angle, and edge radius, significantly affects the machining performance. A positive rake angle reduces cutting forces, while a sharp edge ensures clean cuts.
3. Tool Coatings
Coatings such as TiN, TiAlN, or diamond-like carbon (DLC) improve tool performance by reducing friction, enhancing heat resistance, and extending tool life.
Cutting Parameters in Turning
The performance of the turning process largely depends on the selection of cutting parameters. For Inconel X-750, the following recommendations are typically followed:
- Cutting Speed: 20–50 m/min (low speeds to reduce heat generation)
- Feed Rate: 0.05–0.2 mm/rev (balanced to ensure smooth cutting)
- Depth of Cut: 0.5–2.0 mm (based on tool capability and surface finish requirements)
Tool Wear Mechanisms
1. Flank Wear
Occurs due to abrasion between the tool and the workpiece. This is the most common wear mechanism in turning Inconel X-750.
2. Crater Wear
Happens on the rake face of the tool, caused by high temperatures and chemical reactions with the alloy.
3. Notch Wear
Develops at the cutting edge due to the work-hardening of Inconel X-750.
Prevention Strategies
- Use of coolant to dissipate heat.
- Optimization of cutting parameters.
- Regular monitoring and replacement of tools.
Coolant and Lubrication in Turning
The use of coolant is critical when turning Inconel X-750 to manage heat and reduce tool wear. Common coolants include:
- Water-Based Coolants: Provide excellent cooling but may require additives to prevent corrosion.
- Oil-Based Coolants: Offer superior lubrication and surface finish.
- Minimum Quantity Lubrication (MQL): An eco-friendly alternative that uses a minimal amount of coolant to reduce waste.
Surface Quality in Turning
Surface quality refers to the smoothness and finish of the machined surface. In turning Inconel X-750, achieving superior surface quality is crucial for performance and longevity. Factors influencing surface quality include:
- Cutting tool material and geometry.
- Cutting speed, feed rate, and depth of cut.
- Use of coolant and lubrication.
Optimization of Turning Parameters
To enhance efficiency and quality, turning parameters can be optimized using:
- Experimental Trials: Testing different parameter combinations to find the optimal setup.
- Computational Models: Using software to simulate machining processes and predict outcomes.
- Data Analysis: Monitoring tool wear and surface finish metrics to adjust parameters.
Monitoring and Controlling Quality
Real-time monitoring systems such as vibration sensors and thermal cameras can help maintain machining quality. Additionally, non-destructive testing methods like ultrasonic testing or surface profilometry ensure that the final product meets quality standards.
Environmental Considerations
Turning processes generate waste in the form of chips, coolant, and emissions. To reduce the environmental impact:
- Use recyclable coolants.
- Implement chip recycling systems.
- Adopt dry or near-dry machining techniques.
Case Studies on Turning of Inconel X-750
Several industries have successfully implemented optimized turning processes for Inconel X-750. For example, aerospace manufacturers have achieved significant cost savings by using advanced tools and parameter optimization.
Future Trends in Machining Inconel X-750
- Cryogenic Cooling: Uses liquid nitrogen to reduce heat and improve tool life.
- AI in Machining: Enables real-time adjustments to machining parameters.
- Advanced Tool Materials: Development of hybrid tools combining ceramic and CBN properties.
Advanced Strategies to Improve Quality in Turning of Inconel X-750
To consistently achieve high-quality results while turning Inconel X-750, manufacturers need to employ advanced strategies beyond standard machining techniques. These include:
1. Adaptive Machining
Adaptive machining utilizes real-time monitoring systems to adjust machining parameters dynamically. This method ensures optimal cutting conditions by continuously analyzing factors like tool wear, cutting temperature, and vibration. By automating these adjustments, manufacturers can minimize downtime and ensure consistent quality.
2. Cryogenic Machining
Cryogenic machining involves the use of liquid nitrogen or carbon dioxide as a coolant. The extremely low temperatures reduce heat generation, prevent tool wear, and improve surface quality. Cryogenic machining is particularly effective for work-hardened alloys like Inconel X-750, as it suppresses thermal stresses during cutting.
3. High-Speed Machining (HSM)
High-speed machining (HSM) can enhance productivity while maintaining surface integrity. The key lies in using advanced cutting tools with high thermal stability and carefully calibrated speeds and feeds. HSM minimizes the material’s tendency to harden excessively during machining, improving tool life and efficiency.
4. Hybrid Tool Technologies
Hybrid tools, combining the benefits of different materials (e.g., ceramic tips with a CBN core), offer excellent performance in turning processes. These tools are designed to withstand high cutting forces, provide superior heat resistance, and extend tool life, even under aggressive cutting conditions.
Industrial Applications of Inconel X-750 in Machining
The industrial importance of Inconel X-750 necessitates precision machining to meet demanding operational requirements. Below are examples of how this alloy is used and why machining quality is critical:
1. Aerospace
- Components such as turbine blades, exhaust ducts, and jet engine parts are often made from Inconel X-750 due to its high-temperature stability.
- Surface integrity and dimensional accuracy are essential for ensuring aerodynamic efficiency and mechanical reliability.
2. Nuclear Industry
- Inconel X-750 is used in nuclear reactor components, including springs, bolts, and heat exchangers, where corrosion resistance is paramount.
- Non-destructive testing methods like ultrasonic inspection are widely used to ensure the quality of machined parts.
3. Oil and Gas
- Inconel X-750 pipes and fittings are frequently used in offshore platforms and gas turbines due to their ability to resist oxidation and creep.
- Turning processes must deliver superior surface finishes to enhance fatigue resistance under extreme pressures and temperatures.
4. Automotive
- High-performance exhaust systems and turbochargers often incorporate Inconel X-750 for its heat resistance.
- Accurate turning of pipes ensures proper assembly and performance in high-stress environments.
Maintenance and Troubleshooting in Turning Inconel X-750
Effective maintenance of tools and machinery is critical to achieving high-quality machining outcomes. Troubleshooting common issues helps to minimize disruptions and improve productivity.
1. Regular Tool Inspection
Frequent checks for tool wear, chipping, and deformation are essential. Replacing worn tools promptly reduces downtime and ensures consistent quality.
2. Machine Calibration
Ensuring the turning machine’s alignment, stability, and vibration control are within acceptable limits is critical for precision machining.
3. Managing Workpiece Temperature
Monitoring and controlling the workpiece temperature during machining prevents thermal distortion, improving dimensional accuracy.
4. Addressing Chip Formation Issues
Poor chip evacuation can lead to surface damage and excessive tool wear. Optimizing cutting speed and using proper chip breakers on the tool can resolve this problem.
Emerging Research on Inconel X-750 Machining
Academic and industrial research continues to develop new methodologies for improving the quality of machining Inconel X-750. Prominent areas of study include:
1. Additive Manufacturing Integration
Combining turning with additive manufacturing methods such as selective laser melting (SLM) offers opportunities to produce near-net-shape components. Post-processing with turning can ensure precision and surface quality.
2. Nanocoated Tools
Research into nano-coatings for cutting tools has shown promise for reducing friction and wear during the machining of superalloys like Inconel X-750.
3. AI-Based Process Control
Artificial intelligence and machine learning are being employed to optimize machining parameters in real-time, predicting and mitigating issues such as tool wear and thermal stress.
4. Sustainable Machining
Efforts to develop eco-friendly coolants and minimize waste generation in machining processes are gaining traction, aligning with global sustainability goals.
Final Recommendations for Machining Inconel X-750
To achieve superior quality while turning Inconel X-750, manufacturers should adopt a combination of best practices and innovative techniques:
- Select the Right Tooling: Invest in high-quality carbide, ceramic, or CBN tools with advanced coatings to handle the alloy’s toughness.
- Optimize Parameters: Use lower cutting speeds and appropriate feed rates to manage heat and minimize tool wear.
- Implement Coolant Strategies: Consider advanced cooling solutions, including cryogenic cooling or minimum quantity lubrication (MQL), for improved performance.
- Monitor Quality: Leverage real-time monitoring systems and conduct thorough inspections to maintain dimensional accuracy and surface integrity.
- Stay Updated: Keep up with emerging technologies and research to adopt the latest advancements in machining practices.
FAQs on Turning of Inconel X-750
1. Why is Inconel X-750 difficult to machine?
Inconel X-750’s work-hardening properties and low thermal conductivity make it challenging to machine. These factors increase cutting forces, tool wear, and heat generation during machining processes.
2. What tools are recommended for machining Inconel X-750?
Carbide, ceramic, and CBN tools with appropriate coatings (e.g., TiN or TiAlN) are best suited for machining Inconel X-750 due to their wear resistance and thermal stability.
3. How can I reduce tool wear when machining Inconel X-750?
To reduce tool wear:
- Use optimized cutting speeds and feed rates.
- Apply effective coolants or lubrication.
- Use sharp tools with appropriate geometry and coatings.
4. What role does coolant play in turning Inconel X-750?
Coolant reduces heat generation, improves surface finish, and minimizes tool wear during the turning process. Advanced cooling techniques like cryogenic machining further enhance efficiency.
5. Is it possible to achieve a mirror-like surface finish on Inconel X-750?
Yes, a mirror-like surface finish can be achieved by using high-precision tools, optimizing machining parameters, and employing advanced polishing techniques as part of the post-machining process.
6. Can turning processes be automated for Inconel X-750 machining?
Yes, turning processes for Inconel X-750 can be automated using CNC machines equipped with real-time monitoring and adaptive control systems. This enhances precision and consistency while reducing manual intervention.
Turning Inconel X-750 superalloy steel pipes is a challenging yet rewarding process that demands careful consideration of tools, parameters, and quality control techniques. By understanding the unique properties of this superalloy and leveraging advanced machining strategies, manufacturers can produce high-quality components that meet stringent industrial standards. From selecting cutting-edge tools to adopting sustainable machining practices, there are numerous ways to optimize the process and achieve exceptional results. With ongoing advancements in machining technology, the future holds even greater potential for improving the efficiency and quality of turning Inconel X-750.