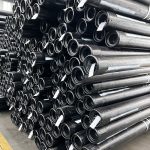
CO2 Corrosion Resistant Tubing and Casing Pipe
November 2, 2024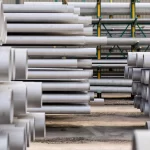
Welding of Nickel Alloy Steel Pipe Buttering and Stainless Steel Pipe
November 16, 2024ASTM A333M Petroleum Cracking Pipe
Introduction
The ASTM A333M specification covers seamless and welded steel pipes designed for low-temperature service, making it a critical material in industries such as petroleum refining, natural gas processing, and chemical plants. One of the key applications of ASTM A333M pipes is in petroleum cracking, where the pipes are exposed to high temperatures and pressures, as well as corrosive environments. These pipes are specifically engineered to withstand the harsh conditions of petroleum cracking units and ensure the safe and efficient transport of hydrocarbons.
In this article, we will explore the properties, applications, and advantages of ASTM A333M petroleum cracking pipes, as well as the factors that influence their performance in the oil and gas industry.
Nominal (average) wall seamless and welded carbon and alloy steel pipe intended for use at low temperatures and in other applications requiring notch toughness.
Composition, % | |||||||||
Element | Grade 1
|
Grade 3
|
Grade 4
|
Grade 6
|
Grade 7
|
Grade 8
|
Grade 9
|
Grade 10
|
Grade 11
|
Carbon, max
|
0.30
|
0.19
|
0.12
|
0.30
|
0.19
|
0.13
|
0.20
|
0.20
|
0.10
|
Manganese
|
0.40–1.06A
|
0.31–0.64
|
0.50–1.05
|
0.29–1.06A
|
0.90 max
|
0.90 max
|
0.40–1.06
|
1.15–1.50
|
0.60 max
|
Phosphorus,max
|
0.025
|
0.025
|
0.025
|
0.025
|
0.025
|
0.025
|
0.025
|
0.035
|
0.025
|
Sulfur, max | 0.025
|
0.025
|
0.025
|
0.025
|
0.025
|
0.025
|
0.025
|
0.015
|
0.025
|
Silicon
|
– | 0.18–0.37
|
0.08–0.37
|
0.10 min
|
0.13–0.32
|
0.13–0.32
|
– | 0.10–0.35
|
0.35 max
|
Nickel
|
– | 3.18–3.82
|
0.47–0.98
|
0.40 max
|
2.03–2.57
|
8.40–9.60
|
1.60–2.24
|
0.25 max
|
35.0–37.0
|
Chromium
|
– | – | 0.44–1.01
|
0.30 max
|
– | – | – | 0.15 max
|
0.50 max
|
Copper
|
– | – | 0.40–0.75
|
0.40 max
|
– | – | 0.75–1.25
|
0.15 max
|
– |
Aluminum
|
– | – | 0.04–0.30
|
– | – | – | – | 0.06 max
|
– |
Vanadium, max
|
– | – | – | 0.08
|
– | – | – | 0.12
|
– |
Columbium, Max
|
– | – | – | 0.02C
|
– | – | – | 0.05
|
– |
Molybdenum, Max
|
– | – | – | 0.12
|
– | – | – | 0.05
|
0.50 max
|
Cobalt
|
– | – | – | – | – | – | – | – | 0.50 max |
Table of Contents
- Overview of ASTM A333M
- Key Properties of ASTM A333M Petroleum Cracking Pipe
- 2.1 Low-Temperature Toughness
- 2.2 Corrosion Resistance
- 2.3 Mechanical Strength
- 2.4 Weldability
- Applications of ASTM A333M Petroleum Cracking Pipe
- 3.1 Petroleum Refining
- 3.2 Natural Gas Processing
- 3.3 Chemical Plants
- Grades of ASTM A333M Pipe
- Manufacturing and Testing Requirements
- 5.1 Hydrostatic Testing
- 5.2 Impact Testing
- 5.3 Nondestructive Testing
- Frequently Asked Questions (FAQ)
- Conclusion
Overview of ASTM A333M {#overview-of-astm-a333m}
ASTM A333M is a specification developed by the American Society for Testing and Materials (ASTM) that covers seamless and welded steel pipes intended for use in low-temperature environments. The “M” designation indicates that the specification follows the metric system. These pipes are primarily used in industries where low-temperature toughness and resistance to brittle fracture are critical, such as petroleum cracking and natural gas processing.
The specification includes several grades, each with different chemical compositions and mechanical properties, allowing engineers to select the appropriate material based on the specific requirements of their application. ASTM A333M petroleum cracking pipes are designed to withstand the high pressures, temperatures, and corrosive environments typically encountered in petroleum refining units.
Key Properties of ASTM A333M Petroleum Cracking Pipe {#key-properties}
The performance of ASTM A333M petroleum cracking pipes is determined by several key properties, including low-temperature toughness, corrosion resistance, mechanical strength, and weldability.
2.1 Low-Temperature Toughness {#low-temperature-toughness}
One of the primary reasons for using ASTM A333M pipes in petroleum cracking applications is their excellent low-temperature toughness. These pipes are designed to maintain their mechanical integrity even at temperatures as low as -45°C. This property is crucial in environments where the pipes are exposed to low temperatures, such as in natural gas processing plants or cryogenic applications.
Low-temperature toughness is achieved through careful control of the pipe’s chemical composition and heat treatment processes. The addition of elements such as nickel and manganese improves the material’s toughness and resistance to brittle fracture at low temperatures.
2.2 Corrosion Resistance {#corrosion-resistance}
Corrosion resistance is another critical property of ASTM A333M petroleum cracking pipes. In petroleum refining and cracking units, the pipes are exposed to corrosive substances such as hydrogen sulfide (H2S), carbon dioxide (CO2), and other aggressive chemicals. The material’s ability to resist corrosion ensures the longevity of the pipes and reduces the risk of leaks or failures.
While ASTM A333M pipes are not inherently corrosion-resistant like stainless steel or corrosion-resistant alloys (CRAs), they can be coated or treated with corrosion inhibitors to enhance their resistance to corrosive environments.
2.3 Mechanical Strength {#mechanical-strength}
Mechanical strength is a key consideration in petroleum cracking applications, where the pipes are subjected to high pressures and temperatures. ASTM A333M pipes offer excellent tensile strength and yield strength, ensuring that they can withstand the mechanical stresses encountered in cracking units.
The mechanical properties of ASTM A333M pipes are influenced by factors such as their chemical composition, heat treatment, and manufacturing process. Engineers can select the appropriate grade of ASTM A333M pipe based on the specific mechanical requirements of their application.
2.4 Weldability {#weldability}
Weldability is an important factor in the installation and maintenance of petroleum cracking pipes. ASTM A333M pipes are designed to be easily welded, allowing for efficient installation and repair in the field. The pipes can be welded using standard welding techniques such as arc welding, gas tungsten arc welding (GTAW), and gas metal arc welding (GMAW).
To ensure the integrity of the welds, it is important to follow proper welding procedures and use compatible filler materials. Post-weld heat treatment (PWHT) may also be required to relieve residual stresses and improve the toughness of the welded joints.
Applications of ASTM A333M Petroleum Cracking Pipe {#applications}
ASTM A333M petroleum cracking pipes are used in a wide range of applications in the oil and gas industry, particularly in environments where low-temperature toughness and resistance to high pressures and corrosive substances are critical.
3.1 Petroleum Refining {#petroleum-refining}
In petroleum refining, ASTM A333M pipes are used in cracking units, where hydrocarbons are broken down into smaller molecules through processes such as thermal cracking and catalytic cracking. These units operate at high temperatures and pressures, and the pipes must be able to withstand the mechanical stresses and corrosive environments encountered in these processes.
3.2 Natural Gas Processing {#natural-gas-processing}
Natural gas processing involves the removal of impurities such as water, carbon dioxide (CO2), and hydrogen sulfide (H2S) from raw natural gas. ASTM A333M pipes are used in gas processing plants, where they are exposed to low temperatures and corrosive gases. The pipes’ low-temperature toughness and corrosion resistance make them ideal for this application.
3.3 Chemical Plants {#chemical-plants}
In chemical plants, ASTM A333M pipes are used to transport chemicals and gases under high pressures and temperatures. The pipes’ ability to withstand corrosive environments and maintain their mechanical integrity at low temperatures makes them suitable for use in a variety of chemical processing applications.
Grades of ASTM A333M Pipe {#grades-of-astm-a333m-pipe}
The ASTM A333M specification includes several grades, each with different chemical compositions and mechanical properties. The most commonly used grades for petroleum cracking applications include:
- Grade 1: This is the most basic grade of ASTM A333M pipe, offering good low-temperature toughness and mechanical strength. It is suitable for general low-temperature applications.
- Grade 6: This grade offers improved mechanical properties and is one of the most commonly used grades in the oil and gas industry. It is widely used in petroleum cracking units and natural gas processing plants.
- Grade 3: This grade contains higher levels of nickel, which improves its low-temperature toughness and corrosion resistance. It is used in more demanding applications where enhanced performance is required.
Each grade of ASTM A333M pipe is designed to meet specific performance requirements, allowing engineers to select the appropriate material for their application.
Manufacturing and Testing Requirements {#manufacturing-and-testing-requirements}
To ensure the quality and performance of ASTM A333M petroleum cracking pipes, the specification includes several manufacturing and testing requirements. These requirements are designed to verify the pipes’ mechanical properties, toughness, and resistance to corrosion.
5.1 Hydrostatic Testing {#hydrostatic-testing}
Hydrostatic testing is used to verify the integrity of the pipes and ensure that they can withstand the internal pressures encountered in petroleum cracking applications. During the test, the pipe is filled with water and pressurized to a specified level. The pipe is then inspected for leaks or deformation. Hydrostatic testing is a critical step in ensuring the safety and reliability of the pipes.
5.2 Impact Testing {#impact-testing}
Impact testing is used to evaluate the pipe’s toughness at low temperatures. The test involves striking a sample of the pipe with a hammer and measuring the amount of energy absorbed by the material before it fractures. ASTM A333M pipes must meet specific impact toughness requirements to ensure that they can withstand the low temperatures encountered in petroleum cracking and natural gas processing applications.
5.3 Nondestructive Testing {#nondestructive-testing}
Nondestructive testing (NDT) methods such as ultrasonic testing (UT) and radiographic testing (RT) are used to detect defects in the pipes without damaging them. These tests are used to identify flaws such as cracks, voids, or inclusions that could compromise the integrity of the pipes. NDT is an essential part of the quality control process for ASTM A333M pipes.
Frequently Asked Questions (FAQ) {#faq}
1. What is ASTM A333M?
ASTM A333M is a specification developed by the American Society for Testing and Materials (ASTM) that covers seamless and welded steel pipes designed for low-temperature service. These pipes are used in industries such as petroleum refining, natural gas processing, and chemical plants.
2. What are the key properties of ASTM A333M petroleum cracking pipes?
The key properties of ASTM A333M petroleum cracking pipes include low-temperature toughness, corrosion resistance, mechanical strength, and weldability. These properties make the pipes suitable for use in harsh environments where they are exposed to high pressures, temperatures, and corrosive substances.
3. What are the common applications of ASTM A333M pipes?
ASTM A333M pipes are commonly used in petroleum refining, natural gas processing, and chemical plants. They are designed to withstand the harsh conditions encountered in these industries, including low temperatures, high pressures, and corrosive environments.
4. What grades of ASTM A333M pipe are used in petroleum cracking applications?
The most commonly used grades of ASTM A333M pipe in petroleum cracking applications include Grade 1, Grade 6, and Grade 3. Each grade offers different levels of mechanical strength, toughness, and corrosion resistance.
5. How are ASTM A333M pipes tested for quality?
ASTM A333M pipes are tested using methods such as hydrostatic testing, impact testing, and nondestructive testing (NDT). These tests verify the pipes’ mechanical properties, toughness, and resistance to defects, ensuring their quality and performance in the field.
Conclusion {#conclusion}
ASTM A333M petroleum cracking pipes play a crucial role in the oil and gas industry, particularly in applications where low-temperature toughness, corrosion resistance, and mechanical strength are critical. These pipes are designed to withstand the harsh conditions of petroleum cracking units, natural gas processing plants, and chemical plants, ensuring the safe and efficient transport of hydrocarbons.
By selecting the appropriate grade of ASTM A333M pipe and following proper manufacturing and testing procedures, operators can ensure the longevity and reliability of their piping systems, reducing the risk of failures and minimizing downtime.