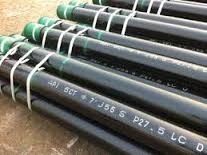
J55 Casing Pipe Expansion Properties
October 28, 2024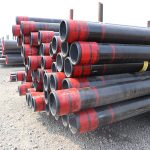
ASTM A333M Petroleum Cracking Pipe
November 7, 2024CO2 Corrosion Resistant Tubing and Casing Pipe
Introduction
In the oil and gas industry, carbon dioxide (CO2) corrosion is a significant concern, particularly in environments where CO2 is present in high concentrations. CO2 corrosion, also known as sweet corrosion, occurs when carbon dioxide dissolves in water, forming carbonic acid (H2CO3), which can aggressively attack steel materials, leading to pitting, uniform corrosion, and ultimately, failure of tubing and casing pipes. This type of corrosion is especially prevalent in CO2-rich reservoirs, enhanced oil recovery (EOR) operations, and gas wells.
To combat CO2 corrosion, the industry has developed specialized CO2 corrosion-resistant tubing and casing pipes. These pipes are designed to withstand the harsh conditions of CO2-rich environments, ensuring the integrity of the wellbore and preventing costly failures. In this article, we will explore the properties, materials, and technologies used in CO2 corrosion-resistant tubing and casing pipes, as well as the factors that influence their performance.
API SPEC 5CT specification for casing and tubing
ANSI/NACE TM0177 Laboratory testing of metals for resistance to sulfide stress cracking and stress corrosion cracking in H2S environment.
ISO 15156 Petroleum and natural gas industries-material for use in H2S containing environments in oil and gas production.
ISO 13680 Petroleum and natural gas industries corrosion-resistant seamless tubes for use as casing , tubing and coupling stock technical delivery conditions third edition.
Grade
|
Product Name
|
Yield strength/Mpa | Tensile strength/Mpa | Elongation
|
Charpy V-Impact/J | Max Hardness(HRC) | |
Min | Max | Min | |||||
55 | BL55-5cr | 449 | 552 | 517 | Calculated according to API 5CT Formula | Hb210 | |
80 | BL80-1cr | 552 | 758 | 689 | 23 | ||
BL80-3cr | |||||||
90 | BL90-3cr | 621 | 724 | 689 | 25.4 | ||
95 | BL95-3cr | 655 | 758 | 724 | 25.4 | ||
BL95-13cr | |||||||
BL95S-13cr | |||||||
110 | BL110-3Cr | 758 | 965 | 862 | 32 | ||
BL110-5Cr | |||||||
BL110S-5Cr | |||||||
125 | BL125-5cr | 862 | 1034 | 931 | – | ||
BL125-15cr | |||||||
130 | BL130-5cr | 896 | 1103 | 1034 | – |
C:Non API Products can also negotiate with clients regarding technical data.
Table of Contents
- Understanding CO2 Corrosion
- Materials for CO2 Corrosion Resistance
- 2.1 Carbon Steel
- 2.2 Low Alloy Steel
- 2.3 Corrosion-Resistant Alloys (CRAs)
- 2.4 Clad and Lined Pipes
- Factors Affecting CO2 Corrosion
- 3.1 CO2 Partial Pressure
- 3.2 Temperature
- 3.3 Water Content
- 3.4 pH Levels
- Testing and Evaluation of CO2 Corrosion Resistance
- 4.1 Autoclave Testing
- 4.2 Electrochemical Testing
- 4.3 Field Testing
- Applications of CO2 Corrosion-Resistant Tubing and Casing
- Frequently Asked Questions (FAQ)
- Conclusion
Understanding CO2 Corrosion {#understanding-co2-corrosion}
CO2 corrosion occurs when carbon dioxide dissolves in water, forming carbonic acid. This acid reacts with the iron in steel to form iron carbonate (FeCO3), which can either form a protective layer or, under certain conditions, lead to aggressive corrosion. The severity of CO2 corrosion depends on several factors, including the partial pressure of CO2, temperature, water content, and pH levels.
The general reaction for CO2 corrosion in steel is as follows:
The formation of iron carbonate can sometimes act as a protective layer, slowing down the corrosion process. However, in high-velocity environments or where the protective layer is unstable, the corrosion rate can increase significantly, leading to pitting, erosion, or uniform corrosion.
Materials for CO2 Corrosion Resistance {#materials-for-co2-corrosion-resistance}
Selecting the right material for CO2 corrosion-resistant tubing and casing is critical to ensuring the longevity and safety of oil and gas wells. Several materials are commonly used, each with its own advantages and limitations.
2.1 Carbon Steel {#carbon-steel}
Carbon steel is the most commonly used material for tubing and casing in the oil and gas industry due to its low cost and availability. However, carbon steel is highly susceptible to CO2 corrosion, especially in environments with high CO2 partial pressures and water content. To mitigate CO2 corrosion in carbon steel, operators often use corrosion inhibitors, coatings, or cathodic protection.
While carbon steel can be used in CO2 environments with the right protection measures, it is generally not recommended for high CO2 concentrations or high-temperature applications, where more resistant materials are required.
2.2 Low Alloy Steel {#low-alloy-steel}
Low alloy steel contains small amounts of alloying elements such as chromium, molybdenum, or nickel, which improve its resistance to CO2 corrosion. These materials offer better performance than carbon steel in moderate CO2 environments but may still require the use of corrosion inhibitors or coatings to enhance their durability.
Low alloy steels are often used in moderate-depth wells or gas wells where CO2 concentrations are not excessively high.
2.3 Corrosion-Resistant Alloys (CRAs) {#corrosion-resistant-alloys}
Corrosion-resistant alloys (CRAs) are specially designed materials that offer superior resistance to CO2 corrosion. These alloys typically contain high levels of chromium, nickel, and molybdenum, which provide excellent resistance to both CO2 and hydrogen sulfide (H2S) corrosion.
Common CRAs used in CO2-rich environments include:
- 13Cr (Martensitic Stainless Steel): Contains approximately 13% chromium and offers good resistance to CO2 corrosion in low to moderate temperatures. It is widely used in CO2-rich gas wells and EOR operations.
- Super 13Cr: An enhanced version of 13Cr with better corrosion resistance at higher temperatures and CO2 partial pressures.
- Duplex Stainless Steel: Combines the properties of austenitic and ferritic stainless steels, offering excellent resistance to CO2 corrosion and high mechanical strength.
- Nickel-Based Alloys (e.g., Inconel, Hastelloy): These alloys provide the highest level of corrosion resistance and are used in the most severe CO2 environments, including high-temperature and high-pressure wells.
While CRAs offer excellent corrosion resistance, they are significantly more expensive than carbon steel or low alloy steel, making them suitable for high-risk environments where failure would be catastrophic.
2.4 Clad and Lined Pipes {#clad-and-lined-pipes}
Clad and lined pipes combine the cost-effectiveness of carbon steel with the corrosion resistance of CRAs. In these pipes, a thin layer of CRA material is bonded to the inner surface of a carbon steel pipe, providing excellent corrosion resistance at a lower cost than using solid CRA pipes.
- Clad Pipes: The CRA layer is metallurgically bonded to the carbon steel pipe, providing a strong and durable corrosion-resistant surface.
- Lined Pipes: The CRA layer is mechanically bonded to the carbon steel pipe, offering corrosion resistance without the need for a metallurgical bond.
Clad and lined pipes are commonly used in CO2-rich environments where cost is a concern, but corrosion resistance is still critical.
Factors Affecting CO2 Corrosion {#factors-affecting-co2-corrosion}
Several factors influence the rate and severity of CO2 corrosion in tubing and casing pipes. Understanding these factors is essential for selecting the right materials and implementing effective corrosion prevention strategies.
3.1 CO2 Partial Pressure {#co2-partial-pressure}
The partial pressure of CO2 is a key factor in determining the severity of CO2 corrosion. Higher CO2 partial pressures result in more CO2 dissolving in water, leading to the formation of more carbonic acid and, consequently, higher corrosion rates. In general, as the CO2 partial pressure increases, the need for corrosion-resistant materials or inhibitors becomes more critical.
3.2 Temperature {#temperature}
Temperature has a complex effect on CO2 corrosion. At moderate temperatures (below 60°C), the corrosion rate tends to increase with temperature due to the increased solubility of CO2 in water. However, at higher temperatures (above 100°C), the formation of protective iron carbonate layers may slow down the corrosion rate.
In high-temperature environments, materials such as super 13Cr or nickel-based alloys are often required to withstand the combined effects of CO2 corrosion and thermal stress.
3.3 Water Content {#water-content}
Water is a critical factor in CO2 corrosion because CO2 must dissolve in water to form carbonic acid. In dry gas wells, where water content is minimal, CO2 corrosion is less of a concern. However, in wells with high water content, especially in wet gas or condensate wells, the risk of CO2 corrosion is significantly higher.
3.4 pH Levels {#ph-levels}
The pH of the environment also affects CO2 corrosion. Lower pH levels (more acidic conditions) increase the corrosion rate, while higher pH levels (more alkaline conditions) can reduce the corrosion rate. In CO2-rich environments, the pH is typically low due to the formation of carbonic acid. pH stabilization techniques, such as adding alkaline substances to the fluid, can help mitigate CO2 corrosion.
Testing and Evaluation of CO2 Corrosion Resistance {#testing-and-evaluation}
To ensure that tubing and casing pipes can withstand CO2 corrosion, several testing methods are used to evaluate their performance in CO2-rich environments.
4.1 Autoclave Testing {#autoclave-testing}
Autoclave testing involves exposing the material to high-pressure CO2 and water in a controlled environment to simulate downhole conditions. The test is conducted at elevated temperatures and pressures to evaluate the material’s resistance to CO2 corrosion. Autoclave testing is commonly used to assess the performance of CRAs and low alloy steels in CO2 environments.
4.2 Electrochemical Testing {#electrochemical-testing}
Electrochemical testing measures the corrosion rate of a material by monitoring the electrochemical reactions that occur when the material is exposed to CO2 and water. This method provides valuable data on the material’s corrosion resistance and can help identify the best materials for specific CO2-rich environments.
4.3 Field Testing {#field-testing}
Field testing involves installing the tubing or casing pipe in an actual wellbore and monitoring its performance over time. This method provides real-world data on the material’s ability to withstand CO2 corrosion under actual operating conditions. Field testing is often used to validate the results of laboratory tests and ensure the long-term performance of the material.
Applications of CO2 Corrosion-Resistant Tubing and Casing {#applications}
CO2 corrosion-resistant tubing and casing pipes are used in a variety of applications, including:
- CO2-Rich Gas Wells: In wells where CO2 is present in high concentrations, corrosion-resistant materials such as 13Cr or super 13Cr are commonly used to prevent CO2 corrosion.
- Enhanced Oil Recovery (EOR): In CO2 injection EOR operations, where CO2 is injected into the reservoir to enhance oil recovery, corrosion-resistant tubing and casing are essential to prevent failure due to CO2 corrosion.
- High-Temperature Wells: In wells with high temperatures, materials such as nickel-based alloys or duplex stainless steel are used to withstand the combined effects of CO2 corrosion and thermal stress.
- Wet Gas Wells: In wells with high water content, corrosion-resistant materials are used to prevent CO2 corrosion, which is exacerbated by the presence of water.
Frequently Asked Questions (FAQ) {#faq}
1. What is CO2 corrosion in tubing and casing pipes?
CO2 corrosion, also known as sweet corrosion, occurs when carbon dioxide dissolves in water to form carbonic acid, which reacts with steel to form iron carbonate. This process can lead to pitting, uniform corrosion, and failure of tubing and casing pipes.
2. What materials are used for CO2 corrosion-resistant tubing and casing?
Materials used for CO2 corrosion-resistant tubing and casing include carbon steel (with inhibitors), low alloy steel, corrosion-resistant alloys (CRAs) such as 13Cr and nickel-based alloys, and clad or lined pipes.
3. How does temperature affect CO2 corrosion?
Temperature affects CO2 corrosion in different ways. At moderate temperatures, the corrosion rate increases with temperature due to higher CO2 solubility. At higher temperatures, protective iron carbonate layers may form, reducing the corrosion rate.
4. What is the role of water in CO2 corrosion?
Water is essential for CO2 corrosion because CO2 must dissolve in water to form carbonic acid. In wells with high water content, the risk of CO2 corrosion is significantly higher compared to dry gas wells.
5. How is CO2 corrosion resistance tested?
CO2 corrosion resistance is tested using methods such as autoclave testing, electrochemical testing, and field testing. These tests evaluate the material’s performance in CO2-rich environments under simulated or actual wellbore conditions.
Conclusion {#conclusion}
CO2 corrosion is a major challenge in the oil and gas industry, particularly in wells with high CO2 concentrations. To prevent costly failures and ensure the integrity of the wellbore, it is essential to use CO2 corrosion-resistant tubing and casing pipes. Materials such as corrosion-resistant alloys (CRAs), clad pipes, and low alloy steels offer excellent resistance to CO2 corrosion, making them suitable for a wide range of applications, including CO2-rich gas wells, EOR operations, and high-temperature wells.
By understanding the factors that influence CO2 corrosion and selecting the right materials, operators can significantly extend the lifespan of their tubing and casing pipes, reduce maintenance costs, and improve the overall safety and reliability of their operations.