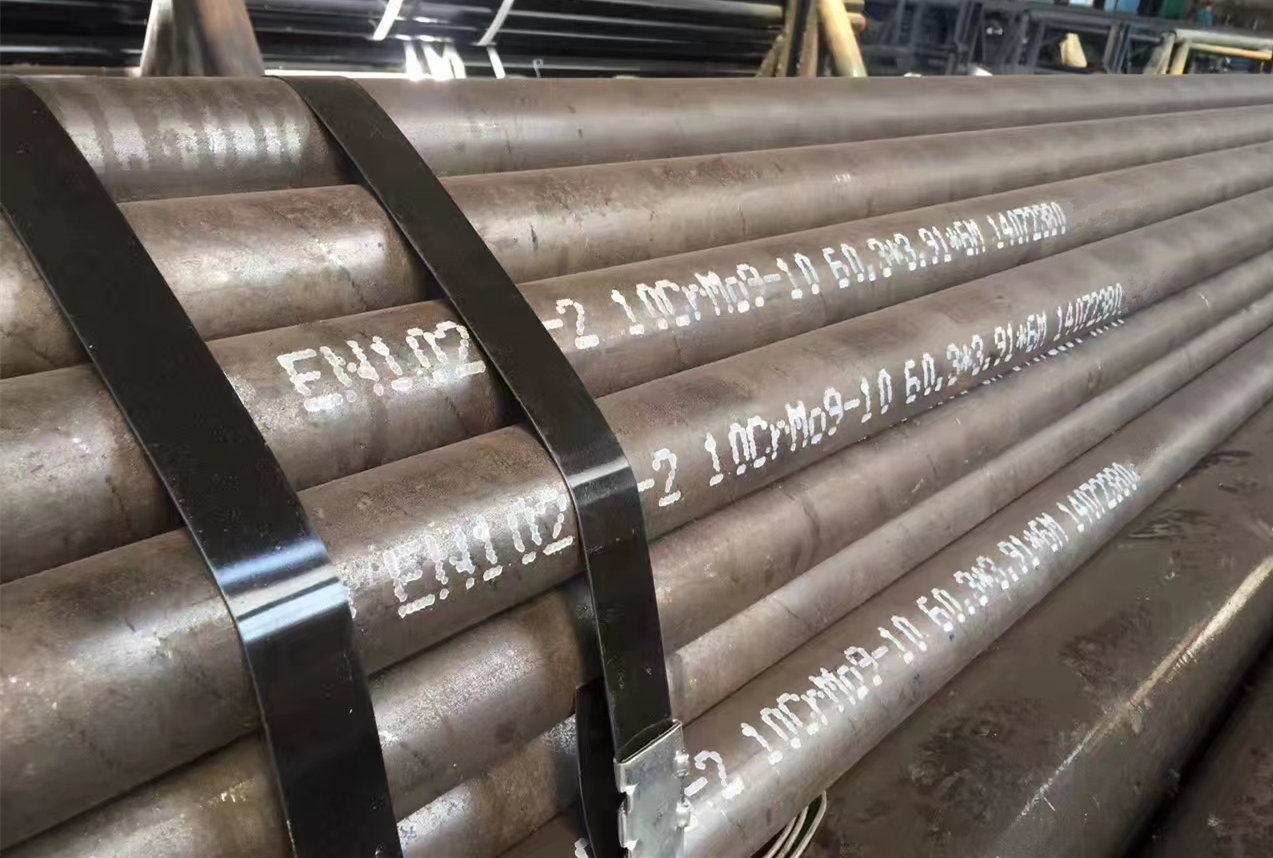
difference between EN 10216 stee pipe and A333 alloy pipe?
February 16, 2023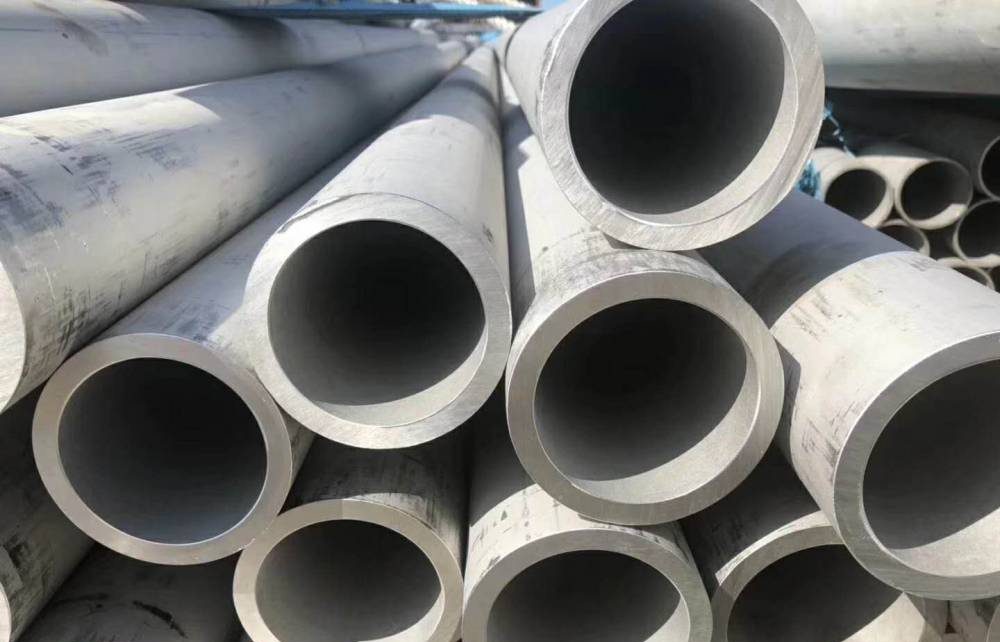
I have a little insight about steel pipe manufacturing
February 25, 2023The all-welded wire wound sieve pipe is widely used in the oil, gas and water well sand control industries all over the world. Its position in the well industry is particularly prominent. It is the most widely used filter screen of various water resources.
abterstee screen using the world’s most advanced all around the welding production process, the application of special trapezoidal wire winding in a circumferential array of supporting wire welded together. Full range of welding, to ensure the product is strictly continuous integrity, so that it forms the ideal gap size, and have the maximum capacity to withstand high pressure.
Each production link by the professional production of advanced sophisticated equipment for professional production. Product specifications and raw materials can be customized according to customer needs, all products are strictly in accordance with the standard SY / T 5182-2008 production testing to ensure product quality, thus ensuring the interests of our customers, the most economical investment to obtain the highest production efficiency.
water well Screen (Filter Pipe): Enhancing Filtration Efficiency
Wire well screens, also known as filter pipes, play a vital role in various industries by facilitating filtration processes. These screens are specially designed to effectively filter out impurities from liquids or gases, ensuring the desired level of purity and quality. In this article, we will explore the features, applications, and benefits of wire wound screens, shedding light on their significance in filtration systems.
1. Introduction to Wire Wound Screens
Wire wound screens are cylindrical filter pipes constructed by tightly winding a thin, continuous wire around a perforated or slotted metal tube. The wire is typically made of stainless steel or other corrosion-resistant materials, ensuring durability and longevity. The winding process creates a series of continuous V-shaped or triangular-shaped openings along the length of the screen, allowing for efficient filtration while maintaining structural integrity.
2. Filtration Efficiency and Precision
One of the key advantages of wire wound screens is their high filtration efficiency and precision. The closely spaced wire winding creates narrow openings, which effectively trap and retain solid particles or contaminants while allowing the desired liquid or gas to pass through. The size of the wire and the gap between windings can be customized to meet specific filtration requirements, ensuring optimal performance and reliable filtration.
Specifications:
- Material: Stainless steel Grade 316L
- Inner Diameter (I.D.): Ranging from 150mm to 1000mm, with a specific size of 400mm
- Slot Size: Ranging from 0.1mm to 30mm, with a specific size of 0.75mm
- Components: None
- Length: Ranging from 300mm to 3000mm, with a specific size of 500mm
- Filter Type: From inside to outside
- Wire Size: 23.5mm (WidthHeight)
- Support Rod: 34.6mm (WidthHeight)
- Wire Shape: V shape
Regular Specifications:
- Material: Stainless steel 302, 304, 316, 304L, 316L, or low carbon galvanized steel
- Inner Diameter (I.D.): Ranging from 150mm to 1000mm
- Slot: Ranging from 0.1mm to 35mm
- Discrepancy: +/- 0.05mm
- Length: Ranging from 300mm to 3000mm
- Filter Type: From inside to outside
- Slot Type: Inside circle wire and slot, inside vertical wire and slot
- Other Components: Flange, stiffener, lifting handle, and other requested components
Sizes of the Wire and Rod:
Wire:
- Width(mm): 1.0, 1.2, 1.5, 2.3, 3.0
- Height(mm): 2.0, 2.2, 2.5, 3.5, 4.6
Rod (Round Wire):
- Width(mm): 2.3, 2.3, 3.0, 3.7, 3.3 (Diameter)
- Height(mm): 2.7, 3.5, 4.6, 5.6, 6.3 (Diameter)
3. Applications of Wire Wound Screens
Wire wound screens find applications in various industries where filtration is essential. Some common applications include:
- Water Treatment: Wire wound screens are widely used in water treatment plants to remove suspended solids, sediments, and impurities from the water supply. They are effective in filtering out particles of different sizes, ensuring clean and safe water for consumption or industrial processes.
- Oil and Gas Industry: Wire wound screens play a crucial role in the oil and gas industry, particularly in well completion and production processes. They are used as sand control screens, preventing sand and other solid particles from entering the production system and causing damage to equipment.
- Chemical and Pharmaceutical Industries: In chemical and pharmaceutical manufacturing processes, wire wound screens are utilized to filter out contaminants and ensure the purity of liquids or gases. They help maintain the quality and integrity of the final products, meeting stringent industry standards.
- Food and Beverage Industry: Wire wound screens are employed in the food and beverage industry for various filtration applications. They are used to remove impurities, particles, and debris from liquids, ensuring product quality and safety.
4. Benefits of Wire Wound Screens
Wire wound screens offer several benefits that make them a preferred choice in filtration systems:
- High Strength and Durability: The construction of wire wound screens using corrosion-resistant materials ensures long-lasting performance, even in harsh operating conditions.
- Easy Cleaning and Maintenance: The design of wire wound screens allows for easy cleaning and maintenance. They can be backwashed or cleaned using appropriate methods, ensuring continuous filtration efficiency.
- Customizable and Versatile: Wire wound screens can be customized to meet specific filtration requirements, including different wire sizes, winding patterns, and slot sizes. This versatility makes them suitable for a wide range of applications.
Conclusion
Wire wound screens, or filter pipes, are indispensable components in filtration systems across various industries. Their ability to efficiently remove impurities while allowing the desired liquid or gas to pass through makes them essential for achieving high filtration efficiency and maintaining product quality. With their durability, versatility, and customizable features, wire wound screens continue to play a vital role in enhancing filtration processes and contributing to the overall efficiency of industrial operations.