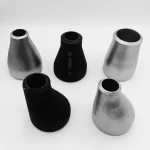
What is a reducer in piping, How to select reducer?
September 30, 2023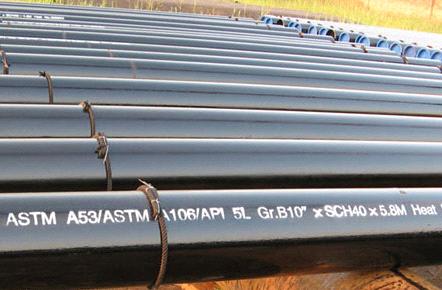
A53 Steel Pipe and Their Differences – A Comprehensive Study
October 8, 2023The Differences Between Induction pipe Bending and Steel Elbow Fittings
Introduction
In the realm of piping systems, the need to change direction is inevitable. For decades, this has been achieved through the use of elbow fittings or the process of pipe bending. As technology and manufacturing processes have evolved, new methods such as induction bending have become increasingly popular. This essay will delve into the differences between induction bending and steel elbow fittings, focusing on their applications, advantages, disadvantages, and the factors that influence the choice between the two.
Steel Elbow Fittings
A steel elbow fitting is a type of pipe fitting installed between two lengths of pipe to allow a change of direction. They are available in various shapes, but the most common types are 45°, 90°, and 180° elbows. Elbow fittings are typically made of steel and are designed to match the diameter and wall thickness of the pipes they are connecting.
Advantages
- Versatility: Steel elbow fittings are available in a wide range of sizes, angles, and wall thicknesses, making them suitable for various applications.
- Ease of Installation: Elbow fittings are simple to install and require minimal labor.
- Leak-Proof Design: When properly installed, steel elbow fittings provide a leak-proof change in direction.
Disadvantages
- Disruptions in Flow: The sharp bends in elbow fittings can cause disruptions in fluid flow, leading to pressure drops and potential erosion over time.
- Limited Flexibility: The angle of the elbow fitting is fixed, limiting the flexibility in designing pipe routes.
Induction Bending
Induction pipe bending, also known as hot bending or heat induction bending, is a process whereby heat is applied to a specific section of a pipe, making it malleable, and then bending it to the desired angle. The heat is usually supplied by an induction coil, which heats the pipe section to a temperature where it can be reshaped without compromising its structural integrity.
Induction pipe Bending radius: 3D bend, 5D bend, 6D, 8D and customized
Bending degree: 15°, 22.5°, 30°, 45°, 60°, 90°, 180° and customized
3D Bend
3D bend radius in 3D, means the bend radius is 3 times of pipe outside diameter. For example if a 3D bend used in a 10 inch pipelines, the bend radius would be 30 inches,.
5D Bend
5D bend means the bend radius is 5 times of pipe nominal diameter. It provides better smooth performance to change pipeline direction than 3D bend.
Large Diameter Pipe Bend / Bending
Steel pipe bending usually required in large diameter in oil and gas pipelines, since it has better capacity to transport the material, and long pipelines will need different radius of pipe bends to be intalled in complex conditions.
Short description:
Name | Seamless & Welded Pipe Bends |
Types | Induction pipe bending |
welded | |
Seamless | |
Material | Stainless steel: A403 WP304/TP304, WP304L/TP304L,WP316/TP316, WP316L/TP316L, WP321/TP321, WP310/TP310 etc Carbon steel: ASTM A234 GR WPB, WPC, ST37.2, ST35.8, API 5L GR/B, API 5L X42/X52/X60/X65/70 Alloy steel: WP11, WP22, WP12, WP5, WP9, WP91 |
Stainless steel: A182 F304, A182F304L,A182 F316, A182 F316L, A182 F321, A182 317H, A182316Ti, F53,F51 Carbon steel: A105, A350LF2 Alloy steel: A182 F11, A182F22, A182F12,A182 F5, A182F91, A182 F9, A420 WPL6, A860 WHPY42/52/62/65/70/80 etc |
|
Standards | ASTM A234 WPB ANSI B16.9/ ANSI B16.28 MSS SP43/MSS SP75 JIS2311/JIS2312/JIS2313 DIN2605 GB-12459/GB-T13401 |
Sizes | 1/2″-36″ seamless, 8″-110″ welded, |
Angle | 15°, 22.5°, 30°, 45°, 60°, 90°, 180° or custom as customer`s requirement |
Bending | 1D-10D |
Wall thickness | STD, XS, XXS, SCH10,SCH20,SCH30,SCH40, SCH60, SCH80, SCH160 |
Surface | Black painting, Color painting Galvanized, Epoxy coated, 3PE, FBE etc and others as requirement |
Advantages
- Smooth Bends: Induction bending creates smooth, continuous bends that minimize disruptions to fluid flow, resulting in less pressure drop and reduced risk of erosion.
- Versatility: The bend angle and radius are highly customizable, offering greater flexibility in pipe route design.
- Strength and Integrity: Since the pipe’s original cross-sectional shape and wall thickness are preserved throughout the bend, the strength and integrity of the pipe are maintained.
Disadvantages
- Complex Process: Induction bending is a more complex process than installing an elbow fitting and requires specialized equipment and skilled operators.
- Cost: The initial cost of induction bending can be higher than using elbow fittings, particularly for small projects.
Differences Between Induction Bending and Steel Elbow Fittings
The primary differences between induction bending and steel elbow fittings lie in their manufacturing techniques, versatility, impact on fluid flow, and cost.
Manufacturing Techniques
Steel elbow fittings are prefabricated components, manufactured separately and then attached to the pipe system. On the other hand, induction bending is a process applied directly to the pipe, reshaping a specific section while maintaining the pipe’s continuous length.
Versatility
While both methods provide a range of angles, induction bending offers greater flexibility in terms of bend radius. This can be an important consideration in pipe route design, particularly in constrained spaces.
Impact on Fluid Flow
The smooth, gradual bends created through induction bending cause less disruption to fluid flow compared to the sharp bends of elbow fittings. This can result in better system performance and longevity.
Cost
For smaller projects, steel elbow fittings may be more cost-effective due to their lower upfront cost and ease of installation. However, for larger projects or those requiring custom angles or large-radius bends, the advantages of induction bending can outweigh the initial cost.
Conclusion
The choice between induction bending and steel elbow fittings depends on several factors, including the project size, budget, design requirements, and desired system performance. Steel elbow fittings, with their ease of use and lower upfront cost, may be suitable for smaller or simpler projects. In contrast, induction bending, with its versatility and superior performance characteristics, may be the better choice for larger projects or those with more complex design requirements. By understanding the differences between these two methods, engineers and designers can make more informed decisions, optimizing the balance between cost, ease of installation, system performance, and longevity.