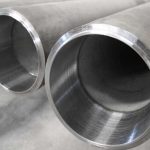
Mechanically Lined Pipes: A Comprehensive Guide
January 11, 2024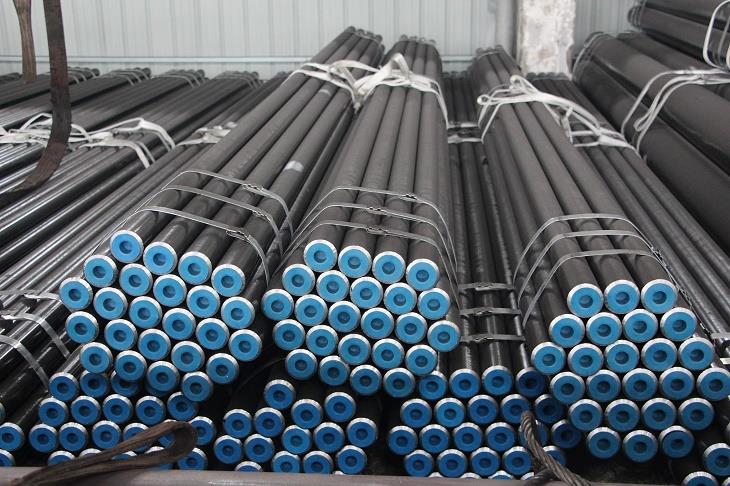
BOILER TUBES for MOROCCO Power Stations
January 15, 2024The Advantages and Applications of Induction Bending Pipe in the Oil and Gas Industry
Introduction
In the oil and gas industry, there is a constant need for efficient and reliable piping systems that can transport fluids over long distances. One method of achieving this is through the use of induction bending pipe. Induction bending is a specialized process that allows for the bending of pipes without the need for mechanical force or the use of multiple fittings. In this article, we will explore the advantages and applications of induction bending pipe in the oil and gas industry.
Advantages of Induction Bending Pipe
1. Smooth Flow
One of the key advantages of induction bending pipe is that it provides a smooth flow path for fluids. The bending process ensures that there are no sharp corners or abrupt changes in direction, which can cause turbulence and increase pressure drop. This smooth flow path allows for efficient fluid transportation and reduces the risk of erosion and corrosion within the pipe.
2. Reduced Welding and Fitting Requirements
Induction bending pipe eliminates the need for multiple fittings and welds that are typically required in traditional pipe bending methods. This not only reduces the overall cost of the piping system but also minimizes the potential points of failure. With fewer welds and fittings, there is a lower risk of leaks and structural weaknesses, resulting in a more reliable and durable piping system.
3. Improved Structural Integrity
Induction bending pipe maintains the structural integrity of the pipe throughout the bending process. The use of induction heating allows for precise control over the temperature distribution, ensuring that the pipe remains within its elastic limits. This prevents the formation of cracks or deformations that could compromise the strength and performance of the pipe.
4. Versatility in Design
Induction bending pipe offers a high degree of design flexibility. It can accommodate various bending radii and angles, allowing for the creation of complex piping configurations. This versatility is particularly beneficial in projects that require customized solutions, such as offshore platforms or pipeline systems with challenging terrain. Induction bending pipe enables engineers to optimize the design for maximum efficiency and functionality.
5. Time and Cost Savings
By eliminating the need for multiple fittings and welds, induction bending pipe reduces the overall installation time and cost. The bending process is faster and more efficient compared to traditional methods, resulting in shorter project timelines and reduced labor costs. Additionally, the reduced number of fittings and welds lowers the material and maintenance expenses over the lifetime of the piping system.
Materials for Induction Bending Pipe
1. Carbon Steel
Carbon steel is a commonly used material for induction bending pipe. It offers excellent strength and durability, making it suitable for various applications in the oil and gas industry. The carbon steel used for induction bending pipe complies with standards such as API 5L, ASME B16.49, and EN 10218. These standards ensure the quality and performance of the carbon steel pipes.
2. Alloy Steel
Alloy steel is another material option for induction bending pipe. It is made by adding different alloying elements to carbon steel, enhancing its mechanical properties and corrosion resistance. Alloy steel pipes for induction bending are typically manufactured according to ASTM A234 standards. The use of alloy steel allows for greater flexibility in designing and constructing complex piping systems.
3. Stainless Steel
Stainless steel is a popular choice for induction bending pipe due to its excellent corrosion resistance and aesthetic appeal. It is commonly used in industries where hygiene and cleanliness are crucial, such as food processing and pharmaceuticals. Stainless steel pipes for induction bending are manufactured according to ASTM 312/403 standards, with various grades available, including 304/304L, 316/316L, 613Ti, 321, 317L, and 310S.
Specifications of Induction Bending Pipe
Induction bending pipe is available in a wide range of specifications to meet different project requirements. The specifications include:
1. Nominal Pipe Size (NPS) and Diameter Nominal (DN)
Induction bending pipe can be produced in various sizes, ranging from 1/2” to 72” for NPS and from 15 to 1800 for DN. This allows for flexibility in designing and constructing piping systems of different scales.
2. Wall Thickness (WT) and Schedule
The wall thickness of induction bending pipe is specified based on the project requirements. It can be less than 120mm, with common schedules including SCH 40, SCH 80, and XXS. The wall thickness determines the strength and durability of the pipe, ensuring its ability to withstand the operating conditions.
3. Bend Radius
The bend radius refers to the radius of the curve created in the induction bending pipe. It is specified as a multiple of the pipe’s diameter (D). Common bend radii include 2.5D, 3D, 4D, 5D, 6D, 7D, 8D, 9D, and 10D. The bend radius affects the flow characteristics of the pipe and the ease of installation in different applications.
4. Bend Angle
The bend angle specifies the degree of the curve created in the induction bending pipe. It can be 15, 30, 45, 60, 90, 135, or 180 degrees, depending on the project requirements. The bend angle determines the direction and orientation of the pipe, allowing for efficient fluid transportation and optimized space utilization.
Surface Coatings for Induction Bending Pipe
To enhance the performance and longevity of induction bending pipe, various surface coatings can be applied. These coatings provide protection against corrosion, abrasion, and other environmental factors. Common surface coatings for induction bending pipe include:
Applications of Induction Bending Pipe
1. Oil and Gas Pipelines
Induction bending pipe is widely used in the construction of oil and gas pipelines. These pipelines transport crude oil, natural gas, and other petroleum products over long distances. The smooth flow path provided by induction bending pipe minimizes pressure drop and ensures efficient fluid transportation. The ability to create customized bends allows for the pipeline to navigate challenging terrains and obstacles, such as mountains or rivers.
2. Offshore Platforms
Offshore platforms require piping systems that can withstand harsh environmental conditions, including strong winds, waves, and corrosive saltwater. Induction bending pipe is ideal for such applications due to its structural integrity and resistance to corrosion. It can be used to create bends and curves in the piping system, allowing for efficient routing and optimization of space on the platform.
3. Refineries and Petrochemical Plants
Refineries and petrochemical plants process crude oil and other raw materials into various petroleum products and chemicals. The piping systems within these facilities must be able to handle high temperatures, pressures, and corrosive substances. Induction bending pipe is well-suited for such environments, as it provides a smooth flow path, reduces the need for fittings and welds, and offers excellent structural integrity.
4. Power Generation
Power generation facilities, such as thermal power plants and nuclear power plants, rely on piping systems to transport steam, water, and other fluids. Induction bending pipe can be used in these applications to create bends and curves that optimize the routing of the piping system. This allows for efficient flow and minimizes pressure drop, resulting in improved energy efficiency and reduced operating costs.
5. Infrastructure Development
Induction bending pipe is also utilized in infrastructure development projects, such as bridges, tunnels, and underground transportation systems. These projects often require customized piping solutions to accommodate the unique design requirements and space constraints. Induction bending pipe enables the creation of bends and curves that fit seamlessly into the infrastructure, ensuring efficient fluid transportation and structural integrity.
Conclusion
Induction bending pipe offers numerous advantages in the oil and gas industry, including smooth flow, reduced welding and fitting requirements, improved structural integrity, design versatility, and time and cost savings. Its applications range from oil and gas pipelines to offshore platforms, refineries, power generation facilities, and infrastructure development projects. By utilizing induction bending pipe, companies can achieve efficient and reliable fluidtransportation, minimize pressure drop, and ensure the longevity of their piping systems. Whether it’s for transporting oil and gas over long distances or optimizing space on offshore platforms, induction bending pipe proves to be a valuable solution.
FAQ
1. How does induction bending pipe work?
Induction bending pipe utilizes the principle of electromagnetic induction to heat a specific section of the pipe. The heated section becomes malleable, allowing it to be bent to the desired angle or radius. This process eliminates the need for mechanical force and multiple fittings, resulting in a smoother flow path and improved structural integrity.
2. What are the advantages of induction bending pipe over traditional pipe bending methods?
Induction bending pipe offers several advantages over traditional pipe bending methods. It provides a smooth flow path, reduces the need for fittings and welds, improves structural integrity, offers design flexibility, and saves time and costs. These advantages make induction bending pipe a preferred choice in various industries, including oil and gas.
3. Can induction bending pipe be used in corrosive environments?
Yes, induction bending pipe is suitable for use in corrosive environments. It can be made from corrosion-resistant materials, such as stainless steel or corrosion-resistant alloys, to ensure longevity and durability. Additionally, the smooth flow path provided by induction bending pipe minimizes the risk of corrosion and erosion within the pipe.
4. Is induction bending pipe suitable for high-pressure applications?
Yes, induction bending pipe is suitable for high-pressure applications. The bending process does not compromise the structural integrity of the pipe, allowing it to withstand high pressures. By reducing the need for fittings and welds, induction bending pipe minimizes potential points of failure and ensures a reliable and durable piping system.
5. Can induction bending pipe be used in infrastructure development projects?
Yes, induction bending pipe is commonly used in infrastructure development projects. Its design versatility allows for customized bends and curves that fit seamlessly into bridges, tunnels, and underground transportation systems. This ensures efficient fluid transportation and structural integrity in these projects.
“Mastering the Art of Induction Bending Pipes: A Comprehensive Guide for Professionals”
“Exploring the Advantages and Applications of Induction Bending Pipes in Industrial Construction”
“Induction Bending Pipes: Unveiling the Key Techniques for Precise and Efficient Results”
“Enhancing Structural Integrity with Induction Bending Pipes: The Future of Pipeline Systems”
“Unlocking the Potential of Induction Bending Pipes: Achieving Smooth Curves and Seamless Joints”
“Induction Bending Pipes: How Heat and Precision Create Customized Solutions for Complex Projects”
“Optimizing Pipeline Design with Induction Bending Pipes: Ensuring Efficiency and Safety”
“Maximizing Efficiency and Cost Savings with Induction Bending Pipes in Industrial Applications”
“Innovation in Pipe Manufacturing: Harnessing the Power of Induction Bending Technology”
“From Theory to Practice: Mastering the Techniques of Induction Bending Pipes for Success”