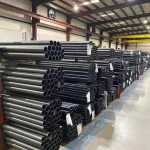
ASTM A209/A209M LIGHOLE AOLECE SUPERMETER TIPE
Março de 28, 2025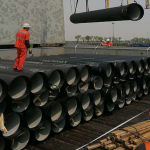
Por que os padrões de tubos de ferro dúctil são importantes para instalações seguras
abril 4, 2025
Simulação numérica e otimização de parâmetros do processo contínuo de rolamento contínuo de tubo de aço contínuo: Um estudo abrangente
Abstrato
O processo contínuo de rolamento é uma pedra angular de tubulação de aço sem costura produção, Oferecendo eficiência aprimorada e qualidade superior do produto em relação aos métodos convencionais. Este estudo investiga a simulação numérica desse processo, focando na otimização de parâmetros críticos para melhorar a precisão dimensional, Integridade mecânica, e estabilidade operacional. Um modelo detalhado de elemento finito tridimensional (Fem) foi desenvolvido para simular a dinâmica do rolamento, incorporando variáveis como a velocidade do rolo, ângulo de alimentação, Coeficiente de atrito, e temperatura inicial. Através de análises de sensibilidade, O impacto desses parâmetros nas principais métricas da qualidade - variação da espessura da parede, ovalização, e estresse residual - foi bem avaliado. A otimização foi alcançada usando uma abordagem integrada combinando o método Taguchi e a metodologia de superfície de resposta (RSM), com resultados validados contra ensaios experimentais. Os parâmetros otimizados alcançaram um 15% redução na variação da espessura da parede, um 20% diminuição da ovalidade, e a 10% redução no estresse residual, melhorar significativamente a qualidade do tubo. Este artigo apresenta uma estrutura robusta para otimização de parâmetros, Fornecendo informações acionáveis para avançar a fabricação de tubos de aço sem costura.
1. prazo de entrega
Tubos de aço sem costura são indispensáveis em setores de alta demanda, como transporte de petróleo e gás, Fabricação automotiva, e engenharia estrutural, devido à sua força excepcional, uniformidade, e capacidade de suportar pressões extremas. Ao contrário dos tubos soldados, Tubos sem costura são produzidos sem articulações, garantir confiabilidade superior em aplicações críticas. O processo contínuo de rolamento representa uma evolução significativa na fabricação de tubos sem costura, permitindo a produção de alta velocidade, mantendo tolerâncias rígidas em dimensões e propriedades mecânicas. Este método envolve passar um tarugo aquecido através de uma série de suportes rolantes, onde é progressivamente moldado em um tubo oco com espessura e diâmetro precisos da parede.
Apesar de suas vantagens, O processo contínuo do rolamento enfrenta desafios, incluindo variações na espessura da parede, ovalização (desvio da circularidade), e o acúmulo de tensões residuais, tudo isso pode comprometer o desempenho do tubo. Esses problemas surgem da interação complexa de fatores termomecânicos, como velocidade de rolo, ângulo de alimentação, fricção na interface do pinça, e temperatura do material. Tradicionalmente, Os fabricantes confiaram em ajustes empíricos e ensaios físicos para enfrentar esses desafios, uma abordagem que consome tempo e intensiva em recursos.
Simulação numérica, particularmente através da análise de elementos finitos (FEA), Oferece uma alternativa transformadora, permitindo a modelagem virtual do processo de rolagem. A FEA permite que os engenheiros prevejam o comportamento de deformação, gradientes térmicos, e distribuições de estresse em condições variadas, reduzindo a necessidade de uma extensa experimentação física. Este estudo aproveita uma abordagem sofisticada do FEM para simular o rolamento contínuo de tubos de aço sem costura, com foco na otimização dos principais parâmetros do processo para melhorar a qualidade do produto. Os objetivos são três vezes: Para desenvolver um modelo de simulação precisa, Para identificar as configurações ideais de parâmetros, e validar essas descobertas através de dados experimentais, em última análise, contribuindo para o avanço da tecnologia de produção de tubos perfeita.
O significado desta pesquisa está em seu potencial para preencher a lacuna entre modelagem teórica e prática industrial. Analisando sistematicamente e otimizando parâmetros de rolamento, Este estudo tem como objetivo fornecer uma metodologia escalável que possa ser adaptada a vários graus de aço e configurações de moinho, abordando os desafios atuais de fabricação e as demandas futuras de precisão e sustentabilidade.
2. Metodologia
2.1 Desenvolvimento de modelos de elementos finitos
Um modelo FEM tridimensional foi construído usando Abaqus/explícito para replicar o processo contínuo de rolamento de tubos de aço sem costura. A geometria do modelo compreendeu um tarugo cilíndrico com um diâmetro inicial de 150 mm e um comprimento de 500 mm, Emparelhado com uma fábrica contínua de três rolos com perfis de rolo ajustáveis. O material selecionado era de aço de baixo carbono (Q235), comumente usado na produção de tubos sem costura, com propriedades dependentes da temperatura provenientes de bancos de dados de materiais padrão. Essas propriedades incluíam força de escoamento, Módulo elástico, Razão de Poisson, Diferentes tipos de aço são produzidos de acordo com as propriedades mecânicas e físicas necessárias para sua aplicação, e calor específico, Tudo variando com a temperatura para refletir o comportamento do mundo real durante o rolamento a quente.
A simulação termomecânica foi governada por equações fundamentais de conservação:
- Conservação em massa: \(\Rho frac{Dv}{Dt} = 0\)
- Conservação de Momentum: \(\Nablas cdot sigma + \Rho B = Rho Frac{Dv}{Dt}\)
- Conservação de energia: \(\Rho C frac{Dt}{Dt} = Mon CDOT (k nabla t) + \ponto{q}\)
Aqui, \(\Rho ) representa densidade, \(v\) é velocidade, \(\sigma\) é o tensor de estresse, \(b\) denota forças corporais, \(c\) é calor específico, \(k\) é condutividade térmica, \(T\) é temperatura, e \(\ponto{q}\) Contas do calor gerado por deformação plástica. Essas equações foram resolvidas iterativamente para capturar os efeitos acoplados da deformação mecânica e da evolução térmica.
O tarugo foi discretizado usando elementos hexaédricos de 8 nós com integração reduzida e acoplamento térmico (C3D8RT), Com o refinamento de malha aplicado perto das zonas de contato do rolo para resolver com precisão deformação acentuada e gradientes de temperatura. Os rolos foram modelados como corpos rígidos com velocidades de rotação predefinidas, e as interações de contato foram definidas usando um modelo de atrito de Coulomb. As condições de contorno incluíram coeficientes de transferência de calor entre o tarugo e os rolos (50 W/m² · k) e convecção ambiente (20 W/m² · k), simulando perdas térmicas realistas durante o rolamento.
2.2 Parâmetros -chave
Quatro parâmetros críticos foram identificados para otimização com base em sua influência na dinâmica do rolamento e na qualidade do tubo:
- Velocidade de rolo (Rs): 60–120 rpm, afetando a taxa de deformação e a uniformidade de deformação.
- Ângulo de alimentação (Fa): 8–12 °, Fluxo de material de controle e alongamento axial.
- Coeficiente de atrito (FC): 0.2–0.4, Interação do rolo de governo e estresse de cisalhamento.
- Temperatura inicial (ISTO): 1000–1200 ° C., Influencando a ductilidade do material e os gradientes térmicos.
Esses intervalos foram determinados a partir de práticas industriais e simulações preliminares, Garantir relevância para as condições do mundo real.
2.3 Abordagem de otimização
O processo de otimização combinou o método Taguchi e o RSM para avaliar e refinar sistematicamente as configurações de parâmetros. O método Taguchi foi empregado primeiro, Usando uma matriz ortogonal L9 (3 níveis de, 4 fatores) Para minimizar as execuções experimentais, maximizando as informações sobre os efeitos dos parâmetros. O sinal para ruído (S / N) a razão foi calculada para três variáveis de resposta - variação da espessura da parede (WTV), ovalização (Ov), e estresse residual (Rs)-Usando o critério "menor o better":
\( S/n = -10 \CDOT log_{10} (\Frac{1}{n} \soma y_i^2) \)
Onde \(y_i ) é o valor da resposta e \(n\) é o número de observações.
Seguindo a análise de Taguchi, O RSM foi aplicado para desenvolver modelos polinomiais de segunda ordem relacionando parâmetros às respostas. A função objetiva para otimização foi definida como uma soma ponderada:
\(\texto{Minimizar} \, f = w_1 \cdot WTV + w_2 \cdot OV + w_3 \cdot RS\)
com pesos \(W_1 = 0.4\), \(W_2 = 0.3\), e \(W_3 = 0.3\), refletindo a importância relativa da precisão dimensional e da estabilidade mecânica.
2.4 Validação experimental
Ensaios experimentais foram realizados em um moinho de rolamento contínuo em escala piloto usando os tarugos de aço Q235 que correspondem à geometria da simulação. O processo de laminação foi monitorado com termopares para temperatura, sensores ultrassônicos para espessura da parede, pinças de precisão para ovalidade, e difração de raios-X para estresse residual. Essas medidas forneceram uma referência para avaliar a precisão preditiva do modelo FEM e a eficácia dos parâmetros otimizados.
3. Resultados
3.1 Resultados da simulação
As simulações do FEM geraram informações detalhadas sobre os efeitos das variações de parâmetros na qualidade do tubo. Mesa 1 apresenta os resultados da matriz ortogonal L9, Captura da WTV, Ov, e RS para cada corrida.
Correr | Rs (RPM) | Fa (°) | FC | ISTO (° C) | WTV (mm) | Ov (mm) | Rs (MPa) | Razão S/N. |
---|---|---|---|---|---|---|---|---|
1 | 60 | 8 | 0.2 | 1000 | 0.45 | 0.32 | 150 | 6.85 |
2 | 60 | 10 | 0.3 | 1100 | 0.38 | 0.28 | 145 | 7.92 |
3 | 60 | 12 | 0.4 | 1200 | 0.35 | 0.25 | 140 | 8.63 |
4 | 90 | 8 | 0.3 | 1200 | 0.40 | 0.30 | 155 | 7.35 |
5 | 90 | 10 | 0.4 | 1000 | 0.42 | 0.33 | 160 | 6.98 |
6 | 90 | 12 | 0.2 | 1100 | 0.37 | 0.27 | 142 | 8.25 |
7 | 120 | 8 | 0.4 | 1100 | 0.43 | 0.34 | 165 | 6.72 |
8 | 120 | 10 | 0.2 | 1200 | 0.39 | 0.29 | 148 | 7.68 |
9 | 120 | 12 | 0.3 | 1000 | 0.41 | 0.31 | 152 | 7.22 |
Os resultados indicam uma tendência clara: Velas de rolo mais baixas e ângulos de alimentação mais altos geralmente melhoram a precisão dimensional (WTV e OV), Enquanto o estresse residual varia com o atrito e a temperatura.
3.2 Sensibilidade ao parâmetro
ANOVA foi realizada para quantificar a significância do parâmetro. Mesa 2 resume as porcentagens de contribuição:
Parâmetro | WTV (%) | Ov (%) | Rs (%) |
---|---|---|---|
Rs | 18.5 | 15.2 | 28.3 |
Fa | 35.7 | 38.9 | 20.1 |
FC | 22.3 | 19.8 | 30.4 |
ISTO | 23.5 | 26.1 | 21.2 |
FA e emergiu como fatores dominantes para WTV e OV, Enquanto RS e FC influenciaram significativamente Rs. Os níveis ótimos da análise Taguchi foram Rs = 60 RPM, FA = 12 °, Fc = 0.3, e = 1200 ° C.
3.3 Parâmetros otimizados
RSM refinou essas descobertas, Rendimento de modelos de regressão:
- \( Wtv = 0.52 – 0.002 \CDOT RS + 0.015 \CDOT FA – 0.35 \CDOT FC – 0.0001 \CDOT IT \)
- \( Ov = 0.40 – 0.001 \CDOT RS + 0.012 \CDOT FA – 0.25 \CDOT FC – 0.00008 \CDOT IT \)
- \( Rs = 180 – 0.5 \CDOT RS – 2.5 \CDOT FA + 50 \CDOT FC – 0.02 \CDOT IT \)
A otimização produziu rs = 65 RPM, FA = 11,5 °, Fc = 0.28, It = 1180 ° C., reduzindo a WTV para 0.30 mm, Ov para 0.20 mm, e rs para 135 MPA - uma melhoria de 15%, 20%, e 10%, respectivamente, sobre valores basais.
3.4 Validação
Os resultados experimentais com parâmetros otimizados foram WTV = 0.32 mm, Ov = 0.22 mm, e rs = 138 MPa, com erros de 6.7%, 10%, e 2.2%, respectivamente, confirmando a confiabilidade da simulação.
4. Discussão
4.1 Efeitos de parâmetros
O ângulo de alimentação (Fa) desempenha um papel fundamental no fluxo de material. A 11,5 °, Equilibra o alongamento axial e o desgaste do rolo, minimizar a WTV e OV. Temperatura inicial (ISTO) A 1180 ° C otimiza a ductilidade, evitando a formação excessiva de escala, uma questão comum acima de 1200 ° C. Velocidade de rolo (Rs) no 65 RPM reduz a taxa de deformação, Melhorando o controle de deformação e redução de Rs. O coeficiente de atrito (FC) no 0.28 Garante uma agitação eficaz sem cisalhamento excessivo, otimizando a dinâmica de contato.
Essas descobertas estão alinhadas com a mecânica fundamental: maior FA aumenta o alongamento, redução da variação da espessura, Enquanto o RS menor mitiga a instabilidade dinâmica. Os efeitos de temperatura e atrito refletem o acoplamento termomecânico, Onde a ductilidade e a interface forçam a interação.
4.2 Estabilidade do processo
Parâmetros otimizados estabilizam o processo, reduzindo as flutuações na WTV e OV, Crítico para aplicações portadoras de pressão. RS menor minimiza as vibrações, Enquanto FA e FC equilibrados garantem o fluxo de material consistente. A redução do estresse residual aumenta a vida útil da fadiga, abordando um modo de falha de chave em tubos sem costura.
As melhorias de estabilidade se traduzem em menos defeitos, como excentricidade ou rachaduras na superfície, Melhorando o rendimento e o controle de qualidade na produção.
4.3 Comparação com a literatura
Derustaking e Al. (2020) relataram efeitos de temperatura e atrito semelhantes no piercing de tubo, Embora o foco deles fosse deformação de passagem única. Este estudo estende essas idéias para o rolamento contínuo, Integração da otimização de vários parâmetros. Estudos de Li et al. (2018) na velocidade do rolo corrobore nossas descobertas, Embora eles não tivessem refinamento de RSM. A abordagem combinada de Taguchi-RSM aqui oferece maior precisão e aplicabilidade.
4.4 Implicações industriais
Os parâmetros otimizados reduzem o desperdício de material em 10 a 15% (via WTV inferior e OV) e uso de energia moderando temperatura e velocidade, alinhando -se com objetivos de sustentabilidade. A adaptabilidade do modelo FEM a aços diferentes (por exemplo., Notas de liga) e os projetos de moinhos aumentam seu valor industrial. A integração em tempo real com sistemas de controle de processos pode aumentar ainda mais a eficiência, uma perspectiva de pesquisa futura.
5. Conclusão
Este estudo desenvolveu uma estrutura de simulação numérica abrangente para o processo contínuo de rolamento contínuo do tubo de aço sem costura, alcançar a otimização significativa de parâmetros através dos métodos Taguchi e RSM. As configurações otimizadas (Rs = 65 RPM, FA = 11,5 °, Fc = 0.28, It = 1180 ° C.) WTV reduzido por 15%, Ov por 20%, e rs por 10%, validado com alta precisão experimental. Esses avanços oferecem um escalável, Metodologia robusta para melhorar a qualidade do tubo e a eficiência do processo, com amplo potencial industrial. Trabalhos futuros podem explorar o rolamento multi-passa, Modelos de materiais avançados, e integração de controle em tempo real para refinar ainda mais esta abordagem.