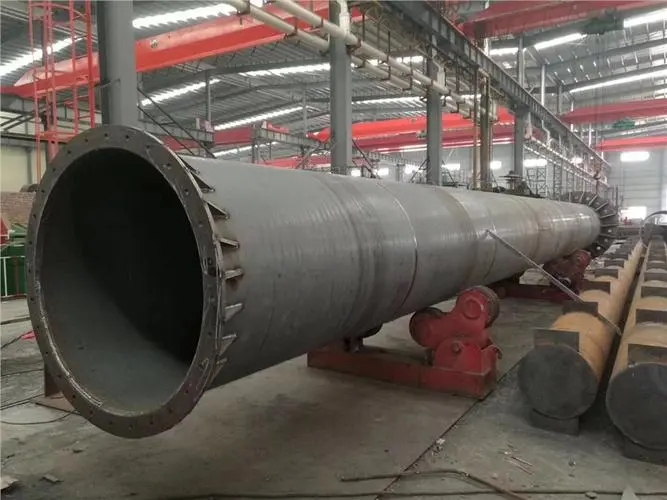
Como ocorre o desgaste nos tubos e por que o aço resistente ao desgaste de alta resistência supera o desempenho do tubo de aço comum em ambientes abrasivos
Junho 21, 2022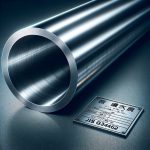
Conhecimento básico e usos de tubos de aço sem costura, invólucros e tubos de óleo
Junho 23, 2022Reduzindo a quantidade de variação, ou alcançar mais consistência de espessura de parede, pode ser a diferença entre atender aos requisitos de um cliente ou não. Também ajuda a reduzir ou até mesmo eliminar a necessidade do cliente de processos subsequentes, como usinagem.
O tubo sem costura normalmente é fabricado em um moinho perfurador de dois rolos. Em alguns casos, esta etapa por si só é suficiente para produzir tubos que satisfaçam os requisitos do cliente. No entanto, se a consistência da espessura da parede precisar de melhorias adicionais após a perfuração, um produtor de tubos pode usar equipamentos adicionais e etapas do processo. Dois desses tipos de equipamentos são um laminador alongador de laminação cruzada (comumente conhecido por seu nome comercial, como um moinho Assel ou Diescher), e um banco de estiramento a frio.
Visão geral das três etapas do processo
A fabricação de tubos sem costura geralmente começa com laminação cruzada a quente em um moinho perfurador. A perfuração é a primeira etapa do processo para fazer um tubo com uma parede de alta qualidade. Esta etapa geralmente é seguida por um ou mais processos de alongamento que podem melhorar a qualidade da parede e, ao mesmo tempo, aumentar o comprimento do tubo. Depois que o tubo sai do moinho sem costura e esfria, pode ser finalizado em uma bancada de estiragem a frio como o terceiro passo para melhorar as tolerâncias da parede.
Moinho de Perfuração. A maior atenção sobre a qualidade da parede sem costura é direcionada ao moinho perfurador. Essa atenção se justifica porque o moinho perfurador tem o maior efeito na variação da parede. A tubulação produzida por um moinho perfurador pode ser otimizada para 7 Para 10 variação percentual da parede.
Embora uma concha perfurada possa ter menos de 10 variação percentual da parede, esta quantidade de variação é para uma seção de parede relativamente espessa. Por exemplo, alcançar ±10 por cento de tolerância de parede produz um tubo com uma espessura de parede de 13.5 mm (0.531 no.) Para 16.5 mm (0.650 no.) ou mais quando encomendado em 15 mm (0.590 no.). Processamento adicional por um moinho alongador pode ser necessário para requisitos mais rigorosos do cliente.
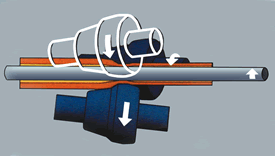
O processo de laminação cruzada usa três rolos de trabalho para reduzir o diâmetro externo do tubo e a espessura da parede. Desenho cortesia de Copperweld, Shelby, Ohio.
Moinho Alongador. Cinco tipos principais de moinhos alongadores são usados na indústria de produção de tubos: o moinho de tubos de mandril, o banco de empurrar, o moinho de plugue, o moinho redutor de estiramento, e o moinho alongador de laminação cruzada. Cinquenta anos de uso em toda a indústria mostraram que, desses moinhos alongadores, o alongador de laminação cruzada fornece a melhoria mais significativa na tolerância da parede do tubo produzido em um moinho perfurador. Um laminador alongador de laminação cruzada usa rolos de trabalho no OD e um mandril no ID (Ver Figura 1).
Banco de Tiragem a Frio. O desenho em uma bancada é um método de acabamento a frio que melhora a dimensão da parede do tubo sem costura. No processo de banco de sorteio, primeiro o tubo é frouxamente rosqueado em um mandril preso a uma haste. Em seguida, um conjunto de alicate prende o tubo e o puxa através de uma matriz estacionária de metal duro ou aço ferramenta. O resultado é um tubo personalizado com muito bom controle dimensional. A tolerância OD típica é de ±0,1 mm (±0,004 pol.), que é aproximadamente um décimo da tolerância de um tubo sem costura acabado a quente típico.
Benefícios adicionais do processo de desenho incluem acabamento de superfície aprimorado, a capacidade de fornecer tolerâncias de ID, e propriedades mecânicas melhoradas. Tubos produzidos com este processo requerem processamento mínimo ou adicional e são considerados produtos de valor agregado.
Diretrizes para alongamento de rolo cruzado
Para alongamento de laminação cruzada, dois requisitos principais dizem respeito à casca perfurada. Estes estão enchendo a seção de altura da corcunda para 80 Para 90 por cento de seu design e maximizando a aderência lateral de entrada. Ambos os requisitos estão relacionados ao projeto do passe de rolo na fábrica de Assel.3
Figura 2
A saliência do rolo está localizada perto do meio do rolo de trabalho. É importante combinar a seção do tubo que entra no moinho com as características de design dos cilindros de trabalho. Desenho cortesia de Copperweld, Shelby, Ohio.
Enchendo o bumbum. Hump é um termo geral para a região próxima ao meio do rolo de trabalho que contém um perfil elevado (Ver Figura 2). Preencher a corcova é uma questão de medir a parede perfurada e depois compará-la com a dimensão conhecida da corcova da impressão. O moinho perfurador é então ajustado para obter o valor adequado. Por exemplo, se o desenho da corcunda for 8 mm (0.315 no.), a casca perfurada deve medir 7 mm (0.276 no.) mais do que o tamanho do cliente (Porque 7 é 90 por cento de 8).
Essa relação é importante na produção de tubos de parede fina porque a tolerância da parede para tubos mecânicos é baseada em porcentagem (por padrão ASTM A519). Tolerâncias para tubos de paredes mais finas são mais difíceis de alcançar porque, por exemplo, 5 por cento de 5 mm (0.197 no.) é uma dimensão muito mais apertada do que 5 por cento de 10 mm (0.394 no.). Os produtores de tubos devem entender que, se a capacidade do moinho for 1 mm (0.040 no.) de variação de parede, isso pode representar metade da tolerância comercial para seções de parede média (valor Cp de 2.0) e variação fora da tolerância para seções de parede fina (Cp inferior a 1.0).
A casca do moinho perfurador precisa ser reduzida na espessura da parede para garantir o enchimento adequado da altura da corcunda. Para tubos de paredes extremamente finas, os fabricantes podem achar que a melhoria da qualidade no laminador cruzado pode ser difícil, se não impossível, porque a casca perfurada tem muita variação. Para alguns tamanhos de tubos, a variação da parede como porcentagem pode ser aumentada em vez de diminuída no moinho perfurador. A porcentagem de variação é determinada por um cálculo cuidadoso. Embora a variação dimensional total diminua o numerador, o denominador diminui a uma taxa maior porque o tubo do laminador de laminagem cruzada tem 50 Para 75 por cento menos espessura da parede do que o tubo do moinho perfurador.
Punho de rolamento cruzado. O segundo requisito é manter a melhor aderência no processo de laminação cruzada. A aderência é definida como o número de espirais do tubo antes da linha central da saliência no projeto da passagem do rolo do laminador alongador de laminação cruzada - em termos simples, a casca perfurada deve entrar em contato com a face do rolo no início do processo para que a alimentação do tubo seja estabelecida antes de encontrar a zona de trabalho na seção de corcunda. O trabalho realizado na seção da corcunda requer uma quantidade extrema de energia, até vários milhares de cavalos de potência. A força de trabalho é aplicada em uma seção muito curta, usualmente 15 Para 25 mm (menos de 1 no.) largo. Se o tubo não estiver preso corretamente, ele vai girar em vez de alimentar, ou pode alimentar irregularmente através da zona de trabalho, criando variação.
Na maioria dos casos, a melhor condição para a casca perfurada é alcançada produzindo o diâmetro externo máximo que se encaixará adequadamente na face do rolo do moinho de alongamento de laminação cruzada. Normalmente, essa relação é resolvida ajustando a configuração do moinho perfurador para produzir a dimensão correta do tubo. Mas, em alguns casos, pode ser necessário aumentar ou diminuir ligeiramente o ângulo divergente do moinho alongador para garantir que o casco se encaixe e prenda adequadamente.
Experimentos conduzidos na qualidade da parede de tubos retirados diretamente de um moinho alongador foram usados para determinar se os tubos tinham melhor qualidade de parede do que os tubos processados por um moinho de dimensionamento ou um moinho redutor de estiramento. Foi determinado que no processo de redução de dimensionamento, forças longitudinais e compressivas atuam na parede e podem aumentar a variação da parede. Os tubos retirados diretamente de um laminador alongador de laminação cruzada têm consistência de espessura de parede superior e melhor qualidade de superfície porque não são expostos às condições de laminação no laminador de dimensionamento. Tubos que passaram por um moinho de dimensionamento, Contudo, pode ter variação de parede reduzida por estiramento a frio em uma bancada de estiramento.
Diretrizes para Desenho a Frio
O sucesso no processamento de tubos sem costura trefilados a frio depende da manutenção da alta qualidade da parede do laminador a quente sem costura e da seleção adequada das ferramentas de bancada de trefilação a frio (conjuntos de mandril e matriz).
Três pontos principais que dizem respeito ao desenho do tubo perfurado são:
- Alguma redução da parede é necessária para garantir que o mandril morda contra a parede no início da extração e, em seguida, assente o mandril adequadamente no rolamento da matriz durante a extração. Se a parede de entrada for muito irregular ou muito clara, o mandril não avançará para o rolamento do molde, e o tubo resultante não terá boas tolerâncias para dimensões externas, dimensão interna, e espessura de parede.
- O desenho de bancada é limitado a um máximo 40 porcentagem de redução na área. Se a parede de entrada for muito pesada, pode fazer com que o metal falhe em vez de ceder durante o desenho, especialmente para aços de liga de endurecimento por trabalho.
- O desenho é um processo longitudinal. Existe um potencial limitado para corrigir a variação severa da parede longitudinal porque a matriz e o mandril flutuam livremente e seguirão a variação da parede em vez de corrigi-la.
A trefilação a frio pode ser otimizada selecionando o perfil de matriz mais apropriado (Ver Figura 3). Nenhum projeto único funciona melhor para todos os tubos sem costura porque o projeto depende de muitos fatores, como a espessura da parede, grau de aço, requisitos de redução de passe, e desenhar limitações de bancada.
Figura 3
Três principais perfis de matriz de trefilação a frio são raios, direto, e mistura reta/raio, ou combinação
Três perfis de matriz são:
- Matriz de raio - a entrada da matriz é um arco sem ângulos agudos ou superfícies planas.
- Matriz reta—a entrada da matriz tem uma, superfície angular, tipicamente 10 Para 20 graus por lado.
- Matriz combinada—a entrada da matriz combina superfícies planas e misturas de raio.
Para cada ordem de produção desenhada, um gráfico de controle estatístico ou método de teste t de Student pode ser preenchido e usado para otimizar o perfil da matriz e a dimensão da matriz como um registro permanente.
Para a maioria dos tubos sem costura, uma matriz de raio produz a melhor qualidade de parede. Porque a matriz de raio tem um perfil de entrada mais gradual e uma mistura suave na seção de rolamento, o desenho do tubo é mais consistente e resulta em dimensões de maior qualidade. Mas há uma desvantagem para este tipo de dado: Por causa do perfil de entrada gradual, apenas uma pequena redução de OD pode ser feita no tubo. O tubo sem costura deve ser personalizado para usar este tipo de matriz, adicionando despesas de mudança.
Alcançar a consistência de forma consistente
Alcançar a consistência requer analisar o processo para trás, do fim ao começo. A espessura da parede do produto acabado especificada pelo cliente fornece as dimensões finais para o tubo processado pela bancada de tração, que orienta a seleção da matriz e do mandril. Esta seleção determina o tamanho adequado da tubulação do moinho sem costura, que determina a configuração adequada e os parâmetros operacionais.