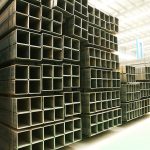
Hollow Section Rectangular and square Steel Pipe for structure
November 25, 2023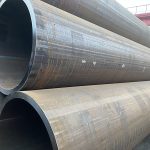
JCOE Welded Steel Pipe | JCOE UOE LSAW
November 26, 2023An Overview of Stainless Steel Pipe Grades and Their Properties
Stainless steels are highly valued for their versatility and durability across numerous applications. There are various grades of stainless steel, each optimized for specific usage scenarios in sectors including industrial, marine, construction, and transport. The table below provides an overview of some common options:
Alloy Group | UNS No. | Commonly Known As |
---|---|---|
Austenitic | S30100, S30400, S30403, S31600, S31603, S32100, S31000, S30815, N08904, S31254 | 301, 304, 304L, 316, 316L, 321, 310, 253MA, 904L, 254SMO or “6Mo” |
Ferritic | S40900, S41003, S43000, S43932, S44400 | 409, 3CR12 or 1.4003, 430, 439, 444 |
Martensitic | S41000, S42000, S43100, S44004 | 410, 420, 431, 440C |
Duplex | S32101, S32304, S32205, S32750, S32520 | 2101, 2304, 2205, 2507, UR2507Cu |
Precipitation Hardening | S17400, S17700, S15500 | 17-4PH or 630, 17-7PH or 631, 15-5PH |
When selecting a Stainless Steel Pipe for a particular application, the first step is determining which fundamental properties need to be prioritized. These can be broken down into five groups: austenitic, duplex, ferritic, martensitic, and precipitation hardening.
Here’s a brief overview of how different alloy groups and grades might be selected based on specific requirements:
- Corrosion resistance: The selection depends on the environment. Further discussion is required for precise selection.
- Heat resistance: Austenitic grades, particularly those high in chromium, often also with high silicon, nitrogen and rare earth elements (e.g., grades 310 and 253MA), are typically selected. Stabilized ferritics are used in less extreme conditions. High chromium ferritic grades have high oxidation resistance (e.g., 446), but have lower hot strength.
- Cryogenic (low temperature) resistance: Austenitic grades have excellent toughness at very low temperatures. No other stainless steels are suitable at very low temperatures.
- Magnetic response: Austenitic grades have low magnetic permeability; higher nickel grades (e.g., 316 or 310) are more likely to be non-magnetic if cold worked.
- High Strength: Martensitic and precipitation hardening grades are generally chosen. Duplex grades can also be useful. Cold worked austenitic grades also have high strength.
Stainless Steel Pipe Selection for Corrosion Resistance
Choosing the most cost-effective grade for a specific corrosive environment can be a complex task. A good strategy often involves considering what has been used before in similar environments, the service life of those materials, and their corrosion patterns.
General Corrosion Resistance
For environments such as strong acids where uniform general corrosion is the primary concern, there are published tables of recommended grades and iso-corrosion curves that provide expected corrosion rates. However, seemingly similar environments can have minor differences that significantly affect corrosion rates. For instance, even traces of chloride can be harmful.
Local Corrosion
Stainless steels often corrode due to local corrosion, mainly via mechanisms of pitting and crevice corrosion, which are largely controlled by the presence of chlorides in the environment, exacerbated by elevated temperature. The resistance of a specific Stainless Steel Pipe grade to pitting and crevice corrosion is indicated by its Pitting Resistance Equivalent number (PRE), which can be calculated as follows:
PRE = %Cr + 3.3 %Mo + 16 %N
Here, %Cr
represents the percentage of chromium, %Mo
the percentage of molybdenum, and %N
the percentage of nitrogen in the alloy. Higher PRE values indicate greater resistance to pitting and crevice corrosion.
“Super austenitic” grades (e.g., N08904 and S31254) with up to 6%Mo and “super duplex” grades (e.g., S32750 and S32520) with very high chromium, molybdenum, and nitrogen additions can resist more severe chloride-containing environments up to near boiling point.
“Tea staining” is a specific form of localized corrosion found in Stainless Steel Pipe items exposed to aggressive atmospheric environments, such as marine exposure. Grade selection, quality of finish, fabrication method, installation, and maintenance all play significant roles in mitigating this issue.
Stress Corrosion Cracking (SCC)
Common austenitic grades like 304 and 316 are prone to stress corrosion cracking (SCC), especially in chloride environments at temperatures over 60 degrees Celsius under tensile stress. Ferritic grades are nearly immune to this form of attack, and duplex grades are highly resistant. If SCC is a potential issue, a ferritic or duplex grade could be a prudent choice.
Stainless Steel Pipe Selection for Mechanical and Physical Properties
The selection of Stainless Steel Pipe often involves considering the desired corrosion resistance and the mechanical and physical properties of the metal. High strength martensitic grades (e.g., 431) and precipitation hardening grades (e.g., 630/17-4PH) are often chosen for applications such as shafts and valve spindles.
A high-strength duplex grade like 2205 might solve a corrosion issue while also contributing to cost-effectiveness due to its high strength. A ferritic grade like 3CR12 might provide adequate corrosion resistance for non-decorative applications and offer the advantage of less distortion from temperature changes due to its low coefficient of thermal expansion, similar to that of mild steel and 2/3 that of austenitic grades like 304.
Remember that the selection should always consider the mechanical and physical properties as early as possible in the process.
When selecting grades for corrosion resistance, it’s important to also consider how the product can be fabricated. This consideration greatly influences the economics of the product. Below is a comparison of some common grades and their relative fabrication characteristics. The comparisons are on arbitrary 1 to 10 scales, with 10 indicating excellent fabrication by the particular method.
Grade | Machinability | Weldability | Formability |
---|---|---|---|
303 | 10 | 2 | 5 |
304 | 5 | 8 | 8 |
316 | 5 | 8 | 7 |
3CR12 | 6 | 8 | 7 |
431 | 6 | 5 | 5 |
630/17-4PH | 5 | 7 | 5 |
It’s important to note there may be a trade-off between desirable properties. For instance, grade 303 has excellent machinability. However, the high sulfur content, which increases the cutting speed so dramatically, also substantially reduces the grade’s weldability, formability, and corrosion resistance. The calculated PRE for this grade does not factor in the negative effect of the sulfur, making it unsuitable for use in marine or other chloride environments.
Stainless Steel Pipe Selection for Cost
Cost can be viewed as the obvious $/kg or $/metre purchase price. However, this approach can provide a distorted short-term view. A more realistic approach is the “Total Cost of Ownership” (TCO) or “Life Cycle Cost” (LCC) view. This evaluates the cost to the asset owner over the required lifetime of the item. It factors in ongoing maintenance or replacement costs, potentially leading to a lower Total Cost of Ownership despite a higher initial purchase price.
For instance, the choice of Stainless Steel Pipe grade 301 for suburban rail cars ensures that the basic vehicle will survive without structural rust for the required life, measured in decades. The stainless panels will be cleanable, will require no painting, and structural members will not need costly regular inspections to validate integrity.
Another consideration is the choice between standard and special products. Standard products available from stockists’ shelves will usually be a lower cost than products that need to be specially manufactured. Designing based on standard stock items usually pays dividends. An exception to this is if the required quantity is large and the requirement has been planned well into the future – here a special product can be lower cost and also reduce fabrication costs.
Conclusion
Before selecting a grade of stainless steel, consider not only the required properties such as corrosion resistance, but also the secondary properties such as physical and mechanical properties, and the ease of fabrication. The correct choice will be rewarded not just by long, trouble-free life, but also by cost-effective fabrication and installation.