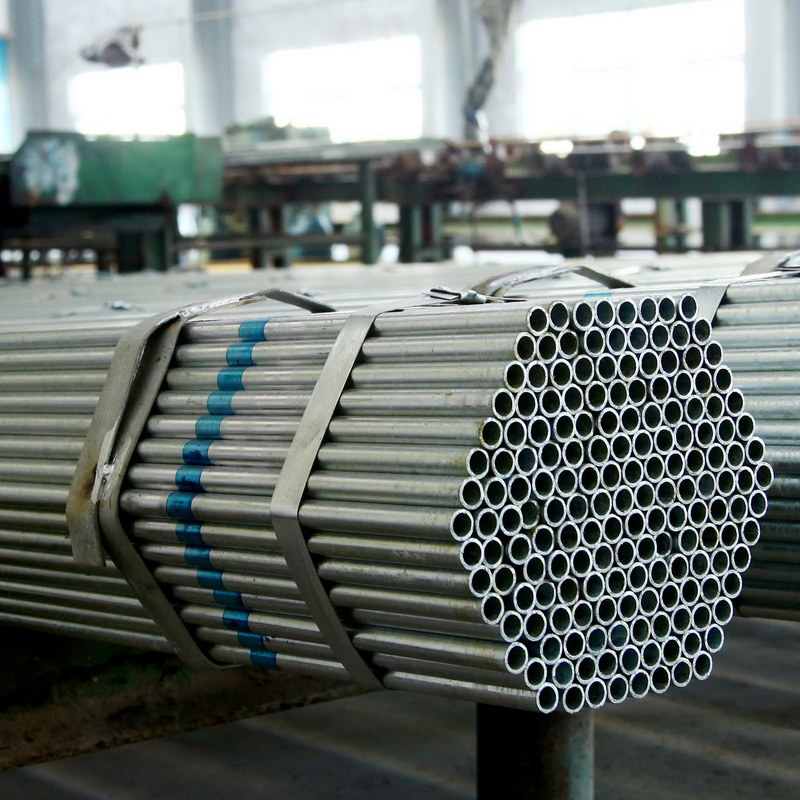
Why not galvanizing after welding for steel pipe
January 2, 2019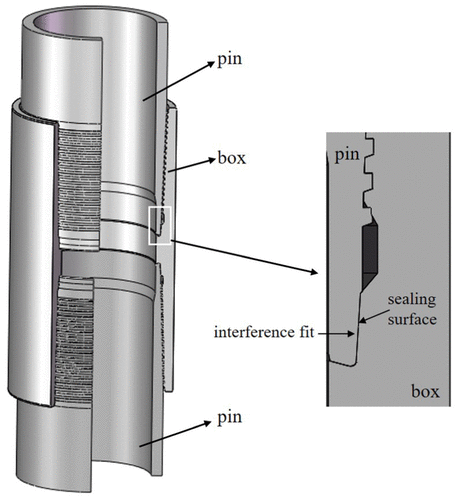
Casing pipe application in high-temperature gas wells
January 4, 2019Properties of Galvanized Steel Pipe Welds
Galvanizing has been used to protect iron and steel from rusting for over a hundred years in places as diverse as the wire rope used for the suspension cables on the Brooklyn Bridge to gutters on houses. Galvanizing is simply coating of zinc over steel. Like paint, galvanizing protects steel from rusting by forming a barrier between the steel and the environment, but galvanizing goes one giant step further than paint — it also provides electrochemical protection of the steel. Since zinc is electrochemically more reactive than steel, it oxidizes to protect the steel near it; as a result, even if a galvanized steel surface is scratched down to the bare steel, the galvanizing coating will prevent the steel from rusting. Galvanized steel is, therefore, a superior product to steel with any other type of coating on it since it protects the steel even when the coating is damaged in handling or in service.
The successful welding of Galvanized Steel Pipe is so widely accepted that there is very little recently-published mechanical property data comparing uncoated versus galvanized weld properties. The welding industry recognized fifty years ago that welds on Galvanized Steel Pipe and welds on uncoated steel are of comparable strength if the quality of the welds is comparable. Recent publications on welding Galvanized Steel Pipes deal with weld toughness, porosity control, weld appearance, restoring corrosion resistance and other issues that are much more complex than the strength of the weld.
When using SMAW (“stick”) welding, Galvanized Steel Pipe can be welded in the same manner as uncoated steel. When using MIG or flux cored welding, one may have to adjust the voltage slightly to control spatter, and one may have to clean the welding gun of spatter and zinc oxide deposits more frequently that when welding uncoated steel. Hobart makes a flux cored wire called “Galvacore” that some users have had good success with when welding Galvanized Steel Pipe.
When difficulty is encountered welding Galvanized Steel Pipe that was not encountered during welding uncoated steel, it is usually because the Welding Engineer has not accounted for the volume of gas that is evolved by the vaporization of zinc during welding. The thicker the zinc coating, the more fumes are generated, and those fumes have to be able to escape easily into the atmosphere and not be forced through the liquid weld metal.
For example, welding galvanized plates to form a T-joint is a commonly troublesome situation. Since the galvanized edge of one plate is butted against another galvanized surface, the zinc vapors that are formed at the abutting surfaces will not be able to escape to atmosphere easily as the zinc is vaporized. Instead, they will blow into the weld pool, creating porosity or a poor weld surface. This is aggravated when welding conventionally hot-dipped products, since the edges frequently have excessively heavy zinc coatings. One solution is to separate the parts by 1/16 inch using wire spacers or fixtures which will leave a gap for the zinc vapors to escape easily. Other approaches are to use a slight (15˚) bevel on one member (Figure 1), to remove the zinc from the faying surfaces by shearing or mechanically cuting the plate where the faying surfaces will meet, and to abrasively remove most of the zinc from one or both of the faying surfaces (Figure 2). Any of these methods will significantly reduce the amount of zinc between the parts, and this will reduce the volume of gas evolved, improving weld quality.