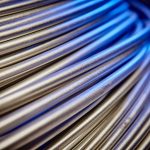
Inconel 601®เหล็กอัลลอยด์ | (UNS N06601, W.Nr. 2.4851)
เกี่ยวกับเรา 26, 2025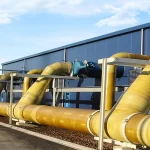
การออกแบบวัสดุสำหรับท่อหม้อไอน้ำแรงดันสูง 700 ℃
อาจ 6, 2025: กระบวนการเชื่อม, วัสดุ, และสิ่งแวดล้อม
ท่อเหล็กไร้รอยต่อเป็นวัสดุสำคัญที่มีการใช้งานที่กว้าง. เทคโนโลยีการเชื่อมสำหรับท่อเหล็กไร้รอยต่อเป็นปัจจัยสำคัญในการรับรอง ไปป์ไลน์ คุณภาพและประสิทธิภาพ. บทความนี้กล่าวถึงสิ่งจำเป็นของ ท่อเหล็กไร้รอยต่อ เทคโนโลยีการเชื่อมจากสี่มุมมอง: กระบวนการเชื่อม, วัสดุเชื่อม, สภาพแวดล้อมการเชื่อม, และการควบคุมคุณภาพ, ให้ข้อมูลอ้างอิงสำหรับผู้ปฏิบัติงาน.
1. กระบวนการเชื่อม
กระบวนการเชื่อมสำหรับท่อเหล็กที่ไร้รอยต่อจะต้องปฏิบัติตามมาตรฐานที่เกี่ยวข้อง, รวมถึงกระแสเชื่อม, แรงดันไฟฟ้า, ความเร็ว, และป้องกันก๊าซ. ก่อนที่จะเชื่อม, ควรตรวจสอบอุปกรณ์เพื่อให้แน่ใจว่าการทำงานปกติ; ในระหว่างการเชื่อม, ต้องมีการควบคุมเงื่อนไขอย่างเคร่งครัดเพื่อให้แน่ใจว่าคุณภาพของการเชื่อม; หลังจากเชื่อม, การตรวจสอบควรตรวจสอบการปฏิบัติตามมาตรฐาน.
วิธีการเชื่อมทั่วไปสำหรับท่อเหล็กที่ไร้รอยต่อรวมถึงการเชื่อมส่วนโค้งด้วยตนเอง, การเชื่อมแบบป้องกันแก๊ส, และการประสาน. วิธีการและพารามิเตอร์ที่เหมาะสมถูกเลือกตามวัสดุท่อ, เส้นผ่าศูนย์กลาง, ความหนาของผนัง, ประเภทร่อง, และตำแหน่งการเชื่อม. ด้านล่างนี้เป็นลักษณะและประเด็นสำคัญของวิธีการเหล่านี้.
1.1 การเชื่อมส่วนโค้งด้วยตนเอง
การเชื่อมอาร์คแบบแมนนวลเป็นวิธีที่ใช้กันอย่างแพร่หลายเหมาะสำหรับท่อเหล็กที่ไร้รอยต่อและรอยเชื่อม. ใช้งานง่าย, มีต้นทุนอุปกรณ์ต่ำ, และสามารถปรับตัวได้สูง. อย่างไรก็ตาม, มันมีข้อเสียเช่นคุณภาพการเชื่อมที่ไม่เสถียร, สปาสเตอร์ที่สำคัญ, การเสียรูปขนาดใหญ่, และความไวต่อความพรุนและรอยแตก.
ประเด็นสำคัญสำหรับการเชื่อมส่วนโค้งด้วยตนเอง:
-
การเลือกอิเล็กโทรด: เลือกอิเล็กโทรดตามวัสดุท่อ, ความหนา, ตำแหน่งเชื่อม, และพิมพ์. ขั้วไฟฟ้าไฮโดรเจนต่ำ (เช่น., J507, j507fe, E7018) โดยทั่วไปจะใช้, มีขนาดเส้นผ่าศูนย์กลางตั้งแต่ 2.5 มม. ถึง 5 มม. และกระแสเชื่อมจาก 80A ถึง 300A.
-
การเตรียมร่อง: สำหรับการเชื่อมก้น, จำเป็นต้องมีการเตรียมร่องหรือการเอียงที่เหมาะสม. ใช้ร่องรูปตัววีหรือรูปตัวฉันขึ้นอยู่กับความหนาของผนัง. พื้นผิวร่องจะต้องเรียบและสะอาด; ไม่ควรเชื่อมปลายท่อที่มีข้อบกพร่อง. ข้อกำหนดของร่อง:ความหนาของผนังประเภทร่องมุมร่องช่องว่างของร่อง≤6mmV60° ~ 70 °1~ 2 มม.>6มม.ผม30° ~ 40 °2~ 4mm
-
การจัดตำแหน่งท่อ: จัดตำแหน่งท่อโดยใช้การรองรับหรือรอกเพื่อให้แน่ใจว่าตำแหน่งที่อยู่ตรงกลางโดยไม่ต้องกระจัด. พื้นผิวด้านนอกจะต้องล้างออก, ตรวจสอบโดยใช้ไม้บรรทัดเหล็กที่ 200 มม. จากรอยเชื่อมบนพื้นผิวท่อตรงข้าม.
-
การเชื่อมตะปู: หลังการจัดตำแหน่ง, ทำการเชื่อมแทคกับความหนาที่ตรงกับชั้นเชื่อมแรก แต่ไม่เกิน 70% ของกำแพงความหนา:. รากเชื่อมจะต้องถูกเจาะอย่างเต็มที่, ด้วยรอยเชื่อมแทคเท่ากันและวางสมมาตร.
-
การเชื่อมชั้น: กำหนดจำนวนเลเยอร์เชื่อมและลำดับตามความหนาของผนังและเส้นผ่านศูนย์กลางอิเล็กโทรด. เชื่อมจากล่างขึ้นไปด้านบน, เริ่มต้นด้วยรูท, ตามด้วยชั้นฟิลเลอร์และหมวก. รักษาความเร็วการเชื่อมที่เหมาะสมและมุมอิเล็กโทรดสำหรับเครื่องแบบ, รอยเชื่อมที่ปราศจากข้อบกพร่อง. ทำความสะอาดตะกรันและสเปรย์ก่อนแต่ละชั้นและอนุญาตให้เย็นตามธรรมชาติ. การเริ่มต้นและจุดสิ้นสุดของอาร์คที่ซ้อนกันโดย 20 มม. หรือ 30 °.
1.2 การเชื่อมแบบป้องกันแก๊ส
การเชื่อมแบบป้องกันแก๊สใช้ก๊าซเฉื่อยหรือก๊าซที่ใช้งานอยู่เพื่อป้องกันส่วนโค้งและสระหลอมเหลว, ป้องกันการปนเปื้อนโดยออกซิเจนหรือไนโตรเจน. เหมาะสำหรับท่อเหล็กที่ไร้รอยต่อและเชื่อม, ให้คุณภาพการเชื่อมสูง, การเสียรูปน้อยที่สุด, สปาสเตอร์ต่ำ, และมีประสิทธิภาพสูง. อย่างไรก็ตาม, มีต้นทุนอุปกรณ์ที่สูงขึ้น, ข้อกำหนดการปฏิบัติงานที่เข้มงวดขึ้น, และความไวต่อสภาพแวดล้อม.
จุดสำคัญสำหรับการเชื่อมแบบป้องกันแก๊ส:
-
การเลือกการเลือกก๊าซ: เลือกประเภทก๊าซ, อัตราการไหล, และความดันตามวัสดุท่อ, ความหนา, และประเภทเชื่อม. ก๊าซทั่วไปรวมถึงการผสมCO₂หรือ AR+CO₂, ด้วยอัตราการไหล 10L/นาทีถึง 25L/นาทีและแรงดัน 0.2MPa ถึง 0.4MPA.
-
การเลือกลวดเชื่อม: เลือกลวดตามวัสดุท่อ, ความหนา, และประเภทเชื่อม. สายเหล็กคาร์บอนต่ำ (เช่น., h08mna, H08MN2SIA) โดยทั่วไปจะใช้เส้นผ่านศูนย์กลาง 0.8 มม. ถึง 1.6 มม., ด้วยขั้วย้อนกลับ (ชิ้นงานลบ, คบเพลิงบวก).
-
การเตรียมร่อง: เช่นเดียวกับการเชื่อมส่วนโค้งด้วยตนเอง (ดูตารางด้านบน).
-
การจัดตำแหน่งท่อ: เช่นเดียวกับการเชื่อมส่วนโค้งด้วยตนเอง.
-
การเชื่อมตะปู: เช่นเดียวกับการเชื่อมส่วนโค้งด้วยตนเอง.
-
การเชื่อมชั้น: เช่นเดียวกับการเชื่อมส่วนโค้งด้วยตนเอง, สร้างความมั่นใจในมุมลวดและความเร็วที่เหมาะสมสำหรับการเชื่อมแบบสม่ำเสมอ.
1.3 การประสาน
การประสานใช้โลหะหลอมเหลวหรือโลหะผสมเป็นฟิลเลอร์เพื่อเข้าร่วมชิ้นส่วนโลหะ, เหมาะสำหรับท่อเหล็กที่ไร้รอยต่อและเชื่อม. มีคุณภาพการเชื่อมสูง, การเสียรูปน้อยที่สุด, สปาสเตอร์ต่ำ, และประสิทธิภาพสูง แต่แบ่งปันข้อเสียเดียวกันกับการเชื่อมแบบป้องกันแก๊ส.
ประเด็นสำคัญสำหรับการประสาน:
-
การเลือกโลหะฟิลเลอร์: เลือกฟิลเลอร์ตามวัสดุท่อ, ความหนา, และประเภทเชื่อม. ฟิลเลอร์ที่ใช้ทองแดงหรือเงิน (เช่น., BCUP-2, BCUP-3, BAG-1) ด้วยเส้นผ่านศูนย์กลาง 1 มม. ถึง 3 มม. และจุดหลอมละลาย 600 ° C ถึง 900 ° C เป็นเรื่องปกติ.
-
การเลือกฟลักซ์: ใช้กรดอนินทรีย์หรือเกลือ (เช่น., กรดฟอสฟอริกหรือบอริก) เป็นฟลักซ์, ด้วยแอปพลิเคชัน 5% –10%, เคลือบอย่างสม่ำเสมอบนพื้นผิวเชื่อมหรือฟิลเลอร์.
-
การเตรียมร่อง, การจัดตำแหน่งท่อ, การเชื่อมตะปู, และการเชื่อมแบบเลเยอร์: เหมือนกับข้างต้น.
2. วัสดุเชื่อม
วัสดุเชื่อมมีผลต่อคุณภาพและประสิทธิภาพการเชื่อมอย่างมีนัยสำคัญ. พวกเขาจะต้องตรงกับวัสดุท่อ, แสดงความสามารถในการเชื่อมที่ดีและคุณสมบัติเชิงกล, และปฏิบัติตามมาตรฐานสำหรับองค์ประกอบทางเคมี, คุณสมบัติทางกล, และความสามารถในการเชื่อม. เก็บวัสดุในแห้ง, ที่ระบายอากาศได้, และสภาพอากาศเย็นเพื่อป้องกันความชื้น, สนิม, หรือการปนเปื้อน.
วัสดุเชื่อมทั่วไปสำหรับท่อเหล็กที่ไร้รอยต่อรวมถึงขั้วไฟฟ้า, สายไฟ, และฟิลเลอร์ประสาน. ลักษณะและหลักการเลือกของพวกเขามีดังนี้:
2.1 ขั้วไฟฟ้า
ขั้วไฟฟ้า, ใช้ในการเชื่อมส่วนโค้งด้วยตนเอง, ประกอบด้วยแกนกลาง (สำหรับปัจจุบันและโลหะฟิลเลอร์) และการเคลือบ (สำหรับการป้องกันส่วนโค้งและสระว่ายน้ำ). พวกเขาเรียบง่าย, คุ้มค่า, และปรับตัวได้ แต่มีแนวโน้มที่จะมีคุณภาพไม่แน่นอน, สาด, การเสียรูป, และข้อบกพร่อง.
หลักการเลือก:
-
จับคู่อิเล็กโทรดกับวัสดุท่อ, โดยทั่วไปแล้วเหล็กคาร์บอนต่ำหรือเหล็กกล้าต่ำ (เช่น., J421, J422, J507, j507fe, E6013, E7018).
-
เลือกเส้นผ่านศูนย์กลาง (2.5มม. - 5 มม.) ขึ้นอยู่กับความหนา; เส้นผ่านศูนย์กลางที่ใหญ่ขึ้นเพิ่มกระแสไฟฟ้าและประสิทธิภาพ แต่มีความเสี่ยงและการเสียรูป.
-
ใช้ขั้วไฟฟ้าไฮโดรเจนต่ำเพื่อการเชื่อมที่ดีขึ้นและคุณสมบัติเชิงกลที่ดีขึ้น, ลดความพรุนและการแตก.
2.2 สายเชื่อม
สายเชื่อม, ใช้ในการเชื่อมแบบป้องกันแก๊ส, ประกอบด้วยแกนหลักและบางครั้งก็เป็นแกนหลักสำหรับการป้องกัน. พวกเขามีคุณภาพสูง, การเสียรูปน้อยที่สุด, สปาสเตอร์ต่ำ, และประสิทธิภาพ แต่ต้องการอุปกรณ์ที่มีราคาแพงและการใช้งานที่มีทักษะ.
หลักการเลือก:
-
จับคู่ลวดกับวัสดุท่อ, โดยทั่วไปแล้วเหล็กคาร์บอนต่ำหรือเหล็กกล้าต่ำ (เช่น., h08mna, H08MN2SIA, ER50-6, ER70S-6).
-
เลือกเส้นผ่านศูนย์กลาง (0.8MM - 1.6 มม.) ขึ้นอยู่กับความหนา; เส้นผ่านศูนย์กลางที่ใหญ่ขึ้นเพิ่มประสิทธิภาพ แต่มีความเสี่ยง.
-
ใช้สายไฟที่เป็นของแข็งหรือฟลักซ์; สายทึบนำเสนอคุณสมบัติที่ดีกว่า, ในขณะที่สายไฟฟลักซ์เพิ่มการป้องกันและลดความพรุน.
2.3 ฟิลเลอร์
ฟิลเลอร์การประสานประกอบด้วยแกนกลาง (สำหรับการเข้าร่วม) และฟลักซ์ (สำหรับการกำจัดออกไซด์และการเปียก). พวกเขาแบ่งปันข้อดีและข้อเสียของสายการเชื่อม.
หลักการเลือก:
-
จับคู่ฟิลเลอร์กับวัสดุท่อ, โดยทั่วไปแล้วทองแดง- หรือเงินตาม (เช่น., BCUP-2, BCUP-3, BAG-1, ถุง 2).
-
เลือกเส้นผ่านศูนย์กลาง (1mm - 3mm) ขึ้นอยู่กับความหนา; เส้นผ่านศูนย์กลางที่ใหญ่ขึ้นเพิ่มประสิทธิภาพ แต่มีความเสี่ยง.
-
ใช้ฟลักซ์ที่เหมาะสม (เช่น., กรดฟอสฟอริกหรือบอริก) ที่ 5%–10%, ใช้อย่างสม่ำเสมอ.
3. สภาพแวดล้อมการเชื่อม
สภาพแวดล้อมการเชื่อมส่งผลกระทบต่อคุณภาพและประสิทธิภาพอย่างมีนัยสำคัญ. ต้องเป็นไปตามมาตรฐานสำหรับอุณหภูมิ, ความชื้น, ความเร็วลม, การส่องแสง, และเสียงรบกวน, รักษาแห้ง, ที่ระบายอากาศได้, สว่าง, และสภาพที่เงียบสงบเพื่อหลีกเลี่ยงการรบกวนจากความร้อนที่รุนแรง, ความชื้น, ลม, แสงสว่าง, หรือเสียงรบกวน.
ข้อกำหนดด้านสิ่งแวดล้อม:
-
อุณหภูมิ: 5° C - 40 ° C. อุณหภูมิสูงทำให้เกิดความร้อนสูงเกินไป, ความพรุน, รอยแตก, หรือเผาไหม้; อุณหภูมิต่ำทำให้เกิดรอยร้าวเย็น, ฟิวชั่นที่ไม่สมบูรณ์, หรือขาดการรุก.
-
ความชื้น: 40%–80%. ความชื้นสูงทำให้เกิดความชื้นของวัสดุ, นำไปสู่ความพรุน, รอยแตก, หรือออกซิเดชั่น; ความชื้นต่ำทำให้เกิดความแห้งมากเกินไป, นำไปสู่การกระเด็นหรือการเสียรูป.
-
ความเร็วลม: 0.5m/s - 1.5m/s. ลมสูงกระจายก๊าซป้องกัน, ทำให้เกิดข้อบกพร่อง; ลมต่ำทำให้เกิดการสะสมก๊าซ, นำไปสู่การกระเด็นหรือการเสียรูป.
-
การส่องแสง: 300LX - 500LX. แสงมากเกินไปทำให้การมองเห็นบั่นทอน, ทำให้เกิดข้อผิดพลาด; แสงไม่เพียงพอนำไปสู่ข้อบกพร่องหรืออันตราย.
-
เสียงรบกวน: 60DB - 80dB. เสียงรบกวนมากเกินไปทำให้ได้ยิน, ทำให้เกิดข้อผิดพลาด; เสียงรบกวนต่ำช่วยลดการโฟกัส, นำไปสู่ข้อบกพร่องหรืออันตราย.
4. ท่อฉนวน
การควบคุมคุณภาพเป็นสิ่งสำคัญสำหรับการสร้างความมั่นใจในคุณภาพและประสิทธิภาพของการเชื่อม, ปฏิบัติตามมาตรฐานสำหรับการวางแผน, การตรวจสอบ, และการประเมินผล. ควรดำเนินการก่อน, ในระหว่าง, และหลังการเชื่อม.
ส่วนประกอบการควบคุมคุณภาพ:
-
การวางแผนคุณภาพ: พัฒนาข้อกำหนดและมาตรการสำหรับกระบวนการเชื่อม, วัสดุ, อุปกรณ์, บุคลากร, สิ่งแวดล้อม, การตรวจสอบ, และการประเมินตามข้อกำหนดของโครงการ. กำหนดก่อนการเชื่อม, ดำเนินการระหว่าง, และตรวจสอบหลังจาก.
-
การตรวจสอบคุณภาพ: ทำการทดสอบ, การวิเคราะห์, และการประเมินผลของรอยเชื่อมก่อน, ในระหว่าง, และหลังจากการเชื่อมโดยบุคลากรที่มีคุณสมบัติหรือบุคคลที่สาม. วิธีการรวมถึงการทดสอบแบบไม่ทำลาย, การทดสอบการทำลายล้าง, และการวิเคราะห์โลหะ, ประเมินลักษณะการเชื่อม, มิติ, รูปร่าง, ข้อบกพร่อง, โครงสร้าง, และคุณสมบัติทางกล. ผลการตอบกลับทันทีสำหรับการแก้ไข.
-
การประเมินคุณภาพ: จำแนกและรับรองคุณภาพการเชื่อมตามผลการตรวจสอบ, ยึดมั่นในระดับชาติ, อุตสาหกรรม, หรือมาตรฐานขององค์กร. ประเมินผลการเชื่อมและเกรดคุณภาพของโครงการและเงื่อนไขการยอมรับ. ผลการตอบกลับสำหรับการแก้ไข.
5. ข้อสรุป
การเชื่อมท่อเหล็กไร้รอยต่อเป็นเทคโนโลยีที่หลากหลายที่เกี่ยวข้องกับกระบวนการ, วัสดุ, สภาพแวดล้อม, และการควบคุมคุณภาพ. การเรียนรู้องค์ประกอบเหล่านี้เป็นสิ่งสำคัญสำหรับการปรับปรุงคุณภาพการเชื่อมและประสิทธิภาพ, สร้างความมั่นใจในความปลอดภัยและความน่าเชื่อถือของท่อ. บทความนี้ได้ระบุประเด็นสำคัญในสี่ด้านเหล่านี้, หวังว่าจะให้ข้อมูลเชิงลึกที่มีค่า.