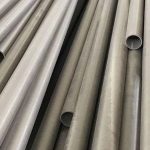
UNS S32750 super duplex stainless steel seamless pipe Study on extrusion process
September 24, 2024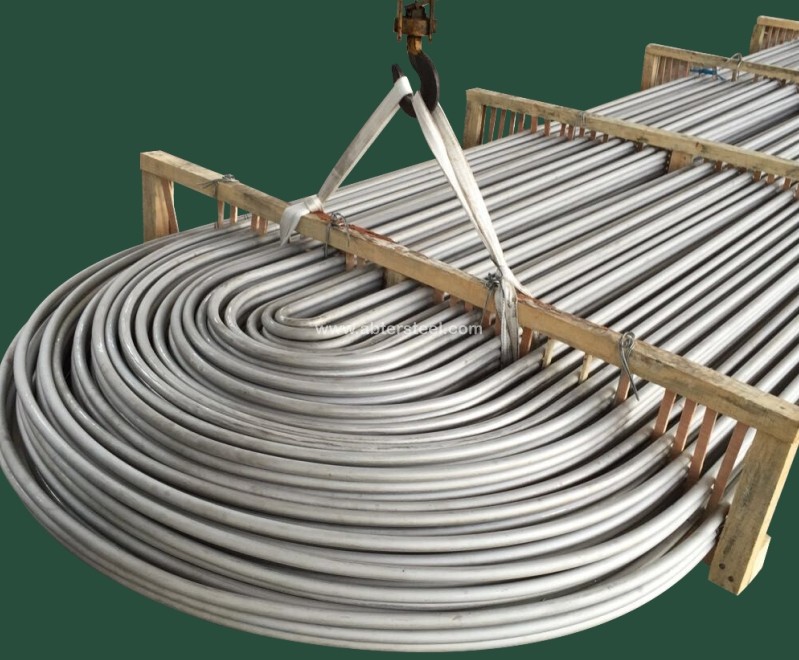
Most Common Mechanical Failure in Shell & Heat Exchanger Pipe
September 30, 2024Corrosion Resistance of API 5L X52 Carbon Steel Pipe in Sulfide Polluted Environments
Introduction
In the world of industrial piping, API 5L X52 carbon steel pipes are a popular choice due to their strength, versatility, and cost-effectiveness. These pipes are widely used in the oil and gas industry for transporting crude oil, natural gas, and other hydrocarbons. However, one of the significant challenges faced by these pipes is corrosion, especially in environments polluted with sulfides. Sulfide pollution can lead to severe corrosion problems, compromising the integrity and safety of the pipeline system. This article explores the corrosion resistance of API 5L X52 carbon steel pipes in sulfide-polluted environments, examining the factors influencing corrosion, mitigation strategies, and the latest research findings.
1. Understanding API 5L X52 Carbon Steel
1.1 Composition and Properties
API 5L X52 is a high-strength, low-alloy carbon steel that meets the specifications set by the American Petroleum Institute (API) for line pipes. Its composition and mechanical properties make it suitable for various applications in the oil and gas industry.
- Carbon (C): Provides strength and hardness.
- Manganese (Mn): Enhances strength and toughness.
- Phosphorus (P) and Sulfur (S): Kept to a minimum to reduce brittleness and improve weldability.
- Yield Strength: Minimum 360 MPa.
- Tensile Strength: Minimum 460 MPa.
1.2 Applications
API 5L X52 pipes are used in:
- Oil and Gas Transportation: For transporting crude oil, natural gas, and refined products.
- Structural Applications: Used in construction and infrastructure projects.
- Water and Slurry Transportation: Suitable for transporting water and slurry in mining and other industries.
2. Corrosion in Sulfide-Polluted Environments
2.1 Types of Corrosion
In sulfide-polluted environments, API 5L X52 carbon steel pipes are susceptible to various types of corrosion, including:
- Uniform Corrosion: A general loss of material over the entire surface.
- Pitting Corrosion: Localized corrosion that leads to the formation of small pits or holes.
- Sulfide Stress Cracking (SSC): A form of hydrogen embrittlement caused by the presence of hydrogen sulfide (H2S).
- Microbiologically Influenced Corrosion (MIC): Corrosion influenced by the presence of sulfate-reducing bacteria (SRB).
2.2 Factors Influencing Corrosion
Several factors influence the corrosion of API 5L X52 pipes in sulfide-polluted environments:
- Concentration of Sulfides: Higher concentrations of sulfides increase the risk of corrosion.
- pH Levels: Low pH levels can accelerate corrosion rates.
- Temperature: Elevated temperatures can enhance corrosion reactions.
- Presence of Chlorides: Chlorides can exacerbate pitting and crevice corrosion.
- Flow Rate: High flow rates can increase erosion-corrosion.
3. Mechanisms of Corrosion
3.1 Sulfide Stress Cracking (SSC)
SSC is a significant concern for carbon steel pipes in sulfide-polluted environments. It occurs when hydrogen sulfide reacts with the steel, leading to the absorption of hydrogen atoms. These hydrogen atoms diffuse into the steel, causing embrittlement and cracking under tensile stress.
- Hydrogen Sulfide Reaction: H2S reacts with iron to form iron sulfide and hydrogen.
- Hydrogen Diffusion: Hydrogen atoms diffuse into the steel matrix.
- Crack Initiation and Propagation: Cracks initiate at stress concentrators and propagate through the steel.
3.2 Microbiologically Influenced Corrosion (MIC)
MIC is caused by the activity of microorganisms, particularly sulfate-reducing bacteria (SRB), which produce hydrogen sulfide as a metabolic byproduct. This hydrogen sulfide contributes to corrosion through:
- Biofilm Formation: SRB form biofilms on the pipe surface, creating localized environments conducive to corrosion.
- Sulfide Production: SRB reduce sulfates to sulfides, increasing the concentration of corrosive agents.
- Localized Corrosion: The biofilm creates differential aeration cells, leading to localized corrosion.
4. Mitigation Strategies
4.1 Material Selection and Coatings
Selecting the right materials and coatings can significantly reduce the risk of corrosion in sulfide-polluted environments.
- Corrosion-Resistant Alloys: Using alloys with enhanced corrosion resistance, such as stainless steel or duplex stainless steel, can mitigate corrosion.
- Protective Coatings: Applying coatings such as epoxy, polyurethane, or polyethylene can provide a barrier against corrosive agents.
4.2 Cathodic Protection
Cathodic protection is a widely used technique to prevent corrosion by making the pipe the cathode of an electrochemical cell.
- Sacrificial Anodes: Attaching sacrificial anodes (e.g., zinc or magnesium) to the pipe, which corrode instead of the pipe.
- Impressed Current Systems: Using an external power source to provide a continuous flow of electrons to the pipe, preventing oxidation.
4.3 Chemical Inhibitors
Chemical inhibitors can be added to the fluid to reduce the rate of corrosion.
- Sulfide Scavengers: Chemicals that react with hydrogen sulfide to form non-corrosive compounds.
- Corrosion Inhibitors: Compounds that form a protective film on the pipe surface, reducing the interaction with corrosive agents.
4.4 Monitoring and Maintenance
Regular monitoring and maintenance can help detect and address corrosion issues before they become severe.
-
- Corrosion Monitoring Systems: Using sensors and probes to monitor corrosion rates and detect early signs of corrosion.
- Regular Inspections: Conducting regular inspections and maintenance to identify and repair damaged sections of the pipeline.
5. Latest Research and Developments
5.1 Advanced Coatings and Materials
Recent research has focused on developing advanced coatings and materials with enhanced corrosion resistance.
- Nanocomposite Coatings: Incorporating nanoparticles into coatings to improve barrier properties and resistance to abrasion.
- High-Performance Alloys: Developing new alloys with improved resistance to sulfide stress cracking and MIC.
5.2 Biotechnology in Corrosion Control
Biotechnology offers innovative solutions for controlling MIC and enhancing corrosion resistance.
- Biocides and Enzymes: Using biocides to target and eliminate SRB and other corrosive microorganisms.
- Genetic Engineering: Engineering microorganisms to produce less corrosive byproducts or enhance bioremediation processes.
5.3 Smart Monitoring Systems
The development of smart monitoring systems has revolutionized corrosion management in pipelines.
- Wireless Sensor Networks: Deploying wireless sensors along the pipeline to provide real-time data on corrosion rates and environmental conditions.
- Predictive Analytics: Using machine learning algorithms to predict corrosion trends and optimize maintenance schedules.
Conclusion
The corrosion resistance of API 5L X52 carbon steel pipes in sulfide-polluted environments is a critical concern for the oil and gas industry. Understanding the mechanisms of corrosion and the factors influencing it is essential for developing effective mitigation strategies. Advances in materials science, biotechnology, and smart monitoring systems offer promising solutions for enhancing the durability and safety of pipelines. By implementing a combination of material selection, protective coatings, cathodic protection, chemical inhibitors, and regular monitoring, industries can effectively manage corrosion risks and ensure the long-term integrity of their pipeline systems. As research continues to evolve, new technologies and approaches will further enhance the corrosion resistance of carbon steel pipes, paving the way for safer and more efficient industrial operations.