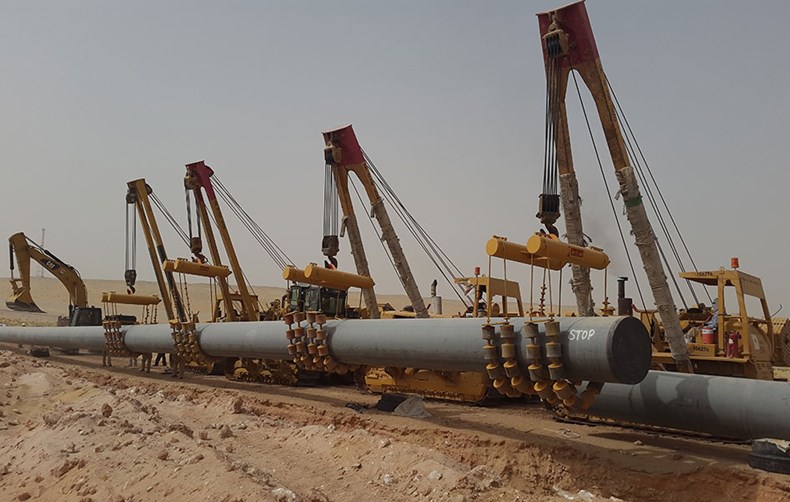
Theoretical weight calculation formula of various steels
August 24, 2022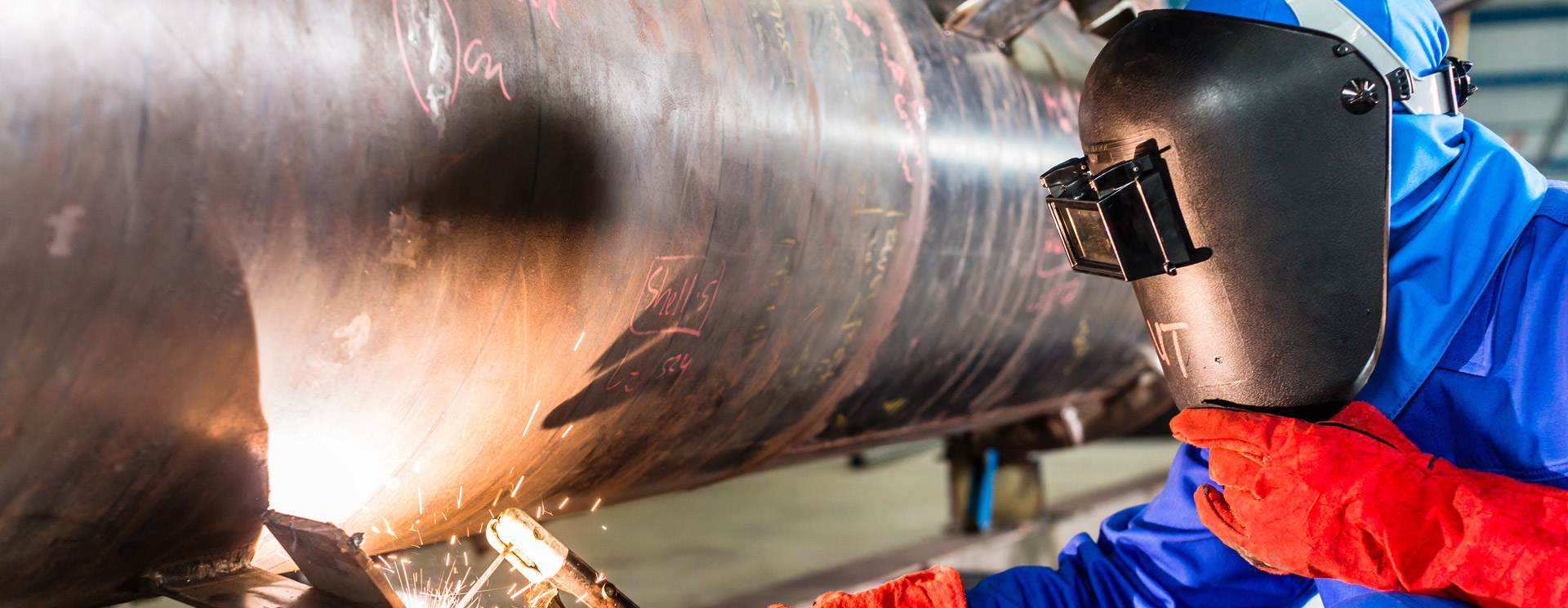
Evergreen Steel company Want buy Cold rolled EN10219 S355JOH seamless pipe
August 31, 2022
API 5CT /5L PIPELINE PIPE OIL CASING PIPE
|
X65 X42 X52 X60 X80 L245 L290 L360 L418 L480
H40, J55,K55, N80, L80, C90,T95, P110, Q125, V150 |
STANDARD
|
API 5L/API 5CT
|
THREAD
|
STC.BTC.LTC.EUE.PH6
|
LENGTH
|
R1(4.86-7.62M). R2(7.62-10.36M). R3(10.36-13M)
|
Keywords: OCTG,oil; Pipe threads; Detection technology
During the drilling operation, there are many different failure forms of oil pipe threads, such as slip off, wire buckle break, etc. If there is an accident problem, it will lead to more serious economic losses, and when the situation is serious, the entire well will be scrapped. Inspections for threads are carried out to find threads of insufficient quality and avoid unnecessary economic losses due to the use of substandard threads. At present, the production and processing of casing threads and drilling tools need to be controlled by multiple processes such as sampling inspection and process inspection, and the newly purchased drilling tools need to be inspected when receiving goods, or the corresponding personnel are assigned to supervise the manufacturing. Before going down the well, the relevant staff should carry out inspections for the situation of thread corrosion and deformation.
First, the basic principle of oil pipe thread measurement
In the specific production process, the comprehensive measurement method is usually used to detect the thread of the oil pipe. Ordinary thread gauges can only be roughly tested whether the thread meets the requirements, and the specific parameter values cannot be given for threads with relatively high accuracy requirements, and when there is dirt on the surface of the thread, the obtained detection results will have a large error [1]. For the contact tubing thread, the basic principle of its measurement is to use the scanning probe as a contact sensor, so as to obtain the data information corresponding to the relevant points on the contour of an axial profile, and then input this information to the computer to use the relevant software to implement fitting processing to obtain the contour profile of the thread, and then obtain the thread pitch, tooth angle and taper and other related parameter values through calculation, and then make a specific judgment on whether these parameter values can reach the corresponding standards.
(1) Testing items
1. Oil casing
It mainly detects the geometric dimensions, appearance quality and other relevant parameters of the oil sleeve.
2. Drilling tools
It mainly detects the thread parameters, appearance quality and structural dimensions of the drill tool.
3. Tools and measuring tools for testing
Inner diameter lever table, thickness gauge, vernier caliper, depth micrometer, inner and outer taper meter, tape measure, etc.
(2) Preparation before testing
First, the cleaning operation is carried out for the thread, and the production batch number, specification and plant name are recorded. Second, select gauges such as thread gauges, contact diameters, and calipers. Third, locate the actual measurement range. Regarding round threaded sleeves, the external thread is the first complete buckle to the 12.7 position of the total length, and the inner thread is the first complete buckle to the J+1P position; With regard to partial trapezoidal bushings, the outer thread is the first complete buckle to the L7 position, and the internal thread and the round thread sleeve are consistent; Regarding the thread of the drill tool, it is necessary to be the first complete buckle to the last complete buckle; With regard to threads, they are consistent with round threaded sleeves. Fourth, establish the actual measurement spacing. First, measure the specific height of the tooth shape. For products with a range beyond 25.4 mm, this needs to be implemented at a spacing of 25.4 mm [2]. For measurements in the 12.7-25.4 mm measurement range, it is necessary to implement it at a distance of 12.7 mm. Second, establish the taper and pitch. For normal threads, the spacing is the same as above. In any case, except for the partial trapezoidal thread, the measured contact point of the pressure type height, pitch and taper cannot exceed the position of the last thread.
(3) Measurement
First, check the appearance quality. There can be insufficient thread damage, etc., for minor damage and threads containing burrs, grinding treatment, and screw the corresponding specification gauge, for threads with more serious damage and deformation do not need to be screwed. Second, check the passage and the associated binding dimensions. Again, detect individual thread-related parameters. A more detailed introduction was made in the API standard to understand the technical points of thread detection, the instrument reading needs to find the maximum turning point, and the taper gauge and pitch gauge need to swing up and down around the fixed contact or left and right; The inner teeth swing up and down or vertically; The outer tooth gauge oscillates up and down or left and right in a direction perpendicular to the thread axis. It is worth noting that the measurement of taper needs to be maintained above the cross-section of the same axis, and the tooth height and pitch should be in the direction of the busbar. Finally, the tight distance is detected. It is necessary to ensure the stability of the rotation, with the strength of one person until it cannot be rotated.
(4) Relevant matters needing attention First, all the relevant gages used, especially the gauges, need to be isothermal enough time with the product being tested to eliminate the temperature difference between the gages. This is because temperature not only has a certain degree of influence on the accuracy of the final measurement result, but also makes the gauge tightly clinging to the joint and unable to be disassembled. Second, in the process of specifically recording the tight distance between the oil sleeve public buckle, the positive and negative signs should be clearly marked. Third, the backhaul error of the scale is effectively eliminated. Fourth, in the process of actually measuring the taper, it is necessary to pay attention to whether the return to zero can be normal, and if it is not normal, it needs to be measured again. For the full thread interval, the measurement spacing needs to be fully covered in this area, that is, the measurement spacing can overlap when the situation requires, and the actual measurement of only one spacing cannot meet the requirements. For example, for the Japanese ITOCHU Red Pill FOX wire buckle sleeve, in the process of production and processing of the public buckle, the 1-inch taper of the small end position meets the requirements, and the second inch cannot meet the relevant requirements, and in order to obtain the corresponding patent authorization, it is necessary to eliminate this phenomenon [3]. In this regard, it is necessary to learn from the experience and implement specific inspection processes by comprehensively covering methods that can overlap. In the process of measuring from the threaded little end position to the big end position, the table reading and the actual measured value need to be kept the same, otherwise the maximum value read using the dial to remove the reading of the position pointed by the pointer is the actual measurement. Fifth, attention should be paid to the revision of the tight distance. Corrections to S1, S2 and P1 are necessary when some measurement results are on the verge of conforming to and not meeting the criteria. Regarding the drill thread, the tight distance tolerance range itself is relatively small, so it is also extremely critical to correct it. Sixth, whether the burrs and inner chamfers of the inner and outer edges of the pipe end can be inverted, especially for the position of the tight end of the machine, more attention should be paid to it. Seventh, after the phosphating treatment, the surface of the thread is relatively rough, and the inner taper gauge has a certain difficulty in oscillating during the actual measurement process because the measuring force is relatively large, and a small amount of lubricating oil needs to be applied to the alveoli. Eighth, the damage to the position of the threaded shoulder of the drill tool needs to be paid great attention, especially the position of the longitudinal groove will seriously affect its sealing, and the damage caused by the mechanical collision of the chamfer diameter and the position of the tooth top is often a problem that is easy to ignore. Ninth, about the single instrument, which belongs to the high-precision instrument, it needs to be extra careful in the operation process, to ensure that it is handled lightly and lightly, and sent for inspection according to the specified time.
The tolerance range of key projects should comply with APISPEC5B and APISPEC7 standards. First, the pitch deviation. The unit is millimeters, with two or three decimal places, which is due to the fact that the index value of the import gauge is 0.001″ or 0.0005″, while the index value of the national production gauge is 0.01 mm. Second, taper. Units are mm/m. There is a decimal place, the index value of the national production gauge is 0.01 mm, the index value of the import gauge is 0.001″, and the 62.5 grid measured in the weekday represents 62.5 mm / m, that is, 0.0625in / in. Third, geometric dimensions. The units are millimeters, with significant digits left in conjunction with the relevant standards. Fourth, close distance. The units are millimeters, leaving two decimal places. Fifth, the tooth high deviation. The units are millimeters and remain the same as the pitch gauge.
2. Judgment
First, the tolerance range of key projects should be consistent with APISPEC5B and APISPEC7 standards. Secondly, projects that do not meet the standards need to be handled carefully, and in order to prevent the occurrence of misjudgments, they can be reviewed by others.
3. Concluding Remarks
In order to ensure the good quality of the oil pipe thread, the corresponding inspection technology should be vigorously applied. It is true that the scientific nature of the operation and whether the speed and torque are reasonable will also affect the quality of the threaded connection to a certain extent. If the clamping force of the large tongs is too large in the actual drilling operation, it will cause the thread to deform and the adhesive buckle will occur. The oiling and running-in are not uniform, the lubrication effect is not exerted, and the adhesive and tooth shape are also damaged, and the phenomenon of blurting occurs when the tensile effect is lost. Therefore, we should strictly comply with the operating regulations and implement the corresponding standards to ensure the good application of thread detection technology.