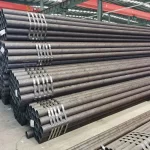
Corrosion Resistance of API 5L X52 Carbon Steel Pipe in Sulfide Polluted Environments
September 24, 2024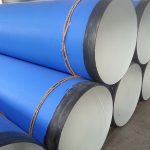
Service Life Prediction of Polyethylene Coated Steel Pipe
October 1, 2024Heat exchangers represent crucial process equipment ubiquitously used across industries for cooling, heating, boiling and condensing applications. Efficient heat transfer relies on reliable piping networks to deliver hot/cold fluids into exchanger shells. However, the complex thermal and hydraulic stresses, presence of corrosive environments and possibility of fouling over many years mean piping is prone to degradation mechanisms undermining structural integrity. This report analyzes dominant mechanical failure modes afflicting heat exchanger tubing and shells in order to aid prevention, inspection, and integrity assessments supporting long operational lifetimes.
Tube Failures
As sensitive heat transfer surfaces, tubes experience the brunt of heat exchanger stresses. Several tubing damage modes rank among the most prevalent:
- Flow Accelerated Corrosion: Formed deposits concentrate corrosives, accelerating wall thinning, especially where flows fluctuate at U-bends. Left unchecked, pinhole leaks/ruptures occur.
- Vibration Wear: Tube support plate interactions induce frictional vibration wear preferentially on upper tubes. Erosion penetrates deeply attacking tube thickness.
- Fouling/Corrosion Under Deposits: Heat exchanger conditions promote deposits harbouring corrosive attack behind an insulated layer, stealthily thinning walls undetected.
- Stress Corrosion Cracking: For some combinations of susceptible tube materials and aggressive environments like chloride solutions, crazing cracks may propagate rapidly.
Mitigation relies upon corrosion inhibitor injection, improved support designs reducing wear points, online monitoring for timely cleaning before perforations.
Shell Failures
The pressure housing shell sustains lower thermal stresses yet must maintain structural integrity. Commonly observed damage modes include:
- General Corrosion Thinning: Shell surfaces exposed directly to process fluids experience uniform corrosion reducing wall thickness, eventually approaching code minimums.
- Pitting: Localized corrosion initiates pits possibly linked to preferential hard second-phase microstructural inclusions. Pits can coalesce undermining integrity.
- Vortex Induced Vibration: Shell resonance from turbulent fluid vortices instigates high cycle metal fatigue especially in subcooled exchangers. Cracking initiates from shell interior.
- Stress Corrosion Cracking: Similar to tubes, some combinations of shells and wet H2S environments risk environmentally assisted cracking problems.
Routine non-destructive inspections assess thinning to flag shells requiring repair/replacement before reaching unserviceable thresholds. Cathodic protection also helps prolong shell lifetimes.
Fouling Effects
Fouling acts as an accelerator for many damage mechanisms by:
- Impeding heat transfer, raising metal temperatures deeper in exchangers’ thermal cycles.
- Concentrating corrosives in deposits dissolving protective oxide films.
- Harbouring microbes promoting microbiologically influenced corrosion.
- Increasing friction elevating vibration/erosion potential.
Regular cleaning maintains acceptable heat transfer coefficient reductions below 25% while deposited layers remain thin enough for removal. Monitoring differential pressures aids scheduling cleanings before deterioration accelerates.
Conclusions
Systematic consideration of materials, fluid properties, operating conditions and damage mechanisms sheds light on where mechanical failures typically initiate within heat exchanger piping networks. Integrating mitigation strategies like inhibitors, non-destructive evaluation and deposition monitoring helps prevent deterioration, thus extending service intervals and reliability of these critical heat transfer assets.