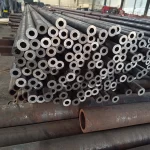
Analysis of Key Elements in Seamless Steel Pipe Welding Technology
April 29, 2025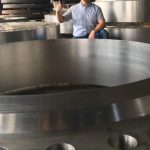
Super-Large Forged Flanges by Abter Steel
May 10, 2025Material Design for 700℃ Ultra-Supercritical High-Pressure Boiler Pipes
Ultra-supercritical (USC) high-pressure boiler pipes designed for 700℃ operation must withstand extreme temperatures and pressures (typically exceeding 27.5 MPa and reaching 700℃ or higher). These materials require exceptional high-temperature strength, oxidation resistance, corrosion resistance, and creep resistance. Below is an overview of commonly used materials for designing 700℃ USC boiler pipes, their properties, and key considerations.
1. Commonly Used Materials
USC boiler pipes typically employ advanced nickel-based alloys, austenitic stainless steels, or high-alloy ferritic/martensitic steels. The material choice depends on the operating conditions of components such as superheaters or reheaters. Below are the typical materials used.
1.1 Nickel-Based Alloys
Nickel-based alloys are the preferred choice for 700℃ USC boiler pipes due to their superior strength, oxidation resistance, and corrosion resistance at high temperatures.
- Typical Grades:
- Inconel 617 (UNS N06617): Contains nickel, chromium, cobalt, and molybdenum, suitable for 700℃ and above, with excellent creep resistance and oxidation resistance.
- Inconel 740/740H: Specifically designed for USC boilers, containing nickel, chromium, cobalt, and titanium, offering high creep strength and resistance to coal ash corrosion.
- Alloy 263: Suitable for high-temperature, high-pressure environments, particularly for welded structures.
- Chemical Composition (Inconel 740H Example):
Element | Ni | Cr | Co | Mo | Nb | Ti | Al | Fe | Others |
---|---|---|---|---|---|---|---|---|---|
Content (%) | Balance | 24.0–26.0 | 19.0–21.0 | 0.1–0.5 | 1.5–2.5 | 1.4–2.0 | 1.2–1.8 | ≤2.0 | Minor C, Si, etc. |
- Mechanical Properties (Example):
- Tensile Strength: ≥1000 MPa (room temperature); ≥600 MPa (700℃)
- Yield Strength: ≥700 MPa (room temperature); ≥400 MPa (700℃)
- Creep Life: ≥100,000 hours at 700℃ under 100 MPa stress
- Applications: Used in superheaters and reheaters in the highest temperature zones, capable of withstanding extreme heat and corrosive gases (e.g., sulfur- or chlorine-containing flue gases).
1.2 Advanced Austenitic Stainless Steels
Austenitic stainless steels are suitable for slightly lower temperature ranges (600–700℃), offering good corrosion resistance and processability, though their creep resistance is inferior to nickel-based alloys.
- Typical Grades:
- Super 304H (UNS S30432): Contains 18Cr-8Ni with added Cu, Nb, and N for enhanced high-temperature strength and oxidation resistance.
- HR3C (25Cr-20Ni-Nb-N): High-chromium-nickel austenitic steel with excellent oxidation and steam corrosion resistance.
- TP347HFG: Fine-grained version of TP347H, with improved creep resistance.
- Chemical Composition (Super 304H Example):
Element | C | Cr | Ni | Cu | Nb | N | Mn | Si | P | S |
---|---|---|---|---|---|---|---|---|---|---|
Content (%) | 0.07–0.13 | 17.0–19.0 | 7.5–10.5 | 2.5–3.5 | 0.3–0.6 | 0.05–0.12 | ≤1.0 | ≤0.3 | ≤0.04 | ≤0.01 |
- Mechanical Properties (Example):
- Tensile Strength: ≥590 MPa (room temperature); ≥300 MPa (700℃)
- Yield Strength: ≥235 MPa (room temperature); ≥150 MPa (700℃)
- Creep Life: 10,000–100,000 hours at 700℃ under 100 MPa stress
- Applications: Used in secondary high-temperature zones for superheaters, reheaters, and steam pipelines.
1.3 High-Alloy Ferritic/Martensitic Steels
These steels are used in areas with temperatures below 650℃, offering lower costs than nickel-based alloys or austenitic steels, but their performance at 700℃ is limited, making them suitable for transitional zones.
- Typical Grades:
- P91 (ASTM A335 P91): 9Cr-1Mo steel, suitable for 600–650℃ environments.
- P92 (ASTM A335 P92): Enhanced 9Cr-2W steel with added W, Nb, and B, offering better creep resistance than P91.
- MARBN: A new high-chromium martensitic steel with 9–12Cr and added B, N, approaching the 700℃ limit.
- Chemical Composition (P92 Example):
Element | C | Cr | Mo | W | V | Nb | B | N | Mn | Si |
---|---|---|---|---|---|---|---|---|---|---|
Content (%) | 0.07–0.13 | 8.5–9.5 | 0.3–0.6 | 1.5–2.0 | 0.15–0.25 | 0.04–0.09 | 0.001–0.006 | 0.03–0.07 | 0.3–0.6 | ≤0.5 |
- Mechanical Properties (Example):
- Tensile Strength: ≥620 MPa (room temperature); ≥350 MPa (650℃)
- Yield Strength: ≥440 MPa (room temperature); ≥200 MPa (650℃)
- Creep Life: ~100,000 hours at 650℃ under 100 MPa stress
- Applications: Used in main steam pipelines, lower-temperature superheaters, or reheaters.
2. Design Considerations for Material Selection
When designing 700℃ USC boiler pipes, material selection must balance the following factors:
- Operating Temperature and Pressure:
- Zones at 700℃ and above (e.g., superheaters, reheaters) prioritize nickel-based alloys (e.g., Inconel 740H).
- 600–700℃ zones can use advanced austenitic stainless steels (e.g., Super 304H, HR3C).
- Zones below 650℃ can use P91, P92, or MARBN.
- Creep Resistance:
- Creep is the primary failure mode at 700℃. Nickel-based alloys and advanced austenitic steels offer significantly longer creep life than ferritic steels.
- Oxidation and Corrosion Resistance:
- High-temperature flue gases containing sulfur or chlorine cause external corrosion, while steam-side oxidation is a concern. Nickel-based alloys and high-chromium austenitic steels (e.g., HR3C) excel in resisting coal ash corrosion and steam oxidation.
- Cost and Processability:
- Nickel-based alloys are expensive and challenging to process and weld, suitable for critical high-temperature components.
- Austenitic stainless steels and P91/P92 are more cost-effective and easier to weld and process, ideal for broader applications.
- Weldability:
- Nickel-based alloys (e.g., Inconel 740H) require specialized welding processes and filler materials.
- Austenitic steels (e.g., Super 304H) have good weldability but require control of the heat-affected zone.
- P91/P92 require strict preheating and post-weld heat treatment to prevent cracking.
- Long-Term Stability:
- Materials must maintain microstructural stability during long-term high-temperature operation, avoiding brittle phase formation (e.g., σ phase) or grain growth.
3. Manufacturing Process
The manufacturing process for 700℃ USC boiler pipes is critical to ensuring material performance. Key steps include:
- Seamless Manufacturing: Hot rolling or cold drawing ensures defect-free pipes without weld imperfections.
- Heat Treatment:
- Nickel-Based Alloys: Solution annealing (1100–1200℃) followed by aging to optimize precipitate phases (e.g., γ’ phase).
- Austenitic Stainless Steels: Solution treatment (1050–1150℃) to prevent intergranular corrosion.
- Ferritic/Martensitic Steels: Normalizing (1050–1100℃) and tempering (750–800℃) to stabilize the martensitic structure.
- Surface Treatment: Shot blasting or pickling to remove oxide scale and enhance corrosion resistance.
- Quality Control:
- Chemical Composition Analysis: Ensures compliance with Cr, Ni, Mo, and other element specifications.
- Mechanical Testing: Includes high-temperature tensile, creep, and fatigue tests.
- Non-Destructive Testing (NDT): Ultrasonic and radiographic testing to detect internal defects.
- High-Temperature Corrosion Testing: Simulates coal ash and steam environments to verify corrosion resistance.
4. Typical Application Cases
- European AD700 Project: Utilized Inconel 617 and Inconel 740H for superheaters and reheaters in 700℃ USC boilers, demonstrating long-term stability.
- Japan A-USC Program: Employed HR3C and Super 304H for superheaters, combined with P92 for lower-temperature zones, achieving high efficiency and low emissions.
- China USC Power Plants: Some plants use HR3C and P92, with nickel-based alloys (e.g., Inconel 740H) gradually being adopted.
5. Conclusion
The design of 700℃ ultra-supercritical high-pressure boiler pipes primarily relies on the following materials:
- Nickel-Based Alloys (e.g., Inconel 740H, 617): Ideal for the highest temperature zones (≥700℃), offering the best creep and corrosion resistance but at a high cost.
- Advanced Austenitic Stainless Steels (e.g., Super 304H, HR3C): Suitable for 600–700℃ zones, providing a cost-effective balance with good oxidation resistance.
- High-Alloy Ferritic/Martensitic Steels (e.g., P91, P92): Used in zones below 650℃, cost-effective but limited in high-temperature performance.
Material selection should consider specific temperature, pressure, corrosion environment, and cost constraints. Rigorous manufacturing processes and quality control are essential to ensure pipe performance. Nickel-based alloys are the future trend for 700℃ and above USC boilers, while austenitic stainless steels and enhanced martensitic steels remain critical for transitional zones.