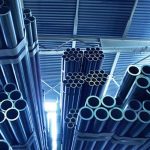
High Temperature and High Pressure Resistance Line Pipe Steel and Pipes of Key Technologies
September 21, 2024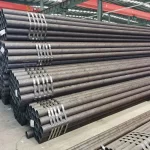
Corrosion Resistance of API 5L X52 Carbon Steel Pipe in Sulfide Polluted Environments
September 24, 2024Introduction
As next-generation energy and petrochemical infrastructures demand highly corrosive service pipelines, super duplex stainless steels attract extensive use for their uniquely balanced combination of strength, toughness and corrosion resistance superior to traditional alloys. Within the family of these Fe-Cr-Ni-Mo austenitic-ferritic materials, UNS S32750 emerges frequently specified due to elevated pitting/ crevice corrosion resistance through tailored Mo and W additions. However, while applications abound its fabrication into seamless pipes requires thorough understanding and optimized processing. This report aims to examine the extrusion technique applied in manufacturung S32750 super duplex seamless pipe through evaluating the alloy’s metallurgy and behaviors during various stages comprising preheating, containerless extrusion, and post-processing.
Microstructure and Properties
The primary microstructural phases governing S32750’sperformance include a near-equal balance of highly corrosion-resistant austenite γ-Fe(Ni,Cr) and ferrite α-Fe providing a synergistic effect. Key alloying elements promote this duplex structure through:
- Chromium (24-26%) stabilizes both ferrite and austenite while imparting corrosion resistance
- Molybdenum (3.5-4.5%) and tungsten (1.5-2.5%) enhance resistance to localized corrosion like pitting
- Nickel (5-7%) increases austenite fraction which then confers elongation capabilities
Together this yields a microstructure of 40-60% austenite islands dispersed within a ferritic matrix possessing the optimum damage tolerance and resistance. S32750 typically exhibits ultimate tensile strengths exceeding 90 ksi with 20% minimum elongation and excellent toughness down to cryogenic temperatures.
Billet Production
Producing the necessary S32750 feedstock (billet) for extrusion starts with pure raw elemental ingredients melted under inert argon gas using vacuum induction furnaces. Careful adjustments secure compositions per ASTM specifications while minimizing unwanted interstitial elements like sulfur, phosphorus and nitrogen linked to detrimental secondary phases. Continuous casting machines rapidly solidify the molten metal into rectangular billets requiring further processing to realize full properties.
Preheating
The primary goal prior to extrusion involves homogenizing billets to refine grain structure and dissolve carbides/nitrides inclusions that could weaken pipe performance. As an alloy strengthening precipitation mechanism relies on this secondary phase refinement a multi-step preheating is commonly adopted:
- Initial soak holds billets at 900-1020°C allowing slow dissolution of inclusions which reprecipitate as finer dispersoids
- Slow cooling over 1-2 days retains precipitates before final temper in the duplex range (850-950°C) to ensure full microstructural balance forms upon slow air cooling
Strict temperature controls safeguard the metallurgical balance during these heating/ soaking stages which can last up to a week overall.
Containerless Extrusion
Containerless direct extrusion denotes the process where billets are compressed through a conical steel die devoid of any surrounding container. This imparts operational advantages over traditional container-based extrusion for manufacturing S32750 pipe. Key aspects:
- Billets preheated to 1050-1150°C enter the die inlet riding upon an insulated shoe and pushed by a hydraulic ram
- Conical geometry oriented at an 8-15° half-angle generates uniform compression stress, forcing metal to smoothly flow through 3-10x reduction ratios
- Near-net shape extruded ‘logs’ exit the die maintaining 95% dimensional accuracy without tears/cracks
- Process productivity reaches 30m/minute with minimal flash generation and defect rates below 1ppm
- Logs immediately quenched in water to lock the duplex microstructure then straightened
Containerless extrusion leverages billet preconditioning, controlled stresses and optimized die design to deliver high quality S32750 pipe without risk of container defects.
Post-Processing
Further shaping and heat treatments tune the microstructure and properties:
- Milling/turning removes surface imperfections and achieves pipe roundness/wall thickness tolerances
- Solution annealing held 1 hour between 1000-1100°C re-solves any work-hardened layers before rapid quenching
- Precipitation hardening involves aging 2-6 hours between 600-750°C to nucleate desired distribution of strengthening nanometer-scale particles like carbides
- Non-destructive testing evaluates soundness and certifies mechanical properties meet application codes
- Optional coating/cladding applied before shipping protects against corrosion during future service
Upon post-treatments S32750 seamless pipe exhibits the target ultra-high strength-toughness profile endowed through refined processing routes like containerless extrusion combined with precision heat treatments.
Conclusion
meeting the stringent requirements demanded in offshore, oil/gas and chemical markets requires optimized fabrication techniques. This report detailed the multi-stage containerless extrusion process applied to produce high-quality seamless pipe from super duplex stainless alloy UNS S32750. By preconditioning billets, leveraging controlled deformation stresses and refining microstructures, seamless pipe achieves the uniquely balanced properties from this alloy’s duplex matrix rendering it indispensable for long-life pipelines transporting corrosive fluids. Continuous advancement nurtures extrusion capabilities ensuring sustainable infrastructure well into the future.