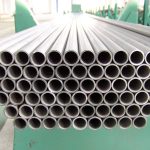
What is super stainless steel? Nickel-based alloy?
February 18, 2025Asia-Pacific
February 27, 2025What is the Difference Between Cladding and Overlay?
Cladding and overlay are terms often used interchangeably in industrial contexts, but they have distinct meanings depending on the application. Both processes involve applying a layer of material onto a substrate to enhance its properties, such as corrosion resistance, wear resistance, or structural integrity. However, their methods, purposes, and outcomes differ.
Cladding typically refers to a broader process where a thick layer of material (often metal, but sometimes polymers or ceramics) is bonded to a base material to provide protection or improve functionality. The cladding layer is usually applied using techniques like roll bonding, explosive bonding, or welding, and it can be significantly thicker than an overlay—sometimes ranging from millimeters to centimeters. Cladding is often used to create a composite material where the cladding becomes an integral part of the structure, contributing to both protection and mechanical strength.
Overlay, on the other hand, is a more specific term that typically describes a thinner layer of material applied to the surface of a substrate, often via welding or thermal spraying. The primary goal of an overlay is to enhance surface properties—like resistance to wear, corrosion, or heat—without significantly altering the substrate’s bulk properties. Weld overlay, a subset of overlay, involves depositing a metal layer through welding techniques, making it a durable and metallurgically bonded solution.
Here’s a concise comparison:
Aspect
|
Cladding
|
Overlay
|
---|---|---|
Thickness
|
Thicker (millimeters to centimeters)
|
Thinner (microns to a few millimeters)
|
Purpose
|
Structural enhancement, protection
|
Surface property enhancement
|
Bonding
|
Mechanical or metallurgical
|
Typically metallurgical (e.g., welding)
|
Methods
|
Roll bonding, explosive bonding, welding
|
Welding, thermal spraying
|
Material Change
|
Often alters bulk properties
|
Primarily affects surface
|
In practice, the distinction can blur, especially in welding contexts where “cladding” and “overlay” might both refer to weld-deposited layers. However, cladding tends to imply a more substantial layer, while overlay focuses on surface-level improvements.
What is Weld Overlay?
Weld overlay, also known as weld cladding or hardfacing (depending on the context), is a process where a layer of metal is deposited onto a base material (substrate) using welding techniques. This layer, called the overlay, is metallurgically bonded to the substrate, meaning the two materials fuse at the molecular level, creating a strong, durable connection. The purpose of weld overlay is to improve the substrate’s surface properties—such as resistance to corrosion, erosion, abrasion, or high temperatures—without replacing the entire component.
Weld overlay is widely used to extend the service life of components exposed to harsh environments. For example, a steel pipe might receive a corrosion-resistant alloy overlay to handle acidic fluids, or a tool might get a hardfacing overlay to withstand wear. The process is cost-effective because it allows the use of a cheaper base material (e.g., carbon steel) while applying a premium material only where needed.
The weld overlay process involves melting a filler material (wire, rod, or powder) using a heat source (e.g., arc, plasma, or laser) and depositing it onto the substrate. The overlay material is chosen based on the desired properties, and the substrate is typically preheated to minimize thermal stress and ensure proper bonding.
Types of Weld Overlay Processes
Several weld overlay processes exist, each with unique advantages depending on the application, material, and precision required. Below are the most common types, followed by a table summarizing key details.
-
Shielded Metal Arc Welding (SMAW)
-
Also known as stick welding, SMAW uses a consumable electrode coated in flux. It’s simple, portable, and cost-effective but offers limited control over deposition and is slower for large areas.
-
-
Gas Metal Arc Welding (GMAW)
-
Known as MIG welding, GMAW uses a continuous wire electrode and a shielding gas. It’s faster than SMAW and suitable for automated systems, though it requires a clean environment.
-
-
Gas Tungsten Arc Welding (GTAW)
-
Called TIG welding, GTAW uses a non-consumable tungsten electrode and a separate filler material. It provides high precision and quality, ideal for thin overlays or critical applications, but it’s slower and more expensive.
-
-
Plasma Transferred Arc Welding (PTAW)
-
PTAW uses a plasma arc to melt powdered filler material, offering excellent control over the overlay thickness and minimal dilution (mixing with the substrate). It’s widely used for hardfacing and corrosion-resistant overlays.
-
-
Submerged Arc Welding (SAW)
-
SAW involves a continuous wire electrode buried in a flux layer that shields the weld. It’s highly efficient for large, thick overlays but less versatile for complex shapes.
-
-
Laser Weld Overlay (Laser Cladding)
-
This advanced method uses a laser to melt a filler material (powder or wire) onto the substrate. It offers precision, low heat input, and minimal distortion, making it ideal for high-value components.
-
-
Oxy-Fuel Welding (OFW)
-
A less common method for overlay, OFW uses a flame to melt the filler. It’s simple but lacks precision and is rarely used for modern industrial overlays.
-
Here’s a table comparing these processes:
Process
|
Heat Source
|
Filler Type
|
Precision
|
Speed
|
Typical Use
|
---|---|---|---|---|---|
SMAW
|
Electric arc
|
Stick electrode
|
Low
|
Slow
|
General repairs, small areas
|
GMAW
|
Electric arc
|
Wire
|
Medium
|
Moderate
|
Automated overlays, medium scale
|
GTAW
|
Electric arc
|
Rod/Wire
|
High
|
Slow
|
Precision, thin overlays
|
PTAW
|
Plasma arc
|
Powder
|
High
|
Moderate
|
Hardfacing, critical components
|
SAW
|
Electric arc
|
Wire
|
Medium
|
Fast
|
Thick overlays, large surfaces
|
Laser Weld
|
Laser beam
|
Powder/Wire
|
Very High
|
Moderate
|
High-value, precise applications
|
OFW
|
Oxy-fuel flame
|
Rod
|
Low
|
Slow
|
Basic, low-tech overlays
|
Each process suits different needs based on factors like cost, component size, and performance requirements.
Laser Weld Overlay Process Benefits
Laser weld overlay, also known as laser cladding, stands out for its advanced capabilities. It uses a focused laser beam to melt a filler material (typically powder or wire) and deposit it onto the substrate. The process is highly controlled, resulting in several benefits:
-
Precision and Control
-
The laser beam can be finely adjusted, allowing for thin, uniform overlays (as little as 0.1 mm) and intricate patterns. This is ideal for repairing small areas or applying overlays to complex geometries.
-
-
Low Heat Input
-
Unlike traditional welding, laser cladding minimizes the heat-affected zone (HAZ), reducing thermal distortion and stress in the substrate. This preserves the base material’s properties.
-
-
Minimal Dilution
-
The overlay material mixes less with the substrate, ensuring the applied layer retains its intended properties (e.g., corrosion resistance or hardness).
-
-
High Bonding Strength
-
The metallurgical bond is strong and defect-free, thanks to the rapid cooling rates and precise energy delivery.
-
-
Versatility
-
Laser cladding works with a wide range of materials, including metals, alloys, and even ceramics, and can be automated for consistency.
-
-
Reduced Material Waste
-
The focused application uses only the necessary amount of filler, making it efficient and cost-effective for expensive materials like titanium or nickel alloys.
-
-
Improved Surface Quality
-
The overlay often requires little to no post-processing due to its smooth finish and lack of porosity or cracks.
-
-
Environmental Benefits
-
Lower energy consumption and reduced need for consumables (e.g., shielding gases) make it more sustainable than some traditional methods.
-
These advantages make laser weld overlay a preferred choice for high-tech industries where quality and longevity are critical.
Industries and Applications
Weld overlay, including laser cladding, is employed across numerous industries to enhance component performance and longevity. Below are key industries and their applications, with a table summarizing examples.
-
Oil and Gas
-
Pipelines, valves, and fittings receive corrosion-resistant overlays (e.g., Inconel) to withstand harsh fluids and high pressures.
-
-
Power Generation
-
Turbine blades, boiler tubes, and heat exchangers use overlays to resist wear, heat, and oxidation.
-
-
Aerospace
-
Engine components and structural parts get overlays for durability and lightweight performance, often using titanium or nickel alloys.
-
-
Mining
-
Excavator buckets, crusher rolls, and drill bits are hardfaced to resist abrasion from rocks and minerals.
-
-
Automotive
-
Engine valves, gears, and dies receive overlays to improve wear resistance and extend service life.
-
-
Chemical Processing
-
Reactors, pumps, and piping systems use corrosion-resistant overlays to handle aggressive chemicals.
-
-
Manufacturing
-
Cutting tools, molds, and dies are overlaid to maintain sharpness and withstand repetitive stress.
-
Industry
|
Application
|
Overlay Purpose
|
---|---|---|
Oil and Gas
|
Pipelines, valves
|
Corrosion and pressure resistance
|
Power Generation
|
Turbine blades, boiler tubes
|
Heat and wear resistance
|
Aerospace
|
Engine parts, landing gear
|
Durability, lightweight strength
|
Mining
|
Buckets, crushers
|
Abrasion resistance
|
Automotive
|
Valves, gears
|
Wear resistance, longevity
|
Chemical Processing
|
Pumps, reactors
|
Corrosion resistance
|
Manufacturing
|
Tools, molds
|
Hardness, precision
|
These applications highlight weld overlay’s role in reducing maintenance costs and downtime.
Materials Often Used for Weld Overlay
The choice of overlay material depends on the substrate and the desired properties. Below are commonly used materials, followed by a table with examples and purposes.
-
Stainless Steel
-
Offers excellent corrosion resistance and moderate wear resistance. Common grades include 316L and 308.
-
-
Nickel-Based Alloys
-
Materials like Inconel 625 and Hastelloy provide superior resistance to corrosion, heat, and oxidation.
-
-
Cobalt-Based Alloys
-
Stellite alloys (e.g., Stellite 6) are renowned for hardness and wear resistance, especially at high temperatures.
-
-
Tungsten Carbide
-
Used in hardfacing for extreme abrasion resistance, often blended with a metal matrix.
-
-
Chromium Carbide
-
Provides a cost-effective solution for wear resistance in high-abrasion environments.
-
-
Titanium Alloys
-
Lightweight and corrosion-resistant, used in aerospace and marine applications.
-
-
Copper-Based Alloys
-
Applied for thermal conductivity and wear resistance in specific applications like bearings.
-
Material
|
Key Properties
|
Common Applications
|
---|---|---|
Stainless Steel
|
Corrosion resistance
|
Pipelines, chemical reactors
|
Nickel Alloys
|
Heat, corrosion resistance
|
Turbine blades, oil rigs
|
Cobalt Alloys
|
Hardness, wear resistance
|
Mining tools, valves
|
Tungsten Carbide
|
Extreme abrasion resistance
|
Drill bits, crushers
|
Chromium Carbide
|
Wear resistance
|
Conveyor systems, wear plates
|
Titanium Alloys
|
Lightweight, corrosion
|
Aerospace components
|
Copper Alloys
|
Thermal conductivity
|
Bearings, electrical parts
|
These materials are selected to match the environmental challenges faced by the component.
To provide a deeper understanding, let’s explore each section further.
Cladding vs. Overlay in Practice
In industries like shipbuilding, cladding might involve bonding a thick stainless steel plate to a carbon steel hull using explosive bonding, creating a robust, corrosion-resistant exterior. Overlay, however, might involve welding a thin layer of nickel alloy inside a pipe to protect against corrosive seawater. The choice between the two depends on whether the goal is structural reinforcement (cladding) or surface enhancement (overlay). In some cases, weld overlay is considered a type of cladding, especially when thicker layers are applied, illustrating the overlap in terminology.
Weld Overlay Process Details
The weld overlay process begins with surface preparation—cleaning and sometimes preheating the substrate to reduce thermal shock. The welding method then deposits the overlay material in layers, with each pass carefully controlled to avoid defects like cracks or porosity. Post-weld treatments, such as grinding or heat treatment, may refine the surface or relieve stresses. Automation is increasingly common, especially with laser and PTAW processes, improving consistency and reducing labor costs.
Laser Weld Overlay in Depth
Laser cladding’s precision stems from its ability to focus energy on a tiny area—sometimes as small as 0.5 mm—allowing for micro-repairs on turbine blades or medical implants. The low heat input is critical for thin-walled components, where traditional welding might cause warping. The process can also deposit gradient layers, transitioning from one material to another (e.g., steel to nickel), enhancing compatibility between substrate and overlay.
Industry-Specific Examples
In oil and gas, a weld overlay of Inconel 625 on a carbon steel valve can withstand sour gas (H2S) exposure, preventing costly replacements in offshore rigs. In mining, tungsten carbide overlays on crusher jaws ensure they endure thousands of tons of ore without wearing down. Aerospace applications often involve laser cladding of titanium onto engine parts, balancing weight savings with durability.
Material Selection Nuances
Nickel alloys like Inconel are pricey but justify their cost in extreme environments, such as nuclear reactors where failure isn’t an option. Cobalt alloys, while harder, can be brittle, so they’re often applied in thin layers over tougher substrates. Tungsten carbide’s exceptional hardness comes at the cost of ductility, making it ideal for static wear surfaces but less so for impact-heavy applications.
Weld overlay, whether through traditional methods or advanced laser cladding, is a versatile and essential technique for enhancing material performance. Its distinction from cladding lies in its focus on surface improvement rather than structural change, though both serve vital roles in engineering. With a range of processes, benefits like those of laser cladding, and applications spanning industries from mining to aerospace, weld overlay continues to evolve with technology. The materials chosen—stainless steel, nickel alloys, carbides, and more—tailor the solution to specific challenges, ensuring durability and efficiency.