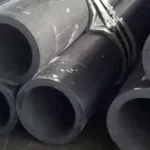
Optimization of the Seamless Steel Pipe Continuous Rolling Process
April 2, 2025Engineering Case Study: KDLFEED Company Factory Construction
April 9, 2025
Why Ductile Iron Pipe Standards Matter for Safe Installations
When it comes to constructing reliable and long-lasting pipeline systems, the materials you choose play a pivotal role. Among the top contenders, ductile iron pipe stands out for its strength, durability, and versatility. However, what ensures its effectiveness in real-world applications isn’t just the material itself—it’s the standards that govern its production, testing, and installation. In this comprehensive guide, we’ll explore why ductile iron pipe standards matter for safe installations, diving into key specifications, parameters, and comparisons with alternatives like PVC and steel pipes.
The Importance of Ductile Iron Pipe Standards
Ductile iron pipe standards are a set of guidelines and requirements established by organizations like the American Water Works Association (AWWA), the International Organization for Standardization (ISO), and the American National Standards Institute (ANSI). These standards ensure that every ductile iron pipe manufactured meets rigorous quality, safety, and performance benchmarks. But why do these standards matter so much?
For one, pipelines—whether used for water supply, wastewater management, or industrial applications—are critical infrastructure. A failure in these systems can lead to catastrophic consequences, including water loss, environmental damage, and even public health risks. Standards provide a framework to minimize these risks by ensuring consistency in material strength, corrosion resistance, and installation practices.
Moreover, adhering to ductile iron pipe standards guarantees compatibility with fittings, joints, and other system components. This uniformity is essential for engineers and contractors working on large-scale projects, as it reduces the likelihood of errors during installation and maintenance.
Key Ductile Iron Pipe Standards You Should Know
Several standards govern the production and use of ductile iron pipes. Below are some of the most widely recognized ones:
- AWWA C151: Covers the manufacturing of ductile iron pipes for water and other liquids, specifying minimum wall thickness, pressure ratings, and material properties.
- ISO 2531: An international standard for ductile iron pipes, fittings, and accessories, focusing on dimensions, mechanical properties, and coatings.
- ANSI/AWWA C110: Details standards for ductile iron fittings used in water systems, ensuring proper design and pressure capacity.
- ASTM A536: Specifies the metallurgical properties of ductile iron, including tensile strength and elongation.
Each of these standards addresses different aspects of ductile iron pipe production and application, ensuring that the pipes can withstand the stresses of underground installation, high-pressure fluids, and long-term use.
Technical Parameters of Ductile Iron Pipes
To understand why standards are critical, let’s look at the technical parameters that ductile iron pipes must meet. These parameters are defined by the aforementioned standards and vary depending on the pipe’s intended use.
Parameter | Description | Typical Value (AWWA C151) |
---|---|---|
Diameter | Nominal size of the pipe | 3″ to 64″ (76 mm to 1625 mm) |
Wall Thickness | Thickness of the pipe wall | 0.25″ to 1.38″ (6.4 mm to 35 mm) |
Pressure Rating | Maximum internal pressure | 150 psi to 350 psi (10 bar to 24 bar) |
Tensile Strength | Ability to resist breaking under tension | Minimum 60,000 psi (414 MPa) |
Yield Strength | Stress at which deformation begins | Minimum 42,000 psi (290 MPa) |
Elongation | Measure of ductility | Minimum 10% |
Coating | Protective layer against corrosion | Cement-mortar lining, zinc coating |
These parameters ensure that ductile iron pipes can handle the demands of various applications, from municipal water systems to industrial fluid transport. Standards like AWWA C151 mandate rigorous testing—such as hydrostatic pressure tests—to verify that each pipe meets these requirements before it’s shipped to a project site.
Why Standards Ensure Safe Installations
Safe installations depend on more than just high-quality materials; they require predictability and reliability. Here’s how ductile iron pipe standards contribute to safety:
1. Structural Integrity
The tensile and yield strength requirements outlined in standards like ASTM A536 ensure that ductile iron pipes can withstand external loads, such as soil pressure, and internal pressures from water or gas. Without these standards, pipes might fail under stress, leading to leaks or bursts.
2. Corrosion Resistance
Standards mandate protective coatings, such as cement-mortar linings and zinc exteriors, to prevent corrosion. This is especially important for underground installations where pipes are exposed to moisture and soil chemicals over decades.
3. Proper Joint Design
Joint systems—like push-on, restrained, or flanged joints—are standardized to ensure leak-proof connections. AWWA C110, for instance, specifies the design of fittings and joints to prevent separation under pressure.
4. Compatibility
Standardized dimensions and tolerances mean that pipes, fittings, and valves from different manufacturers can work together seamlessly, reducing the risk of installation errors.
Comparison: Ductile Iron Pipe vs. PVC and Steel
To fully appreciate the value of ductile iron pipe standards, it’s worth comparing ductile iron pipes to other common materials like PVC and steel. Below is a detailed comparison table:
Feature | Ductile Iron Pipe | PVC Pipe | Steel Pipe |
---|---|---|---|
Material Strength | High (60,000 psi tensile) | Moderate (7,000 psi tensile) | Very High (up to 80,000 psi) |
Corrosion Resistance | Excellent with coatings | Excellent (non-corrosive) | Moderate (requires coatings) |
Durability | 50-100 years | 50-70 years | 30-50 years |
Pressure Rating | 150-350 psi | 100-200 psi | 200-500 psi |
Weight | Heavy (e.g., 50 lbs/ft for 6″) | Light (e.g., 2 lbs/ft for 6″) | Moderate (e.g., 20 lbs/ft for 6″) |
Cost | Moderate to High | Low to Moderate | High |
Installation Ease | Moderate (heavier equipment) | Easy (lightweight) | Moderate (welding required) |
Ductile Iron Pipe: Excels in strength, longevity, and corrosion resistance when standards are followed. Its heavier weight and higher cost are trade-offs for durability and reliability in high-pressure or harsh environments.
PVC Pipe: Lightweight and corrosion-resistant, but lacks the strength and pressure capacity of ductile iron, making it better suited for low-pressure applications.
Steel Pipe: Offers exceptional strength and pressure ratings but is prone to corrosion unless heavily coated, and its shorter lifespan makes it less ideal for long-term infrastructure.
How Standards Impact Project Success
Beyond safety, adhering to ductile iron pipe standards directly influences the success of a project. For example, a municipal water system designed with AWWA-compliant pipes is more likely to meet regulatory requirements, pass inspections, and avoid costly repairs down the line. Contractors also benefit from standardized installation procedures, which streamline workflows and reduce training time.
From a financial perspective, standardized pipes may have a higher upfront cost, but their extended lifespan (often exceeding 100 years with proper maintenance) and lower failure rates make them a cost-effective choice over time. This is particularly true in regions prone to earthquakes or soil shifts, where ductile iron’s flexibility and strength shine.
Real-World Applications of Ductile Iron Pipe Standards
Ductile iron pipes are used in a variety of applications, and standards ensure they perform reliably in each scenario:
- Water Distribution: AWWA C151 pipes deliver potable water under high pressure without leaks.
- Wastewater Management: Corrosion-resistant linings protect pipes from sewage’s harsh chemicals.
- Industrial Systems: High tensile strength supports the transport of abrasive or high-temperature fluids.
In each case, standards provide the assurance that the pipes will meet the specific demands of the environment and application.
Challenges When Standards Are Ignored
What happens when ductile iron pipe standards are not followed? The risks are significant:
- Pipe Failures: Non-compliant pipes may crack under pressure or corrode prematurely.
- Installation Issues: Inconsistent dimensions can lead to joint leaks or fitting mismatches.
- Regulatory Penalties: Projects using substandard materials may fail inspections, delaying timelines and increasing costs.
These challenges highlight why adherence to standards isn’t just a best practice—it’s a necessity for safe and successful installations.
Conclusion: The Value of Ductile Iron Pipe Standards
Ductile iron pipe standards are the backbone of safe, reliable, and efficient pipeline installations. By setting clear benchmarks for strength, durability, and compatibility, they ensure that these pipes can handle the demands of modern infrastructure projects. Whether you’re comparing ductile iron to PVC or steel, or planning a water distribution system, understanding and adhering to these standards is key to achieving long-term success.
Investing in standardized ductile iron pipes means investing in safety, longevity, and peace of mind. So, the next time you’re specifying materials for a project, remember: standards matter—and with ductile iron pipes, they make all the difference.