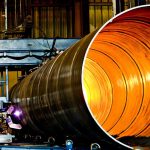
Yeni Enerji Çelik Boruları
Ekim 13, 2024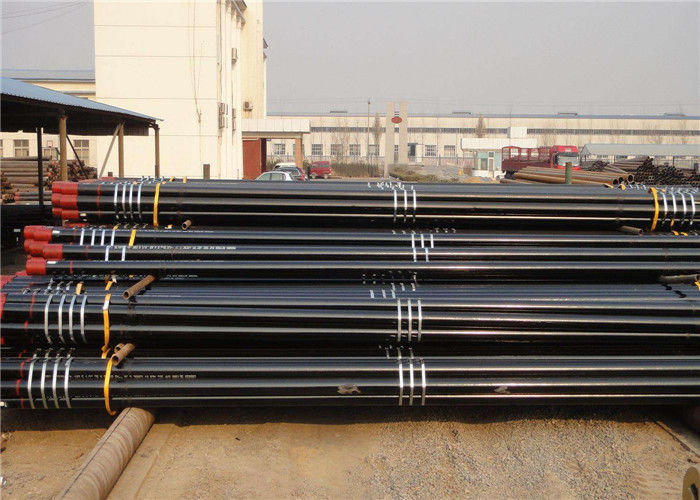
Petrol ve Gaz Kuyularında İç Korozyon: Korozyon İnhibitörlerinin Zorlukları ve Fırsatları
Ekim 18, 2024ASTM A335 P91 10Cr9Mo1VNbN – Kaynak ve Isıl İşlem Süreci Araştırması
soyut: ASTM A335 P91 10Cr9Mo1VNbN çeliği, kazan üretimi için yüksek kaliteli bir hammaddedir tüpler. ancak, Kaynak kabiliyeti zayıftır ve ısıl işlem sıcaklığına çok duyarlıdır.. Premium bağlantıların kasasını ve gaz sızdırmazlık mekanizmasını gösterir, soğukta çatlamaya karşı yüksek bir eğilimi vardır, Kaynak sonrası kaynak bölgesinde ve ısıdan etkilenen bölgede darbe tokluğu ve sertliği gibi niteliksiz mekanik özelliklerin tespitine duyarlı hale getirilmesi. 10Cr9Mo1VNbN'nin kaynak prosesi üzerine kapsamlı bir çalışma yapıldı. Çelik borunun kaynak prosesi ve ısıl işlem parametreleri, kaynak testleri ve kaynak prosesi değerlendirmeleri ile optimize edilmiştir.. Bu, ASTM A335 P91 10Cr9Mo1VNbN çelik borunun kaynak kalitesinde bir iyileşmeye neden oldu, benzer malzeme ürünleri için kaynak prosesi referansı sağlayabilen.
Anahtar kelimeler: ASTM A335 P91 10Cr9Mo1VNbN çelik; Kaynak; ısıl işlem; işlem; optimizasyon
ASTM A335 P91 10Cr9Mo1VNbN çeliği ilk kez Amerika Birleşik Devletleri'ndeki Oak Ridge Ulusal Laboratuvarı'nda başarıyla geliştirildi, ve çelik kalitesi ASTMA335P91 olarak belirlendi, P91 çeliği olarak anılır. Ülkem P91 çeliğini başarıyla geliştirdikten sonra, ulusal standarda dahil edildi ve çelik kalitesi 10Cr9Mo1VNbN olarak belirlendi. 10Cr9MolVNbN çeliği, standart 9Cr-1Mo çeliği bazında C içeriğinin azaltılmasıyla elde edilir, Nb ve V gibi eser elementlerin eklenmesi, ve N elemanının uygun şekilde kontrol edilmesi. Sıradan paslanmaz çelikle karşılaştırıldığında, ASTM A335 P91 10Cr9Mo1VNbN çelik malzeme, yüksek sıcaklık dayanıklılık mukavemetinde mekanik performans avantajlarına sahiptir, izin verilen stres, termal genleşme katsayısı, Uygulamaları için gerekli mekanik ve fiziksel özelliklere göre farklı çelik türleri üretilmektedir., darbe tokluğu, genel bükme performansı, yüksek sıcaklıkta yorulma performansı ve yüksek sıcaklıkta oksidasyon direnci [1-51, Bu, çalışma sırasında sıradan ısıya dayanıklı çeliğin organizasyonel bozulması sorununu çözebilir ve boru patlaması kazalarının oluşumunu azaltabilir. Kazan borularının üretim ve imalatında sıradan ısıya dayanıklı çeliğin yerini alan yüksek kaliteli bir üretim malzemesidir.. ASTM A335 P91 10Cr9Mo1VNbN çeliğinin dezavantajları zayıf kaynaklanabilirliktir, Isıl işlem sıcaklığına karşı yüksek hassasiyet, soğuk çatlamaya karşı yüksek eğilim, ve kaynak sırasında kaynaklı bağlantıların mukavemetinin azalması ve bunların neden olduğu iş parçalarının erken arızalanması sorunu. kaynak sonrası, kaynak bölgesi ve ısıdan etkilenen bölgede darbe tokluğu ve sertliği gibi niteliksiz mekanik özellikler gibi kusurların tespit edilmesi kolaydır 6-81. ASTM A335 P91 10Cr9Mo1VNbN çeliğinin kaynak özelliklerini tam ve derinlemesine anlamak ve gerçek kaynak prosesindeki teknik sorunları çözmek için, İlgili personel ve akademisyenler araştırma yaptı. Xiong Yifeng ve diğerleri.. 10Cr1·9Mo1VNbN çelik kaynaklı bağlantıların ısıdan etkilenen bölgesinin sertliğinin ön ısıtma sıcaklığının artmasıyla azaldığını buldu, minimum ön ısıtma sıcaklığı 150°C'den düşük olamaz, ve malzemenin soğuk çatlama eğilimi ön ısıtma sonrasında önemli ölçüde azalır. Zhu Ping, farklı izolasyon sıcaklıklarının mukavemet üzerindeki etkisini elde etti, sertlik, Kaynak sonrası ısıl işlem testleri yoluyla P91 çelik kaynaklı bağlantıların darbe dayanıklılığı ve mikro yapısı, ve daha düşük bir yalıtım sıcaklığı kullanılsa bile, bağlantı sertliği ilgili spesifikasyonların gerektirdiği göstergelerden daha yüksektir. Liu Chisen ve ark.10, P91 çeliğinin kaynak kalitesini sağlamak için kaynak sırasında soğuk çatlakların önlenmesinin birincil önlem olduğunu öne sürdü, Kaynakta soğuk çatlakların oluşmasını önlemek için kaynak öncesi ön ısıtmanın makul şekilde kullanılması ve kaynak sonrası ısıl işlem tedbirlerinin alınması gerekmektedir.. NS boru hattı Bir firmanın doğalgaz arıtma cihazının kuyruk gazı yakma fırını atık ısı geri kazanım sistemi projesinin malzemesi ASTM A335 P91 10Cr9Mo1VNbN çeliğidir.. Boru hattı kaynak kalitesinin standartlara uygun olmasını sağlamak ve güvenilir kaynak prosesi ve ısıl işlem parametrelerini elde etmek amacıyla, bu makale malzeme kaynak karakteristik analizini yürütmektedir, kaynak testi ve kaynak prosesi değerlendirmesi.
1 ASTM A335 P91 10Cr9Mo1VNbN çelik kaynak test malzemeleri ve ekipmanları
1.1 Malzemeleri
1.1.1 tekrar test et
ASTM A335 P91 10Cr9Mo1VNbN malzemesi testi yerli bir malzemedir. dikişsiz çelik boru yüksek basınçlı kazanlar için, φ114,3mm×14mm boyutunda, ve tedarik durumu normalleştirildi + temperli. GB5310-2008'e göre “Yüksek Basınçlı Kazan için Dikişsiz Çelik Boru”, kimyasal bileşimi, mekanik özellikler ve sertlik yeniden test edilir. Sonuçlar Tablolarda gösterilmektedir 1 ve 2, bunların tümü standart gereksinimleri karşılıyor.
Tablo 1 Kimyasal bileşimin yeniden test sonuçları (kütle kesri) ASTM A335 P91 10Cr9Mo1VNbN çelik boru
element | C | MnSiSPCrMo | |||||
Standard content | 0.08~ 0.12 | 0.3~ 0.6 | 0.2• 0.5 | ≤0,01 | ≤0.02 | 8.0~ 9.5 | 0.85~ 1.05 |
actual content | 0.1 | 0.46 | 0.28 | 0.002 | 0.012 | 8.78 | 0.93 |
element | V | Ni | Al | Ti | NB | Zr | n |
Standard content | 0.180.25 | ≤0.40 | ≤0.02 | ≤0,01 | ≤0.10 | ≤0,01 | 0.03-0.07 |
actual content | 0.20 | 0.06 | 0.006 | 0.002 | 0.08 | 0.002 | 0.041 |
Tablo 2ASTM A335 P91 10Cr9Mo1VNbN çelik borunun mekanik özellikleri yeniden test sonuçları
Mechanical properties | MPa Tensile strength R/MPa | MPa Yield strength R/MPa | /% Elongation A/% | HRC Hardness/HRC |
Standard requirements | ≥585 | ≥415 | ≥20 | ≤25 |
actual performance | 655,660 | 505,495 | 29,30.5 | 20,19 |
1.1.2 Kaynak malzemelerinin seçimi
ASTM A335 P91 10Cr9Mo1VNbN çeliğini kaynak yaparken, kolayca soğuk çatlaklar oluşmakla kalmaz, ancak kaynak malzemeleri eşleşmediğinde de sıcak çatlaklar meydana gelecektir121. Kaynak malzemeleri bileşen eşleştirme prensibine göre seçilmelidir, ve Cr gibi alaşım elementlerinin içeriği, sen, V, Kaynaklı bağlantının yapısının ve performansının ana malzemeyle mümkün olduğunca tutarlı olmasını sağlamak için kaynak malzemelerindeki N ve N sıkı bir şekilde kontrol edilmelidir..
Kaynak malzemesi olarak Bōhler Welding firmasının MTS3 marka 2.4mm spesifikasyonlu argon arkı kaynak teli ER90S-B9 ürünü seçilmiştir.. Kaynak malzemesinin kimyasal bileşimi Tabloda gösterilmektedir. 3, ASME Kodunun gerekliliklerini karşılayan, Bölüm Bölüm C-2021 “Kaynak Çubuklarının Özellikleri, Elektrotlar, ve Dolgu Metalleri Demir Dışı Malzeme Şartnamesi” [13].
Tablo 3 Testte kullanılan kaynak malzemesi ER90S-B9'un kimyasal bileşimi
.
1.2 Test ekipmanı
Kaynak ekipmanı AOTAIZX7-400STG elektrikli kaynak makinesini kullanıyor. Bu ekipmanın özelliği kaynak akımının 1A'e hassas bir şekilde ayarlanabilmesidir., itme akımı ayrı olarak ayarlanabilir, ark akımı ayrı ayrı ayarlanabilir, ve iyi bir ark vuruşu performansına sahiptir, ve ark başlatma arızasının olması kolay değildir, Ark kırma ve kaynak çubuğunun yapışması.
2ASTM A335 P91 10Cr9Mo1VNbN çelik kaynak prosesi değerlendirmesi
NB/T47014-2011'e göre “Basınçlı ekipmanlar için kaynak prosesi değerlendirmesi” 14, ASTM A335 P91 10Cr9Mo1VNbN çelik kaynak prosesi derlenerek kaynak proses değerlendirmesi gerçekleştirilir.
2.1 Numune hazırlama
2.1.1 Eğim işleme
φ114,3mm×14mm dikişsiz çelik boru kullanın, proje ihtiyaçlarına göre, 150 mm uzunluğunda numunelerden oluşan iki bölümü makinede işleyin, ve eğimi işleyerek bunları inceltin. Eğim formu ve boyut gereklilikleri Şekilde gösterilmektedir. 1. İşleme sırasında, Soğuk işleme benimsendi, İş parçasının aşırı ısınmasını ve ana malzeme performansının bozulmasını önlemek için kesme işlemi sırasında kesme sıvısı zamanında yenilenir.
şekil 1 Numune oluk formu ve boyutu gereklilikleri
2.1.2 Temizleme ve montaj
Suyu temizle, pas, oluk yüzeyinde ve çevresinde yağ ve diğer zararlı yabancı maddeler (oluk kenarından ölçüldü, her iki taraf da 20 mm'den az değil), ve oluğu metalik parlaklık ortaya çıkana kadar taşlayın. Argon arkı kaynağı kullanın (GTAW) kaynak yapmak ve montaj nokta kaynağı yapmak.
2.1.3 Ön ısıtma sıcaklığı ve pasolar arası sıcaklık kontrolü
Kaynağın ön ısıtma sıcaklığı 100°C'den düşük olduğunda, Kaynak sonrası soğuk çatlakların oluşması muhtemeldir [15-16]. ancak, çok yüksek ön ısıtma sıcaklığı ve pasolar arası sıcaklık da ASTM A335 P91 10Cr9Mo1VNbN çeliğine zararlıdır, bu da kaynak tokluğunda önemli bir azalmaya neden olacaktır17.
Referansın araştırma sonucuna dayanarak [2], kaynak numunesinin ön ısıtma sıcaklığı 150~200^∘ C'ye ayarlanmıştır. Ön ısıtma için alevle ısıtmayı kullanın. İzleme noktasının sıcaklığı ön ısıtma sıcaklığına ulaştığında, kaynak yapmadan önce bir süre saklayın.
Geçiş sıcaklığının 250°C'yi aşmaması gerekir. Kaynak işlemi sırasında, Her kaynak tamamlandıktan sonra pasolar arası sıcaklığı ölçmek için bir kızılötesi termometre kullanılır, ve her kaynağın kaynak zamanlaması, pasolar arası sıcaklığın proses gerekliliklerini aşmamasını sağlamak için makul şekilde kontrol edilir.
2.2 Numune kaynağı
2.2.1 Koruyucu gaz ve akış hızı
Argon koruması, numune tabanı kaynak bağlantısının performansını artırmak için önemli bir önlemdir, gaz kalitesi ve çalışma parametrelerinin kontrol edilmesi gerekir. Argon saflığı gereksinimi 99.99% (hacim oranı), ve önerilen ön gaz akış hızı 10~14L/dak'tır. Aynı zamanda, arkada argon gazı değişimi gerekiyor. Spesifik yöntem, suda çözünür kağıdı numunenin her iki tarafına yapıştırmak ve bunu kapalı bir oda oluşturacak şekilde yüksek sıcaklık bantıyla sabitlemektir.. Önerilen gaz hacmi akış hızı 8~10L/dak'dır.
2.2.2 Kaynak işlemi parametreleri
GTAW kaynak için kullanılır, ve kaynak sıcaklığı ön ısıtma sıcaklığına ulaştıktan sonra başlar. Aşırı ısı girişi neden olur 8 ısıdan etkilenen bölgede ve kaynak bölgesinde ferrit oluşması, ve ayrıca kaynağın sürünme kopma mukavemetini ve darbe dayanıklılığını önemli ölçüde azaltacaktır. Referans [1] ilgili içerik, kaynak prosesinin kaynak parametreleri kontrol edilir, Tabloya bakınız 4.
2.3 Kaynak sonrası ısıl işlem
Kaynak durdurulduktan sonra iş parçası gerilim giderme ısıl işlemine tabi tutulmadığında, Kaynak parçası belirli bir sıcaklığa kadar ısıtılır ve kaynağın daha yavaş bir hızda soğumasını ve hidrojenin kaynaktan yeterli sürede kaçmasını sağlamak için bir süre tutulur.. Bu işlem veya yönteme ısıl işlem sonrası denir. Isıl işlem sonrası iki hedef vardır: 1. Termal stresi azaltın ve soğuma sırasında çatlakların oluşmasını önleyin. 2. Kaynakta hidrojenin difüzyonunu ve kaçışını teşvik etmek ve daha sonraki aşamada hidrojenin neden olduğu çatlama riskini ortadan kaldırmak için dehidrojenasyon işlemi. Isıl işlem sonrası sıcaklık
Tablo 4 ASTM A335 P91 10Cr9Mo1VNbN çelik kaynak işlemi parametreleri
Çeliğin sürekli soğutulması sırasında martensitik dönüşüme uğramamış kalıntı östenitin ferrit veya perlite dönüşmesini önlemek için martensitik dönüşümün başlangıç sıcaklığının altında olmalıdır., böylece bağlantının darbe dayanıklılığı azalır.
ASTM A335 P91 10Cr9Mo1VNbN çeliği için, ısıl işlem sonrası sıcaklık parametreleri sürekli soğutma dönüşümüne göre belirlenir (ŞNT) eğri [17]. ASTM A335 P91 10Cr9Mo1VNbN çeliğinin CCT eğrisi Şekilde gösterilmektedir. 2.
Martensitik dönüşümün başlangıç sıcaklığı M_S, Şekil 1'e göre belirlenir. 2 yaklaşık 380°C. Gerçek üretim deneyimiyle birleştirildi, ASTM A335 P91 10Cr9Mo1VNbN'nin ısıl işlem sonrası işlem koşulları 2 saat boyunca 300~350°C'ye ayarlanır.
Şekil 2ASTM A335 P91 10Cr9Mo1VNbN çelik sürekli soğuma dönüşüm eğrisi (SKK eğrisi)
2.3.2 Kaynak sonrası ısıl işlem
Kaynak sonrası ısıl işlem, kaynağın belirli bir sıcaklığa kadar ısıtıldığı bir ısıl işlem sürecini ifade eder. (genellikle ısıtma sırasında perlitin östenite dönüşümünün başlangıç sıcaklığı) 30Kaynak sonrası çizginin ~50^∘ C altı, ve belirli bir süre bu sıcaklıkta tutularak, böylece kaynaklı bağlantının metalografik yapısını ve özelliklerini iyileştirmek veya artık gerilimi ortadan kaldırmak için kaynak bağlantısı nispeten yavaş bir hızda soğutulur.. NB/T47015-2011'e göre “Basınçlı Kap Kaynak Kodu” 18, ASTM A335 P91 10Cr9Mo1VNbN çeliğin kaynak sonrası ısıl işlem sıcaklığı 730 ° C'ye ayarlanmıştır, ve yalıtım işlemi 13 saat boyunca gerçekleştirilir. Maksimum ısıtma hızı, daha küçük olarak alınır. (birim °C/saat, δ_PWHT mm cinsinden kaynak metali kalınlık değeridir) ve 220°C/saat, ve maksimum soğutma hızı 280°C/saat'ten küçük olanı olarak alınır.. bu nedenle, ısıtma hızı 55~220^∘ C/saat olarak ayarlanmıştır, ve soğutma hızı 55~280^∘ C/saat'e ayarlanmıştır.
3ASTM A335 P91 10Cr9Mo1VNbN çelik kaynak sonrası muayene
Kaynaktan hemen sonra, kaynak oluşumunu kontrol edin. Kaynak ve ana malzeme düzgün bir geçişe sahiptir, alttan kesme gibi kusurları yoktur, füzyon ve çatlak eksikliği. 24kaynak sonrası h, kaynak ultrasonik test gibi tahribatsız testlere tabi tutulur (UT) ve radyografik testler (RT) kaynakta gecikmeli çatlakları önlemek için. Tahribatsız muayene NB/T47013-2015'e dayanıyordu “Basınçlı Ekipmanların Tahribatsız Muayenesi” 191.
4 Kaynak kalite kontrol testi ve sonuç analizi
4.1 Kimyasal bileşim analizi
ASTM A335 P91 10Cr9Mo1VNbN çelik kaynaklı bağlantılardan kimyasal bileşimlerini elde etmek için numune alındı ve analiz edildi (Tablo 5). Kompozisyon NB/T47008-2017 gerekliliklerini karşıladı “Basınçlı Ekipmanlar için Karbon Çelik ve Alaşımlı Çelik Dövmeler” [20].
4.2 Mekanik Özellikler
NB/T47014-20111 gerekliliklerine göre, 2 çekme numuneleri, 4 yan bükme numuneleri ve 1 farklı bölgelerden grup darbe numunesi hazırlanarak mekanik özellik testleri yapılmıştır.. Çekme numunelerinin çekme mukavemeti 704MPa ve 710MPa idi., ve yan bükme numunelerinde çatlak yoktu. Kaynak bölgesinin darbe enerjisi, ısıdan etkilenen bölge ve ana materyal bölgesi Tabloda gösterilmektedir 6.
NB/T47008-2017'ye göre, çeliğin plaka kalınlığı 300 mm'ye eşit veya daha az olduğunda, Çekme mukavemeti ve darbe enerjisinin nitelikli göstergeleri 585~755MPa'dır ve 47J'den az değildir. bu nedenle, ASTM A335 P91 10Cr9Mo1VNbN kaynaklı bağlantının mekanik özelliklerinin gereksinimleri karşıladığı görülebilir.
4.3 Metalografik yapı ve sertlik ASTM A335 P91 10Cr9Mo1VNbN kaynaklı bağlantının kesiti test yüzeyi olarak alınmıştır.. Testten önce, test edilecek bölüm işlenir, mekanik taşlama dahil, HCl sulu çözeltisinde kütle fraksiyonu ile mekanik parlatma ve dağlama 3% FeCl3 ve kütle fraksiyonu 10% 3~5 saniye için. T/2'de iki konum seçildi (T temel malzemenin kalınlığıdır) test için kaynak kesitinin, ve elde edilen metalografik yapı analiz diyagramı Şekilde gösterilmektedir. 3. Şekilde gösterildiği gibi 3, kaynak numunesi 730°C'ye ısıtıldıktan ve bu sıcaklıkta 13 saat tutulduktan sonra, kaynak bölgesinin yapısı temperlenmiş martenzittir + az miktarda beynit. Bu metalografik yapının özelliklerine dayanarak, Kaynak malzemesindeki alaşım elementlerinin östenit içerisinde çözündüğü sonucu çıkarılabilir., CCT eğrisi üzerindeki Ms noktasının konumunun azaltılması, böylece kaynak numunesinin 150-200° ön ısıtma aşamasında kalma süresi nispeten uzatıldı, ve tahıllar büyümeye devam etti. soğutma sonrası, şekilde gösterilen yapı oluşturuldu.
şekil 3 T/2'de ASTM A335 P91 10Cr9Mo1VNbN kaynağının kesitinin farklı konumlarındaki metalografik yapılar (100x)
5 Sonuç
ASTM A335 P91 10Cr9Mo1VNbN çelik malzemenin kaynaklanabilirliği zayıftır, ısıl işlem sıcaklığına çok duyarlıdır, soğuk çatlamaya karşı daha büyük bir eğilime sahiptir, ve kaynaklı bağlantıların mukavemetinin azalması gibi sorunlara eğilimlidir, iş parçalarının erken arızalanması, ve kaynak sırasında kaynak sonrası niteliksiz mekanik özellikler. Kaynak prosesi değerlendirmesi ve kaynak sonrası mekanik özellikler test muayenesi yoluyla, kaynak teli seçimi gibi proses parametreleri ve koşulları, kaynak öncesi temizlik, kaynak öncesi ön ısıtma, ASTM A335 P91 10Cr9Mo1VNbN çeliğinin ara katman sıcaklığı ve kaynak özellikleri optimize edildi. Ortaya çıkan kaynak işlemi pratiktir ve ürün kaynağına başarıyla uygulanmıştır., Benzer çelik ürünlerin kaynaklanması için rehberlik sağlayabilecek.